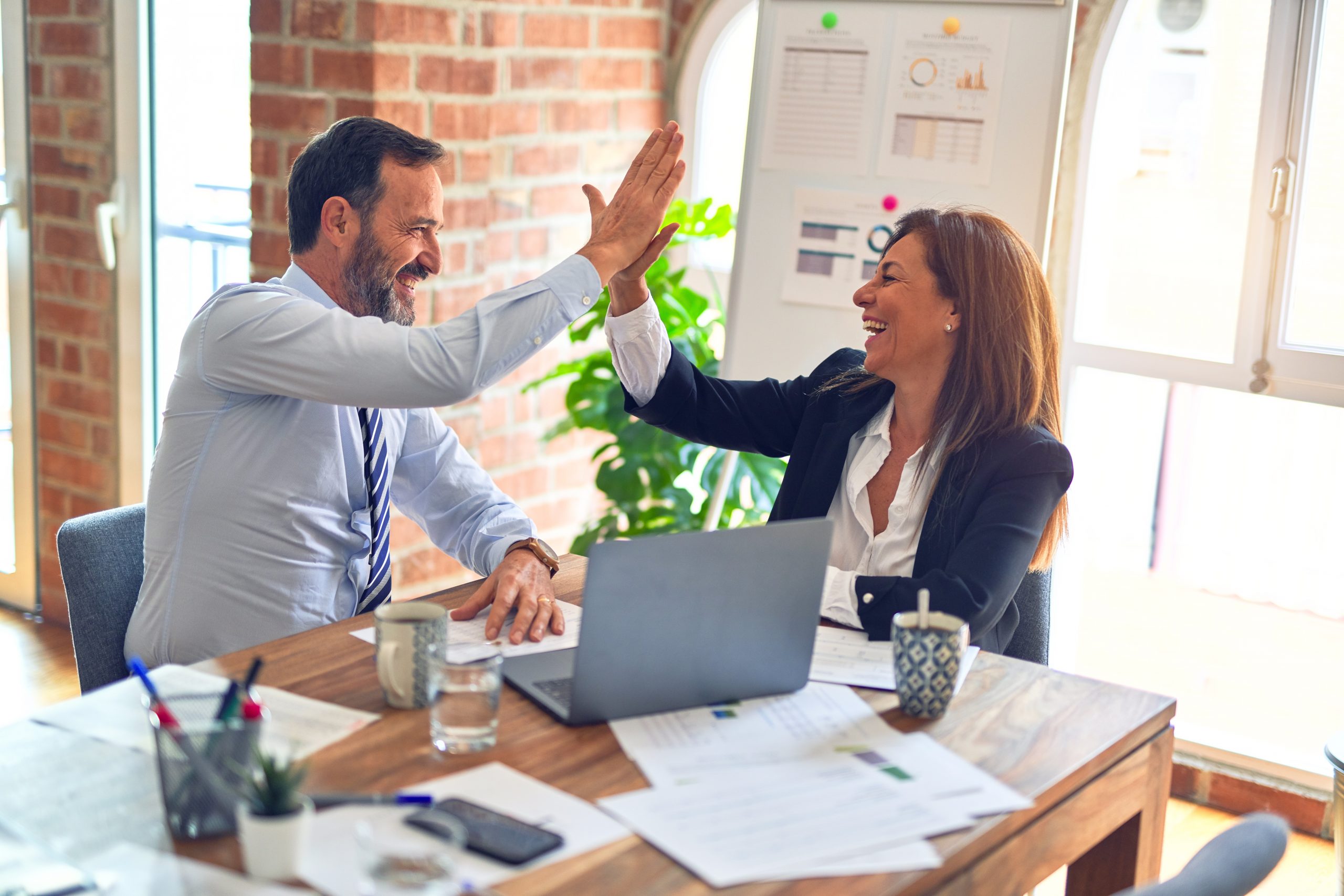
Process mapping is a technique for making work visible. A process map shows who is doing what, with whom, when and for how long. It also shows decisions that are made, the sequence of events and any wait times or delays inherent in the process.
Process maps are good for streamlining work activities and telling new people, as well as internal and external customers, “what we do around here.” They also can help in the effort to reduce cycle time, avoid rework, eliminate some inspections or quality control steps, and prevent errors.
Once a process map is completed, the team that put it together will analyze it. There has probably never been a process map developed where someone has not said, “Do we still do that?” or “Why does X happen there?” or “Why are we doing it that way?” or “I did not realize….”
The analysis is no more than considering the process activities and flow by:
A. Looking at each process step for:
- Bottlenecks
- Sources of delay
- Errors being fixed instead of prevented (rework)
- Role ambiguity (we did not know who…)
- Duplications
- Unnecessary steps
- Cycle time
B: Looking at each decision for:
- Authority ambiguity (two or more people get to decide…)
- Are the decisions needed at this point?
C: Looking at each rework loop for:
- Possibly eliminating the step(s) or doing in less time, or trying to prevent
D: Using the customer’s point of view
- Value-added versus non-value-added steps (from the customer’s point of view)
Below is a chart which provides a checklist of things to Be On the LookOut for when mapping and analyzing any process. Items on the list are, of course, called BOLOs, for short.
BOLO List in Process Mapping | ||
1. | Assumptions | Challenge all assumptions: It is easy to forget that a process step was based on one or more assumptions and not fact. |
2. | Changes | Idiosyncratic change or changes made to be creative or for some other reason that are NOT linked to the business plan or a business need. |
3. | Duplication | Duplicate data entry. |
4. | Duplication | Duplicate work steps in another group. |
5. | Flexibility | Can the process respond to changes in customer/technology requirements? Is it flexible? |
6. | Forgot how, or too complex | Mistakes because of a complex-clerical procedure or mistakes because people forgot what to do: Consider job aids: list, checksheet, flowchart, picture, etc. |
7. | Intermediaries | When you hear words like “coordinate,” “pass it by me first,” “expedite” and “liaison,” question whether the intermediary step is value added. |
8. | Lack of consequences | Standards not followed and there is no consequence or negative feedback. |
9. | Old ways | Tools/software available that is not used because people have not taken time to get trained or do not want to. |
10. | Old ways with new tools | Lots of steps in software that are just replicating the old by-hand process. |
11. | Paper records | Is the process adding, maintaining or eliminating paper records? |
12. | Quality control | Quality control (QC) of work when the supplier could have checked and sent 100 percent ok input to you. |
13. | Quality control | QC is when someone else checks work not when someone checks their own work. |
14. | Quality control | When talking about QC consider poka yoke – can the work be mistake proofed to make it impossible for the defect to be passed on? |
15. | Quality control | Is the QC really needed? Prevention instead of detection is the desired process. |
16. | Repetition | Can repetitive work be automated? |
17. | Resistance | Do professionals want to make changes rather than “stick with the standard” or do what they want, saying there is no standard since they did not agree to it. |
18. | Resistance | Someone continually saying this will not work, cannot make any changes. Focus on objective and say that changes to improve the process is why we are here. |
19. | Scalability | Is the process limited to the current workload? Is it scalable to handle a larger volume of work? |
20. | Specifications/every time like first | Developing specifications each time something is done instead of the first time as a standard or template. |
21. | Supplier input | Input supplier sends inaccurate/incorrect input. Ask if they know what to do. |