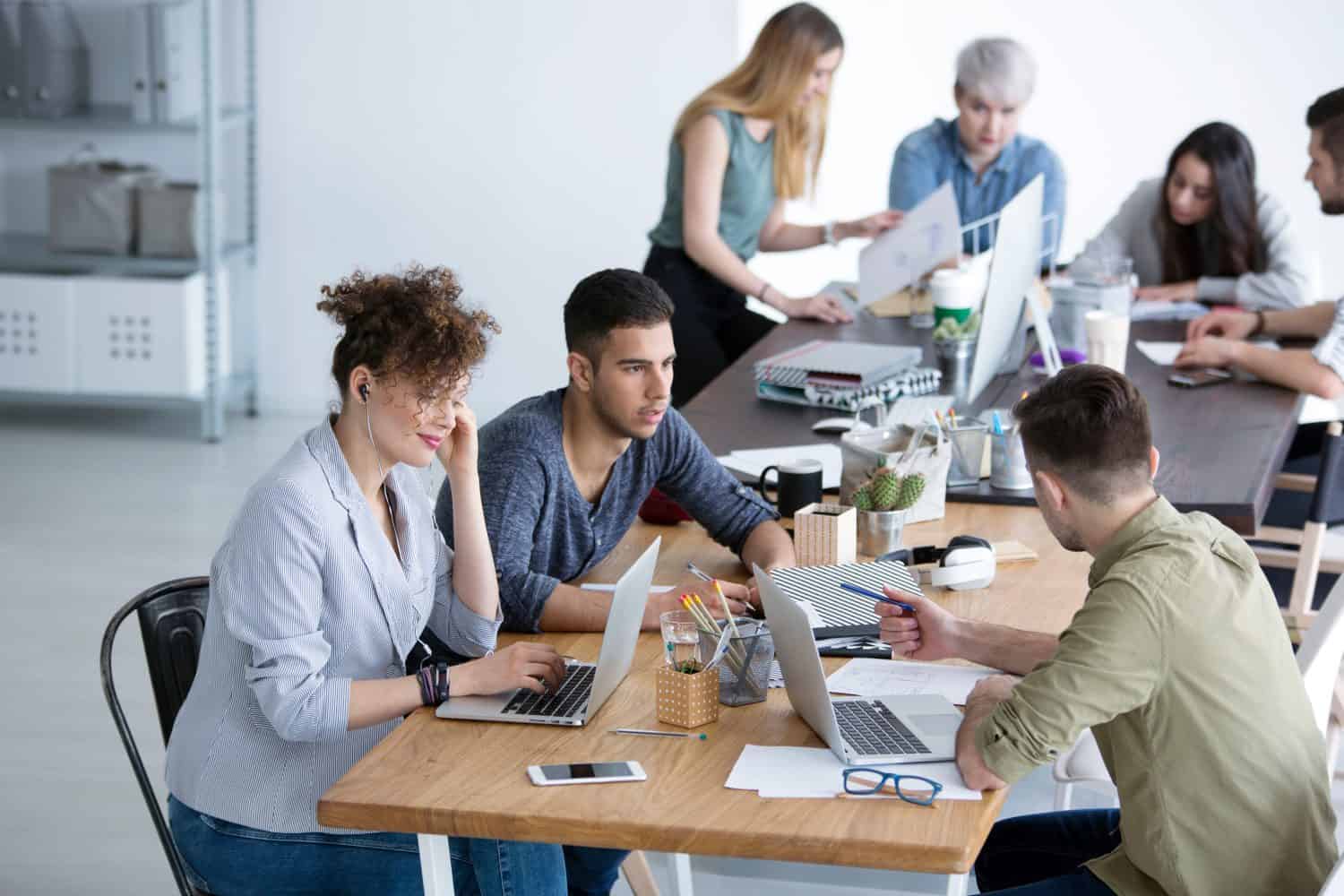
© Ground Picture/Shutterstock.com
Key Points
- SIPOC diagrams are powerful tools for mapping out processes at a high level.
- You want your diagrams to have enough detail to account for all variables in a process.
- Good SIPOC diagrams should be readily understood.
- You need to use current data when generating a SIPOC diagram.
What are the most common mistakes when using SIPOC? The SIPOC Diagram is one of the most useful tools in your arsenal when it comes to process analysis. It readily allows you and your team to grasp the various elements of a process before diving fully into detail on how everything fits together.
That said, it’s easy enough to lose the forest in the trees, especially with a tool like this. As such, we’re taking a closer look at the cardinal sins of using this tool and how to best avoid them.
A Brief Refresher on SIPOC
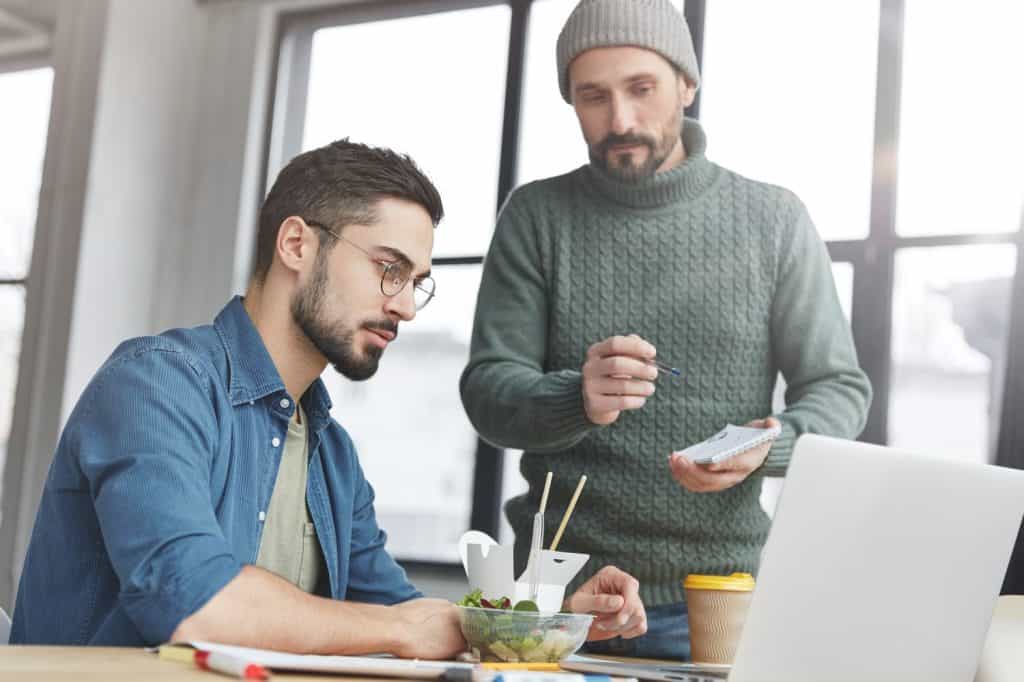
©Cast Of Thousands/Shutterstock.com
Before diving into the common mistakes when using SIPOC, it might help to remind our readers what it is. SIPOC Diagrams are used in the define stage, or D of DMAIC. They are high-level diagrams intended to map out the Suppliers, Inputs, Processes, Outputs, and Customers. Hence the name, SIPOC.
These diagrams can be relatively simple. However, they can grow in complexity depending on the scope and scale of a given process. It is one of the most important tools you have at your disposal when planning a new project, so understanding its use is paramount.
What It’s Used For
The Six Sigma methodology is all about structure, so having a process map in place before any work takes place only makes sense. You would typically create a SIPOC Diagram before any actual work on a project takes place. Taking the time to get your team on the same page helps to align the vision for the entire project.
It also helps to identify potential issues that may arise during the development of a project. By taking the time to map out everything. As this is a visual representation, it offers a structured view of the flow and goals of a project and how they subsequently align with the voice of the customer.
Additionally, it is a highly useful tool for providing a high-level view of complex processes. Since it takes such a broad look at things, it readily allows a team to interpret the intricacies of a project while getting into granular detail regarding the numerous components of a seemingly daunting process. This in turn, allows your team to drill down to what matters the most.
SIPOC is a powerful tool in the Six Sigma methodology, but can readily be integrated into other process improvement approaches like Lean, Kaizen, and Lean Six Sigma. Understanding how to effectively structure a SIPOC Diagram can save potential headaches further down the line.
The Biggest Common Mistakes When Using SIPOC
It isn’t all roses when dealing with SIPOC diagrams. As such, there are some common mistakes when using SIPOC diagrams. There are certainly other complications that can arise when creating the diagram, but we’ll be honing in on four key points. They are as follows:
- Detail
- Alignment
- Clarity
- Action
Even one of these can be a fatal mistake when designing your diagram. If you’re hitting all four at once, you’ll need to go back to the literal drawing board and try some different techniques to make sure things are hitting where they need to be.
Skimping on Detail
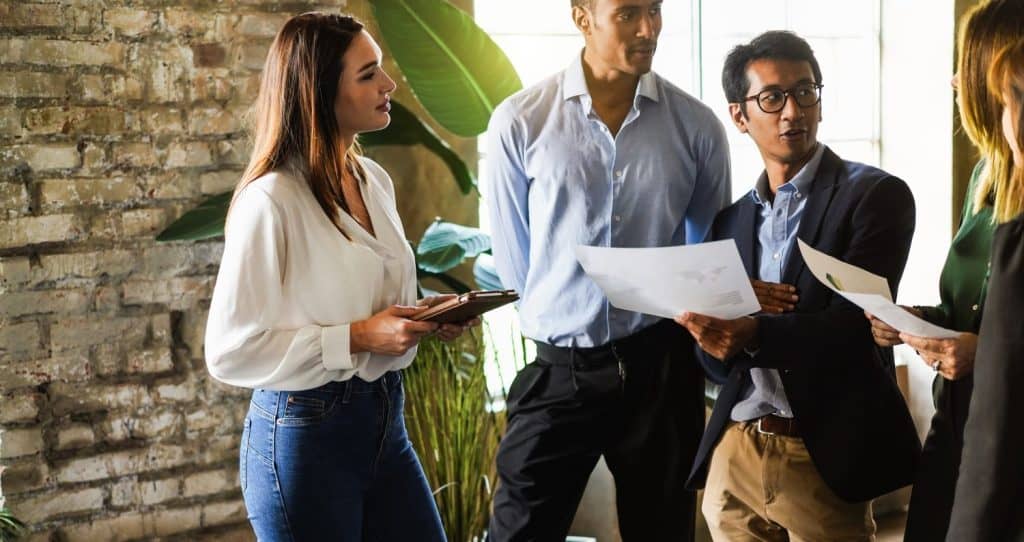
©Tint Media/Shutterstock.com
One of the most common mistakes when using SIPOC diagrams that you’ll see is a lack of detail. What do I mean by detail? When you’re drafting out the diagram, you’re considering all aspects of the process itself. It is intended to be a high-level overview of the process, so going too in-depth can be to your detriment.
However, the inverse is also true. If you’re lacking detail, like missing stakeholders and suppliers, key inputs, or simply forgetting potential customers, you’re asking for trouble. Think of it a bit like asking for directions to get somewhere. If you’re looking for a good pizza place, you’re not asking for just the street or area, you’re looking to drill down on the matter at hand.
Why It Matters
A lack of detail can lead to trouble down the line as I’ve already stated. Generating a SIPOC diagram can be somewhat daunting if you’re new to the process. You don’t want things to be vague or simply depicted. As such, it pays to get everyone’s input in creating the diagram itself. If needed, you can create additional SIPOC diagrams, which can be helpful for particularly large processes.
Sure, it takes more time, but you want enough detail that things don’t get bogged down when it comes time to use it as a roadmap to your project’s success. Skipping by key components of the process itself can come back to bite you later on.
It Doesn’t Align with Current Data
You’re on a Six Sigma site reading this, so I trust you understand the importance of data. Your organization is generating data constantly, which goes on to influence further processes, improvements, and what have you. So, what happens if you’re generating a new SIPOC diagram and the data is out of date?
You’re asking for trouble in this scenario. If you’re relying on outdated metrics, faulty data, or things that don’t reflect the current situation, how do you expect the project to succeed? Data drives modern businesses, and that is something you need to pay keen attention to. Otherwise, you’re just committing another one of the common mistakes when using the SIPOC diagram.
How to Correct It
This should be fairly self-explanatory, but you want to get all your ducks in a row. Data, analysis, and any other materials need to reflect current trends and conditions within your organization. If you don’t have access to those points, find somehow who does have them. SIPOC diagrams are a group effort, not a solo endeavor.
Think about it, if I’m your manager and you bring a SIPOC diagram that isn’t accounting for processes we integrated into production months ago, do you think I’ll sign off? If your answer was a resounding no, you see the issue with not listening and heeding current data.
You want to maintain that forward momentum and work with data sets that are clear, current, and reflect the current climate in your organization. Relying on data that is years old is just a roadmap to failure.
It Isn’t Clear

Creating a good SIPOC diagram is a balancing act. We’ve already covered the need for just enough detail to be worth following. However, that detail is worthless if it isn’t understood by everyone on board. A good SIPOC diagram should be clear and to the point, rather than a confusing mess. II can speak from personal experience, creating these high-level documents is a far cry from the more detailed documentation many professionals are accustomed to creating.
If you’re in a specialized line of work, you likely understand the struggle. When presenting high-level documents, it needs to be clear enough that a layperson can read it and understand it instantly. So, this sort of runs against the concept of providing enough detail. However, you have to think of it as being detailed enough that a high-level manager grasps the concept, but clear enough that they don’t have questions on what you mean.
Accounting for Everything
As with any balancing act, you have to take special care to keep things just right. This goes right along with detail, so you’ll want to keep track of every input, output, customer, supplier, and so forth.
If you’ve got multiple shareholders, account for those. Multiple customers? Same deal. At the end of the day, anyone involved in putting this into action needs to understand what they’re seeing without having to ask multiple questions to drill down.
You Can’t Put It Into Action
You’ve got the diagram drafted, everything seems to check out, it’s time to put it into action and get started. One of the most common mistakes when using SIPOC diagrams is just a simple lack of follow-through. If you’re struggling to put the document together, how can you expect to actually get the plan up and running?
Preparation, Preparation, Preparation
As with all tools and concepts presented in the Six Sigma methodology, you have to prepare. Diving into how to implement the SIPOC diagram after it’s created requires a whole different article to even explore. Simply put, you have to keep track of everything. If circumstances change, the document needs to change.
Before you even draft out the SIPOC diagram with your team, take care and precautions to define the scope and goal of your process. This will save time, energy, and heartache in the long run.
Real-World Consequences of Common Mistakes When Using SIPOC Diagrams

We’ve talked about some dire things today, but we aren’t done yet. I’ve kept the conversation fairly high-level, so it’s time to dive into what can go wrong. Consider for a moment that you’re in charge of a tech department at a large financial institution. It’s time to upgrade everyone’s workstations, but you need to submit a SIPOC diagram before putting together the work order.
You’re new to this, only on the job a few months, this is your first time being entrusted with this level of responsibitly. You don’t consider the data, things are hazy and lacking clarity as a whole. You’ve failed to properly identify the suppliers, the process itself is poorly outlined, the recipients of these workstations have been identified using data that is over a year out of date.
Your superior is furious, this isn’t at all what they had in mind. Now, you’ve got to go back to square one, and the whole process is taking time and money. If you had taken the time to read up and heed good design workflow for the diagram itself, this could’ve been avoided.
Other Tools for Process Analysis
The SIPOC diagram is just one part of many when it comes to process analysis in the Six Sigma methodology. If you want a clear and proven method of generating a good SIPOC diagram, take a look at our guide here.
That said, you might want some other approaches to mapping out your processes. Our tips and tricks for effective process mapping might be the cure for what ails you. This guide covers some of the basic ways you can make an effective and actionable process map that leads to greater success for your processes as a whole.
Conclusion
There are plenty of common mistakes when using the SIPOC diagram. However, the thing to keep in mind is that you don’t need to succumb to these pitfalls. Understanding how to effectively generate, submit, and act upon a SIPOC diagram is just part of the methodology. Failing to do so has consequences, some of which might just land you in hot water.
The image featured at the top of this post is ©Ground Picture/Shutterstock.com.