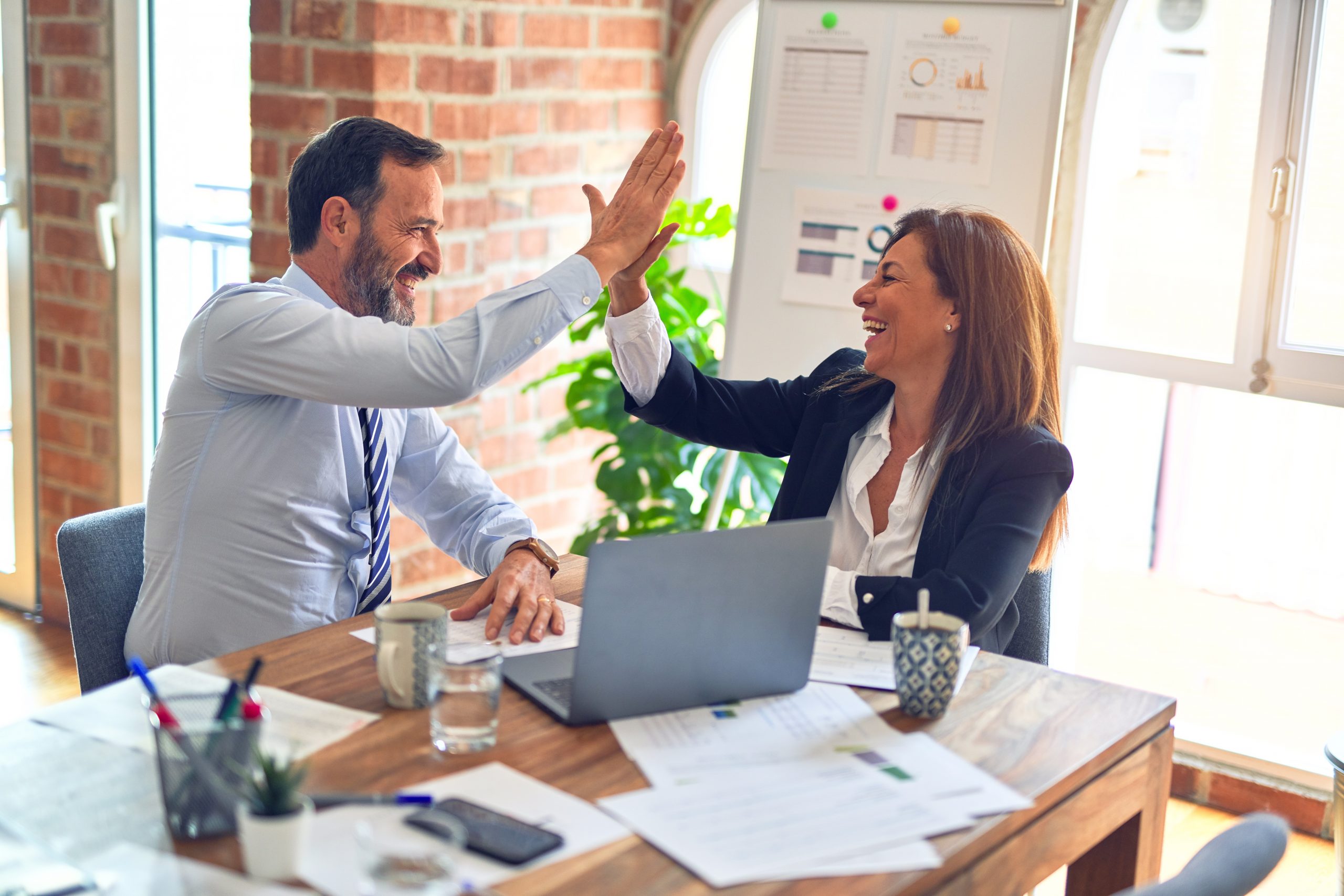
As parents of young children know, “Why?” is one of the most frequently asked questions they hear. And not just once. A girl asks, “Why is the sky blue?” and will proceed with further “Why?” demands to each subsequent answer for as long as the parent is willing (or able) to play along.
As frustrating as answering “Why?” questions can be in those circumstances, “Why?” can be the most critical question asked and answered when related to understanding a process.
In the context of process improvement, the 5 Whys is an qualitative approach to root cause analysis. It refers to asking, five times, why a failure has occurred in order to get to the root cause or causes of the problem. (Keep in mind that there may be more than one cause for any given problem.) In some cases, getting to the root cause will require asking “Why?” more or fewer than five times.

Analysis using the 5 Whys is typically performed by a team, requires no special statistical knowledge and makes the most of the collective knowledge of a team. And it is as simple as continuing to ask “Why?”
To learn more about 5 Whys and related topics, and to see examples of the tool in use, refer to the following articles and discussions:
- 5 Whys and 2 Hows
- Determine the Root Cause: 5 Whys
- Going Beyond the 5 Whys
- Is 5 Times Enough to Ask “Why?”
- The 5 Whys: A Simple Tool in Value Stream Analysis
- Who Developed the 5 Whys?
- Why Not Six or Seven Whys?
The three tools that are considered to be fundamental when starting a process improvement program are 5 Whys, process mapping and 7 wastes. To learn more about these tools and more, purchase the Lean Six Sigma Toolset Research Report at the iSixSigma Marketplace.