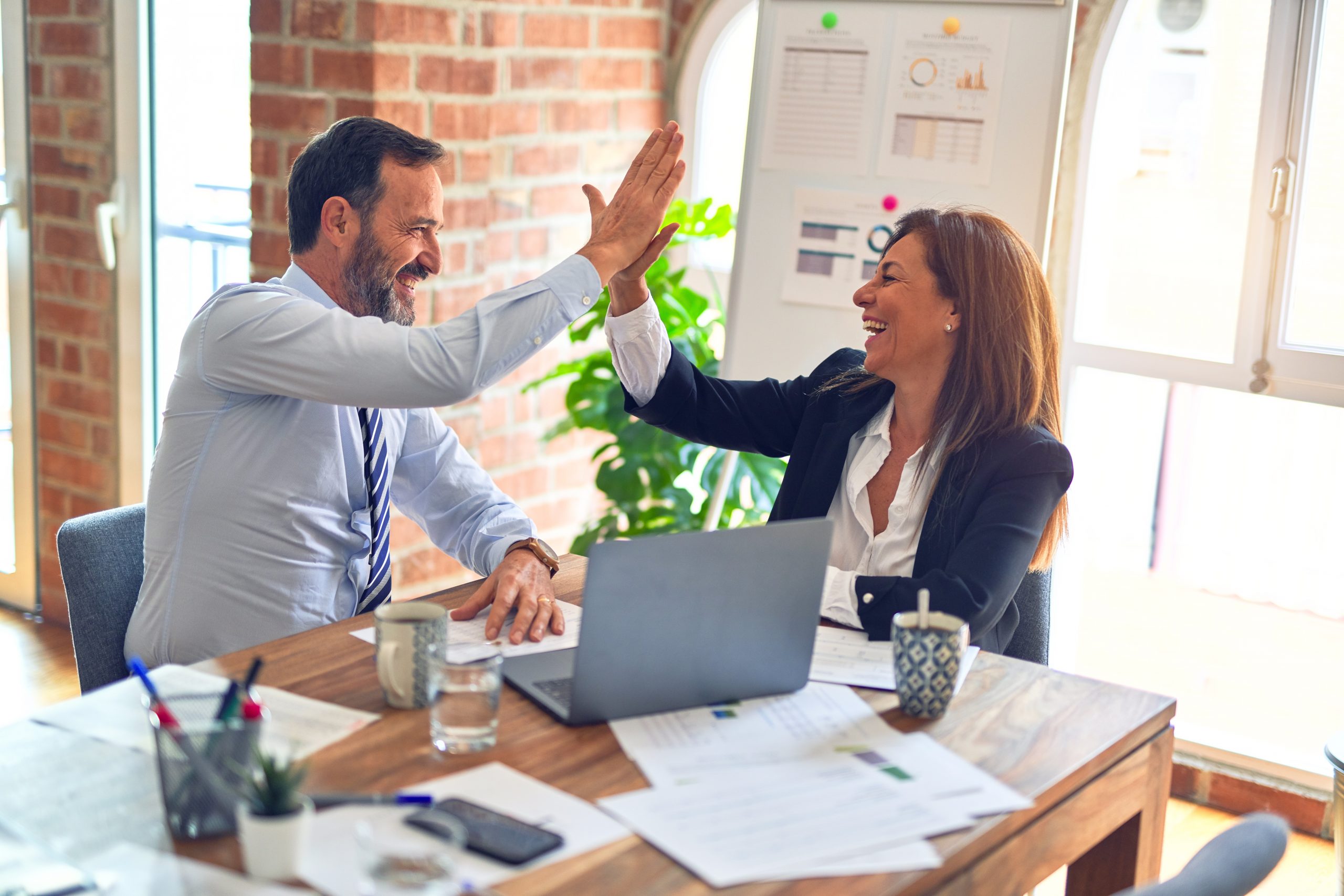
Finding and selecting the right improvement projects and developing a valuable project pipeline are crucial to the success of any Six Sigma initiative, especially when the initiative is in its infancy. If “boil the ocean” projects are selected, Black Belts and Green Belts will lose their energy and the Six Sigma initiative may fade. However, if “just-do-it” type projects are chosen, the company will not get the benefits or the investment return from their highly trained business improvement experts.
A six-step process can help Six Sigma Champions and Master Black Belts to identify appropriate projects properly and create an organization’s project pipeline.
To be successful, the project identification, prioritization and allocation process must be well defined and disciplined, addressing the most critical issues a company or division faces in a systematic way. Following these six key steps, those responsible for project selection will find the right projects and fill the project pipeline reliably.
Step 1: Understand the Issues
Champions or Master Black Belts should start by meeting individually with senior managers to discover the problems underlying the overall business. Big Y type issues can be found by asking senior division managers (e.g., human resources manager, maintenance manager, plant manager, etc):
- What are their major concerns within their division?
- What is their division’s actual performance versus target?
- What are their performance results from past years and identify:
- Gaps in performance
- Less dollars (revenue, profit, etc.) than expected
- Areas they think the division could do better in but did not
- What comments or feedback have they received from their customers?
Below are some possible areas to investigate:
- Finance – Investigate overhead costs, expenses and payment from debtors.
- Operations – Look at delays, quality issues and unplanned shutdowns.
- Maintenance – Examine reliability and availability.
- Human Resources – Consider staff turnover and sick leave.
- Safety – Probe into the most frequent injury and location of injuries.
Step 2: Consolidate the Issues and Confirm
Structure the ideas and areas of concern from Step 1 and categorize them into areas of similar subject (i.e., production, maintenance, human resources, etc.) making use of affinity diagrams. Be prepared to pull out just-do-it projects during this step.
After consolidating the issues, confirm the categories with senior management. Champions or Master Black Belts should briefly meet with each senior manager again and review the affinity diagram results. This is senior management’s chance to verify these are indeed the main issues facing the organization.
Step 3: Review Meeting with Senior Management
Conduct a meeting with all the senior managers interviewed in Step 1 and present the consolidated concerns. As a team, drill down into the issues behind the concerns. Ask root cause, 5-why and cause-and-effect type questions. The objective is to determine the specific, key issues senior management wants fixed.
This meeting has a useful side effect – getting all senior management on the same page, building the burning platform for change. The senior management team sees the need for the continuous improvement effort, strengthening their commitment to the Six Sigma initiative.
Step 4: Develop a Picture of Projects
Using the issues stemming from Step 3, meet individually with staff who report directly to senior management to drill down into more specific issues. These people may include plant and maintenance managers, financial accountants or safety supervisors.
Try to validate each issue by asking for numbers, trends, performance charts, etc. Also try to determine which level of Six Sigma expertise may be most appropriate for each project (i.e., Black Belt, Green Belt or just-do-it). At the end of this step, a clear picture of specific projects should emerge.
Step 5: Prioritize Project List
Champions and Master Black Belts next need to prioritize the list of projects from Step 4 using tools such at the pay-off matrix, criteria rating (the table below), or failure mode and effects analysis. When prioritizing, take into consideration:
- Feedback from the meetings with senior management and their direct reports.
- Divisional key performance indicators or measures.
- One- to five-year corporate and site goals.
- The voice of the customer.
- The voice of the business.
- Time and ease to complete each project.
- Black Belt, Green Belt and divisional resources.
Criteria Rating – Project Prioritization | |||||||
|
Criteria |
Project |
|
|
|
|
|
Return on Investment |
4 |
> 50% = 5 |
4 x 3 = 12 |
4 x 1 = 4 |
4 x 1 = 4 |
4 x 5 = 20 |
4 x 3 = 12 |
Contribution to |
2 |
High = 5 |
2 x 2 = 4 |
2 x 3 = 6 |
2 x 2 = 4 |
2 x 3 = 6 |
2 x 3 = 6 |
Addresses Voice |
3 |
Yes = 5 |
3 x 5 = 15 |
3 x 1 = 3 |
3 x 1 = 3 |
3 x 3 = 9 |
3 x 1 = 3 |
Change |
1 |
Easy = 5 |
1 x 1 = 1 |
1 x 2 = 2 |
1 x 1 = 1 |
1 x 4 = 4 |
1 x 4 = 4 |
Overall Rating |
 |  |
32 |
15 |
12 |
39 |
25 |
Step 6: Assign People to Projects
Assign the right people to the right projects. Six Sigma project leaders and team members must have the appropriate training, skills, energy, experience and authority to make improvements on their assigned projects. They also must be allowed time to investigate, analyze and improve the issues properly.
Champions and Master Black Belts need to know the strengths, weaknesses and availability their Black Belts and Green Belts well before assigning projects to them. Anything less is just playing lip-service to Six Sigma initiatives.
Six Sigma Champions and Master Black Belts should constantly work on identifying Six Sigma projects. Over the long term, it is their responsibility to create an easy access and user friendly repository, where any member of the organization can drop ideas or opportunities for projects that can later be more clearly defined and be fed into the pipeline.

By working through this six-step process (figure above) every three to six months, projects can be quickly found and the pipeline kept full. Depending on availability, the project review can take several days to complete, yet it builds a firm foundation for maintaining a strong project pipeline, continuing the Six Sigma initiative and driving continuous improvement. Finally, this process drives commitment by giving senior management and staff an opportunity to contribute to the Six Sigma effort.