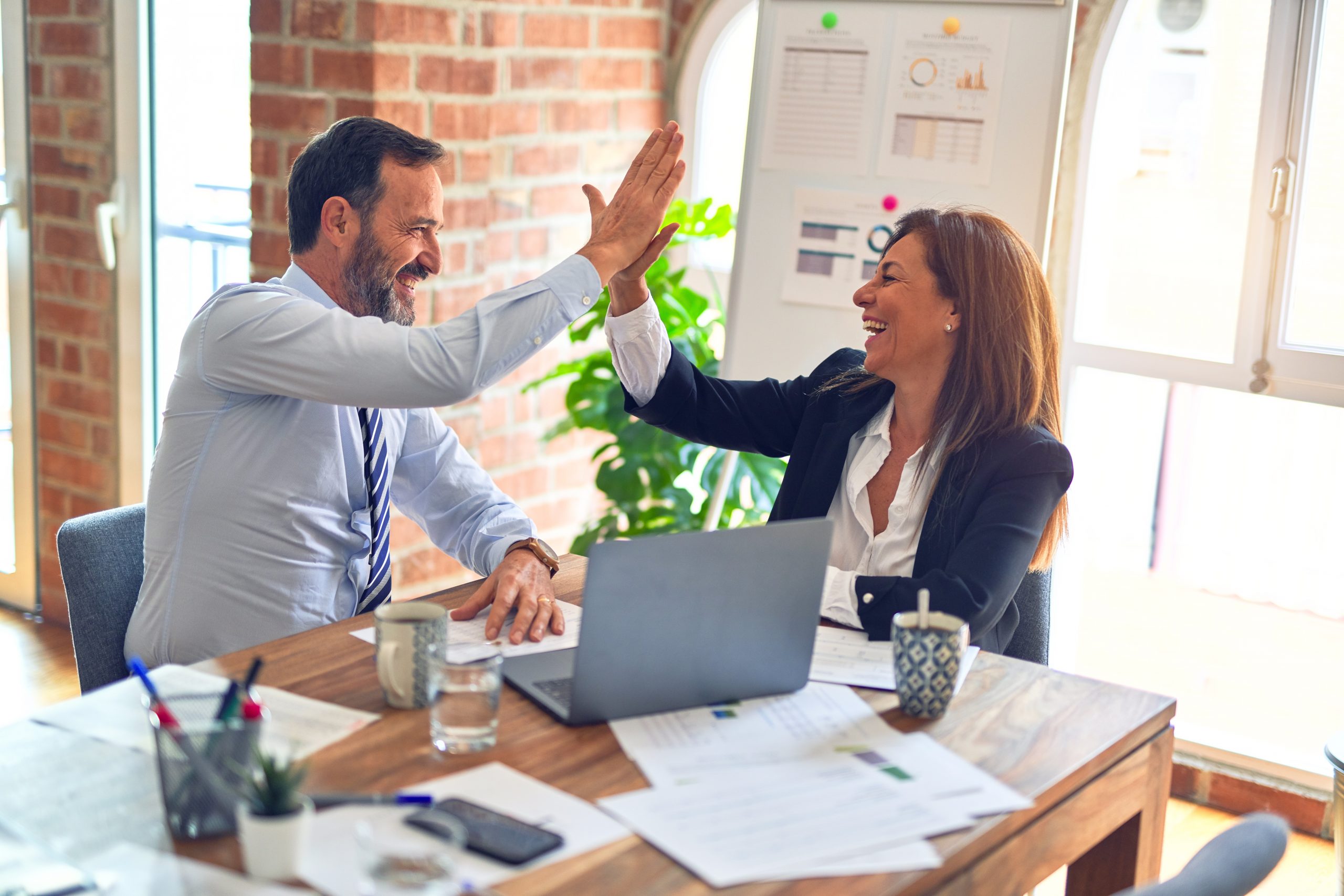
Providing Six Sigma project leaders with appropriate project definitions is an underestimated challenge in managing Six Sigma initiatives. Project charters typically contain project scopes too broad or too high level, with weak or unclear problem and goal statements. This can cause newly trained project leaders to use their precious time trying to “boil the ocean.”
One of the key success factors for Six Sigma programs is establishing good project starting points through appropriate problem definitions. How should this be approached? A simple 1-2-3 model (Figure 1) can explain roles and responsibilities in selecting projects. The 1-2-3 model shows that strategic improvement initiatives need to be started at the top, and that a natural downward flow, in which everyone understands his or her role, is critical
The 1-2-3 Model
Level 1. Top management decides to launch Six Sigma to confront serious business challenges (the big Ys).
Level 2. The next step is to establish people, usually in middle management, as process owners and project sponsors. The process owner is a role required in any company serious about process management. Project sponsors may even be recruited from senior management if their influence will effectively help the team overcome roadblocks.
Players on Level 2 look for improvement potential within the corporate process landscape. To do this, they need to translate the business goals into process goals. They have to identify those processes whose outcomes (the little y’s) are currently not meeting targets and are constraints to achieving the higher level business goals.

Level 3. The resulting improvement ideas from level two are distributed to project leaders – Green Belts and Black Belts – as first draft project definitions. The Belts fine-tune their assigned project definitions, gather data and analyze the root causes of variation in their assigned y-variables.
Though this sounds simple enough, in practice, many organizations initially fail to grasp or choose to overlook the importance of following the ordered top-down deployment flow. They follow a pattern of 1-3-2 instead of 1-2-3.
Arguably, this pattern might have some advantages, explaining why it is so common. For example, an organization may jump from level one directly to the launching of projects at level three to get fast process improvement and financial results. Or perhaps middle management is too busy or hesitant to participate in yet another quality program, so its formal involvement is postponed until later.
However, the 1-3-2 approach often results in some serious problems that can stall a Six Sigma program and threaten its long-term success.
An Example of Not Following the 1-2-3 Model
Top management at one company decides to launch Six Sigma and does so with much fanfare. Leadership wants to see significant project results within the year, as this will win over the skeptics and get stakeholders on board quickly. To this end, a large-scale Black Belt training program is immediately launched to train people as improvement project and business unit leaders. Department heads are asked to identify candidates and supply them with suitable project definitions to bring to the first day of training.
So far so good? Not really. Level one (top management) and level three (project leaders) have been formally mobilized by now. Middle management, however, has merely been asked to cooperate. They may be inadequately informed about Six Sigma goals and the roles they are expected to play as process owners and project sponsors. They also have not been told what constitutes suitable Black Belt project definitions.
The results are almost predictable. Black Belt candidates are handed project charters from inexperienced process owners. The projects have broad titles such as “Reduce Excessive Costs at Plant A” or “Increase Falling Sales for Product B.” Of course, high costs and falling sales are important business issues, but they are not the type of process-specific problems that are the starting points and focus of Six Sigma improvement projects.
The Black Belts-in-training must spend weeks, or even months, trying to comprehend the cost structures of plant A, or customer complaints and sales patterns for product B. This is not the job of a Black Belt in a properly defined project. Such broadly drawn project charters could send them down the wrong path.
As Black Belt training nears its end, many trainees are still struggling with project definitions. Unfortunately, this leads to misunderstandings with disappointed managers who assumed all their business headaches would be solved in a single project. The Six Sigma engine is sputtering, and frustration is mounting on all fronts.
The confusion and loss of momentum could have been avoided through a consistent, top-down Six Sigma deployment.
A Better Example of Six Sigma Deployment
To stay competitive, top management at another company determines costs must be reduced and customer satisfaction increased. A Six Sigma program is initiated to address these urgent issues and to prepare for future issues.
At a briefing, middle managers learn that the major business targets (and big Ys) are to reduce costs and customer complaints at plant A. Local management at plant A is asked to take steps within given budgets to meet the new targets.
After receiving Six Sigma awareness training and participating in workshops to learn basic tools and better understand their jobs within the overall program, the local managers now know that after accepting their business assignments, they must move from the business level into the process level and become process owners seeking process improvement potential.

Instead of launching massive improvement projects with broadly stated goals, the new process owners work together in a team to drill down from the original business issues to discover the individual process problems. To do this, they use their dashboard process performance results and other high level data as well as standard Six Sigma tools such as voice of the customer research and SIPOC (suppliers, inputs, process, output, customers) diagrams in a form of pre-analysis.
The pre-analysis identifies a series of little-y issues such as employee discipline (e.g., absenteeism), slow cycle times, high product defect rates and machine downtimes. These, in turn, are causing plant A’s high costs at the big Y level. After prioritizing these problems and identifying the corresponding processes that require immediate attention, individual project charters are drafted to address them. These are then distributed to Black Belt candidates, who are about to begin their training. They are then asked to form a team and formally kick off their assigned projects to validate the root causes for the well-defined y-variables.
Depending on the number of Black Belts available, finding all the potential for achieving the full business goal of reduced costs at plant A could take one or two years. But the project pipeline is now flowing. And a system (Figure 2) has been put in place to implement Six Sigma further down in the organization.
Conclusion: Another 1-2-3
Three key factors for Six Sigma project success are:
- Define projects in the processes themselves – not on the balance sheet or in the boardroom – to provide project leaders with suitable starting points.
- Improvement projects should address specific problems within limited scopes in order to avoid overwhelming resources and overextending project timelines.
- Engage middle management as the program is being deployed and, in the long run, have the process owner doing the pre-analysis work as the main link – or translator – between business imperatives and process issues.