isixsigma.com

Process Control Plan: A Roadmap to Process Success
Published:In Six Sigma, you will often hear the phrase, “It worked so well we stopped doing it.” The purpose of a process control plan is to maintain the gains of your project and prevent this from happening.
Read more »
What Are the 7 Wastes of Lean?: How to Identify and Eliminate Them
Published:Waste is all around your organization. Using the acronym TIMWOOD, you will learn how to identify the 7 wastes of lean and eliminate them to improve your organization.
Read more »
First-Time Yield: The Key to Minimizing Rework and Improving Efficiency
Updated:The purchasing department manager left another message, informing the planning department that they once again sent over a request for a quote that didn’t contain all the information needed to place the order. It’s a problem that seems to keep repeating, but is it truly that impactful an issue? To better understand the situation, the […]
Read more »
The Importance of Implementing Effective Metrics
Published:When a company promises and delivers on quality, there is a good chance that customer satisfaction and retention will be high. But paving the road to success depends on companies being well-informed about their own business. They achieve that knowledge by developing and utilizing effective metrics. Why Do We Need Them? Metrics are […]
Read more »
A Guide To Remote Work, And The Major Trends Today
Updated:DISCLAIMER: We have a newer version of this article, which you can view here. Remote work has been around for years now. However, the recent COVID-19 pandemic showed the flexibility of working from home for some of your team members. With that in mind, we’re going to take a deeper look at remote […]
Read more »
How the Taguchi Method Simplifies Experimental Design and Analysis
Updated:When you have multiple factors at different levels, it can be challenging to figure out which is the optimal combination. Design of Experiments is one common method you can use. The Taguchi Method is another.
Read more »
Operations Process: The Plan for Your Organization’s Success
Updated:When it comes to getting a task accomplished, having an operations process greatly increases the probability of success.
Read more »
Repeatability vs. Precision: What’s the Difference?
Published:Repeatability vs. precision, how do they apply to your workflow? Six Sigma is filled with different tools, terms, and methodologies applied across the production line. Today, we’re looking at two core concepts that deal with the accuracy of your processes. What Is Repeatability? Repeatability is the typical variation that occurs when a person […]
Read more »
Introduction To Robust Design (Taguchi Method): Increase Productivity and Customer Satisfaction
Updated:The Robust Design method, also called the Taguchi Method, pioneered by Dr. Genichi Taguchi, greatly improves engineering productivity. By consciously considering the noise factors (environmental variation during the product’s usage, manufacturing variation, and component deterioration) and the cost of failure in the field the Robust Design method helps ensure customer satisfaction. Robust Design focuses on […]
Read more »
The Power of Special Cause Variation: Learning from Process Changes
Updated:This article will introduce you to special cause control chart patterns. You will learn why special cause variation is one of the foundational concepts in quality improvement and the use of special cause variation in process improvement.
Read more »
6W Methodology: Master Problem Analysis With Ease
Published:6W? 5W1H? 5W? The bigger question is, how do you make sure you’re asking the right questions to guarantee you properly solve your problem or execute your project?
Read more »
Plackett-Burman Experimental Design: When and How to Use It in Your DOE
Published:Plackett-Burman experimental design is used to identify the most important factors early in the experimentation phase when complete knowledge about the system is usually unavailable. Developed in 1946 by statisticians Robin L. Plackett and J.P. Burman, it is an efficient screening method to identify the active factors using as few experimental runs as […]
Read more »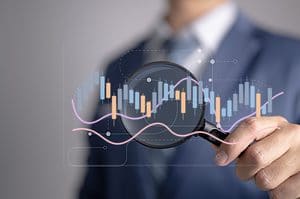
Making Sense of the Two-Sample T-Test: Supercharge Your Hypotheses Tests
Updated:The two-sample t-test is one of the most commonly used hypothesis tests in Six Sigma work. It is applied to compare the average difference between two groups. You use it to determine if the difference is significant or if it is due instead to random chance. It helps to answer questions like whether the average […]
Read more »
Margin of Error and Confidence Levels: Make the Most of Your Customer Surveys
Published:Do you know how to account for the margin of error in your customer surveys? A survey is a valuable assessment tool in which a sample and information relate to a larger population. Surveying is like tasting a soup, a few spoonfuls tell what the whole pot tastes like. An Example of Margin […]
Read more »
Six Sigma Methodology: Using the Five W’s and One H Approach
Updated:How do you implement the Six Sigma methodology? Consider the 5W1H approach when implementing it for your organization. 5W1H (who, what, where, when, why, how) is a method of asking questions about a process or a problem taken up for improvement. Four of the W’s (who, what, where, when) and the one H are used […]
Read more »
Lead Time vs. Cycle Time: What’s the Difference?
Published:Lead time vs. cycle time, which do you choose? Improving your processes is a nuanced and complicated thing. Understanding the difference between the various measurements of time can only benefit your workflow. So, let’s dive into what this means and how it applies to your production. What is Lead Time? Lead time is […]
Read more »
Understanding Poka-Yoke: Eliminating Defects with Proactive Measures
Updated:What is poka-yoke? Have you ever accidentally microwaved your face? No? You’ve never opened the microwave door while it was cooking and accidentally exposed your face to microwave energy? I know that you haven’t because whenever you open the door, the microwave stops running. There is a switch that triggers when the door is opened […]
Read more »
Why Upper Specification Limits Matter in Process Improvement
Updated:The upper specification limit represents the highest limit that a measurement or reading can reach and still be acceptable to the customer. There are several benefits of monitoring USL and determining if a process can satisfy customer requirements.
Read more »
1.5 Sigma Process Shift: What It Means For Your Business
Updated:Why is 6 sigma 3.4 ppm, not 2 ppb? The calculation of process sigma after a process improvement project should be reported as short-term sigma.
Read more »
Voice of the Business: Benefits and Uses for Your Organization
Updated:Do you hear voices? In a business context, that’s normal. Let’s listen in to the voice of the business and hear what it has to say.
Read more »
Out of Control Action Plan: Correcting Process Variants for Optimal Performance
Updated:Out-of-control Action Plans (OCAPS) are a piece of the Lean Six Sigma methodology that is often overlooked. Though they have been phased out in some organizations, it is important to understand their purpose and how they can help a company improve its processes.
Read more »
What You Need to Know to Calculate CP and Interpret Its Value
Updated:Cp is one of the metrics calculated for determining whether your process is capable of meeting customer specifications or requirements. It is useful in comparing different functions and their ability to meet their unique specifications.
Read more »
Revolutionizing Organizational Change with the CAP Approach
Updated:Do you feel that implementing change in your organization is going too slowly? So did Jack Welch of GE, which is why GE developed the Change Acceleration Process (CAP). Let’s explore how the concepts of CAP might help your organization.
Read more »
Cycle Time vs. Throughput Time: What’s the Difference?
Updated:Cycle time vs. throughput time, do you know the difference? Typically, when we look at the steps of our workflow, you’ll want metrics to gauge effectiveness and efficiency. Depending on the scenario, you’ll want to use one of these two metrics while looking at the work time needed to complete a deliverable. What is Cycle […]
Read more »
B10 Life: Engineering Products for Reliability
Published:As competitive and market pressures increase, having a clear understanding of product reliability, service life, and expected failure rate is crucial. We explore how by utilising B10 life, we can optimise our product development and satisfy our customer requirements.
Read more »
Mastering the Basics: The Fundamentals of Statistics and Inference
Updated:Statistics is a branch of math that involves the collection, description, analysis, and inference of conclusions from quantitative data. But what is a statistic? Let’s find out. The word statistic is a word with numerous possible definitions. In its simplest form, a statistic can be defined as a descriptor of a set of data. The […]
Read more »
Understanding Exponentially Weighted Moving Average for Time Series Analysis
Updated:Does your data from yesterday represent the current state of your process better than that from a month ago? How can you place more emphasis on it yet still make use of older data? That’s what the Exponentially Weighted Moving Average does.
Read more »
Tangible vs. Intangible Benefits: What’s the Difference?
Updated:Do you know the difference between tangible vs. intangible benefits? Measuring the results of your company’s output can be of vital importance. Understanding how these two measurements line up and differ from one another can help refine productivity. Additionally, failing to pay attention to these measurements could have serious ramifications. What Are Tangible Benefits? Tangible […]
Read more »
How House of Quality Shapes Product Excellence: Meet Your Customer’s Needs
Updated:House of Quality? No, this is often referred to as a House of Pain because of the effort needed to complete one. Let’s see if we are just being overly pessimistic.
Read more »
What Is Six Sigma?: Transform Your Organization’s Productivity
Updated:Six Sigma at many organizations simply means a measure of quality that strives for near perfection. Six Sigma is a disciplined, data-driven approach and methodology for eliminating defects (driving toward six standard deviations between the mean and the nearest specification limit) in any process — from manufacturing to transactional and from product to service.
Read more »
Sigma to DPMO to Yield to Cpk Table: Take Control of Your Data
Updated:Use this table to go between and convert Sigma to DPMO to Yield to Cpk.
Read more »
Null Hypothesis vs. Hypothesis: What’s the Difference?
Updated:Null hypothesis vs. hypothesis, which is the right choice? When you get into the different methods of analyzing data, there is no shortage of tools at your disposal. Understanding the difference between a null hypothesis and a hypothesis can make or break your testing and analysis stages. Let’s dive into both of these tools and […]
Read more »
Driving Quality Improvement with DPMO: A Roadmap to Process Excellence
Updated:Lean Six Sigma professionals, much like every other professional, love to talk in acronyms. The acronym of the day is DPMO. Let’s check out what it means.
Read more »
Defects per Opportunity (DPO): Get Context for the Flaws in Your Processes
Updated:Defects per opportunity, or DPO, refers to the number of defects that occur in relation to a given number of opportunities for which an error could occur. Let’s consider some of the benefits of measuring and monitoring DPO.
Read more »
Flowchart vs. Process Map: What’s the Difference?
Updated:Flowchart vs. process map, what do you choose to use? When it comes to mapping out a project, you’ve got several choices on how to visualize them. If you’ve had trouble deciding on a format for your visualization, then read on. Today’s guide is meant to cast more light on these individual tools and how […]
Read more »
Rolled Throughput Yield (RTY): Make Sure Your Production Is Making the Grade
Updated:What is rolled throughput yield? Your company has just announced that its product line has a 100% total throughput rate, touting it as a great win for everyone. However, from your perspective, you see massive amounts of rework being performed, disrupting the production lines, costing additional money, and impacting on-time delivery. If only there was […]
Read more »
How to Use Voice of the Customer to Improve Customer Experience
Updated:An organization may hear many voices (Customer, Business, Employee, and Process). It is the voice of the customer (VOC) that is the driving voice. Additionally, it is what should be important to the organization and what the organization should focus on. The satisfaction of the VOC needs to be balanced against the Voice of the […]
Read more »
How ZARA Revolutionized the Fashion Industry with Lean Practices
Published:ZARA changes its clothing designs every two weeks, offering 11,000 distinct garments annually. In comparison, competitors change their designs every three or four months and produce 3-4,000 distinct pieces. This is fast fashion: the business model of replicating high-fashion, luxury-brand pieces quickly and cheaply, making them available to customers while the trend and […]
Read more »
Calculate Capability Indices with Only One Specification
Updated:How do you calculate capability indices? Capability analysis is an essential tool for statistical process control (SPC) and process improvement, applicable to a variety of environments from hospitals and labs to assembly and manufacturing. How to Calculate Capability Indices The formula for calculating a Cpk index is easily found: USL, upper specification limit; LSL, lower […]
Read more »
The Harada Method: Templates to Measure Long-term Goal Achievement – Part 2 of 2
Updated:The Harada method helps individuals achieve self-reliance which in turn facilitates a company’s process improvement journey. Part One provides an overview of the method and its genesis. Subsequently, part Two presents five templates to use to plan a goal, measure the goal’s progress, and assess success. An example helps illustrate their practical use. As described […]
Read more »
How to Foster a Culture of Innovation and Agility in Startups
Published:In today’s fast-paced, technology-driven world, fostering a culture of innovation and agility is essential for startups that want to stay competitive. Startups thrive on innovative ideas, quick pivots, and the ability to adapt to change. This 2014 article raised awareness of Lean Startups. But creating an environment where continuous improvement and creativity flourish […]
Read more »
Value Stream Map vs. Process Map: What’s the Difference?
Updated:Value stream map vs. process map, which is better for you? As with many tools and methods in Six Sigma, there isn’t a one-size-fits-all approach to mapping things out. Both of these tools have specific functions with some overlap. If you’re new to Six Sigma, then you’re in luck. Today, we’re going in-depth into how […]
Read more »
Case Studies: Startups That Scaled Using Lean Methodologies
Published:Lean Startup methodologies have revolutionized the way modern entrepreneurs approach launching and scaling their businesses. At the core of Lean Startup is the idea of minimizing risk through rapid experimentation, customer feedback, and iterative development. This approach enables startups to efficiently test their business models and products with minimal resources while remaining adaptable […]
Read more »
Root Cause Analysis: Integrating Ishikawa Diagrams and the 5 Whys
Updated:Root cause analysis (RCA) is a way of identifying the underlying source of a process or product failure. As such, then the right solution can be identified. RCA can progress more quickly and effectively by pairing an Ishikawa diagram. You can also use the scientific method in the form of the well-known plan-do-check-act (PDCA) cycle […]
Read more »
Repeatability vs. Reproducibility: What’s the Difference?
Updated:Repeatability vs. reproducibility, which should you use? Repeatability and reproducibility are two ways that scientists and engineers measure the precision of their experiments and measuring tools. They are heavily used in chemistry and engineering and are typically reported as standard deviations in scientific write-ups. While these two measurements are both used in many types of […]
Read more »
Navigating Data Analysis: The Importance of Testing for Normality
Updated:Is your data normal? Oh no! Is that a problem? The concept of data normality can be important when using certain statistical tools to make data-driven decisions.
Read more »
Dealing with Non-normal Data: Strategies and Tools
Updated:What is non-normal data? Normally distributed data is a commonly misunderstood concept in Six Sigma. Some people believe all data collected and used for analysis must be distributed normally. But normal distribution does not happen as often as people think, and it is not a main objective. Normal distribution is a means to an end, […]
Read more »
Application of Lean Six Sigma to the EHS Function of an Organization
Updated:Lean Six Sigma (LSS) is a structured approach that combines two powerful process improvement methodologies: Lean, which focuses on eliminating waste, and Six Sigma, which focuses on reducing variation and defects. When applied to the Environmental, Health, and Safety (EHS) function of an organization, Lean Six Sigma provides a robust framework for driving operational efficiency, […]
Read more »
Understanding the Formula and Benefits of Cycle Time
Updated:The customer just called again, wondering if the item they ordered will be on time. Will it? Do your company’s processes make it possible to be on time per the customer’s needs? To know that requires understanding how long it takes to produce the product, and that requires knowing your cycle times. An Overview: What […]
Read more »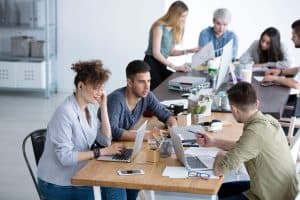
Common Mistakes When Using SIPOC
Updated:What are the most common mistakes when using SIPOC? The SIPOC Diagram is one of the most useful tools in your arsenal when it comes to process analysis. It readily allows you and your team to grasp the various elements of a process before diving fully into detail on how everything fits together. That said, […]
Read more »