isixsigma.com

Comparing and Contrasting AI, CI and Big Data
Published:AI (Artificial Intelligence) involves creating systems and algorithms capable of mimicking human intelligence to perform tasks like decision-making, problem-solving, and pattern recognition. It leverages techniques such as machine learning and neural networks to improve through experience. Continuous improvement focuses on systematically enhancing processes, products, or services through incremental changes, using methods like Lean […]
Read more ยป
Real Life Examples of Quality Management That Worked
Updated:Quality management is the process of ensuring that products and services meet consistent standards of excellence. It encompasses various strategies, tools, and techniques that aim to enhance organizational performance, improve customer satisfaction, and reduce waste. Many businesses around the world have effectively utilized quality management principles to drive significant improvements. Over the years there have […]
Read more ยป
Effective Project Management with SMART Goals
Published:You need to be SMART when writing the goals for your project charter: specific, measurable, achievable, relevant, and time-bound. Here’s how the SMART framework can help you write better goal statements.
Read more ยป
Exploring the Benefits of Fractional Factorial DOE
Published:Fractional factorial DOE is a cost- and time-effective designed experimentation statistical tool for understanding the impact of your process inputs on your process outputs.ย
Read more ยป
Suppliers, Inputs, Process, Output, Customers (SIPOC): Powerful Visualization
Published:What does your process look like from 25,000 feet up in the air? Your extended process view can be described using SIPOC, or supplier, input, process, output, and customer. Letโs get in our plane and go up.ย
Read more ยป
Three Steps for Aligning Projects to Business Priorities
Published:A company with a Six Sigma deployment identifies a process improvement area within the business. It is easy to figure out what comes nextย โ just define the problem, set the goal, select the project team, pick the team leader, and get out of the way, right? Well, sort of…but before deployment leaders get […]
Read more ยป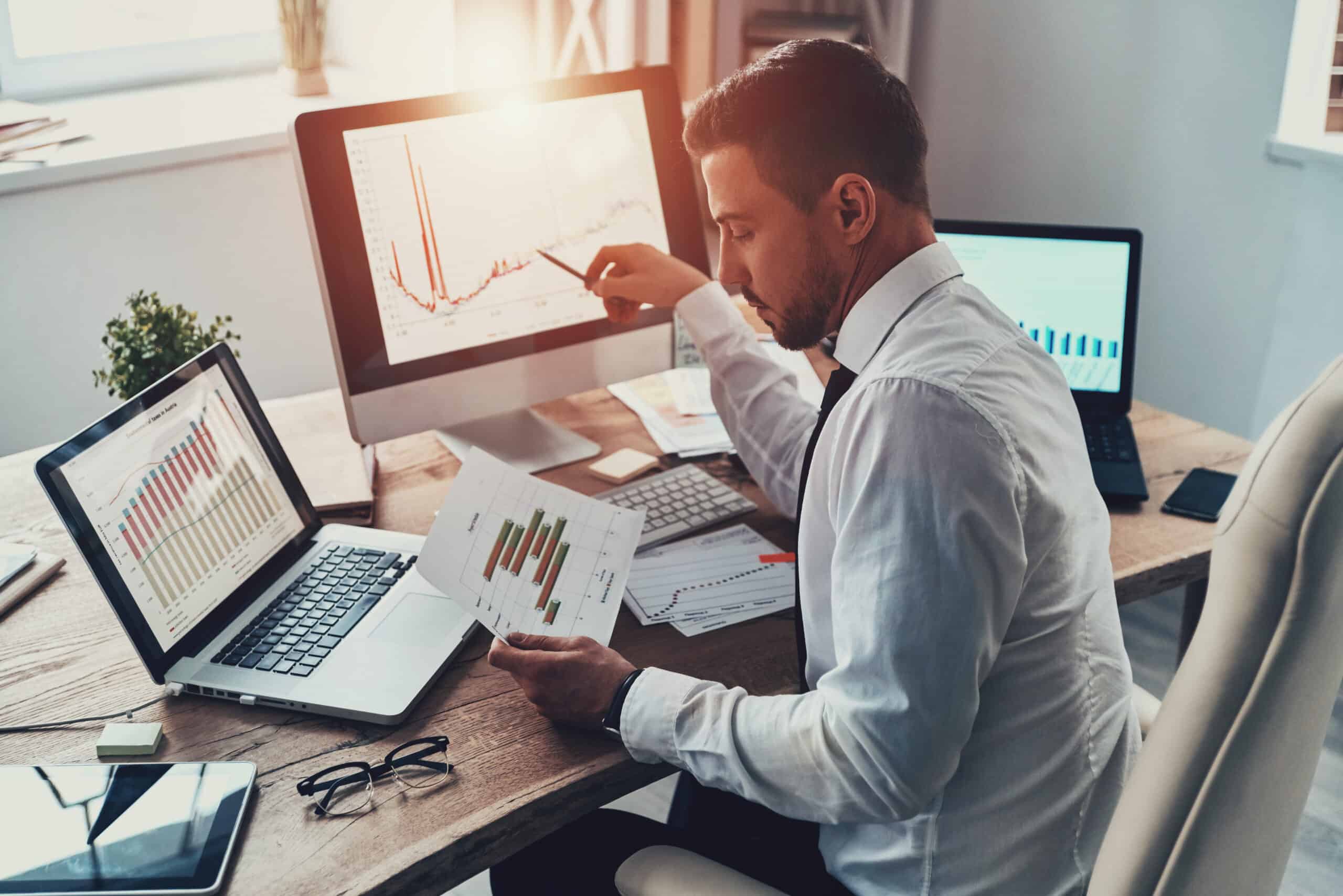
Center Points: Finding the Mathematical Center of Your Data
Published:The use of center points in your designed experiments can be valuable in determining the actual relationship between your input factors and your response variable. Letโs explain this in a little more detail.ย
Read more ยป
Understanding the Purpose and Use of Benchmarking:
Published:Benchmarking is a way of discovering what is the best performance being achievedย โ whether in a particular company, by a competitor, or by an entirely different industry. This information can then be used to identify gaps in an organization’s processes to achieve a competitive advantage. Thus it is important for Six Sigma practitioners […]
Read more ยป
What is the Bartlett Test and How is it Used in Statistical Analysis
Published:The Bartlett Test is named after the English statistician, Maurice Stevenson Bartlett. The test is also known as the Bartlettโs test for homogeneity of variances. It is most used in doing a 1-way Analysis of Variance (ANOVA). ANOVA is used to determine whether there is any statistical difference between the means of three […]
Read more ยป
Understanding Customer Needs: The Importance of Quality Targets
Published:Understanding what quality targets are and how to center product uniformity around them is a helpful step in overall process improvement, ultimately leading to increased profits and customer satisfaction rates.
Read more ยป
Containment Best Practices: Ensuring Product Integrity
Published:If you have a non-conforming or defective product coming off your production line, what do you do with it? Utilizing a strategy of containment might be the way to go. Letโs learn more about this. Containment of non-conforming products refers to the actions you take to prevent the distribution or use of products […]
Read more ยป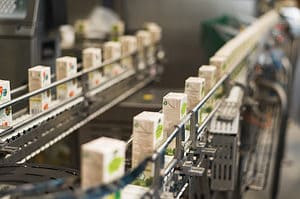
Tolerance Range: Expecting Variation in Your Data
Published:Understanding and determining the upper and lower statistical limits are the key to determining tolerance range (TR). Find out more about this LSS concept.
Read more ยป
Corrective Action: Eliminating Nonconformity Permanently
Published:Corrective action is the process, known as a corrective action plan (CAP), of taking the appropriate steps to identify the root cause of a problem and implementing a solution that corrects the root cause to prevent its recurrence. The aim is to improve the processes in place within an organization so that problems […]
Read more ยป
Radar Charts: The Visual Tool for Multi-Dimensional Data Comparison
Published:A radar chart, also known as a spider chart, is a great tool to graphically compare multiple outcomes for specific characteristics and criteria.ย
Read more ยป
Cause-and-Effect Diagrams: A Visual Tool for Root Cause Analysis
Published:Getting to grips with the many different causes of defects and quality issues is key to ensuring business success and avoiding customer dissatisfaction. The cause and effect diagram is a clear, visual representation of all possible causes and keeps the team focused upon quality improvement.
Read more ยป
Monitoring Process Performance with X-Bar and R Charts
Published:Is the variation in your process data to be expected, or has something special occurred? A control chart will give you the answer. The X-bar and R chart will give you the details.
Read more ยป
The Importance of Fisher’s (1-way ANOVA) in Statistical Analysis
Published:Fisher’s 1-way ANOVA is a classic analysis of variance utilized in statistics to determine if there are statistical differences between the means of two or more unrelated groups.
Read more ยป
Subject Matter Expert vs. Consultant: Whatโs the Difference?
Published:What is a Subject Matter Expert? Subject matter experts (SMEs) are people who have a significant amount of knowledge or experience regarding a specific subject. They can specialize in any kind of academic discipline, profession, or practice. Even though their area of expertise is relatively narrow compared to general consultants, there is still […]
Read more ยป
Homogeneity of Variance and Statistical Inference: What You Need to Know
Published:There are several statistical tests which assume that independent data sets have equal, similar or equivalent variances. Violating this assumption could render any statistical conclusions invalid.ย
Read more ยป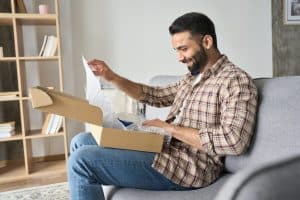
How Six Sigma Improves Customer Satisfaction
Published:With Six Sigma, customer satisfaction comes first. We’ve talked at length in the past about the various nomenclature, techniques, and so forth that drive Six Sigma. As a comprehensive discipline, it is a transformative means of making your organization the best it can be. However, it is a methodology and approach that takes […]
Read more ยป
Hard and Soft Savings: What Counts Can Be Counted
Published:Six Sigma is all about what can be quantified and measured. So it is not surprising that organizations that utilize Six Sigma often prefer to measure success in terms of hard savings or dollars to the bottom line now. They are subsequently less impressed with soft savings, or the possibility of dollars to […]
Read more ยป
Key Tools for Defect Reduction in Lean Six Sigma Processes
Updated:Lean Six Sigma is a system that measures how well a process operates, with โsix sigmaโ being the level of perfection in which processes operate at or below 3.4 defects per million units produced. In order to achieve this, companies must eliminate all but the most critical process steps and then re-engineer those remaining steps to be more efficient and effective.
Read more ยป
Strengthening Business Health: Lot Tolerance Percent Defective as a Vital Tool
Published:It is important in business to have a sampling system in place to determine when to dump a pack of units dumped due to an unacceptable amount being defective. LTPD is part of this sampling system.
Read more ยป
Visual Controls: Managing Processes With a Glance
Published:When things go wrong in the process, how do you know? And how do you know what to do?
Read more ยป
Leveraging Key Process Input Variables for Success
Published:Complex products and processes can often yield significant variation in output, with resultant poor customer satisfaction, especially when process inputs are not well controlled. By understanding and controlling our key process input variables, we have the perfect approach to keep output variation in check.ย ย
Read more ยป
Project ROI: A Key Metric for Project Selection and Resource Allocation
Published:Financial project metrics can be cumbersome to use and jargon-heavy. We demystify and simplify project return on investment, making the concept accessible to all and giving you the confidence to use it in your project management operations.
Read more ยป
See Long and Short-Term Results with a 3-6-12-24 Plan
Published:A major dilemma companies face today is the pressure to deliver short-term improvements and benefits while still contributing to longer-term breakthrough objectives. The 3-6-12-24 planning tool helps practitioners find a way out of this predicament.
Read more ยป
Discrete vs. Continuous Data: What’s the Difference?
Published:When it comes to Six Sigma, data is your lifeblood. The ability to interpret what the data is saying is how you know whether you are on the right path. Further, it shows how you’re achieving your goals and objectives and avoiding roadblocks on your journey toward success. Accurately collected and analyzed data […]
Read more ยป
Tips for Interpreting Discrete Data: Understanding Category Variables
Published:Understanding discrete data will give you yet another tool for understanding your process measure or outcome. This article will explain the tips and traps of using discrete data in process improvement.
Read more ยป
Machine Capability Index: A Tool for Authentication and Verification
Published:If you have a new machine or equipment, you need to be able to determine if it is going to have the potential to make the cut. That is where Cmk comes in.
Read more ยป
Process, Product, and People: The 3P Approach to Quality
Published:Quality management should be a holistic approach. Process, product, and people are the three key elements of a companyโs quality system and all of them need to be focused on for an overall improvement in performance. Why It Matters So, why consider this approach for your quality management? While there are many approaches […]
Read more ยป
How the Toyota Production System Can Improve Your Business Processes
Published:The Toyota Production System (TPS) serves as the foundation for Lean Manufacturing. Letโs explore this powerful method for improving your processes. The Toyota Production System (TPS) is a manufacturing philosophy and a set of management practices developed by the Toyota Motor Corporation. It emphasizes continuous improvement, just-in-time production, and efficient use of resources, […]
Read more ยป
The 10 Questions of DMAIC: Process Improvement Done Right
Published:Use these 10 questions when teaching DMAIC. Learn when and where some commonly used Six Sigma tools do – or donโt – apply; align the tools to the underlying question as part of this coaching task.
Read more ยป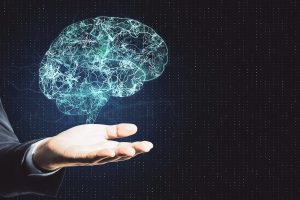
How Lean Six Sigma Training Must be Adapted to Incorporate AI
Published:The Need for Adapting LSS Training The traditional LSS approach relies heavily on human expertise for data collection, analysis, and decision-making. While effective, this can be time-consuming, prone to errors, and limited in scope. AI, on the other hand, can process vast amounts of data in real-time, identify patterns that may not be […]
Read more ยป
Deming’s 14 Points: A Blueprint for Achieving Quality and Productivity in Business
Published:Demingโs 14 Points provide a roadmap to transform American Business and increase productivity and competitive position. Without W. Edwards Deming, modern quality improvement might not exist. If you have never heard of Dr. Deming or his 14 Points for Management, welcome aboard. If you have, get ready to reacquaint yourself. What Are Deming’s […]
Read more ยป
Linearity vs. Repeatability: What’s the Difference?
Published:What Is Linearity? Before understanding linearity, we must understand another measurement error known as bias. Bias is a consistent mistake that occurs in measurement. For example, every measure taken with your scale comes out heavier than the actual weight. Linearity measures the consistency of a bias over the entire range of possible measurements. […]
Read more ยป
6 Alternate Frameworks To Quality Management That Work
Published:Quality management is an essential aspect of any business that strives to deliver products and services that meet or exceed customer expectations. The core principles of Quality Management were developed as part of the International Organization for Standardization (ISO) seven principles of quality management. Traditional quality management systems like Total Quality Management (TQM) […]
Read more ยป
The Benefits and Drawbacks of Box-Cox Transformation: What You Need to Know
Published:In many industries, it is possible to find distributed data that does not follow the typical bell-shaped curve. In some instances, you will find that there is a much longer tail on the right side. This type of distribution follows the 80/20 rule, which states that roughly 80% of consequences come from 20% […]
Read more ยป
Design for Six Sigma: Using the IDOV Methodology
Published:Design for Six Sigma (DFSS) can be accomplished using any one of many methodologies. IDOV is one popular methodology for designing products and services to meet Six Sigma standards. IDOV is a four-phase process that consists of Identify, Design, Optimize, and Verify. These four phases parallel the four phases of the traditional Six […]
Read more ยป
Attribute Data: Quantifying the Qualitative
Published:You will often see attribute data and discrete data being used interchangeably. At some level, they are similar. But, if we dive a little deeper, youโll see that thereโs a bit more distinction than meets the eye.
Read more ยป
Process Time: Boosting Efficiency
Published:Process time is the time it takes for one or more inputs to be transformed into a finished product or service by a business process.
Read more ยป
Exploring the Path to Achieving World-Class Quality
Published:Achieving world-class quality isn’t something every organization can do, because so much of what makes it possible cannot be taught. It boils down to mindset and certain character traits that some people have, some people don’t. Do you?
Read more ยป
The Non-Conformance Process: Five Vital Steps to Rectify Issues
Published:The definition of non-conformity is provided and then described with examples of what non-conformities involve, giving examples of the process approach to facilitate the management of the non-conformities.
Read more ยป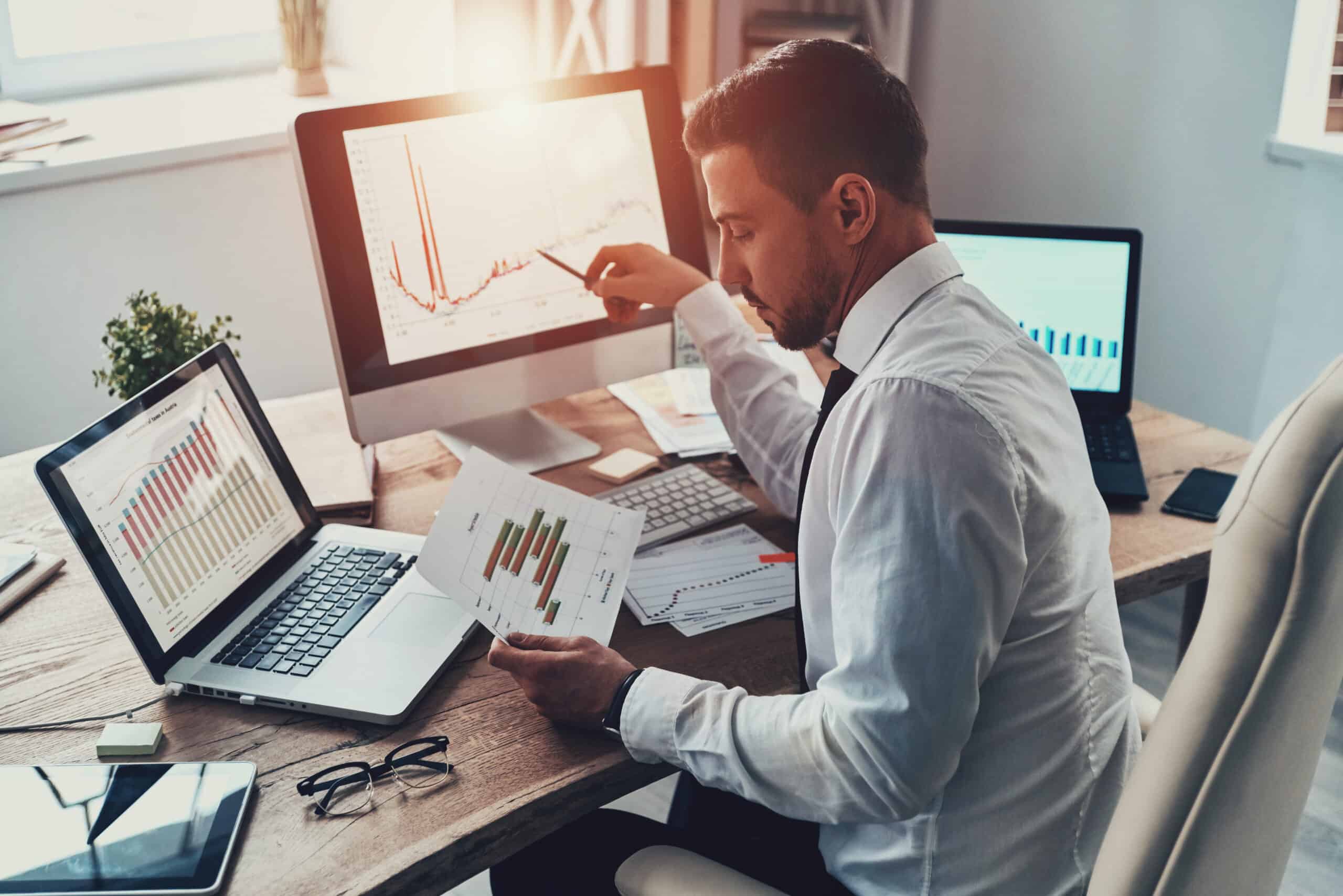
Making Sense of the Two-Proportions Test
Updated:Consider a production process that produced 10,000 widgets in January and experienced a total of 100 rejected widgets after a quality control inspection (i.e., failure rate = 0.01, success rate = 0.99). A Six Sigma project was deployed to fix this problem and by March the improvement plan was in place. In April, the process […]
Read more ยป
Predicting Success: A Comprehensive Guide to Trend Analysis Tools
Published:Do you possess a crystal ball to see what the future brings for your organization? Probably not, but you do have a statistical version of a crystal ball by using trend analysis.ย
Read more ยป
Importance of Test Plans/Test Protocol: Go Into Testing Prepared
Published:Test plans, also called test protocols, are formal documents that typically outline requirements, activities, resources, documentation, and schedules to be completed. Some form of test plan should be developed before any test. The key reasons for developing test plans are: The Importance of a Plan Before embarking on any testing, experimentation, and so […]
Read more ยป
Quality Operating System (QOS): Delivering Constant Quality
Published:With increasing competitive and market pressures, understanding customer requirements and delivering high-quality products, processes and services has never been more important. By implementing a Quality Operating System, you can ensure that quality improvement is every employeeโs responsibility and focus.
Read more ยป
Predetermined Motion Time System (PMTS): Maximizing Efficiency and Productivity
Published:A predetermined motion time system can be useful for everything from estimating labor costs to balancing production lines. It is a concept worth exploring for its myriad applications.
Read more ยป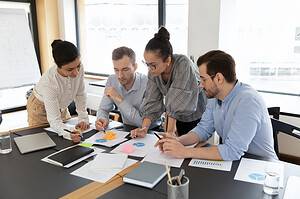
Practical Guide to Creating Better-Looking Process Maps
Updated:Process mapping is one of the basic quality or process improvement tools used in Lean Six Sigma. It has acquired more importance in recent times, given the complexities of processes and the need to capture and visualize knowledge that resides with the people who perform the task. Often process mapping is looked at as an […]
Read more ยป
Big Data vs. Small Data: Which Is Right for Your Business?
Published:Big Data vs. Small Data Big data vs. small data, which should you be paying attention to? Data is generated throughout an organization. You’re gathering it when selling products, producing things, and even just interacting with customers. However, when we start talking about data, the notion of big data and small data enter […]
Read more ยป