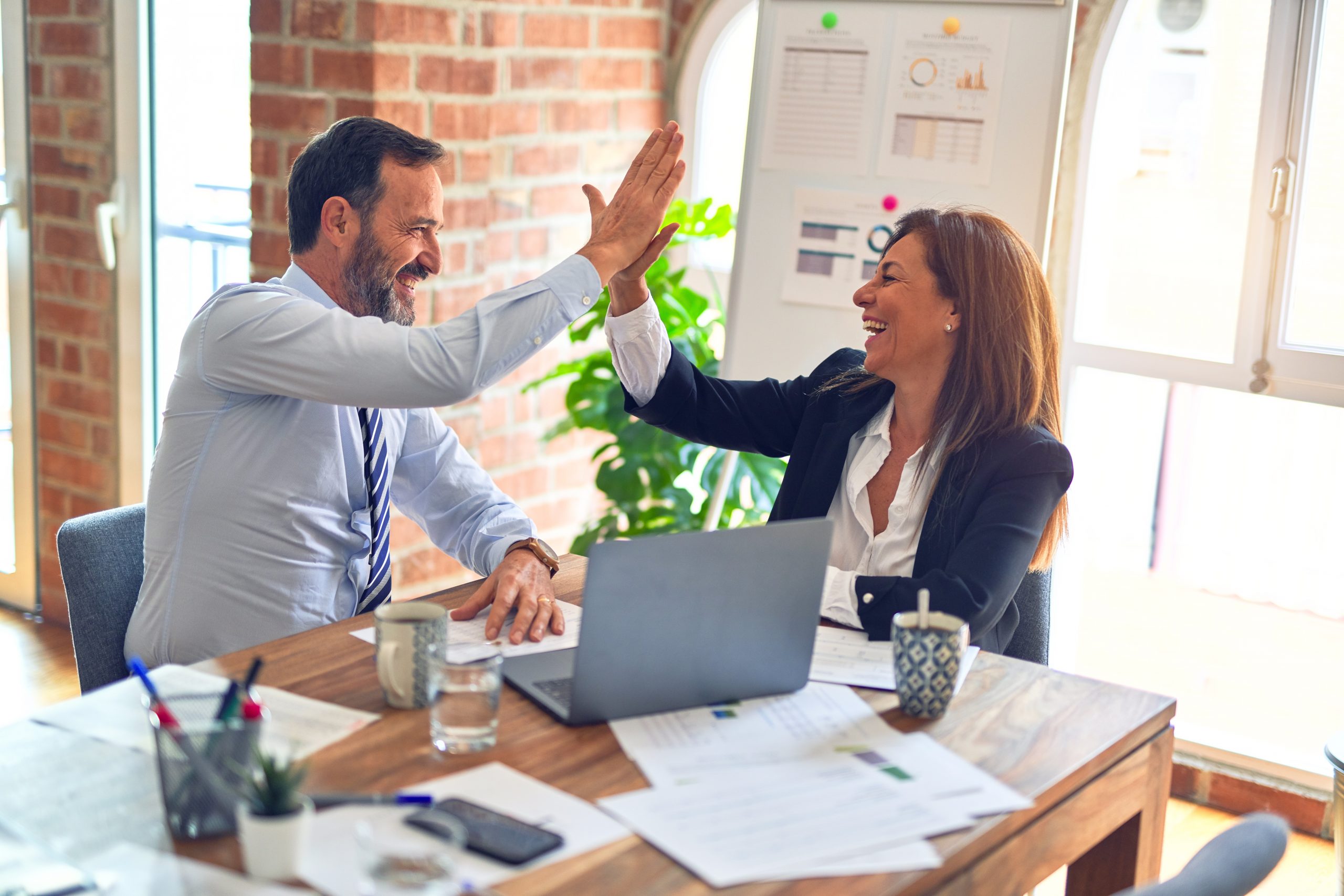
How does one sustain high levels of performance in manufacturing after the first successful waves of Lean Six Sigma projects? Research done on 75 manufacturers, predominantly European, sheds light on the balance between product/process and people leadership capabilities needed to sustain high levels of performance.
Of High Performers and Lagging Performers
High Performers: Sustaining high levels of performance is more about leadership than training and using the latest problem-solving tools and techniques, let alone new manufacturing and IT systems. This is according to Robert Collins and Roger Schmenner in “Understanding Persistently Variable Performance in Plants” (July 2004, IMD and Kelley School of Business, Indiana University). The authors of the IMD study conclude:
- “What leads to sustained high performance has more to do with beliefs and attitudes than with equipment purchases, ERP systems or wage rates…”
- “It is the mentality of the management and the workforce in the factory that matters most…”
- “The plant manager is key…one that hungers for improvement…keeps up relentless momentum…has a passion for the customer, product, processes, the plant’s people and its profitability.”
- “The effective plant manager communicates a vision, or master plan. His role is to stimulate people…engage the workforce directly…in pursuit of the vision.”
Manufacturing plants that score consistently high levels of performance (on-time delivery, quality, safety) turbo charge the use of Lean and Six Sigma with a hands-on, people-oriented management style. They focus simultaneously on breaking bottlenecks in the flow of operations and on improving process capability. They create an environment that encourages experimentation, the engine of innovation and continuous improvement. They stay close to the shop floor, relentlessly following through on implementation. They are decisiveness in their decision-making style while at the same time inclusive and “get along well with their people.”
Lagging Performers: Those plants that habitually report average to below average results, fall down on both the product/process side and people side. They are less aware of the value of Lean Six Sigma and less aggressive in taking action to break bottlenecks in the flow of operations. They have performance measures and key performance indicators (KPIs), but lose focus and are slow to follow up and implement corrective actions. These plant managers tend to be pre-occupied with technical solutions, less open for input from their people. The big picture vision is missing. They score the lowest scores on experimentation and change.
High Performers Versus Laggards
As the ratings in the table below shows, it is both technical and people management capabilities that separate high performers from laggards.
Biggest Differences Between Lagging and Sustained High Performance | ||
 |
Lagging |
High Performance |
Product and Process Characteristics > Breaking of Bottlenecks |
3.40 |
5.43 |
Managerial Characteristics > Leadrship Style > Way Plant Has Been Measured > Culture Within the Plant |
3.67 |
6.07 |
Style of Plant Manager > Seels Input from Everyone in the Plant > Vision > Followup; Implementation > Decisiveness |
3.24 |
5.57 |
Nature of Culture of Plant > Experimentation and Change |
2.80 |
4.80 |
High performing plants put much greater emphasis on breaking bottlenecks in process flows. The plant manager mobilizes the involvement of others in creating and realizing a compelling vision the future. This is reinforced by a clear product and technology strategy that gives the plant focus. People are held accountable for the actions that commit to take. Measures are used to help set priorities and get feedback on whether those actions have had the desired affect. There is a culture and leadership style in leading plants that embraces change as an opportunity to experiment and innovate.
The importance of the leader as role model was one of the conclusions of a global benchmarking study in a leading fast moving consumer goods company. The top 10 countries in terms of service and results within a global network were visited in order to understand the keys to their success. There were striking similarities in the leadership style of all 10 managing directors. One summarized it as, “My job is to create an environment in which people feel free to experiment, to take risks. That is what drives innovation and breakthroughs in performance. Rather than punish people for mistakes, I ask them ‘what can we do differently next time?'” It is a supportive environment that encourages risk-taking that leads to breakthroughs, a repetitive cycle that fuels high performance.
The difficult side of creating a high performance culture is confronting and dealing with the conflict inherent in managing underperformers. Cummins Engines, one of the pioneers in Lean manufacturing, promoted human resources managers to site leaders. The company realized that when a manufacturing system like Lean is in place and working well, the biggest management challenges are people-related – selecting, developing and managing talent. Plant managers who over-rely on engineering solutions to solve problems, are using only a fraction of the performance potential of their organization.
Lean Six Sigma for Sustainable Performance Improvement
A technically competent site leader with excellent people management skills will use Lean Six Sigma as a vehicle to simultaneously develop product, process and managerial capabilities. They select high-potential managers to lead Lean Six Sigma projects because it is an ideal environment in which to learn the leadership competences needed in today’s industrial environment:
- Translating strategies into business objectives and project goals.
- Managing complex (cross-functional, cross geography) projects.
- Basing decisions on data.
- Motivating others to bring forward and develop ideas.
- Solving root cause issues rather than symptoms.

The paradox of leadership is that one has more accountability with less control. The DMAIC roadmap is a way to ensure that others are keeping the business goal and boundaries of a project in mind while applying a logical sequence that will lead to results. Learn to trust that the approach, if followed, will guide others to insights and solutions that they own and implement. It is a fundamental lesson in leadership – how to let go without losing control.
The Lean Six Sigma benchmark plants are those that have flattened their organization structures and organized around self-directed process teams. They have invested as much in selecting and developing the skills needed to be self-managing as they have in new equipment and technology. The Novartis Suffern New York plant is a case in point. It has eliminated first line supervisors so that engineers, operators and support staff, such as IT, maintenance and mechanics, report directly to one team leader. On a process-oriented product team, such as Diovan, 80 people report to the team leader, Brain Hanifin. “You need to take an end-to-end approach to team building, from when raw materials come in the door to when the product leaves,” said Hanifin. “Any time you have a hand-off, you add complexity.” Clearly not everyone is comfortable, let alone has the necessary skills to work in self-directed work environment. Getting there from a traditional plant structure and culture was a difficult journey, but it has paid enormous dividends. Cycle times have been reduced by 70 percent and operating costs are down 40 percent and being sustained.
Conclusion: Leadership and Lean Six Sigma
Getting and sustaining high levels of performance is above all a leadership responsibility that requires:
- Developing a compelling vision and building a powerful site leadership team.
- Setting a clear product and process strategy and roadmap for implementation.
- Developing a dashboard of KPIs to focus improvement and drive implementation.
- Deploying Lean Six Sigma to improve flow, the capability of processes and create a culture of experimentation and change.
- Systematically growing the managerial pool of talent, especially people skills.
- Flattening and aligning organization structure with product process flows.
State-of-the art problem-solving tools and techniques can never compensate for weak leadership. In the hands of skilled leaders, those who can shape a vision, lay out a roadmap to that vision and energize people to get involved, Lean Six Sigma builds the capabilities to achieve and sustain success.