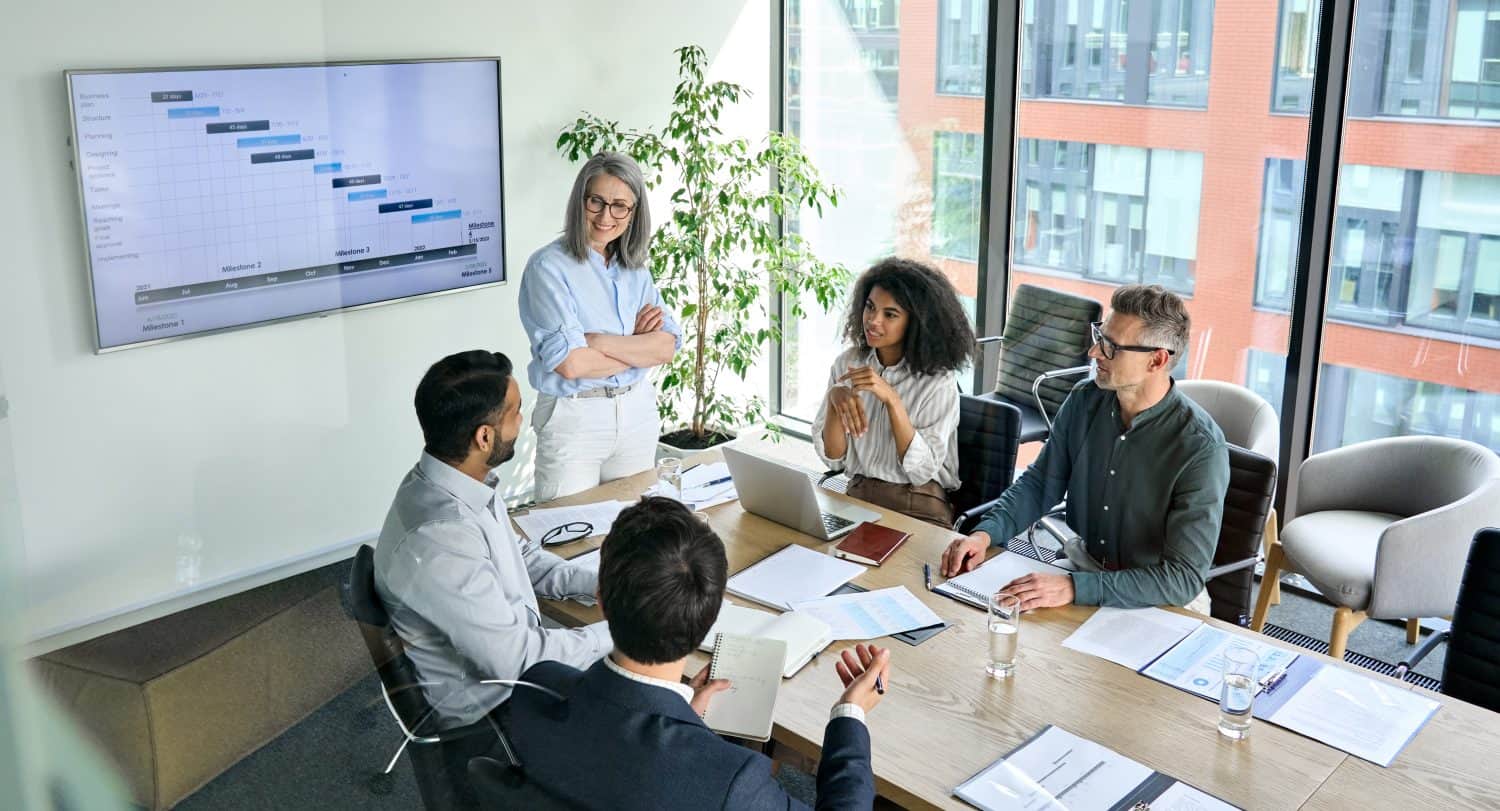
© Ground Picture/Shutterstock.com
Key Points
- FMEA is an approach to rooting out and remediating failures.
- It requires a multi-disciplined team with experts across all departments to succeed.
- FMEA plans need regular updates to account for changes as they occur.
FMEA is one of the most powerful approaches to safeguarding your projects from failures and defects. It isn’t a cakewalk to implement, but in the right hands, it can make projects run without a hitch. As you’re already used to utilizing data in making decisions, it only makes sense to start using this approach in your projects.
With that in mind, what industries are best suited for FMEA? There are a few that come to mind, as we’ll explore in today’s guide. You can certainly use FMEA in industries other than the ones mentioned today, but you’ll find it pays off to take this exhaustive approach for your projects.
What Is FMEA?
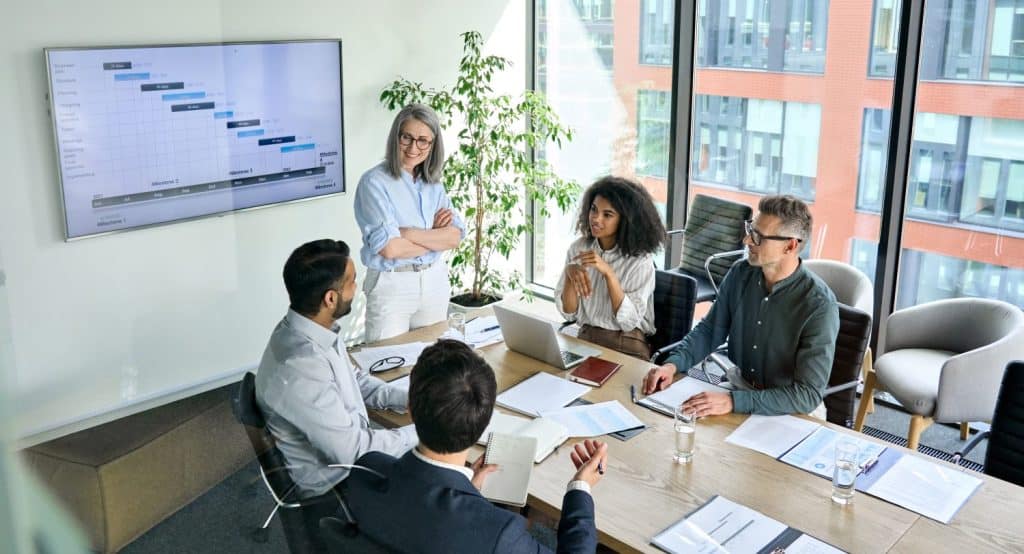
©Ground Picture/Shutterstock.com
FMEA is an acronym like you might expect to find in many of the tools employed in Lean Six Sigma. Its proper name is Failure Mode and Effects Analysis, which is a systematic approach to looking at and analyzing failure points in a given project.
Originally devised for the United States Military, it has since taken on a new life as a comprehensive means of planning for failure and defects in deliverables. Some industries simply cannot afford to let things go out in a less-than-ideal state.
When you consider its origin point, it makes sense, however. If failure isn’t an option, then you’ll want to plan. If you’re planning, you’ll want to use one of the approaches best encompassed by FMEA. That said, let’s dive into how this approach works.
How It Works
FMEA is a systematic approach, rather than a fire-and-forget sort of tool. When setting out to use FMEA, you’ll want to take a few steps which are as follows:
State the Scope
Before defining your FMEA, you’ll want to determine and define the scope of the plan itself. This includes the product or process you’re evaluating, the functions of said process, and who is performing work on the project.
Build Your Team
With the scope defined, you’ll want to get to work building a team. This is a different sort of team than your usual sort, needing subject matter experts and people from other departments. Your team is going to provide a wider breadth of functionality, so pick the right people.
Develop a Process Flow Diagram
With your team in place, you’re ready to visualize the process. For this step, you’ll want to create a process flow diagram. This should provide plenty of detail for your process, showing each step in sequential order.
Identify Modes or Points of Failure
With your process flow diagram, you can start to get creative. In this case, you’ll want to look for potential pain points or failure states within the process. These can come out of left field, so it helps to have the right team members looking over the process flow diagram.
Analyze the Potential Severity of Failure Points
After identifying potential failure points, you’ll want to rank them. This is best done on a scale from 1 to 10. 1 denotes something minor at best, and 10 is something catastrophic in your projects.
Determine the Likelihood of Failure
Now that your failure points are ranked, you’ll want to figure out just how likely these failure states are. This can be somewhat daunting, especially when you consider that some factors are simply out of your control. However, this is the point where you should consider the things that are in control throughout any project.
Calculate Your RPN
With everything else in place, you’re ready to calculate your risk priority number. This is done easily by multiplying the severity, likelihood, and detectability scores of a given failure state. RPN is a standard measurement for risk assessment.
Create Corrective Solutions
With your RPNs calculated, it’s time to craft corrective solutions. Which ones do you pick? You’ll want to go for those that have a higher overall RPN since those are areas of most concern.
Implement Corrective Solutions
With your solutions devised, it’s time to simply put them in place. These corrective solutions can save potential headaches and might save time and energy when it comes time to revise or improve processes further down the line.
Review and Update the FMEA Plan as Needed
Finally, you’ll want to review and update your FMEA as needed. It isn’t going to be of use later down the line if the information is out of date. Take the time and make sure everything is current.
FMEA: Industries and Projects That Benefit from It

Now that we’ve defined FMEA, it’s time to take a closer look at some of the top industries utilizing this approach in regular operations. As you’ll notice, just about every one of these industries has certain things in common: a low tolerance for defects.
That said, you could certainly apply the previously described steps to any industry. I’ve personally seen such measures taken for the implementation of new server racks in IT. I wouldn’t be shocked if software devs are using similar measures coupled with Agile or DevOps for a secure and fluid pipeline.
Automotive
Cars and other automobiles are complex machines. As such, it only stands to reason that FMEA is regularly utilized in the design process for the modern car. It is implemented at the design level in this case, taking a look at potential failure points like engines, brakes, and transmissions. Then they ascertain how it impacts the overall performance of a vehicle.
Aerospace
This one doesn’t come as much of a surprise, especially when you consider the roots of FMEA in the United States Military. If a car is complex, an aircraft is immensely more so. Points of failure can mean the difference between life and death. Much like automobiles, the aerospace industry uses FMEA as part of the design process itself.
Semiconductors
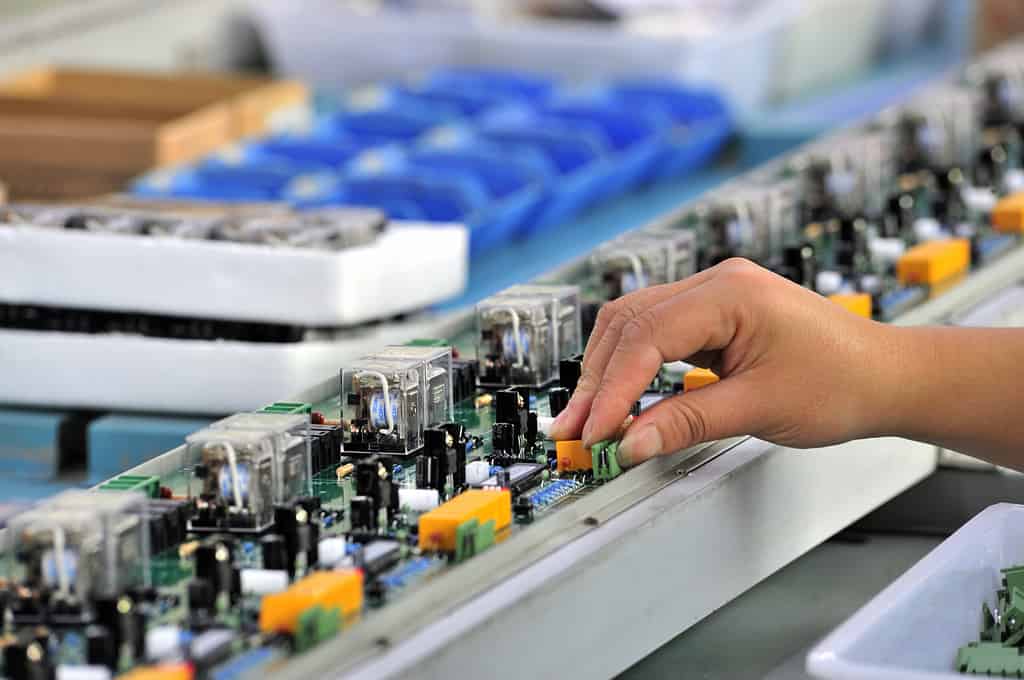
Semiconductors are the lifeblood of the modern computer, but they’re still prone to failure. I’m sure plenty of you have seen something like a new phone or laptop fail to work out of the box. This is one of those rare failures that made it past a semiconductor manufacturer.
In this case, however, FMEA is utilized during manufacturing to guarantee a solid throughput of quality. You want nearly identical results every single time, especially when you’re selling standardized equipment like microchips, processors, and other vital components for your average computer.
Food
We’re right back to more serious fare. Food has been industrialized for nearly a century at this point. FMEA is also utilized during the production process to help guarantee safety. Points of failure here are things like contamination, packaging, and poor handling from workers on the floor.
Failure to pay attention to such things can lead to sick customers and potential fatalities, so it pays to utilize FMEA here.
Medical Devices
I’ll readily admit I don’t have much experience in the medical tech field. However, FMEA is utilized here for the likes of determining points of failure during the servicing and maintenance stages of a machine’s lifecycle. Since these are already manufactured to exacting standards, they help illuminate potential pain points after regular use.
Further, this is a great means of guaranteeing continued safety when utilizing machines. You certainly don’t want to hop into a malfunctioning MRI or CAT scan, right? Medical technology is a different beast entirely when compared to semiconductors, but there is a bit of crossover in how FMEA applies to the machines themselves.
Telecommunications
This is something I have extensive experience with at this point. Telecommunications typically use FMEA as a point of service and maintenance. You can follow things to the letter and still experience failures due to unforeseen circumstances. When this happens, you’ll want to have a plan in place to reduce service outages.
Networks are finicky creatures at the best of times. FMEA is best utilized here to minimize the potential for billing errors, and network outages. Further, it guarantees customers are receiving stable and quality service on the whole.
Why It Matters
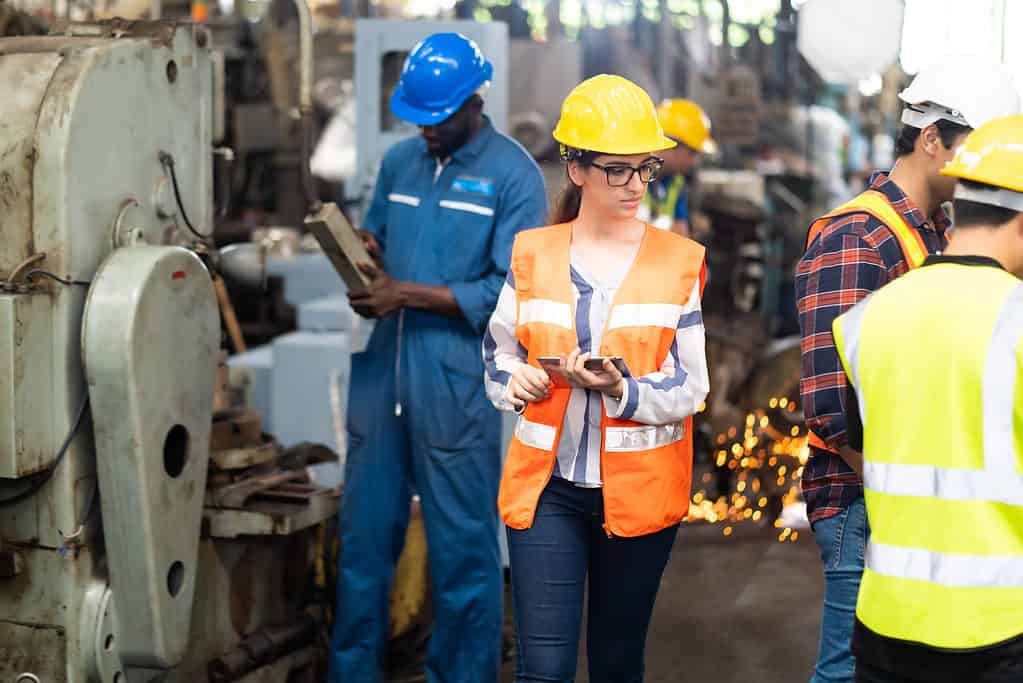
So, we’ve illuminated the industries and the approach itself, but why should you use FMEA? If you’re an adherent or certified in Lean Six Sigma, you certainly understand the necessity for quality in your deliverables. An organization lives and dies by customer trust. As such, when you betray that trust, you’re in a world of hurt.
That said, risks and points of failure are common occurrences in any industry. Depending on your organization, you might already be leveraging something like FMEA when it comes time to remediate issues.
Simply put, FMEA matters because it gives an effective and comprehensive means of cataloging, ranking, and remediating potential failure points. It can be used during service, design, or manufacturing itself.
Other Useful Tools and Concepts
We’ve spent a fair amount of time talking about FMEA today, but what about other concepts and tools to help your organization? One way of determining the root cause of a problem is the use of Ishikawa or Fishbone diagrams. Our comprehensive guide on the subject takes a close look at how to create and use them in your root-cause analysis.
The Harada Method is an approach meant to increase self-reliance in your employees, but how does that apply to other tools in Lean Six Sigma? Thankfully, we’ve got an article that answers that question with ease.
Finally, you might want to consider learning how SIPOC is used in modern manufacturing. The SIPOC diagram is one of the most important tools at your disposal when it comes to designing effective and reliable processes. Knowing how it applies to modern industry is worth its weight in gold.
Conclusion
FMEA is one of the handiest tools you have at your disposal when it comes to guaranteeing quality in the long term. It does require a fair bit of legwork to properly implement. However, that’s certainly worth the effort when you consider delivering consistent quality regularly.
It differs from other approaches where you’re rectifying issues after they’ve already arisen. You can certainly use it in such a capacity, but it will certainly depend on your applications and needs. Organizations succeed when implementing it during production and the design stages of projects, as well.
That said, your organization will likely benefit from adhering to FMEA. Since it is a plan driven by data, you can leverage that historical knowledge later on to know what steps were taken. Simply put, account for failure in your organization by leveraging FMEA.
The image featured at the top of this post is ©Ground Picture/Shutterstock.com.