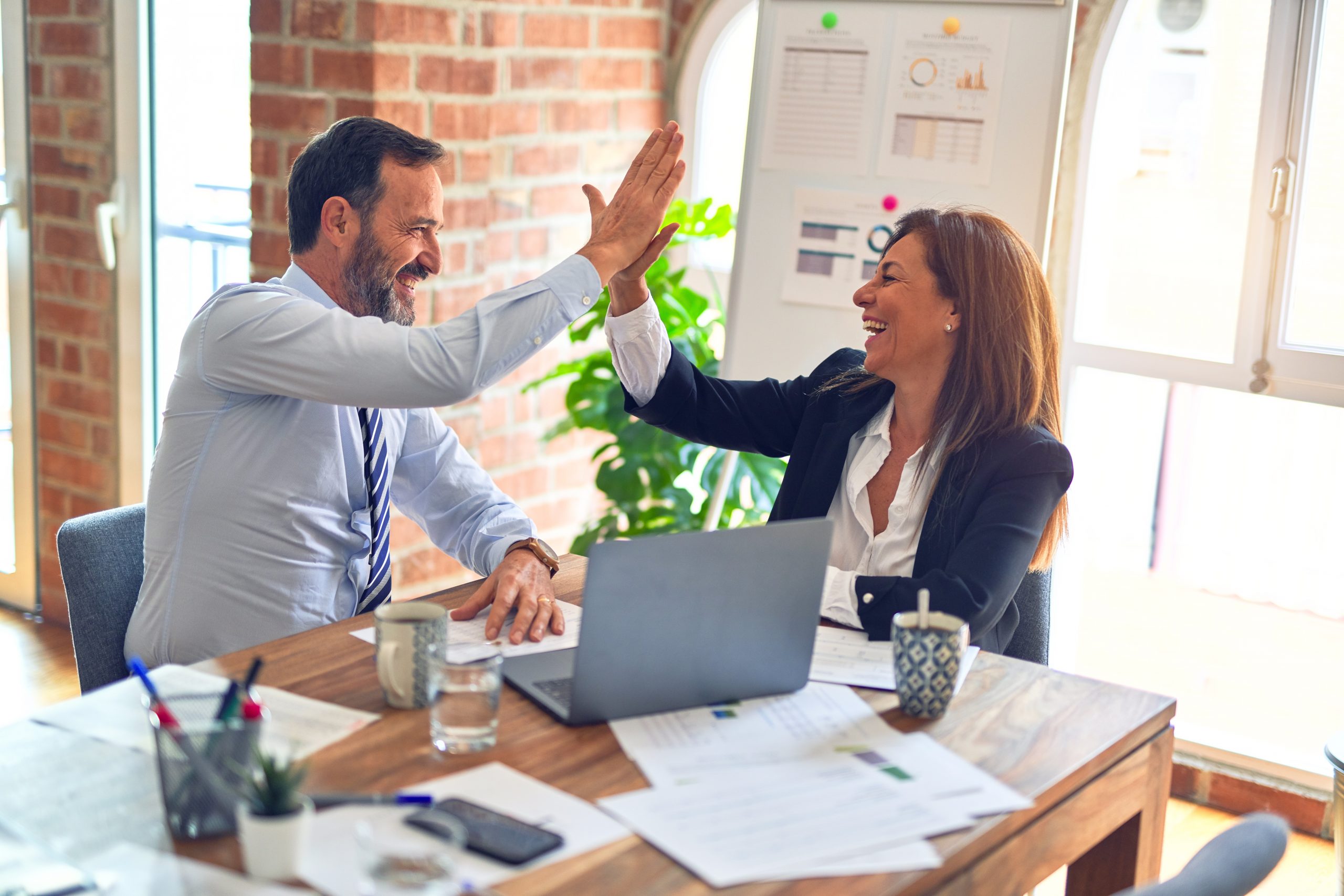
A Six Sigma initiative can be wildly successful or it can sadly fail. The reasons are found in 10 major points critical to the success of a Six Sigma deployment. The points also are in the list of the 10 ways that a Six Sigma initiative can fail.
By Gopal Ranjan
The returns from a well-deployed Six Sigma initiative can be richly rewarding. The results of many business organizations stand in testimony to that. But the opposite also is true. Many organizations have started Six Sigma initiatives with much fanfare only to have the deployment eventually fizzle out miserably. So what goes wrong? Why are there conflicting experiences with Six Sigma initiatives? The answer lies in the basics of deployment.
Ten major points are critical to the success or failure of a Six Sigma deployment. Here the points are outlined as the 10 ways that a Six Sigma initiative can fail:
1. Lack of Commitment from the Top
Commitment to Six Sigma from top leadership means 100 percent commitment, or in other words walk-the-talk. Paying lip service or expressing support to the initiative only in mailers or meetings is not sufficient. The commitment needs to be visible through actions. Top management should embrace the principles of Six Sigma in such a manner that it becomes a way of life. In many organizations, the CEO thinks that Six Sigma is the responsibility of a select few Black Belts and Master Black Belts. That is one sure route toward a failed Six Sigma program. The Champion or deployment leader should have a fair knowledge about the methodology. A deployment leader who himself does not know much about the methodology would hardly be expected to inspire confidence in others.
2. Part-time Black Belts
Many of the organizations that fail to realize the true impact of Six Sigma treat Black Belt positions as part-time jobs. It is essential that Black Belts be full-time positions. Black Belts require a lot of skill, both technical as well as behavioral. The position needs to concentrate full-time on improving the performances in areas that are linked to strategic objectives of the organization. A typical return expected from each Black Belt project is several times that person’s annual salary, and a number of projects can be completed each year. A part-time Black Belt is really only the equivalent of a Green Belt. A business should select the best of its people to undergo training and certification as Black Belts. Black Belt positions should be used as a step in the grooming of the organization’s future leaders.
3. Projects Not Linked to Organizational Objectives
For Six Sigma to yield the benefits desired, projects undertaken must be aligned to the strategic objectives of the company. A democratic approach does not work here. Project selection must use a balance of top-down and bottom-up approaches. Localized improvements that are disconnected from the strategic objectives could be more harmful than beneficial to the organization.
4. Focusing on Quantity Instead of Quality
Although a wider participation in a Six Sigma initiative – especially at the start of the initiative – is desirable, this should not lead to the quality of projects being sacrificed for quantity of projects. A large number of projects completed might look good, but the impact of the projects undertaken is much more important.
5. No Review Mechanism
It is almost universal that whatever is not reviewed degenerates into disuse. Projects and the progress of the improvement initiative if not reviewed regularly will lead to the momentum of the initiative fizzling out. Getting starting again would then be an uphill task. There should be a sound governance mechanism to ensure that the projects get reviewed regularly, and the projects progress in a timely manner. Review committees should include senior management.
6. No Visible Reward and Recognition Mechanism
There needs to be a visible reward and recognition mechanism to the initiative. Rewards can be monetary as well as non-monetary like public recognition, certification, etc. Some organizations link incentives to the initiative.
7. No Infrastructural Support to Teams Working on Projects
Teams working on projects require a lot of support in driving their projects. This means infrastructural support like statistical software, mentoring supports, etc. Availability of these reduces a lot of difficulties that teams face during the life of their project. Organizations with deployment leadership that expect project teams will manage on their own are doomed to failure.
8. Copy-and-Paste Deployment
Deployment of any initiative requires a lot of sensitivity toward an organization’s prevalent environment. Just a copy-and-paste kind of approach, wherein one reads a book and tries to deploy, does not work. One needs to be cognizant of the specific needs of the organization and customize the deployment accordingly while keeping the basics intact. Also, Six Sigma is quite different from other methodologies like Kaizen, TQM, Quality Circles, etc., hence requires a different approach. What worked with these methodologies may not work for a Six Sigma deployment.
9. Too Much Insistence on Statistics and Tools
Although Six Sigma as a methodology boasts a multitude of robust statistical tools, one needs to be wary of getting trapped by these tools. The practitioner needs to use these tools to drive improvement and not the other way round. In fact, according to one survey, 60 to 70 percent of improvement projects do not require advanced statistical tools. While driving projects, the larger goal of improvement and the essence of the methodology should be kept intact. Using tools just for the sake of using them because they are part of the Six Sigma toolkit is not smart or efficient in terms of time. Flexibility is important.
10. Expecting Too Much and Too Soon
While Six Sigma deserves the positive reputation it gets from the larger returns it provides to the bottom-line, it is not wise to expect too much from the very start of the initiative. Like all major initiatives, it requires a good amount of investment. This investment typically starts giving significant returns about the third year. A business organization should not be discouraged if returns are slow initially. Since Six Sigma is focused on reducing variation and improving performance and is a system-oriented methodology, it takes time for the returns to grow and stabilize. Expecting phenomenal results too soon may discourage top leadership and result in those driving the initiative become defensive. These two factors together could put the deployment in jeopardy.
These are the major pitfalls that one needs to avoid while deploying Six Sigma in an organization. If those deploying Six Sigma keep wary of these, the initiative is likely to be much smoother and more successful.
About the Author: Gopal Ranjan has 12 years of experience in consulting in the field of breakthrough improvement methodologies like Six Sigma, balanced scorecard and design of quality management systems. He has deployed these methodologies in manufacturing and service industries. He can be reached at [email protected].