Tag: TIM WOOD
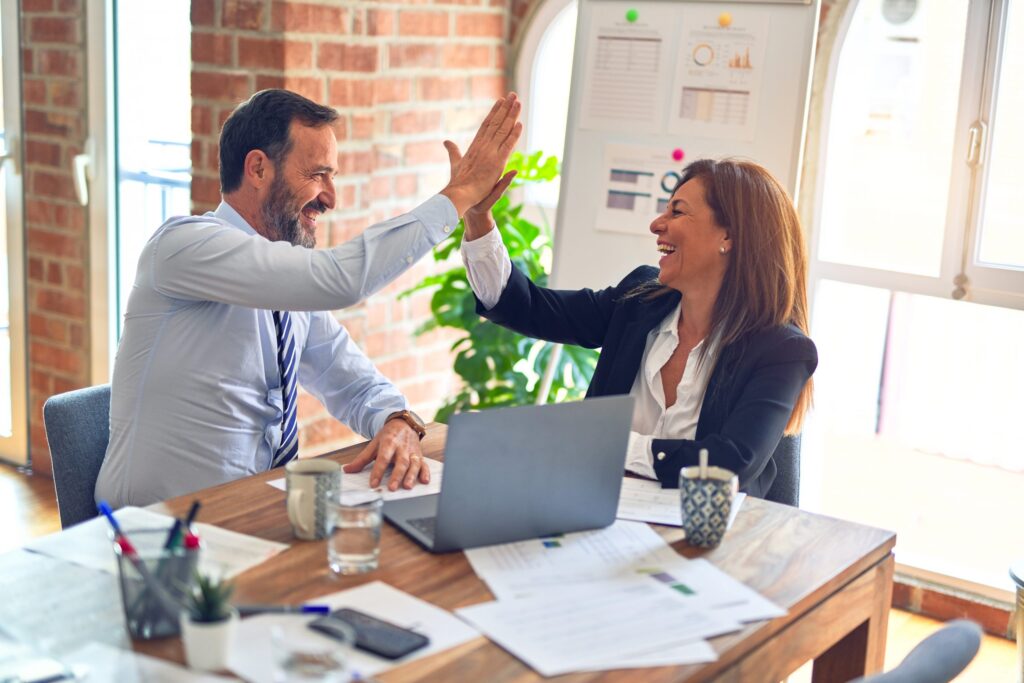
Beware the DOTWIMP: Beyond the Seven Wastes in the Transactional Process
Published:To improve the results of processes and make them leaner, practitioners need to identify which of the traditional seven wastes (or muda) are present in the process and take appropriate action. The seven wastes can be summarized with the acronym: DOTWIMP. D: Defect in the output, as identified in the eyes of the customer. O: […]
Read more ยป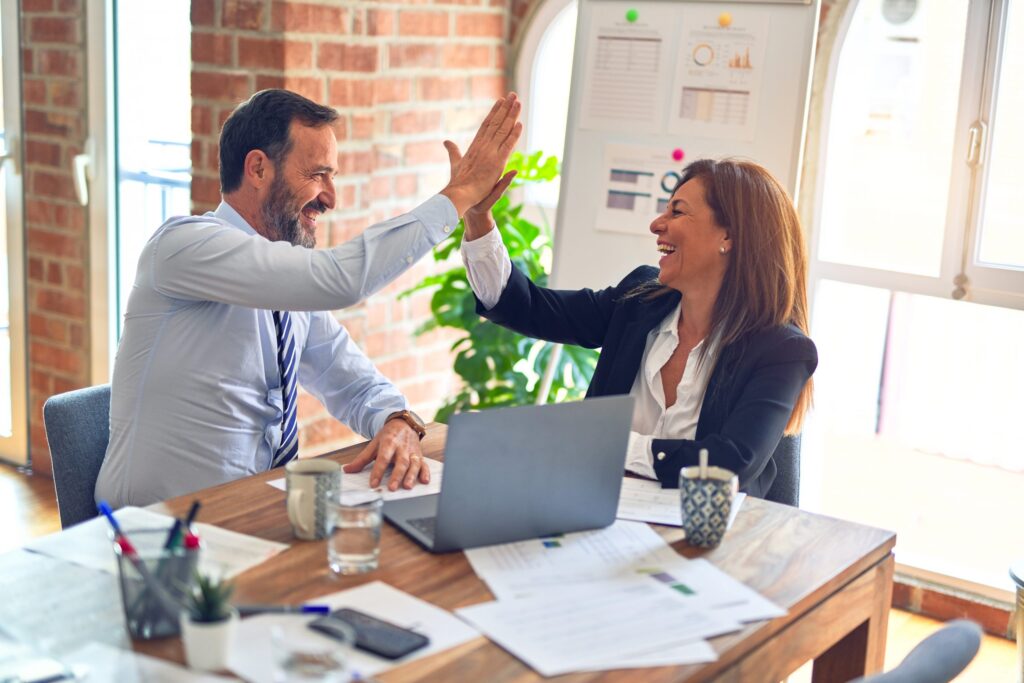
Lean Services: Doing Transactions Right the First Time
Published:In a service organization, the most efficient method for cutting waste is to attack anything and everything that is not done right the first time. This concept, known as first time right, involves making sure that all activities are carried out in the right manner the first time and every time. Examples include a customer […]
Read more ยป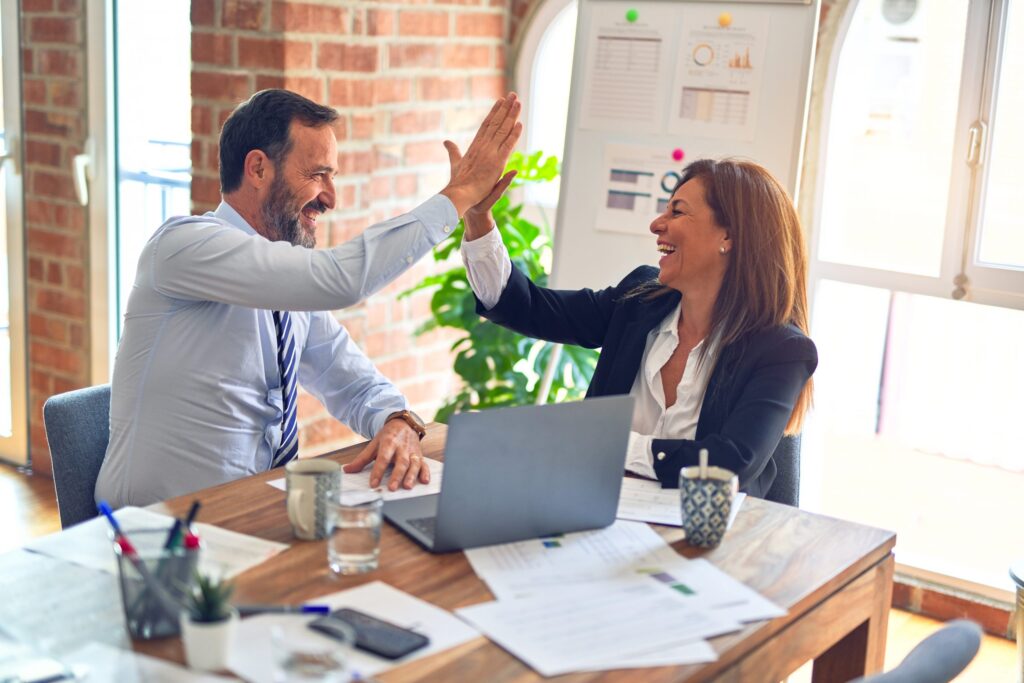
Lean: Relentless Pursuit of Product Value and No Waste
Published:Lean, like other process improvement methodologies, is based on the big idea from the 1980s that a business is composed of a series of processes, a value stream, that delivers value to its customers. A process is Lean if it uses only the absolute minimum of resources (material, machines and labor) to add value to […]
Read more ยป
Learning to Think Lean: 6 Steps with Review Points
Published:Organizations can profit from learning to think in terms of Lean, a philosophy that aims to eliminate waste. Learn the six steps to a strong Lean foundation, including detailed questions to ask at each step to review current status.
Read more ยป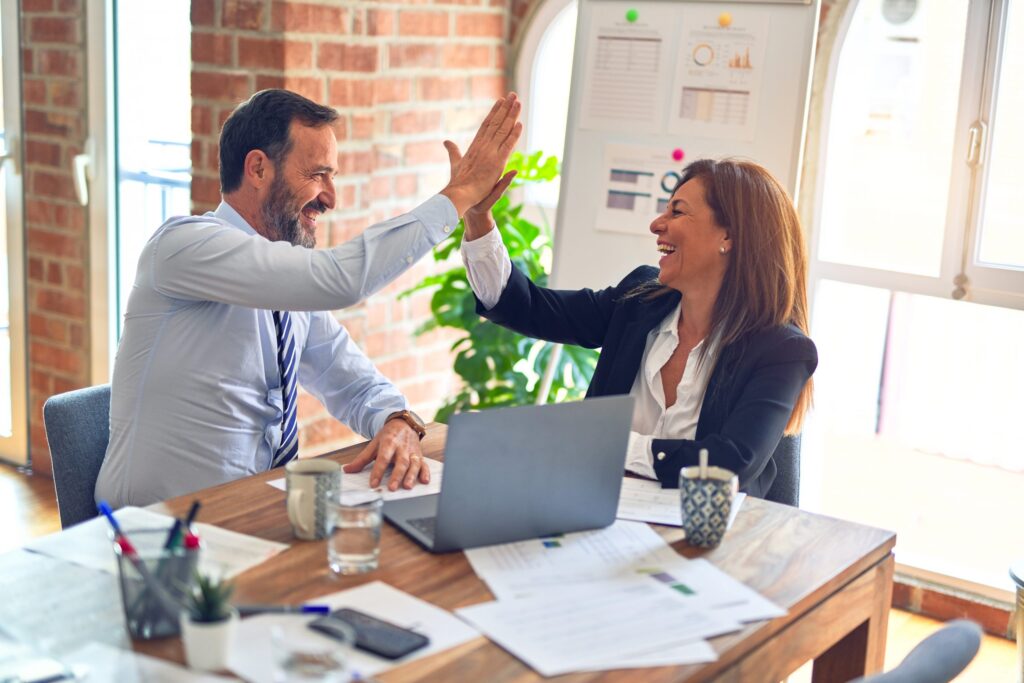
Learning to Recognize Process Waste in Financial Services
Published:One of the biggest challenges for Six Sigma practitioners in financial services is developing the ability to recognize waste. Imagine an “overnight pack” entering Bank One’s wholesale lockbox process for processing remittance payments. By the time it has been through every step, up and down the elevators, back and forth between departments, it would have […]
Read more ยป