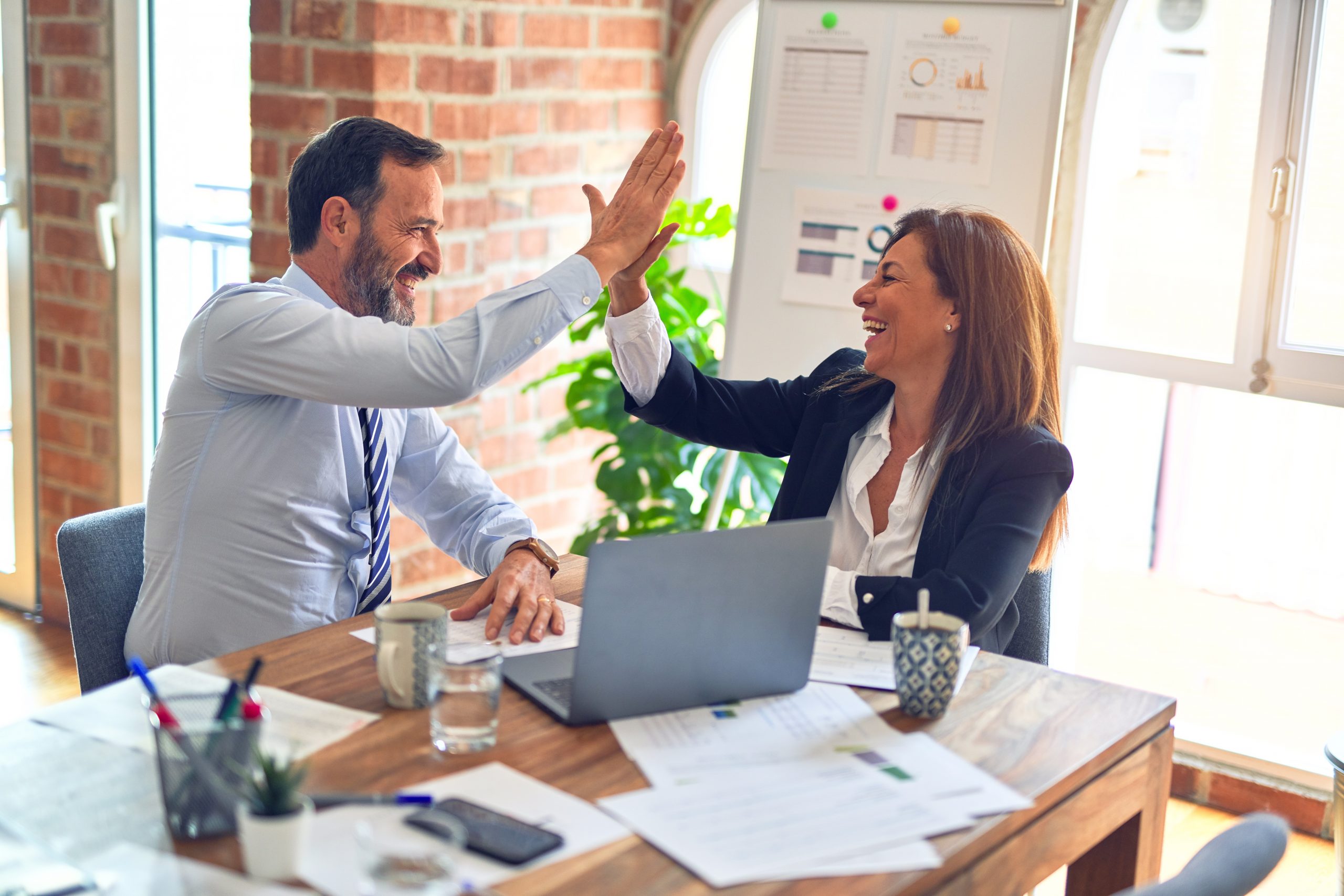
In the Six Sigma methodology, the equation Y = f(x) shows that the output (Y) is dependent on several variables (x). The same can be said about cycle times for process improvement projects. The correct variables mean improved project cycle times.
By Eva Zaccaria
In teaching the Six Sigma methodology to Green Belts, Black Belts, Champions and others, the equation Y = f(x) is referenced to illustrate that the output (Y) is dependent on several variables (x). The same can be said about cycle times for process improvement projects. In organizations that use Six Sigma as a tool for creating change, there is the expectation of the shortest possible project cycle times. However, the correct variables need to be in place to meet those expectations.
Adopting Six Sigma as a business tool requires forethought, planning, training and cultural adaption. Preparing for a process improvement project is equally important. Using the following 10 variables and inputs can improve project cycle times.
1. Establish within the organization why change is needed and why Six Sigma is the management tool chosen by the organization: As with any change initiative, it is important to understand the business decisions driving improvement; and the adoption of the Six Sigma methodology for change must be culturally understood and accepted to be successful.
2. Integrate Six Sigma as a management tool for doing business rather than doing a “program,” “initiative” or “effort”: Six Sigma is more than just project management. Steering away from words like “program” and “effort” can help remove resistance or barriers to change. Six Sigma’s customer-focused, fact-oriented, data-driven culture can positively transform the way an organization does business.
3. Define who the advocates for change are and ensure they have the right level of influence and decision-making authority, as well as accountability: Improved project cycle times require that change agents can make decisions effectively and in a timely manner. This includes having the appropriate Champions aligned with the selected project. (Do they have skin in the game? Can they influence/implement the change?) Also, project leaders selected must possess the change agent competencies needed for successful and sustainable results.
4. Ensure that the processes selected for improvement benefit the organization in terms of its strategy and objectives: Change for the sake of change can be detrimental. Any program should always support an organization’s strategy, resulting in enhanced customer (both internal and external) satisfaction.
5. Go after the easiest opportunities for success to demonstrate the use of Six Sigma and that results can be delivered: It is not all about transformational change. Cultural change and acceptance of Six Sigma as a part of doing business relies on quantifiable success. The more an organization experiences successful results, the more it can sustain continuous process improvement. Quick wins can create and motivate advocates for Six Sigma, and prove that new methods for creating change work better than previous methods.
6. Encourage and reward risk taking and creative and forward thinking: Creative thinking is simply the process of coming up with a new idea. New ideas are risky. However, creating change requires implementing new ideas. And sustaining continuous improvement requires ongoing creative thinking – continuous measurement, analysis and improvement – which is the basic Six Sigma DMAIC process.
7. Prepare to expand the change effort by leveraging data, solutions and lessons learned from initial improvements: This can include broadening infrastructure, policies and number of change agents to support successive rounds of improvement, continuing to enhance project cycle times. Another key consideration is whether the organization’s infrastructure supports and rewards change.
8. Train change agents for superior performance: Change cannot be implemented and processes cannot be improved without the contributions of change agents. Training is the first step in creating confident and competent change agents. The timing of training delivery should be aligned with the launch of the process improvement project; and the activities and tools used in training should be meaningful to project leaders within the contest of their projects. Additional training modules also should be aligned with the progression of projects.
9. Recognize and reward change agents for superior performance: An organization should recognize that both technical skills and leadership skills are a powerful combination. Employing some tactical techniques will reward change agents with the right attitude. This begins with setting stretch business goals. Embed goals associated with change in performance management and bonus programs. Speak openly about what is not working or where performance gaps exist. Build career paths for change agents as future leaders.
10. Follow an execution checklist: Once the infrastructure, training and project prioritization is completed, there are key steps in ensuring that a process improvement cycle stays on track and on time. Projects should be scoped according to the desired time frame for completion and the availability of data. All key stakeholders should be identified and engaged, as well as appropriate subject matter experts. Project leaders should have sufficient time to work on their projects. There should be constant communication of progress and challenges. Structured coaching sessions can be facilitated through scheduled, ongoing weekly meetings. And finally, scheduled tollgates should be on the calendars of required attendees.
Process improvement projects progress when project leaders understand, support and are accountable for the mission of the project they are leading. Understanding comes after receiving the appropriate level of training in the DMAIC methodology, change management and project management. Also critical for successful project leaders is a mentor who is available, supportive, knowledgeable and experienced in change management, Six Sigma and the business. Support from the process owner/Champion accountable for the goals and objectives of the project is key in achieving optimal cycle times. With these variables positively addressed, the output of the process – in this case project cycle time – can easily meet and exceed expectations.
About the Author: Eva Zaccaria is an independent change leadership consultant and certified Master Black Belt currently representing DeLeeuw Associates, a division of Conversion Services International. She specializes in Lean Six Sigma deployments, training and coaching. She has more than 18 years of experience in the financial services industry, serving in various senior leadership roles in quality and operations for J.P. Morgan Chase & Co. She can be reached at [email protected].