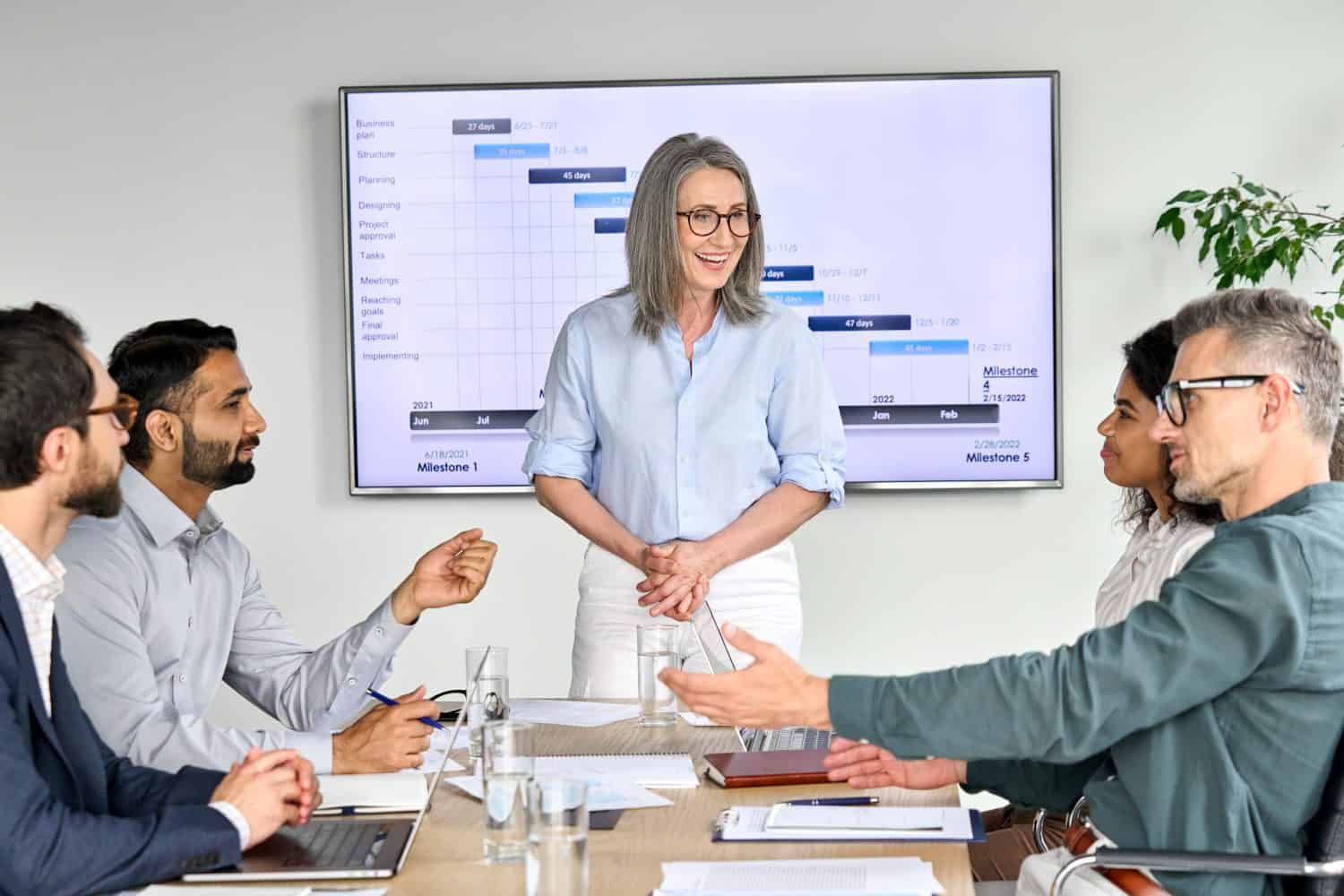
© Ground Picture/Shutterstock.com
Key Points
- Originally designed for manufacturing, Lean Six Sigma principles are now widely adopted in corporate and transactional settings to streamline workflows, reduce inefficiencies, and improve quality across various departments such as finance, HR, and customer service.
- Lean Six Sigma optimizes finance (e.g., faster invoice processing), HR (e.g., improved hiring efficiency), customer service (e.g., shorter response times), and marketing (e.g., better campaign ROI) by eliminating waste and reducing variation.
- Companies like Bank of America, Xerox, Verizon, Dell, and Amazon have effectively used Lean Six Sigma to enhance operational efficiency, improve customer satisfaction, and achieve cost savings in corporate functions.
- The methodology’s potential is further amplified by digital transformation technologies such as AI, machine learning, and robotic process automation, enabling real-time monitoring, advanced analytics, and automation of repetitive tasks.
Lean Six Sigma, a methodology that combines lean manufacturing and Six Sigma principles, has long been synonymous with the factory floor. Born out of Toyota’s production system and popularized through companies like Motorola and General Electric, Lean Six Sigma has been instrumental in streamlining manufacturing processes, reducing waste, and improving quality.
However, its potential extends far beyond the assembly line. In today’s competitive and dynamic business environment, organizations across industries are harnessing Lean Six Sigma to enhance corporate and transactional processes, drive efficiencies, and deliver superior value to customers.
Understanding Lean Six Sigma’s Core Principles

©Ground Picture/Shutterstock.com
Before exploring its expansion into corporate domains, it’s essential to understand the core principles of Lean Six Sigma. The methodology revolves around two main objectives:
- Eliminating Waste (Lean): This involves identifying and removing non-value-adding activities (waste) from processes. Examples include overproduction, waiting, unnecessary transportation, and defects.
- Reducing Variation (Six Sigma): By using data-driven decision-making and statistical tools, Six Sigma focuses on minimizing defects and inconsistencies, achieving process excellence with a target of 3.4 defects per million opportunities.
Together, Lean and Six Sigma create a robust framework that improves efficiency, quality, and customer satisfaction.
The Transition to Corporate Processes
Corporate and transactional processes, often perceived as less tangible than manufacturing workflows, can also benefit significantly from Lean Six Sigma. Common challenges in corporate settings include inefficient workflows, excessive bureaucracy, and inconsistent service delivery. By applying Lean Six Sigma principles, organizations can:
- Streamline workflows to reduce bottlenecks and delays.
- Ensure consistency and quality in customer-facing processes.
- Reduce redundancy and maximize the utilization of human and technological resources.
- Minimize frustration caused by inefficient or redundant processes.
Key Corporate Applications of Lean Six Sigma

1. Finance and Accounting
Lean Six Sigma has proven to be a game-changer in finance and accounting departments. Processes such as invoicing, accounts payable, and payroll often suffer from inefficiencies and errors. By implementing Lean Six Sigma, companies can:
- Streamline workflows to ensure faster invoice approvals and payments.
- Use statistical analysis to identify and address common sources of errors.
- Ensure adherence to regulatory requirements through consistent, documented processes.
Example: Bank of America implemented Lean Six Sigma to improve transaction accuracy and customer satisfaction. The initiative led to a reduction in errors, shorter processing times, and improved client experience.
2. Human Resources (HR)
HR processes, such as recruitment, onboarding, performance management, and employee training, are ripe for Lean Six Sigma optimization. Key benefits include:
- Identify bottlenecks in the recruitment pipeline to fill positions more quickly.
- Standardize and streamline onboarding to ensure new hires are productive from day one.
- Use data-driven insights to refine training programs and performance evaluations.
Example: Xerox utilized Lean Six Sigma to overhaul its hiring process, reducing the time to fill positions by 30% while improving candidate quality and experience.
3. Customer Service and Support
Customer service is a critical touchpoint for building brand loyalty. Lean Six Sigma helps organizations deliver exceptional service by:
- Streamline ticketing and escalation processes.
- Analyze common customer issues and provide targeted training for support teams.
- Use voice-of-the-customer data to refine processes.
Example: Verizon employed Lean Six Sigma to improve call center operations, leading to reduced call handling times and enhanced customer satisfaction.
4. Sales and Marketing
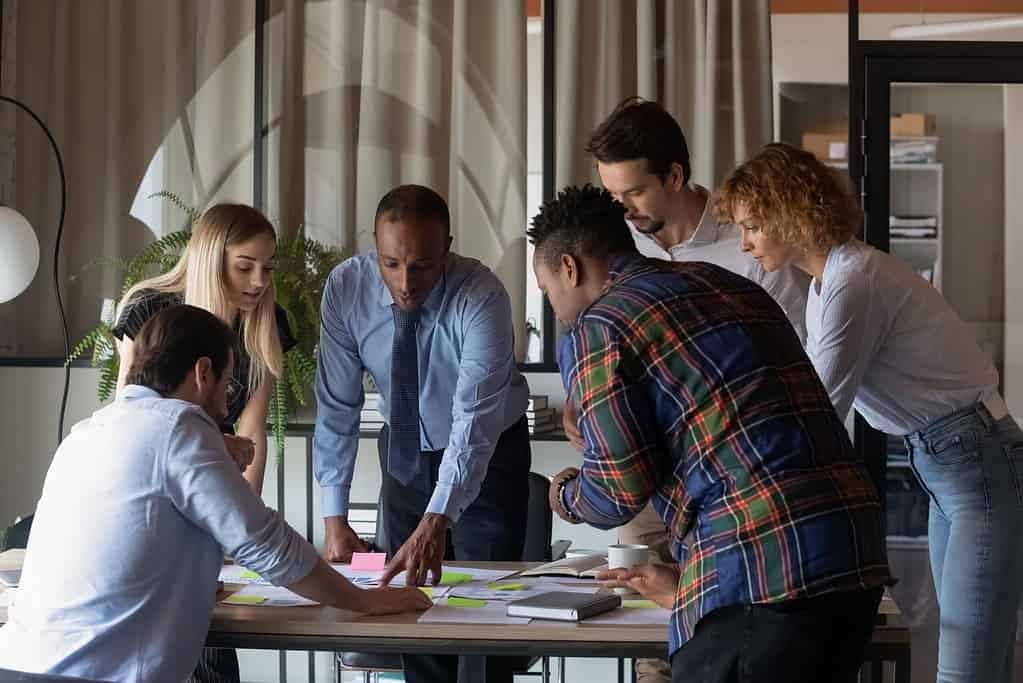
Sales and marketing teams can leverage Lean Six Sigma to optimize lead generation, customer segmentation, and campaign execution. Benefits include:
- Use data analytics to identify high-value leads and tailor outreach strategies.
- Eliminate ineffective campaigns and focus resources on high-impact initiatives.
- Align sales and marketing efforts for better outcomes.
Example: Dell applied Lean Six Sigma principles to its marketing campaigns, achieving a 25% improvement in campaign ROI by eliminating redundant and low-impact activities.
5. Supply Chain and Logistics
While closely related to manufacturing, supply chain and logistics processes in corporate environments involve numerous transactional activities, such as procurement, inventory management, and order fulfillment. Lean Six Sigma enables companies to:
- Streamline procurement and inventory replenishment processes.
- Enhance order accuracy and delivery precision.
- Identify and eliminate wasteful practices.
Example: Amazon employs Lean Six Sigma extensively in its supply chain operations, ensuring efficient inventory management and rapid delivery times to maintain its competitive edge.
Best Practices for Expanding Lean Six Sigma Beyond Manufacturing
Organizations looking to implement Lean Six Sigma in corporate settings should consider the following best practices:
- Executive support is crucial for driving cultural change and ensuring the success of Lean Six Sigma initiatives.
- Equip employees at all levels with Lean Six Sigma knowledge through certification programs and hands-on training.
- Focus on processes that directly impact customer satisfaction, revenue, or compliance.
- Use data analytics tools and software to enhance process analysis and automation.
- Continuously measure performance metrics to ensure sustained improvements and identify new opportunities for optimization.
Challenges and Solutions
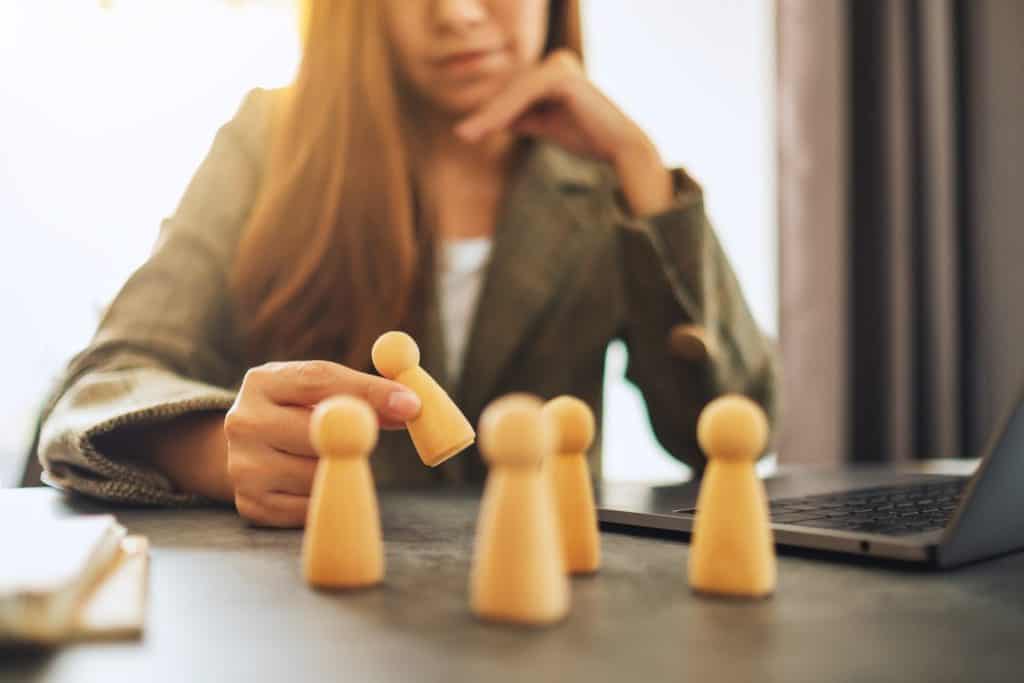
©Blue Titan/Shutterstock.com
Adopting Lean Six Sigma in corporate processes is not without challenges. Common obstacles include:
- Employees may be reluctant to alter established workflows. Solution: Foster a culture of continuous improvement through transparent communication and incentives.
- Applying Lean Six Sigma to non-manufacturing processes requires specialized knowledge. Solution: Partner with experienced consultants or invest in employee training.
- Corporate processes may lack robust data available in manufacturing environments. Solution: Develop systems to collect and analyze relevant data.
The Future of Lean Six Sigma in Corporate Settings
As digital transformation accelerates, the integration of Lean Six Sigma with technologies like artificial intelligence, machine learning, and robotic process automation (RPA) will redefine its application in corporate environments.
Artificial Intelligence (AI) enhances the application of Lean Six Sigma in corporate and transactional environments by enabling data-driven decision-making and process automation. AI-powered analytics identify inefficiencies and bottlenecks across workflows, offering actionable insights for process optimization. For example, machine learning algorithms can predict process outcomes, helping organizations proactively address issues and reduce variation.
Incorporating AI also facilitates real-time data collection and monitoring, critical for maintaining process control and sustaining improvements. Robotic Process Automation (RPA), an AI-driven tool, automates repetitive tasks in finance, HR, and customer service, reducing waste and ensuring accuracy.
Additionally, natural language processing (NLP) tools analyze customer feedback, enabling businesses to align operations with customer needs. AI’s predictive capabilities also enhance project prioritization, ensuring Lean Six Sigma efforts focus on high-impact areas. By integrating AI, organizations can scale Lean Six Sigma beyond manufacturing, driving efficiency, consistency, and innovation in corporate processes.
Similar Concepts
Much has been written about the use of Lean Six Sigma in non-manufacturing applications. Here are a few articles about how Lean Six Sigma was used in corporate and transactional processes.
- Here is an interesting article on how Lean Six Sigma was used in the EHS (Environmental, Health, and Safety) function of an organization.
- This article explores the use of Lean Six Sigma in Pharmaceutical Sales and Marketing.
- This last article suggests some possible projects for a Human Resources department.
Wrapping It Up
Lean Six Sigma’s journey from the factory floor to the corporate office marks a significant evolution in business management practices. By addressing inefficiencies, reducing variation, and enhancing customer satisfaction, Lean Six Sigma empowers organizations to thrive in an increasingly competitive landscape. From finance and HR to customer service and marketing, its principles are driving transformation across industries.
Companies like Bank of America, Xerox, Verizon, Dell, and Amazon are leading the charge, demonstrating the immense potential of Lean Six Sigma beyond manufacturing. As organizations continue to embrace this methodology, Lean Six Sigma will remain a cornerstone of operational excellence, unlocking new opportunities for innovation and growth.
The image featured at the top of this post is ©Ground Picture/Shutterstock.com.