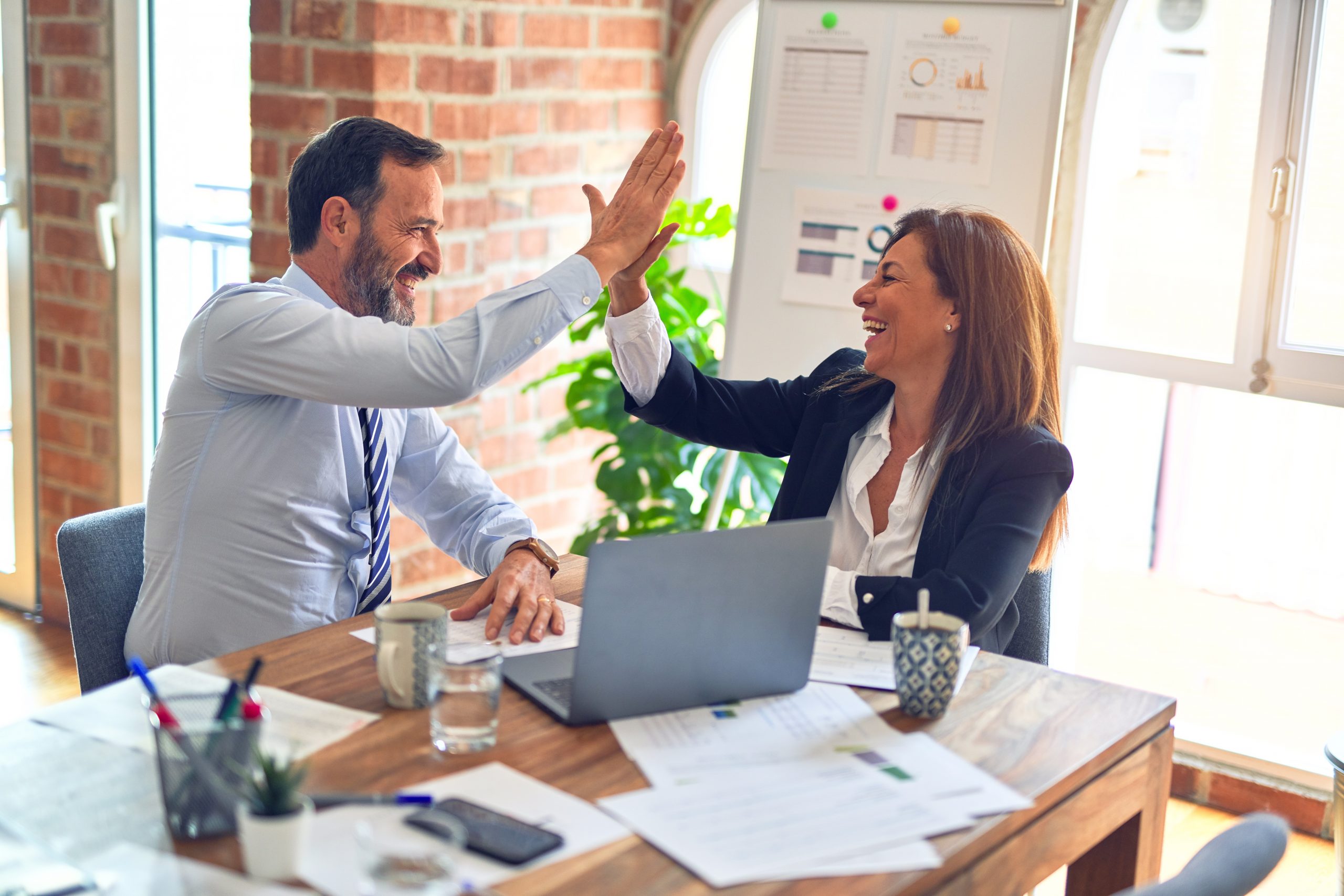
Many times Six Sigma practitioners start projects or analysis at a broad level. These projects may include processing a patient through a clinical procedure, transferring medical records, registering a patient, or analyzing lab or equipment usage. In healthcare, the number of processes and their complexity can be very high; there may be thousands of processes per day per facility due to technology, procedures, medications and specializations.
The common goal is to do the processes better, faster, safer and cheaper. However, practitioners may encounter a number of problems during process analysis, including the following:
- Results that are too general or broad to draw a specific conclusion or action
- A number of exceptions that cause the most problems. These instances are the variations that most administrators do not want to hear about, yet do not want to eliminate for business or service reasons.
Working with a broad population can produce these generalized results, as well as large variances (wide dispersion). Stratification is an optional but helpful step to do before sampling and subsequent analysis in order to address this variation. Stratification segments the population into smaller segments, called strata, to narrow the focus in order to develop more specific results. The stratification process works in a similar way to the marketing concept of segmentation and targeting. A case study is presented here to illustrate a structured approach to stratification. This approach can be utilized to study many situations and to develop a more structured and fact-based improvement effort.
Case Study: Stratifying MRI Use Data
A particular administrative, clinical or other service-related process, such as an MRI, may take x amount of time on average. Sampling from the population will produce general results. For example, the mean for an MRI may be 26.5 minutes with standard deviation of 15.6 minutes and range of 2 minutes to 72 minutes, indicating a fairly wide dispersion. The coefficient of variation (CV), the standard deviation divided by the mean, which is a good measure of dispersion, is 59 percent. With such a high variance, using the mean of 26.5 minutes for scheduling, performance evaluation or process improvement will produce marginal results. Queuing theory or a simple glance at the backlog will draw the same conclusion.
A good way to start the stratification is with a frequency histogram (Figure 1). Figure 1 also illustrates how the majority (53 percent) of the work effort is taken up by long-tail, or high-variation, instances; the long-tail instances are a major problem and opportunity.

Figure 2 provides a cumulative frequency of this same data and a visual representation of the short tail of the graph, the long tail and that in between. Based on Figures 1 and 2, three strata were picked in order to isolate the two tails. The dividing line between Strata 2 and 3 was selected based on keeping Stratum 2 fairly large (61 percent) and the standard deviation low (6 minutes compared to 15.6 minutes for the total population).

The normal curve shows the breaks at the tails and that the middle section is close to normal, as illustrated by the straight line overlay (Figure 3). The tails (mostly out-of-control) also show up on the control chart (Figure 4).


The coefficient of variances (standard deviation/mean) of the two main strata (2 and 3) are 31 percent and 27 percent, making up more than 50 percent of the original population (Table 1). This CV value difference is the most significant part of the whole analysis. Variation is chaos, and stratification allows process improvements to be tailored to less variance. It is always easier to define and optimize a process that has less variance.
Table 1: Stratum Characteristics and Statistics | ||||
Stratum | Size | Mean (minutes) | Standard Deviation (minutes) | Dispersion or Variance (CV) |
1. Short tail – range 1 to 10 | 8 percent | N/A | N/A | N/A |
2. In between – range 11 to 30 | 61 percent | 19.6 | 6.0 | 31 percent |
3. Long tail – range 31 to 72 | 31 percent | 45.1 | 12.0 | 27 percent |
4. Original population | 100 percent | 26.5 | 15.6 | 59 percent |
At this stage it is also possible to describe the stratum based on their characteristics. For example, the short tail might be called “Pre-screened,” the in-between might be the “Routine MRI” and the long tail could be “Special handing.” A series of questions and actions are related to these strata (Table 2).
Table 2: Stratum Identification and Action Plans | |||
Stratum | Size | Process Questions and Actions | |
Instance | Work effort | ||
1. The short tail – “Pre-screened” | 8 percent | 2 percent | Study these “best” cases. What are the characteristics of these occurences? How can these be fast tracked to bypass standard operations? |
2. The in-between – “Routine” | 61 percent | 45 percent | What can be done to improve these? Can some of these be shifted into Stratum 1 with some process improvements? |
3. The long tail – “Special handling” | 31 percent | 53 percent | These occurences cause havoc to the organization. Can some of these be shifted into Stratum 2 with some process improvements? Some of these are outliers and special causes. Can these be identified up front? If so, how, organizationally, should these be handled? |
Three different process improvement plans can be established (corresponding to Strata 1, 2 and 3), avoiding the one-size-fits-all approach. Because variability has been reduced, safety and patient-centric factors can be integrated and standardized. The reduced variation also allows expectations to be improved both for internal work flow and the patient. The costs savings can be noteworthy, too; for example, a 6-minute reduction in an MRI or CT is considered significant.
Additional Lessons Learned
Numbers tell a story. The wide dispersion, CV of 59 percent, in the original population strongly suggests that the process is not standardized. Hence, stratifying into multiple processes is a logical step. The percentage of instances on the long tail (31 percent) is enough to warrant a separate process.
Also, because the practitioners found that Stratum 2 is near normal, they had an additional level of information and metrics for process improvement. For example, 16 percent of the Stratum 2 instances (equivalent to 9.8 percent of total population) are in the 10-minute to 12-minute range and are potential candidates for shifting to Stratum 1.
Breaking Down Further
If a process is complex, stratification may need to be taken down several levels. In other words, the original problem or population can be segmented, and then the segments can be segmented. This may be most applicable when the population can be categorized nominally, such as “Referrals from staff physician.”
Likewise, as in the case presented, the quantitative data can be analyzed to create nominal classes of data (for example, the “Routine”) and corresponding tailored processes.
The stratification process also can be used in electronic data mining to reduce complexity, generalizations and scope for detailed analysis. For example, in lab or service use, variables might include requester or source (organization, facility, department or physician), patient demographics, types of services requested, causes (diagnostic code, procedure code) and frequency. This type of information could be used to better serve the requester, forecast use of the lab or service, and measure efficacy (financial or clinical). In these cases, a pivot table analysis (versus the frequency chart used in Figure 1) would work best to give a multi-directional view of strata prior to the statistical analysis. The results of the stratification could include efficacy per stratum versus efficacy per population. Further statistical analysis may determine dispersion and characteristics of the variances. Results could be used to better manage expected benefits, costs and risks.
Making Specific Changes
The stratification process starts with a broad population and breaks it into manageable segments (strata). Although this can be done intuitively, many times it is not, resulting in broad, low-impact changes, and disconnects or misunderstandings with management. A more structured and fact-based stratification process, quickly done up front with some basic statistics, can be used to identify, quantify, isolate and manage the routine and the noise in these processes.