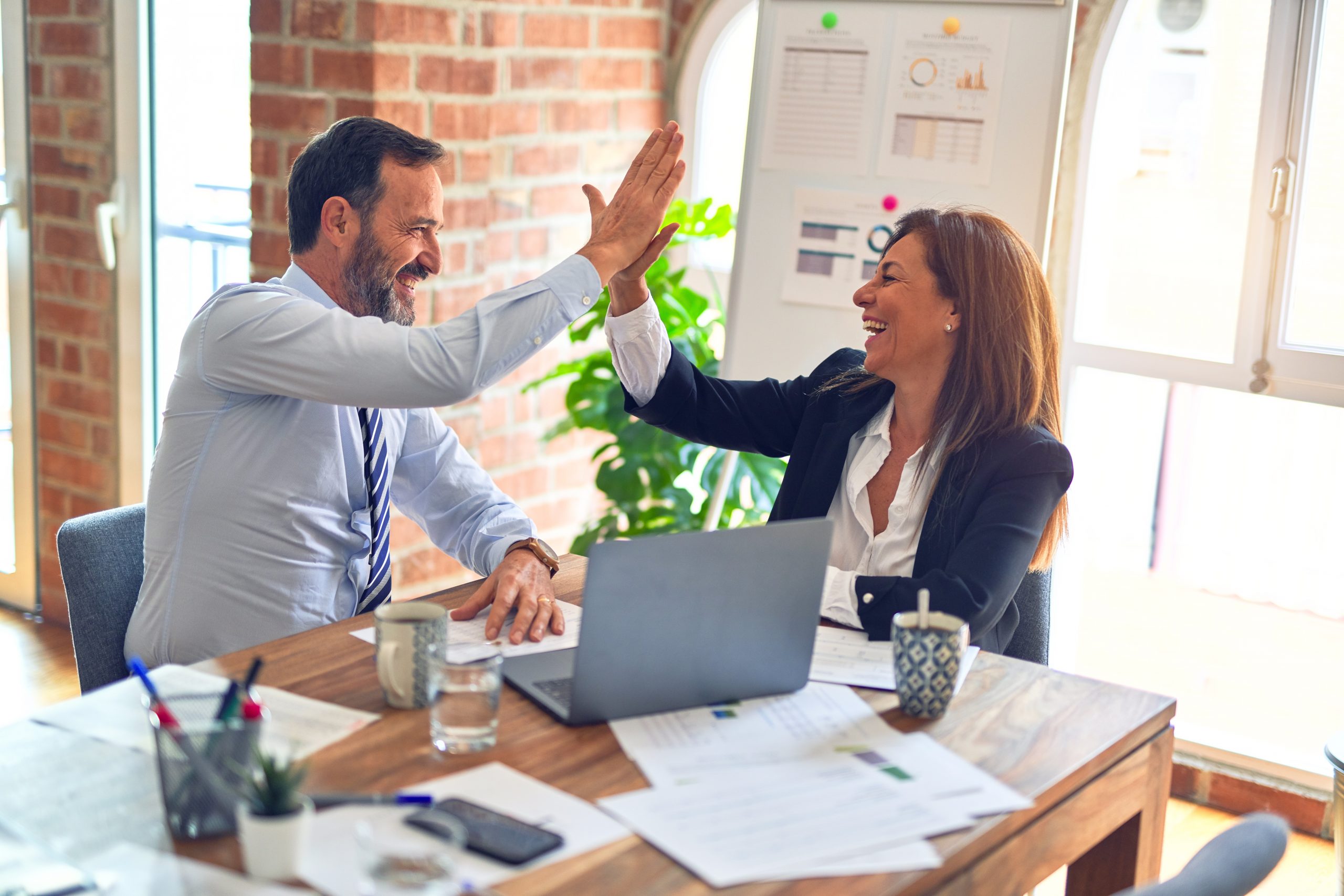
An internal audit by a team using Lean Six Sigma tools solved the mystery of what happened to about $1 million of a liquid chemical “misplaced” at a global chemical company. Case study shows how the team used a Kaizen event and DMAIC methodology.
By Leah Lutz
Imagine the chagrin that a supply chain team at a global chemical company felt when it realized it could not account for about $1 million of a liquid chemical. A month of investigation led nowhere. The team was unable to say for certain whether the material was actually lost, had been improperly accounted for in the books or was missing as the result of theft.
The team had a pet theory that the loss had occurred three years prior during the acquisition of a storage site. But two external audits did not support that idea.
That is when the operations director stepped in, requesting that an internal Lean Six Sigma consultant put together a team of experienced, well-respected employees to research the loss, prove or disprove the root cause theory, and come up with recommendations to prevent a reoccurrence of the problem.
At this point, the traditional approach would have been to assemble a team and then have meetings for a period of weeks or months to gather and analyze data. This company did not want to wait that long for results, so it chose to have the team work fast and intense through a week-long Kaizen event. The goal of a Kaizen week is to complete the first four improvement phases – Define, Measure, Analyze, Improve – so the team can then hand off tested improvement ideas to the process owner who will be responsible for full-scale implementation and the Control phase.
Brainstorming Theories and Gathering Data
During the Kaizen week, the team began by brainstorming possible reasons for the loss of material. Top ideas included:
- What the team labeled its “organization theory” – the fact that three years before the loss was recognized, the terminal, tank farm and material were acquired from another company. It was possible that the material was actually lost or mistakes were made in the logs during the acquisition.
- Multiple “short” deliveries that were not recognized, but which accumulated over time to a noticeable level.
- Leaks in the material storage and/or transport systems.
- Flaws in the mechanical system that moves the raw material into the process for conversion to another process.
- Flaws or transactional errors in the material tracking system used to record material consumption.
- Internal theft of material.
Once the team had its ideas down on paper, it went on to map the material inventory management processes. The team also used measurement system analysis (MSA) to evaluate the measurement system equipment, processes and people responsible for generating inventory information. Last, the team “walked the process,” doing a visual inspection of the material flow path and reviewing consumption logs.
A schematic of the process and measurement points is shown in Figure 1
|
The team’s maps, MSA and inspection allowed it to eliminate the theories Nos. 2, 3 and 4. That is, short deliveries, leaks in storage or transport systems, or flaws in the charging system were not the cause of the problem. This left the team with three additional theories to investigate and the risk of having to return to the blackboard if the data disproved those theories as well.
The team began its next phase by reviewing transactional records for the previous three years. It verified that the records were consistent with the process norms (material input equaled converted material output equaled material sold). The team could not identify any variation that would account for $1 million of lost material, so it eliminated the theory that transactional errors in the tracking system was the root cause of the problem (No. 5).
That left only two competing theories – the organization theory or internal theft. Because of the sensitivity of the theft issue, the team decided to wait and tackle it only if it had to (i.e., if the organization theory ended up being disproved).
Exploring the Organization Theory
The team’s organization theory was that the material was inaccurately accounted for when it was acquired, three years earlier, and the problem had remained hidden (undetected by two external audits) until now.
Analysis of this theory began by collecting all inventory and audit records and documenting the receipt and tracking process, which is shown in Figure 2.
|
Working from the assumption that the loss had actually occurred three years prior, the team began to review the process by which the material was purchased and transferred during the original acquisition. The company thought it had acquired material volume equating to about $2 million at the same time it acquired the new equipment. But the investigation showed that material being conveyed by barges had been double counted and that only $1 million of material had been transferred during the acquisition. How had this happened? It turned out that the company and the seller had determined the material value for the selling price from an inventory record that included both the volume of liquid material being held at a tank farm and that from an incoming barge volume. But at that time the barges had not docked yet. Approximately two days later, when the barges docked and were unloaded, the material was counted again – and that volume was added to the purchase volume a second time. (Note highlighted box in Figure 3.)
|
Identifying this fact led to the question of why two external audits during the last three years had failed to recognize the “missing” material. One of the audits had occurred within six months of the acquisition. The team then used the receipt and processing of material process map (Figure 2) to recreate raw material transactions during the periods when the two external audits were conducted as well as during the rest of the three-year period. The team realized that:
- A flaw in the process of tracking and recording incoming material managed by supply chain associates managing the material receipt process created points of significant variation in volume (actual versus documented) over short time periods. These periods occurred while barges of material were in transport from the ship to the terminal.
- External audits occurred during time periods when the material was in flux causing any short-falls to be hidden by the process.
- Recreation of the material inventory in the tank farm and barges and audit information during the critical time periods allowed the team to assemble demonstrable proof that the audit results were incorrect.
Team’s Work: Positive Outcomes
As a result of the team’s work, the company changed, formalized and documented how material was tracked and recommendations for improvement to internal audit practices were generated. The overall outcomes included:
- The new documentation is now used to ensure standards are followed.
- The company found a low-tech solution (using Excel spreadsheets) to allow more accurate tracking and management of incoming material inventory.
- Training was revised and staff members were given additional training on material tracking procedures, spreadsheet usage and proper transaction procedures for materials within their supply chain software.
As the team discovered, most of the time, external and internal audits depend on the knowledge of the process provided by staff. Assuming this information is correct without verifying its accuracy can lead to the inability to identify large problems in the processes being audited.
The team also found that process mapping, reviewing the maps for accuracy, and understanding how the process works are simple steps that can reduce the risk of overlooking significant process errors. If process maps are not readily available, a company should take the time to develop a high-level map based on experience that can be used by internal or external auditors to drive accuracy and effectiveness. Having such a map can make it easier to reference specific process steps or elements when validating results and verifying transactional information.
About the Author: Leah Lutz is a consultant with George Group who specializes in supporting Lean Six Sigma deployment in the federal sector. Her experience spans supply chain, operations, finance and strategy. She has coached and led teams to success on both technical and transactional projects. She can be reached at [email protected].