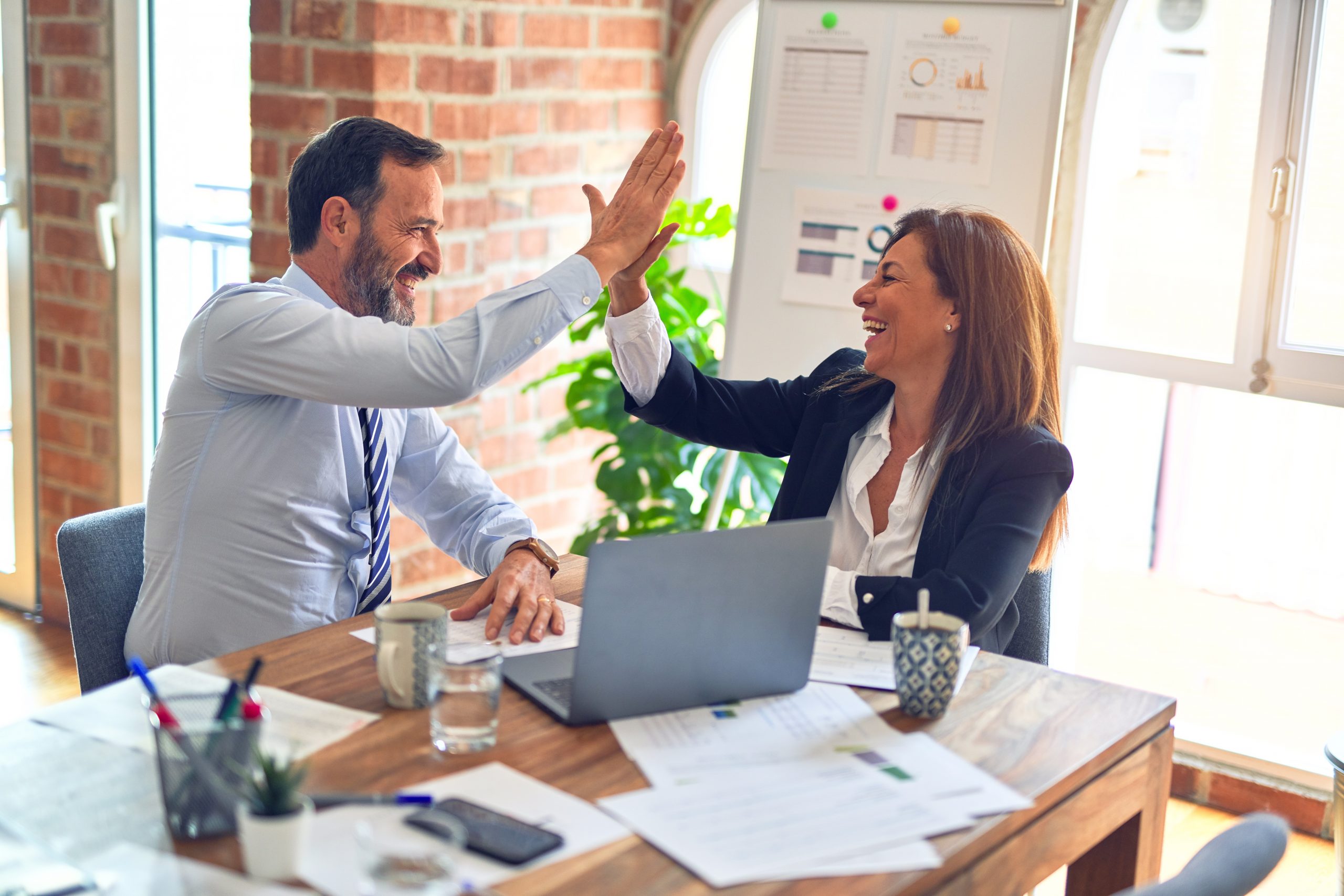
Many Six Sigma practitioners have asked how the Supply-Chain Operations Reference model, or SCOR®, relate to Six Sigma and Lean. However, perhaps a more relevant question should be, “How can Six Sigma and Lean make a SCOR model more effective?”
SCOR, a trademark of the Supply-Chain Council, consists of several hierarchal levels. These are shown in Figure 1 and include an evaluation of strategic goals and objectives in a context of competitive supply chain analysis, value stream mapping of major process workflows and at the lowest level an operational analysis of work tasks, standards and metrics. These hierarchal levels form a generic supply chain model which provides standardized workflows, procedures and metrics. However, the usefulness of a SCOR model is that it can be customized to fit the specific supply chain of almost any organization, but, major process workflows are standardized and include basic control elements based on the combined knowledge of many industry experts.
Building a supply chain model or process with using a highly standardized structure enables an organization to detect and eliminate process variation. This is because variation from a well-known standard is easily detected, analyzed and eliminated using Lean, Six Sigma and similar improvement methodologies. This concept is shown in Figure 1 at the second and third levels of the pyramid. As an example, Lean methods can be applied to simplify, standardize and mistake proof process workflows prior to migration to a SCOR model.
On the other hand, Six Sigma methods can be used to analyze customer and process data to identify repeatable patterns associated with the root causes of poor operational performance. These types of analyses also can be used to build quantified models of a system’s metrics as described by the Six Sigma expression Y=f(X). In other situations, when customization is required to match a specific supply chain operational design, Design for Six Sigma tools and methods can be used to augment the basic SCOR model. But, at this point a team should consider using the Logistics Council’s Design-Chain-Operations-Reference model.
Integrating Organizational Process Workflows
A SCOR model also helps to integrate organizational process workflows and their internal operational work tasks into a coherent whole within a global supply chain. Integration is especially important because global supply chains are heavily dependent on information technology to build and manage their demand and capacity planning infrastructure. Standardizing operational methodologies ensures that a common approach is taken by supply chain participants to development of procedures and metrics. This tends to integrate rather than isolate operational segments.
Also, to the extent that there are process breakdowns, Lean Six Sigma methods can be used to identify and eliminate their root causes. As an example, Six Sigma methods are very useful in identifying and analyzing the voice of the customer during the deployment of SCOR methodology and development of a SCOR model within a supply chain. Lean methods are used to simplify and eliminate non-essential operations by identifying value-adding and non-value-adding operations.

A major goal of applying a SCOR model is to develop a value stream map describing a supply chain’s major process workflows. Figure 2 shows that a SCOR model consists of five major process workflows. These are:
- Demand and supply planning
- Sourcing strategies
- Transformation processes
- Warehousing and delivery
- Reverse logistics
These major process workflows are then broken into lower level workflows. As a simple example, using the SCOR modeling method, the “sourcing” component is broken into several lower level process workflows – S1, or source stocked product, S2, or source make-to-order products and S3, or source engineer-to-order. Each of these workflows is then broken down further into operation within workflows and then into the specific work tasks of each operation.
Providing Definitions, Metrics, Tools and Methods
A SCOR model also provides operational definitions, expected performance metrics for basic supply chain operations as well as best-in-class tools, methods and systems for its members to use to modify their process workflows. This approach enables users to more easily adapt a SCOR model to their specific process workflows. As an example, S1, or source stocked product, is broken into the operations S1.1, or schedule product deliveries, S1.2, or receive product, S1.3, or verify product and S4, or authorize supplier payment. Metrics which have been shown to be predictors of best-in-class global supply chain performance also are provided by a SCOR model. These include: perfect order fulfillment, order fulfillment cycle time, system flexibility, cash-to-cash cycle time and similar metrics. A global supply chain can be analyzed relative to its major components to compare its actual to best-in-class performance benchmarks using this metric linkage concept. As a result, supply chains using a SCOR model provide Lean Six Sigma practitioners with a highly standardized supply chain process, but, also one that is operationally flexible as its needs change over time.

Some of the major process workflows within supply chains can help demonstrate where Lean Six Sigma methods can be used in relation to a SCOR model. These include ordering materials, components and items; managing purchase orders and accounts payable systems; selecting and managing suppliers; estimating freight rates; choosing shipping modes, claims and returns systems; managing fleet maintenance and operations, forecasting workloads; maintaining equipment; developing inventory storage strategies and rules; receiving inbound trucks, order-picking activities including pack-out; and dock auditing and loading outbound trucks.
However, supply chain process does not always perform according to standard due to myriad reasons. As an example, Lean Six Sigma projects have been deployed to improve customer service levels and on-time delivery, reduce overdue backlogs, increase inventory asset utilization efficiency (turns), reduce unplanned orders, reduce scheduling changes, improve material availability, improve forecast accuracy and reduce operational lead-time. It would be an easier if processes were standardized upfront using SCOR principles, prior to deployment of Lean Six Sigma projects aimed at identifying and eliminating the root causes for process breakdowns.
Starting a SCOR Deployment…
How would one start a SCOR deployment? The experts at the Supply-Chain Council can help, but, at an elementary level, an organization can compare its current supply chain at all operational levels to the established SCOR procedures, standards, metrics and benchmarks. Then value stream map, simplify, standardize major process workflows. In parallel, remember to apply Lean Six Sigma methods wherever there are process breakdowns whose root cause analysis requires a reduction in process variations.