Tag: root cause analysis
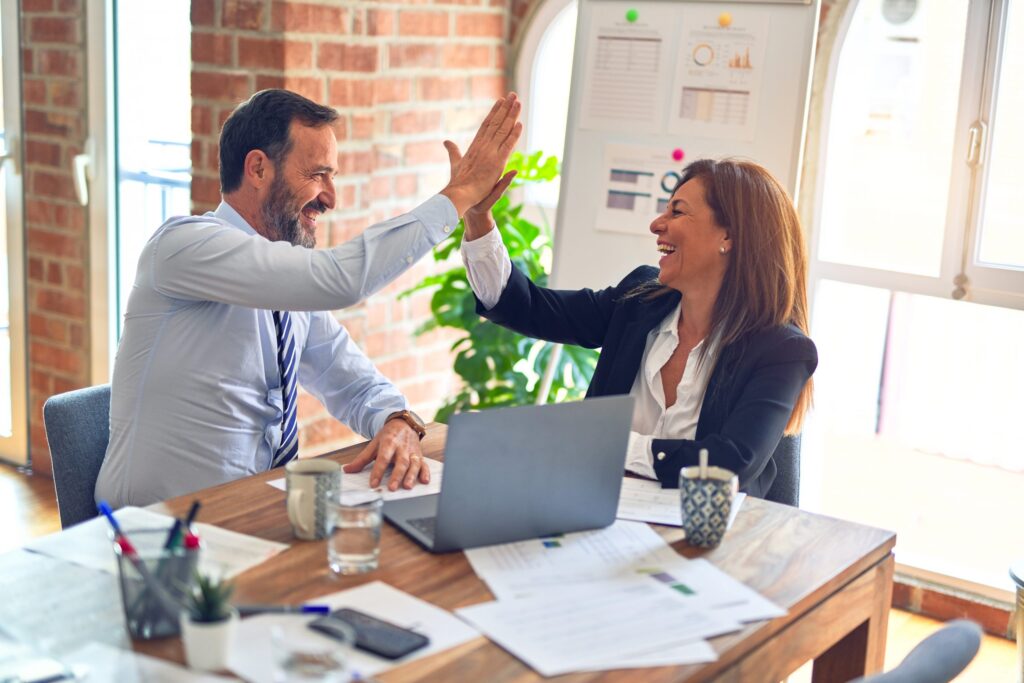
Current Reality Tree Helps to Identify Hidden Barriers
Published:Lean Six Sigma projects are a learning journey and, unfortunately, despite practitioners’ best efforts, projects can become delayed on their way to completion. A number of reasons may contribute to project delays, such as the occasional unforeseen organizational crisis due to business, operational or personnel issues. The conventional management response to delays is to arrange […]
Read more »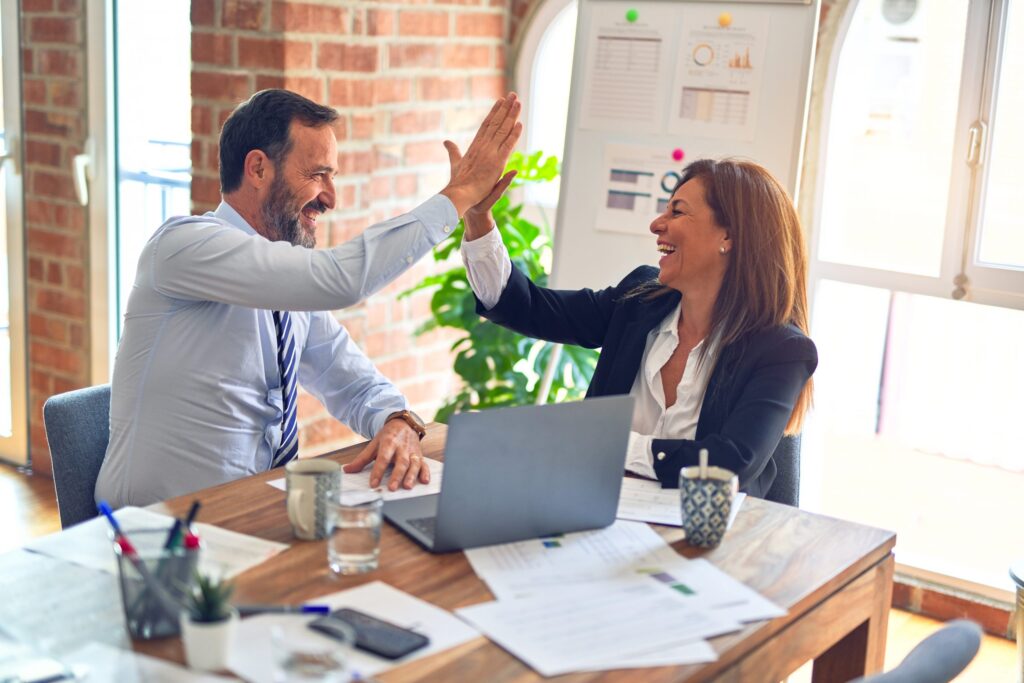
Reveal Assumptions and Find Root Causes with Webbing
Published:Six Sigma practitioners looking to clarify or explore a task, find root causes of a problem or develop their strategic thinking skills may want to consider using webbing, a valuable exploration tool. Similar to the 5 Whys, this tool encourages practitioners to ask a web of questions about a task or process in order to […]
Read more »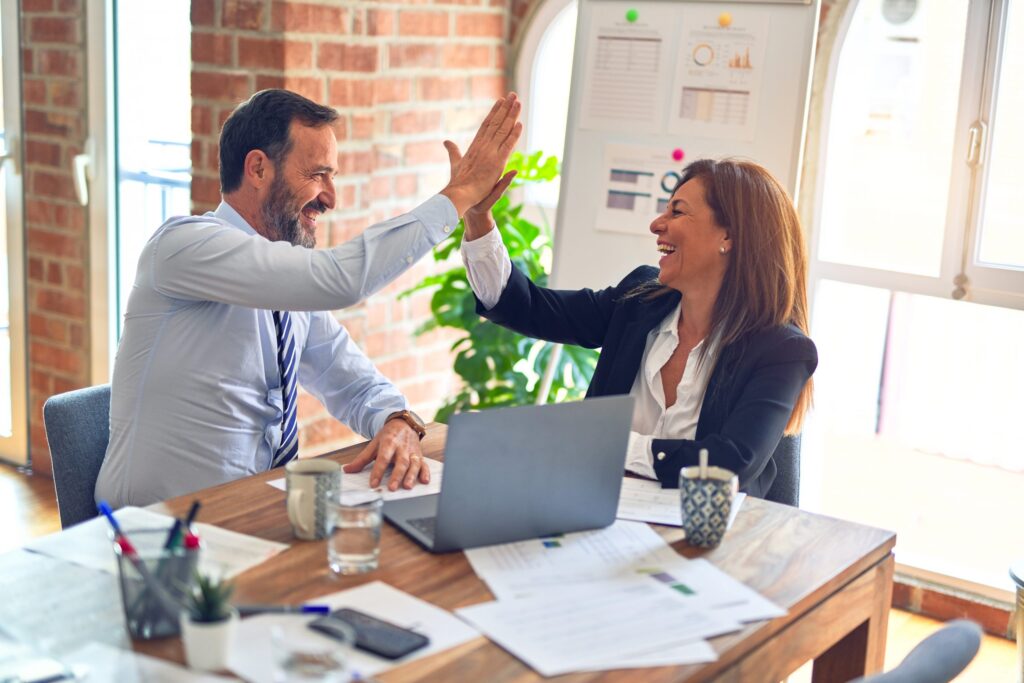
Teamwork and Creativity Help to Identify Root Causes
Published:In problem-solving methodologies, identifying potential causes is a crucial step between process mapping and data collection and analysis. It involves the best available process knowledge, as well as creativity. Creativity and team management tools, more often employed for solution finding than for root cause finding, can generate deep understanding of the process mechanics and help […]
Read more »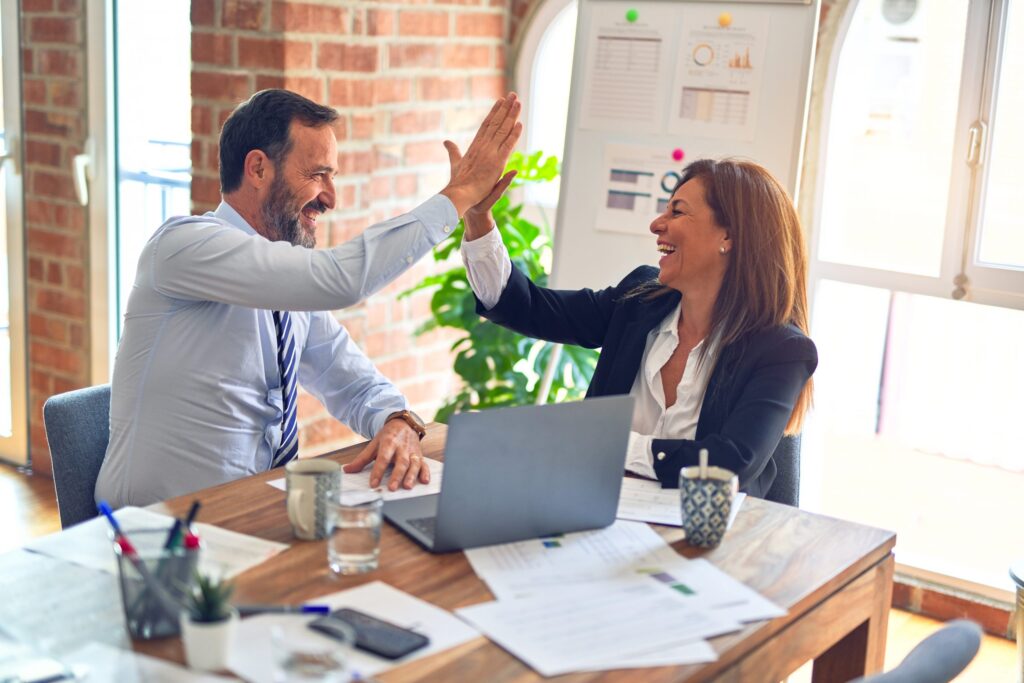
FMEA: Tool for Process Documentation and Discovery
Published:While the name of the failure mode and effects analysis (FMEA) concentrates on how a process fails, the real objective is to concentrate on assessing the effects and process controls for the root causes related to any given failure mode. Practitioners examine the root cause-failure-effect sequence by starting in the middle and working outward. During […]
Read more »
8 Basics of Lean Six Sigma for Manufacturing Firms
Published:It takes more than quick fixes, outsourcing and downsizing to consistently achieve growth and profit objectives. For companies to grow, they need to master eight basics of Lean Six Sigma.
Read more »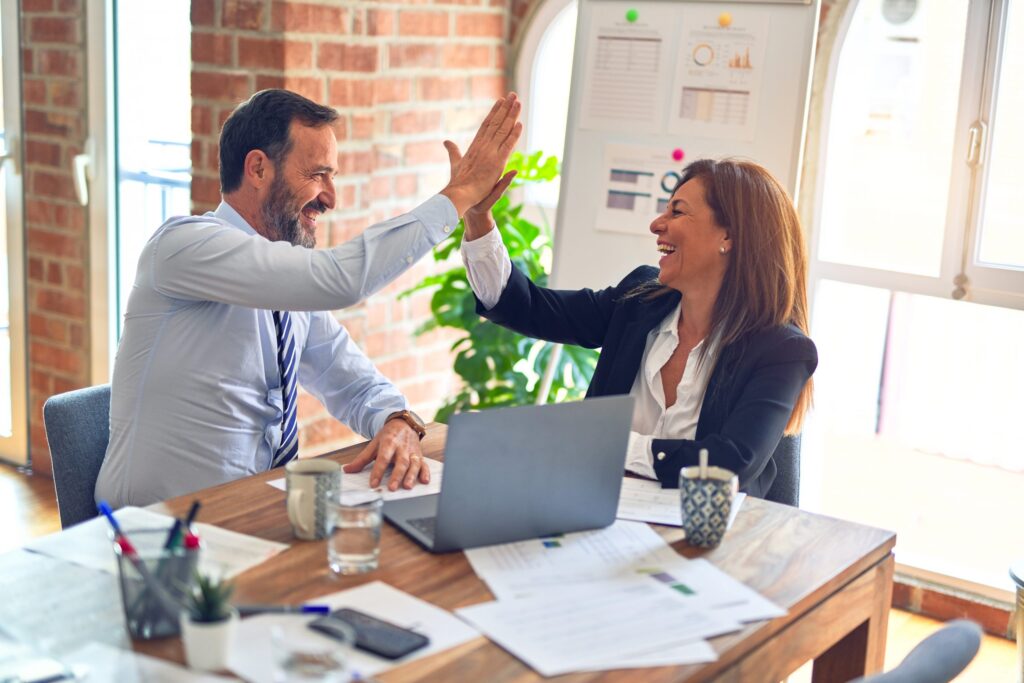
Basic Strategies for Avoiding and Overcoming Resistance
Published:The pattern is so predictable as to be universal. A leadership team announces to a company that they are going to launch Lean Six Sigma. The next few months are a blur of activity with executives and their direct reports scrambling to conduct an assessment, plan the deployment and determine how to recruit and allocate […]
Read more »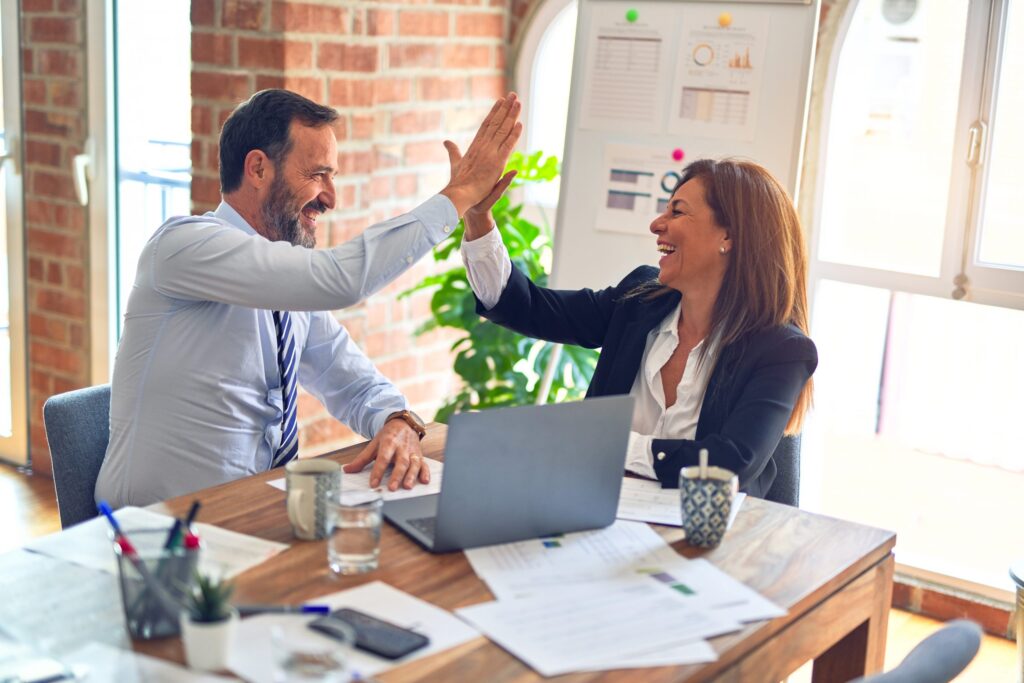
Making the Case for FMEA in Managing Software Projects
Published:Many times, a company is required to do a root cause analysis once a defect or bug is found in the software system it has developed and released to customers. Such an approach is not only costly, but almost without exception results in customer dissatisfaction. What is needed is a proactive approach to understand the […]
Read more »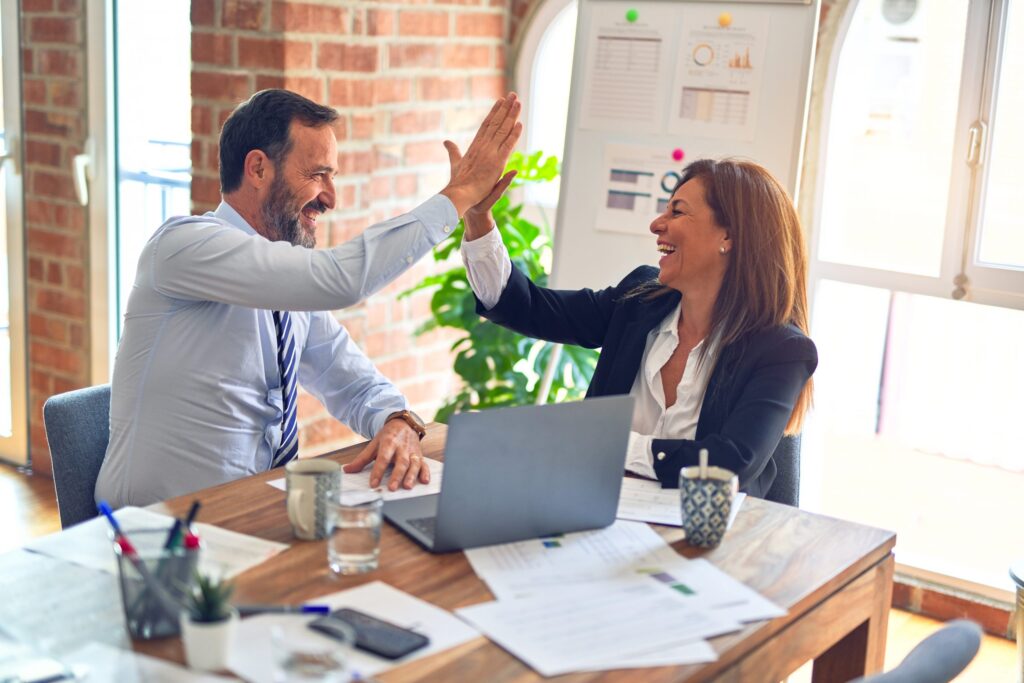
Bridging Functional Silos to Achieve ‘Customer Impact’
Published:During the Define phase, it is common that a project is made smaller and more manageable by limiting the scope of the business process it will address. This may, however, cause problems during the Measure and Analyze phases when root causes outside the project scope are found. An exploration of this issue is found in […]
Read more »
Solving the Dilemma Created by the No-Show Patient
Published:Patients who fail to show up for their exams interrupt the scheduling process and disrupt the delivery system. Healthcare facilities must control no-shows to realize process efficiencies and minimize missed revenue opportunities.
Read more »