
© Ground Picture/Shutterstock.com
Key Points
- Essential Skills for 2025: Lean Six Sigma (LSS) professionals must develop advanced data analytics, digital transformation proficiency, project management expertise, and sustainability knowledge, alongside leadership and collaboration skills, to address evolving industry demands.
- Comprehensive Development Strategies: Organizations should invest in tailored training programs, mentorship initiatives, cross-functional collaboration, and the use of modern learning technologies like gamification and AI-powered platforms to cultivate LSS talent.
- Aligning Training with Strategic Goals: LSS talent development must focus on organizational priorities, ensuring training initiatives are linked to measurable outcomes like cost reduction, improved efficiency, and customer satisfaction.
- Proactive Individual Actions: Professionals can bridge the skills gap by pursuing certifications, mastering emerging tools, engaging in networking opportunities, and gaining hands-on experience through real-world process improvement projects.
The global workforce is evolving rapidly, with emerging technologies, shifting market demands, and a renewed emphasis on efficiency. For organizations striving to maintain a competitive edge, Lean Six Sigma (LSS) has become a crucial methodology for streamlining processes and improving quality. However, as we enter 2025, one challenge looms large: the skills gap in Lean Six Sigma talent. Bridging this gap requires a deliberate and multifaceted approach that incorporates targeted training, hands-on experience, and alignment with emerging trends.
Understanding the Lean Six Sigma Skills Gap in 2025
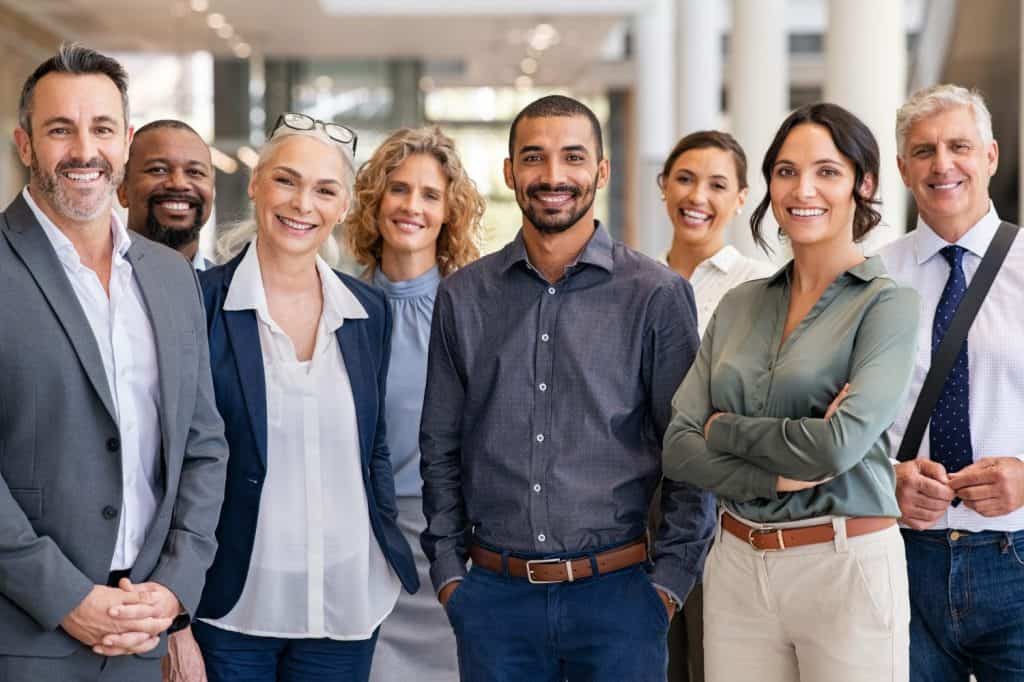
©Ground Picture/Shutterstock.com
The skills gap in Lean Six Sigma stems from several factors, including:
- Technological Disruption: Automation, artificial intelligence (AI), and data analytics tools have transformed how Lean Six Sigma is applied, demanding new technical skills.
- Generational Shift: A significant portion of the experienced workforce is retiring, leaving a void in leadership and expertise.
- Evolving Business Needs: Companies now demand more agile, cross-functional LSS professionals who can adapt to dynamic challenges.
To address these issues, organizations must adopt a proactive approach to developing Lean Six Sigma talent.
Key Skills for Lean Six Sigma Professionals in 2025
Lean Six Sigma practitioners must possess a combination of technical, analytical, and soft skills to thrive in today’s environment. The following skills are particularly vital in 2025:
1. Advanced Data Analytics
- Why it matters: Big data is at the heart of Lean Six Sigma in 2025. Professionals must interpret complex data sets to identify inefficiencies and optimize processes.
- How to develop it: Invest in training programs that teach statistical software such as Python, R, Minitab, and Power BI. Certifications in data science can also complement LSS credentials.
2. Digital Transformation Proficiency
- Why it matters: Lean Six Sigma solutions increasingly leverage digital tools like IoT sensors, robotic process automation (RPA), and machine learning models.
- How to develop it: Encourage familiarity with digital technologies through hands-on projects and partnerships with tech-focused training providers.
3. Project Management Skills
- Why it matters: LSS professionals often lead complex projects. Understanding Agile and Scrum methodologies enhances project efficiency and stakeholder alignment.
- How to develop it: Provide dual certifications in Lean Six Sigma and project management frameworks such as PMI’s PMP or Agile certifications.
4. Soft Skills for Leadership and Collaboration
- Why it matters: Effective communication, team leadership, and stakeholder engagement are critical for project success.
- How to develop it: Facilitate workshops on leadership development, emotional intelligence, and conflict resolution.
5. Sustainability and Circular Economy Knowledge
- Why it matters: Modern LSS projects must consider environmental and social impacts alongside traditional efficiency goals.
- How to develop it: Introduce training on sustainability principles and metrics, such as carbon footprint analysis and lifecycle assessment.
Recommendations for Developing Lean Six Sigma Talent in 2025
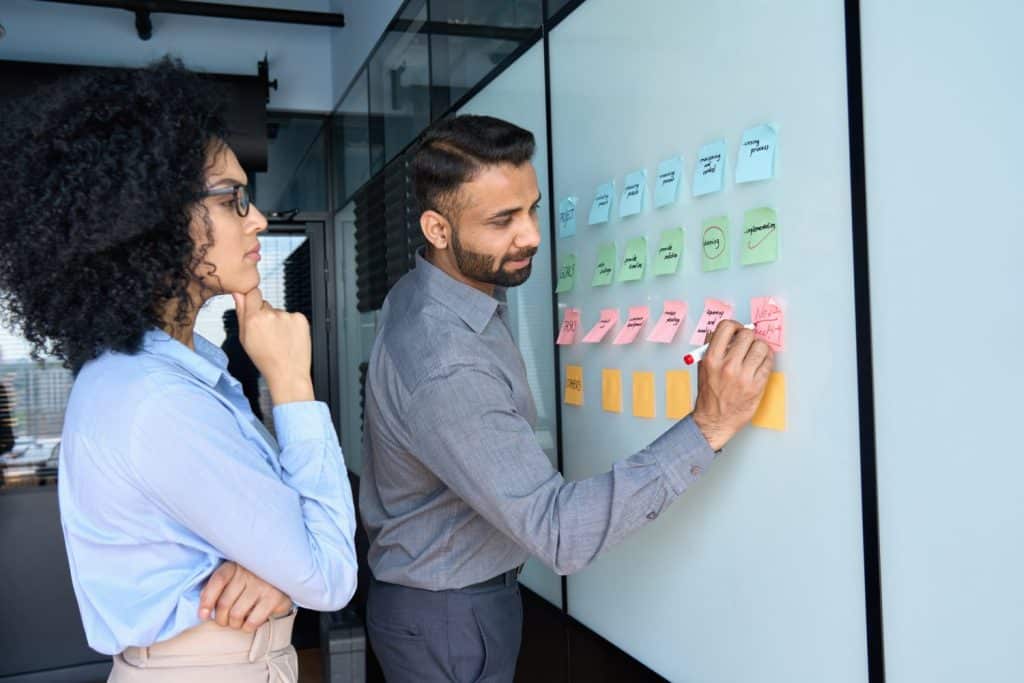
©Ground Picture/Shutterstock.com
Bridging the skills gap requires a structured approach that integrates education, mentorship, and organizational support. Here are key recommendations:
1. Invest in Comprehensive Training Programs
Organizations should create robust training frameworks that cover both foundational and advanced Lean Six Sigma skills. This includes:
- Customized LSS Training: Develop tailored programs aligned with your industry’s specific challenges.
- Blended Learning Models: Combine online modules with in-person workshops to maximize flexibility and engagement.
- Continuous Education: Offer advanced certifications like Lean Six Sigma Master Black Belt or specialized training in areas such as AI-driven process improvement.
2. Establish Mentorship Programs
Experienced Lean Six Sigma practitioners can play a pivotal role in nurturing the next generation. Mentorship programs help transfer tacit knowledge and provide practical guidance.
- Structure mentorship pairings based on experience levels and career goals.
- Incorporate reverse mentoring to allow younger employees to share their technological insights with senior mentors.
3. Encourage Cross-Functional Collaboration
Lean Six Sigma thrives in environments where diverse perspectives are valued. Encourage collaboration across departments to:
- Break down silos and identify inefficiencies that span multiple functions.
- Foster innovation by combining insights from operations, IT, marketing, and other areas.
4. Leverage Technology to Facilitate Learning
Modern tools can make training more accessible and impactful. Consider:
- Gamification: Create interactive simulations where employees can apply LSS principles in virtual environments.
- AI-Powered Learning Platforms: Use adaptive learning systems that tailor content to individual strengths and weaknesses.
- Virtual Reality (VR) Training: Enable immersive process improvement simulations for hands-on experience.
5. Align LSS Training with Strategic Goals
To maximize ROI, Lean Six Sigma development must align with the organization’s broader objectives:
- Identify priority areas where LSS can deliver the greatest impact, such as cost reduction, customer satisfaction, or supply chain efficiency.
- Track outcomes using key performance indicators (KPIs) to ensure training translates into tangible improvements.
6. Build a Culture of Continuous Improvement
Cultural change is essential for sustaining Lean Six Sigma’s success. Organizations should:
- Encourage a growth mindset by rewarding employees who pursue LSS certifications and demonstrate innovation.
- Embed LSS principles into everyday workflows through process audits and regular feedback loops.
Case Studies: Success Stories in LSS Talent Development
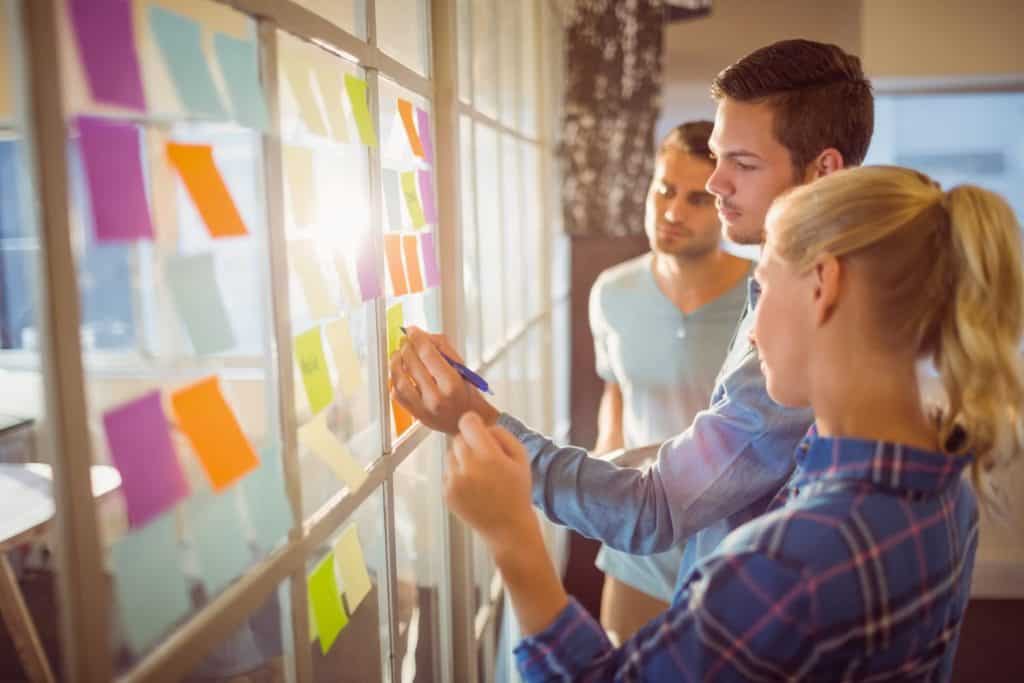
©ESB Professional/Shutterstock.com
Example 1: A Manufacturing Giant
A multinational manufacturing firm faced a talent shortage in Lean Six Sigma expertise. To address this, they:
- Partnered with local universities to create an LSS-focused curriculum.
- Launched an apprenticeship program where employees gained real-world experience in process improvement.
- Result: A 15% increase in operational efficiency within two years.
Example 2: A Healthcare Provider
A healthcare organization sought to improve patient outcomes while reducing costs. They:
- Implemented a mentorship program pairing senior LSS practitioners with junior staff.
- Conducted LSS workshops focused on digital health technologies.
- Result: A 25% reduction in patient wait times and 10% cost savings.
Actions for Individuals to Bridge the Gap
Professionals looking to advance their careers in Lean Six Sigma can take proactive steps to develop relevant skills:
- Pursue Certifications: Enroll in reputable Lean Six Sigma programs offered by organizations like ASQ or IASSC.
- Learn Emerging Tools: Gain expertise in automation platforms, data visualization software, and predictive analytics tools.
- Network Actively: Join industry forums, attend conferences, and participate in online communities to stay updated on trends.
- Seek Real-World Experience: Volunteer for process improvement projects within your organization to build hands-on expertise.
How AI Can Be Used to Help Bridge the Skills Gap

©Golden Dayz/Shutterstock.com
Artificial intelligence (AI) is a transformative force in addressing the skills gap in Lean Six Sigma (LSS) by enhancing training, enabling personalized learning, and optimizing process improvement initiatives. AI-powered tools can deliver tailored training experiences that adapt to individual learning styles and proficiency levels. For example, machine learning algorithms analyze a learner’s performance by identifying areas for improvement and suggesting targeted content, ensuring efficient skill development.
AI also facilitates interactive and immersive learning through simulations and virtual reality (VR) environments. These tools enable LSS practitioners to practice problem-solving in real-world scenarios without the risks associated with live operations. Gamified platforms driven by AI encourage engagement and retention by creating a dynamic and competitive learning experience.
Additionally, AI enhances the application of Lean Six Sigma by integrating advanced analytics into problem-solving processes. AI tools can quickly analyze vast datasets to identify inefficiencies, predict trends, and recommend actionable solutions. This accelerates the Define-Measure-Analyze-Improve-Control (DMAIC) cycle, enabling LSS professionals to deliver results more effectively.
For organizations, AI can streamline talent management by identifying employees with potential for LSS roles, mapping skill gaps, and recommending personalized development paths. By automating repetitive tasks, AI allows professionals to focus on strategic initiatives, fostering innovation and growth.
In 2025, the integration of AI into Lean Six Sigma talent development is not just a possibility but a necessity. It empowers organizations and individuals to overcome challenges, adapt to technological advancements, and achieve excellence in process improvement.
Similar Concepts
Here are a few articles on how LSS training and certification may need to change as AI is adapted to support LSS deployments.
- This article discusses how LSS training must be adapted to incorporate AI.
- The questions of whether AI can replace Lean Six Sigma Master Black Belts or Statistical Software are answered in these two articles.
The Future of Lean Six Sigma Talent Development
In 2025, bridging the Lean Six Sigma skills gap will require organizations and individuals to embrace a forward-thinking approach. By investing in training, fostering collaboration, and leveraging technology, companies can build a robust pipeline of LSS professionals capable of driving innovation and efficiency. For professionals, continual learning and adaptability will be key to staying relevant in this ever-evolving field.
Through collective effort, the Lean Six Sigma skills gap can be transformed from a challenge into an opportunity—empowering businesses to achieve sustainable growth and operational excellence.
The image featured at the top of this post is ©Ground Picture/Shutterstock.com.