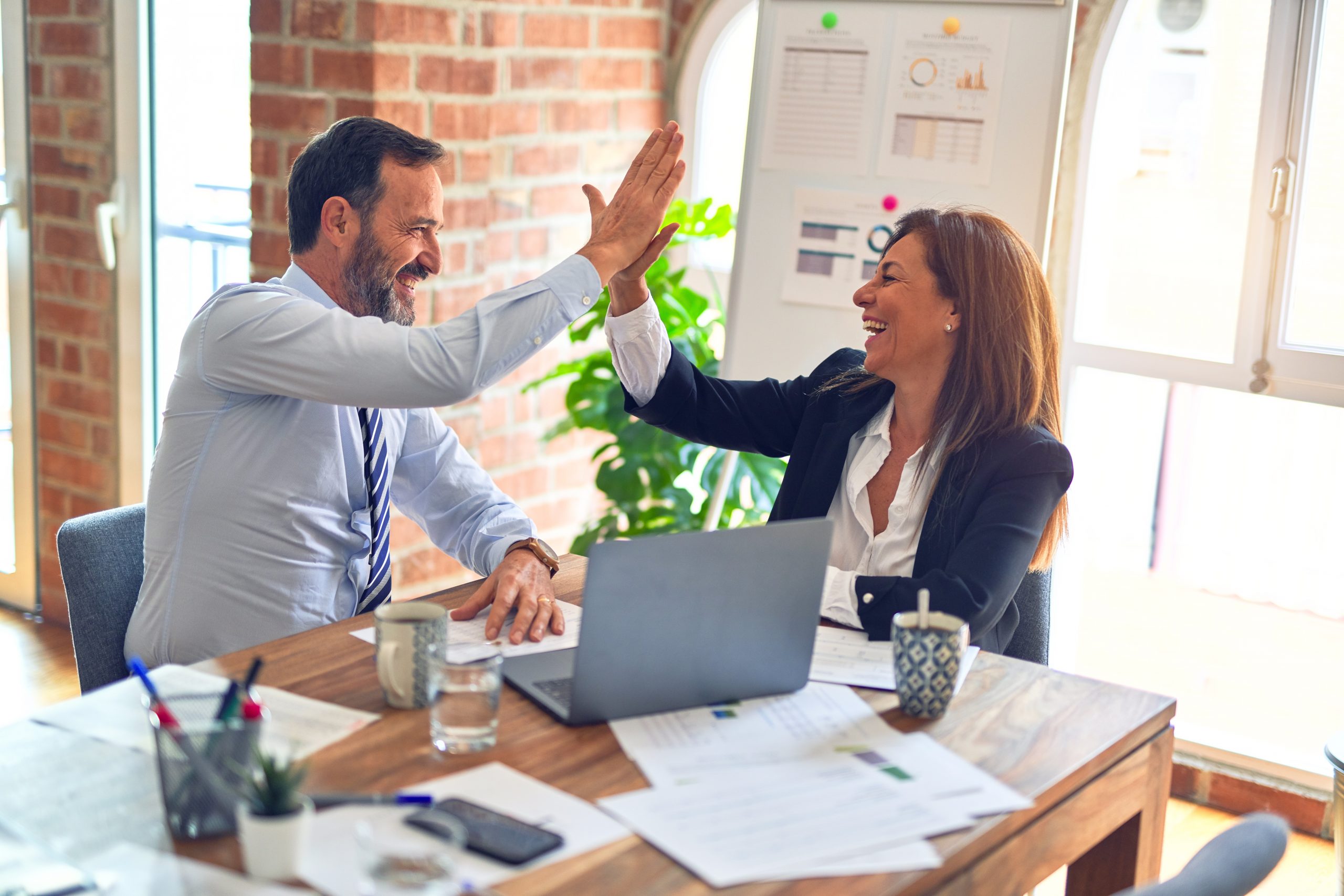
Capability Maturity Model Integration (CMMI) is a framework for business process improvement. Like any model, CMMI reflects one version of reality, and like most models, it may be more idealistic than realistic in some ways. Organizations can use the model as a jumping off point to create process improvement solutions that fit their unique development environment.
One way organizations have adapted CMMI is to integrate it with the Six Sigma DMAIC roadmap. The two frameworks complement each other’s strengths and combining the two can help accelerate quality improvements.
Six Sigma Tools in CMMI
Like a Six Sigma project, CMMI is essentially process oriented. Each method follows through certain phases. For a typical Six Sigma project, the phases are Define, Measure, Analyze, Improve and Control. CMMI follows maturity levels, from L2 (Managed) to L3 (Defined) to L4 (Quantitatively Managed) to L5 (Optimizing). Some of the tools used when following the DMAIC roadmap also can aid an organization in reach the next CMMI level (Table 1).
Table 1: Six Sigma-CMMI Matrix
Level | Process Area and Link to Six Sigma Phase |
L-2 (Managed) | Process and product quality assurance Measurement and analysis – Measure Configuration management Supplier agreement management Project monitoring and control – Control Project planning – Define Requirements management – Analyze |
L-3 (Defined) | Decision analysis and resolution – Analyze Organizational training – Improve Organizational process definition – Define Organizational process focus – Improve Risk management Integrated project management – Define, Control Validation Verification Product integration Technical solution Requirements development – Define |
L-4 (Quantitatively Managed) | Organizational process performance – Analyze Quantitative project management – Measure, Analyze, Control |
L-5 (Optimizing) | Causal analysis and resolution – Analyze Organizational innovation and development – Improve |
Some of the process areas can be attributed and linked to corresponding DMAIC phases, as shown in Figure 1.
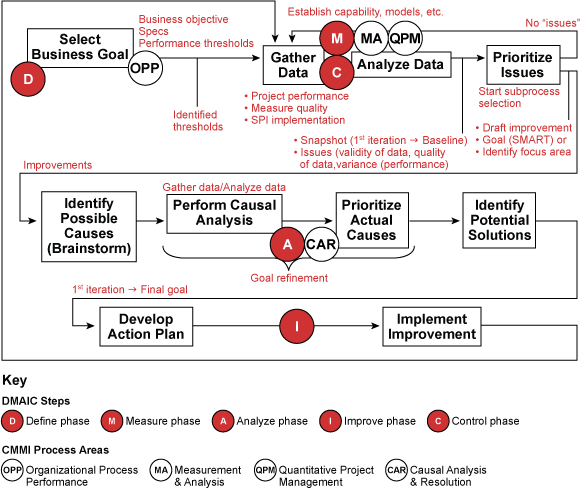
This map can help spread the CMMI message through the more common Six Sigma approach. It may work to dispel the myth that CMMI is predominantly used in the IT sector but not in other sectors. This figure demonstrates the use of CMMI, irrespective of the industry or domain.
Case Study
When one particular service-industry company decided to go for CMMI L5 certification, they leveraged the strengths of Six Sigma and used it as a spring board to achieve the certification in a shorter time and without redoing the documentation and reinventing the wheel.
To transition to L5, the company needed to make quality improvements. They did this by adopting Six Sigma to help stabilize processes and reduce variation.
For example, one of the metrics the company was trying to improve was cost of quality (COQ). This was measured as the total hours spent doing quality control and rework for a deliverable divided by the total hours taken to complete the deliverable, multiplied by 100. They approached this issue using DMAIC.
Define
The team used voice of the customer and a SIPOC (suppliers, input, process, output, customers) diagram to define the problem and identify critical-to-quality characteristics. They defined the problem as high cost of quality. COQ for the month was the average COQ for each of the deliverables.
Measure
They measured the current COQ level, using the formula above.
Analyze
The analysis involved identifying the type of errors in the deliverables and listing the number of errors identified, capturing the quality control times taken to identify those errors and the time taken to rectify those errors. The team created a Pareto chart of the COQ for the various deliverables. Then, they analyzed the causes of the errors that were causing the high COQ.
Improve
The team brainstormed to determine an action plan for addressing the root causes. They implemented the action items and gathered data for the next set of deliverables.
Next, they calculated the COQ for the new set of deliverables. Using the two-sample t-test, they compared the new average against the corresponding average before implementing the actions.
Control
The change in the averages indicated the effectiveness of the process change. The team continued to monitor the COQ data using a control chart for the next few months. Any reoccurrence of the out-of-control situation would be handled by following the DMAIC approach.
Once a process is established, matured and the data variation is stable for a couple of months, the internal target is redefined and the bar is raised further. This revised target becomes the target to be achieved for the subsequent months (Figure 2). This shows the maturity of the process and effectiveness of Six Sigma in achieving and sustaining CMMI L5.

Recognizing the Differences
Although Six Sigma can help a company achieve higher levels in CMMI, the two methods do have some significant differences (Table 2).
Table 2: Differences Between Six Sigma and CMMI
Six Sigma | CMMI |
Assumes processes have been identified and defined | Focus on defining management and technical processes early |
Doesn’t distinguish between organizational standards and project processes | Organizational process definition is used to capture best practices |
Emphasis on training to motivate and communicate skills | Emphasis on infrastructure to ensure that the key processes are addressed |
Relies on statistical methods to manage performance | Statistical approach is intended but often not implemented |
Focus on learning from internal experience and data | Additional mechanisms to leverage external technology |
Prioritization of efforts based on business payoff | Link to strategic planning weak and often ignored |
Certification of individual practitioners, not organizations | Certification of assessors and organizations, not practitioners |