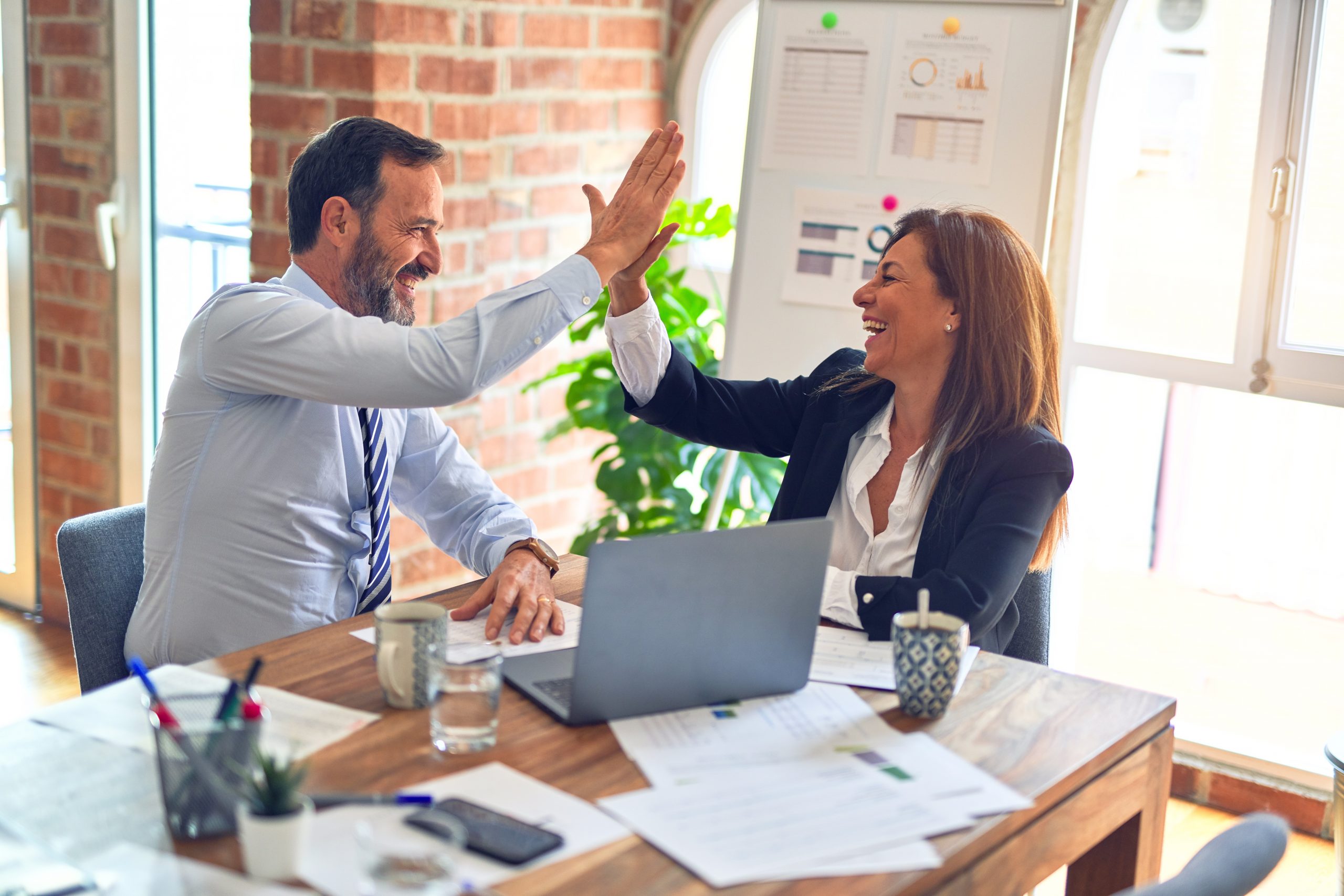
Overall equipment efficiency (OEE) – the percentage of production time that is actually productive – has its roots in manufacturing where all production ceases when the equipment is offline. It is possible to gain a greater understanding of how effectively a system is operating, however, by expanding the concept to include all process steps in the work done. By considering all policies, processes, systems and resources to be part of the “machine” that creates value, OEE can be used to extract and communicate significantly more insight about the nature of the work being done.
OEE is simple and practical. It focuses on where time that is needed to be productive is lost – rather than just assuming that these losses are a function of how the employee works. In most systems, the differences between individual productivity, although numerically inflated, are practically trivial when compared to the built-in losses inherent in the workflows and systems we use. OEE places these designed-in constraints front and center so that they can be addressed, rather than blaming employees for minor differences.
The overall concept of OEE is elementary. There are only so many hours in a day and every hour not devoted to productive work reduces the overall efficiency. Furthermore, since most of these losses are not random or at the discretion of the individual associate, the system and its assumptions must be looked at. When reducing the built-in losses, more bandwidth is created. More can be achieved by changing the assumptions than can be managed out of the remaining few hours of potentially productive time.
Formally defined, OEE is the product of availability, performance and quality. When one or more of these three drivers is compromised, productivity must fall.
OEE = Π (availability * performance * quality)
Availability is simply the time that could be devoted to productive use. Often much of a day is consumed by various planned and unplanned activities that limit how much work can be accomplished in a given day. By formally detailing these times leadership is provided with valuable insight into why so many hours must be consumed to generate a given amount of work.
Consider the example data shown in Figure 1.
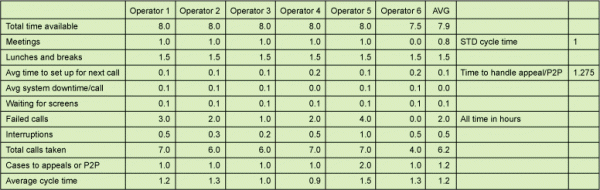
This data shows that much of the day is not available to do productive work. Putting that data into a waterfall chart quickly demonstrates to leadership where the time available is going. (See Figure 2.)
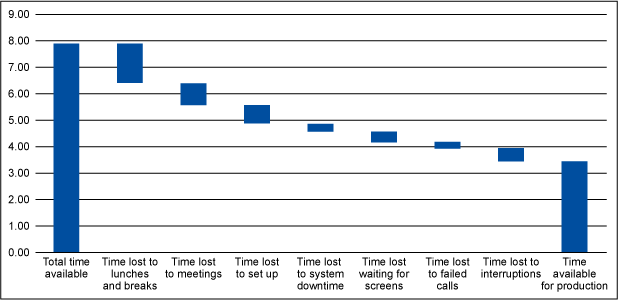
By looking at availability alone, more than half the work day (57 percent) is lost time that cannot be used for productive work.
Performance is the way the efficiency of the individual employees is typically measured. It is the measure of how well work is done relative to a standard. Typically performance is measured as the ratio of the individual’s cycle time to a benchmarked cycle time designed for the process. Alternatively, the individual’s cycle time with respect to takt may be measured. Either way, how well individuals do their jobs is being judged. To keep things simple, this time is converted to time lost due to performing at a level other than ideal.
or
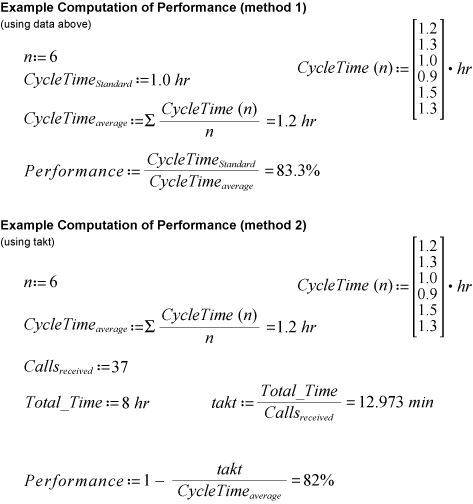
Since productivity becomes an abstract concept subject to arbitrary interpretation, it is best to convert this efficiency number to actual time by multiplying the performance by the time available.
Performance losshours = Performance * availability * total hours
In the provided example, this becomes:
Performance losshours = 0.82 * 0.43 * 3.5 hours = 1.23 hours
That result can then be added to the waterfall (Figure 4).
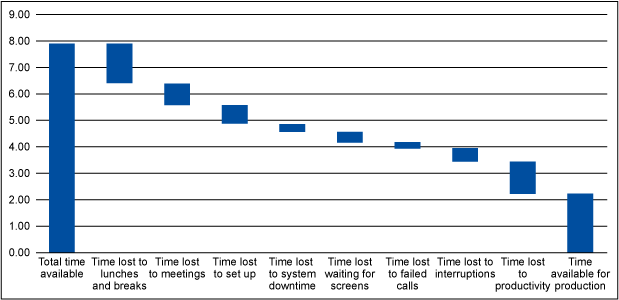
The final element in OEE is quality – the percentage of work which is considered to have been performed properly the first time (i.e., no rework), or the first-pass yield. In this example, first-pass yield is used because it is the goal to account for all the time devoted to rework and failed work in the system as a part of quality losses. (This may include appeals, peer-to-peer reviews, hand-offs to other functions, corrections of pervious errors and various other time-consuming tasks, some of which are not part of the value stream under study.) Since these rework tasks are large and often handled outside the function under study, do not be surprised if quality losses exceed the remaining time available. This is an indication that more work is being generated than accomplished by this function; it is part of the nature of transactional workstreams.
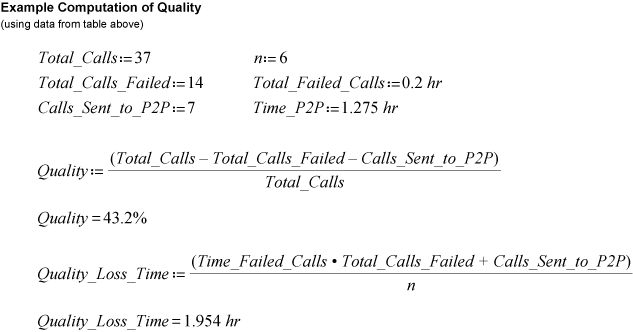
When this is added to the waterfall, the total of all of our productivity losses is visible (Figure 6).
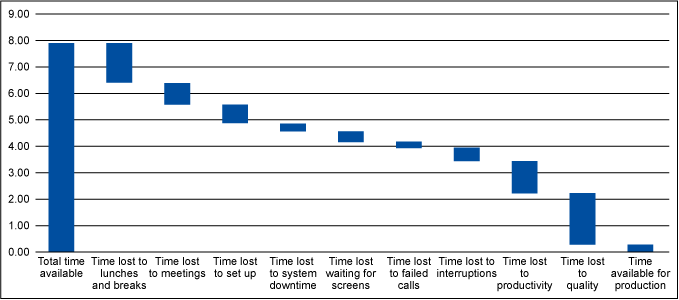
Here is a complication. Pure OEE would indicate that the process is actually performing much better than summing the losses does. When computing the pure OEE of the process,
OEE = Π (availability * performance * quality)
OEE = 0.43% * 82% * 43% = 15.2%
That number is much higher than what is compute when the losses are added. This highlights the importance of always working in hours lost rather than the summary statistics. The true OEE of this process comes from the waterfall chart and is the resultant time available divided by the total time. This highlights not just that almost all of the time is consumed in planned losses but also demonstrates where.
True OEE = 0.29 hours / 8 hours = 3.6%
This indicates that the system used to do this work is inadequate.
As shown, the additional insight gained with an OEE will uncover more opportunities to improve that work than the typical end-to-end audit or time study.