isixsigma.com

The 5 Phases of Design Thinking: A Step-by-Step Guide
Published:What are the 5 phases of design thinking? Design thinking is a human-centric approach to product development. However, it operates in five distinct phases when broken down into its core elements. As this is an iterative approach, some phases bear repeating, provided the product hasn’t met its design specifications. So, with that in […]
Read more ยป
Design Thinking Tools to Enhance Creativity and Problem-Solving
Published:What design thinking tools are companies using to make the most of their work? Design thinking isn’t a new concept, but it has caught in a big way over the last decade. As such, a whole cottage industry of software and other tools has sprung up to accommodate the needs of teams. Good […]
Read more ยป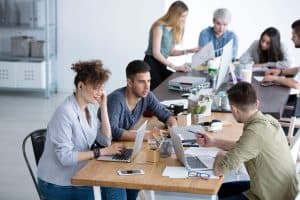
The 10 Companies That Do Design Thinking The Best
Published:Which companies do design thinking the best? Design thinking is a relatively new approach to the likes of product delivery. While products are often drummed up with the customer in mind, few approaches consider the customer’s needs before even analyzing the problem and developing a solution. That said, some companies are embracing design […]
Read more ยป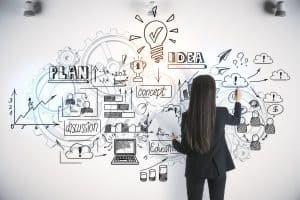
The Industries That Benefit Most from Design Thinking
Published:What industries benefit the most from design thinking? Design thinking is a growing approach to the entire conceptualization and execution of new products to market. However, despite its increasing popularity, it is better suited for certain industries. Now, that isn’t to say your organization should forego implementing design thinking. It all depends on […]
Read more ยป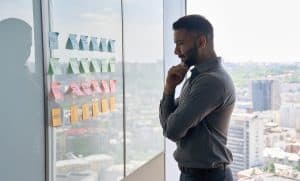
Key Digital Tools Driving Business Agility
Published:What tools are needed to create business agility? An agile business can adapt and roll with the punches. I don’t mean a momentary setback but events that a business can easily adapt and overcome. In software development, this methodology is known as Agile and is one of the driving forces behind modern development […]
Read more ยป
The Most Popular Tools For Data-Driven Decisions In Business
Published:What tools are businesses using for data-driven decisions? There is plenty to be said about the proliferation of data in the workplace. However, one thing is clear: it is here for the long haul. As such, learning how to manipulate this data for your organization’s well-being is simply part and parcel of the […]
Read more ยป
How to Build a Data-Driven Culture in Your Organization
Published:Is it easy to build a data-driven culture for your business? Data is a driving force in any modern organization. Even mom-and-pop stores are leaning on what they can glean from the digital revolution. As such, it is more important than ever to take the steps to create a data-driven culture to take […]
Read more ยป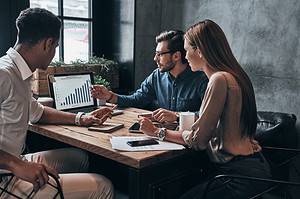
Big Data vs. Small Data: Which Is Right for Your Business?
Published:Big data vs. small data, which one are you choosing for your business? Data is a big market right now, something that it has held the distinction of for the last decade or more. Data drives business decisions, calls forecasts for future trends, and so much more. As such, it helps to have […]
Read more ยป
Step-by-Step Guide to Conducting an FMEA
Published:What’s the best process for conducting an FMEA? If you want to start implementing lasting changes into your production line, FMEA is one of the top ways to get things rolling. However, there is a certain procedure you’ll want to follow to make the most of your efforts. If you’re new to the […]
Read more ยป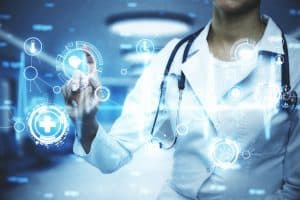
The 9 Industries That Will Benefit The Most From AI
Updated:Artificial intelligence (AI) has emerged as one of the most transformative technologies of the 21st century, reshaping industries, revolutionizing processes, and unlocking unprecedented opportunities. As AI continues to advance, its impact on various sectors becomes increasingly evident. Some industries stand to benefit more significantly than others due to their reliance on data, automation […]
Read more ยป
Preparing Your Workforce for the AI Revolution
Published:The advent of artificial intelligence (AI) is reshaping industries, transforming workflows, and altering the future of work. As AI continues to grow in sophistication and application, organizations must act proactively to prepare their workforce for the opportunities and challenges this revolution presents. Reskilling and upskilling employees isnโt just an operational necessity, itโs a […]
Read more ยป
Reviving a Restaurant Chain: How Kano Analysis Transformed Sales
Published:Background The COVID-19 pandemic brought unprecedented challenges to businesses, and the food and beverage industry was among the hardest hit. For TasteTown Bistro, a medium-sized restaurant chain known for its casual dining experience, the pandemic decimated customer traffic. As restrictions eased, TasteTown hoped for a strong recovery, but they faced a new challenge: traffic and […]
Read more ยป
FMEA in Product Development: Reducing Risk Early On
Published:How can you use FMEA in product development? I’ve talked at length about using FMEA as a means of rectifying problems in production. However, you can apply the methodology to the design process of any product or service you’ve got in the works. It isn’t similar to DMAIC, as DMAIC is generally used […]
Read more ยป
Case Studies: Companies Successfully Using AI to Innovate
Published:Artificial Intelligence (AI) has emerged as a transformative force, enabling companies to innovate, streamline operations, and improve customer experiences. Across industries, forward-thinking businesses are leveraging AI to gain competitive advantages, address complex challenges, and create value. This article explores case studies of companies that have successfully integrated AI into their core operations, highlighting […]
Read more ยป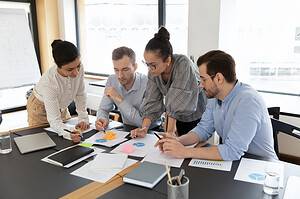
Common Pitfalls in FMEA and How to Overcome Them
Published:What are the most common mistakes you can make with FMEA? As a framework, FMEA is aimed at creating lasting solutions to potential problems before they even arise. However, that doesn’t mean it’s completely foolproof. As we’ve seen with many of the tools of the trade, there is certainly a right and a […]
Read more ยป
Real-World Examples of FMEA in Action
Published:How does FMEA work in the real world? We often discuss concepts, methodologies, and frameworks in a vacuum. However, understanding the realistic applications of a useful and quality-driven framework like FMEA pays off in the end. So, with that in mind, let’s look at a few examples of how FMEA is implemented in […]
Read more ยป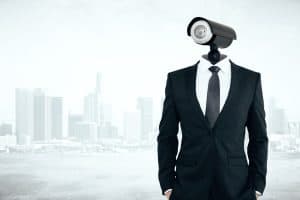
Ethical Challenges in Adopting AI in the Workplace
Published:Artificial Intelligence (AI) is revolutionizing workplaces across the globe. By automating routine tasks, enhancing decision-making, and driving innovation, AI has become an indispensable tool for many businesses. However, as organizations embrace this transformative technology, they encounter significant ethical challenges that require careful consideration and proactive measures. This article explores three key ethical dilemmas […]
Read more ยป
Mistakes When Using Fishbone (Ishikawa) Diagrams
Published:What mistakes are common when using Ishikawa diagrams? As one of the easiest tools to use in the Lean Six Sigma toolbox, there is a very real potential for misusing these diagrams. It isn’t necessarily a lack of knowledge that hinders these tools, but other common pitfalls that make them less effective than […]
Read more ยป
A New Way to Understand Customers: The Conjoint Analysis Journey
Published:Background When FreshSense, a mid-sized packaged goods company, decided to launch a new line of healthy snack bars, excitement buzzed through the office. The team knew the market was ripe for innovation, but the challenge lay in determining the perfect combination of attributes for their new product. Color theme, graphics, package size, graphic orientation, price, […]
Read more ยป
The Best Tools To Make a Fishbone (Ishikawa) Diagram
Published:What are your best resources for making a Fishbone diagram? You might not always have a pen and paper handy, and you might need something more readily presentable for leadership. So, what do you do? You’d likely turn to some of the many popular and powerful software packages available for visualization tools. With […]
Read more ยป
Pareto Chart: How to Use It to Identify Root Causes
Published:Solving a problem in a business context can be extremely daunting at first glance. As a general example, it isn’t quite like looking for where a recipe went wrong. Even the simplest of business processes are complex when taken as a whole. As such, you need the right tools for the job. With […]
Read more ยป
Using the Harada Method in Education To Help Students Set and Achieve Personal Goals
Updated:In an increasingly competitive world, education systems are evolving to focus not only on academic success but also on empowering students to develop skills for lifelong personal and professional growth. The Harada Method, developed by Takashi Harada, offers a structured framework to help individuals achieve personal excellence by fostering self-reliance, goal-setting, and strategic […]
Read more ยป
Comparing the Harada Method with Other Goal-Setting Techniques
Updated:Goal-setting frameworks have been integral in guiding individuals and organizations to clarity, efficiency, and achievement. Among these, the Harada Method, SMART goals, Objectives and Key Results (OKRs), and Lean Thinking each have unique attributes, target different areas of improvement, and fit varying operational contexts. This article explores the distinctive elements of the Harada […]
Read more ยป
The Harada Method for Athletes: How It Works And Drives Success
Updated:In the world of sports, achieving peak performance requires more than just physical training. It demands mental clarity, strategic planning, and a deep commitment to personal growth. The Harada Method, originally developed for business and personal development, has emerged as a powerful tool for athletes striving for excellence. This article explores how the […]
Read more ยป
How Automation Is Revolutionizing Operational Efficiency
Published:Automation seems like all the rage these days. While it is certainly nothing new, especially for those well-versed in manufacturing, it is making a splash elsewhere. Automation is a useful tool, but it is only part of the proverbial equation regarding day-to-day operations. So, why not dive deeper into the subject and see […]
Read more ยป
Hybrid vs. Remote Work Compared
Published:What are the real advantages of hybrid vs. remote work? There has been quite a bit of talk since the start of the pandemic about the merits of remote work. For many organizations, this is the only way they could exist for any period. However, there has been a push to return to […]
Read more ยป
7 Best Examples of Design Thinking
Published:Is your company leveraging design thinking? There are several different approaches to accomplishing a project or delivering a new product. For some organizations, implementing Lean principles and frequent Kaizen events is the way to go. For others, it might require a comprehensive overhaul of their organization to embrace TQM. Design thinking is similar […]
Read more ยป
Improved Executive Decision Making Using the Six Thinking Hats
Published:In the heart of downtown, Apex Bank was known for its strong community ties and financial stability, but not necessarily for its swift decision-making. The executive team meetings were notorious for being long, unproductive, and often marked by clashes between personalities. The CEO, Maria, saw that the inability to make decisions efficiently was affecting the […]
Read more ยป
Evaluating Promotional Approaches at This Pharma Company Saved Over $700,000
Published:Background MegaPharma (fictitious name), a global pharmaceutical company, sought to optimize its promotional strategies to increase access to healthcare providers for one blockbuster drug. Sales representatives used several approaches to gain appointments and engagement with physicians, including free lunches, educational materials, promotional items like branded pens, and remote communication tools such as Zoom. While all […]
Read more ยป
The 6 Best Industries and Projects to use FMEA (Failure Mode and Effects Analysis)
Updated:FMEA is one of the most powerful approaches to safeguarding your projects from failures and defects. It isn’t a cakewalk to implement, but in the right hands, it can make projects run without a hitch. As you’re already used to utilizing data in making decisions, it only makes sense to start using this approach in […]
Read more ยป
Fishbone Diagrams: How to Diagnose Process Problems
Updated:How do you use fishbone diagrams to get to the root of a problem? Fishbone diagrams are one of the 7 QC tools afforded to us by Lean Six Sigma and one of the most effective at determining issues. These are simple tools to use, meaning anyone in your team can leverage their […]
Read more ยป
Real Life Examples Of The Harada Method Unlocking Success
Updated:In a world where personal and professional success is increasingly defined by self-mastery, the Harada Method has emerged as a powerful tool for unlocking potential and driving performance. Developed by Takashi Harada, a former high school track coach in Japan, this method provides a structured approach to achieving oneโs goals. The method is […]
Read more ยป
Combining the Harada Method with Other Techniques (Kaizen, Lean, SMART, etc.)
Published:In todayโs fast-paced and competitive world, achieving sustainable growth and high performance requires more than just setting goals. It requires a systematic approach that not only clarifies objectives but also refines skills, improves processes, and fosters continuous improvement. The Harada Method is an effective personal development system that emphasizes self-reliance, skill-building, and disciplined […]
Read more ยป
How Takashi Harada Created The Harada Method To Elevate Athletes, and Business
Published:In the fields of sports and business, achieving peak performance requires more than just technical skills and hard work. It involves cultivating the right mindset, creating structured goals, and following a path of continuous improvement. Takashi Harada, a former Japanese track and field coach, developed a unique method to help individuals achieve excellence […]
Read more ยป
Real-Life SIPOC Examples in Manufacturing
Updated:What are some real-life SIPOC applications in the field of manufacturing? While Lean Six Sigma tools and methodologies can be applied to any industry, they truly excel when pointed toward something like manufacturing. When you get right down to it, manufacturing is one of the most complex undertakings a business can undergo. What that in […]
Read more ยป
Is SIPOC Still Relevant? 9 Alternatives
Updated:Is SIPOC still worth using? Lean and Six Sigma have many tools for improving or designing new processes. You’ll see SIPOC diagrams often touted, but there are other tools where you might find they are better suited for your needs. Today, we’re looking at a few alternatives that might just fit the bill for your […]
Read more ยป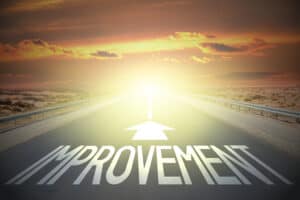
How AI Can Be Used in the DMAIC Process
Updated:The DMAIC methodology (Define, Measure, Analyze, Improve, Control) is a structured, data-driven approach central to Six Sigma practices and quality improvement efforts across various industries. By clearly outlining steps to understand, address, and control quality issues, DMAIC drives process efficiency, product quality, and customer satisfaction. With artificial intelligence (AI) capabilities, DMAIC’s potential is significantly amplified, […]
Read more ยป
Productivity Target: Reaching Your Goals
Published:A productivity target is an established, quantifiable result from a given process. It represents the minimum acceptable value yield from a given quantity of time and resources invested into it.
Read more ยป
What AI Tools Can be Used in Lean Six Sigma Projects?
Updated:Lean Six Sigma is a powerful methodology used to improve processes, reduce waste, and enhance quality. It incorporates data-driven decision-making and focuses on optimizing workflows using structured frameworks like DMAIC (Define, Measure, Analyze, Improve, Control) and DMADV (Define, Measure, Analyze, Design, Verify). With the advent of Artificial Intelligence (AI), the potential of Lean Six Sigma […]
Read more ยป
Design of Experiments: A Primer
Published:Design of experiments (DOE) is a systematic method to determine the relationship between factors affecting a process and the output of that process. In other words, it is used to find cause-and-effect relationships. This information is needed to manage process inputs in order to optimize the output. An understanding of DOE first requires […]
Read more ยป
Finding the Sigma Level of Customer Complaints
Published:At the beginning of a deployment, many companies set a goal of 3.4 defects per million opportunities (DPMO) using Six Sigma quality concepts in production and later extend this concept to other operational areas. Fewer companies, however, have extended Six Sigma from a manufacturing application to manage customer satisfaction or customer complaints. However, […]
Read more ยป
Quality Program Report (QPR): Guaranteeing You Hit the Mark
Published:It is important to regularly check if your processes are operating as optimally as they could be. If not, actions should be taken for improvement. For this to be appropriately determined, you can create a QPR.
Read more ยป
The Cause-and-Effect (a.k.a. Fishbone) Diagram
Updated:When utilizing a team approach to problem-solving, there are often many opinions as to the problem’s root cause. One way to capture these different ideas and stimulate the team’s brainstorming on root causes is the cause and effect diagram, commonly called a fishbone. The fishbone will help to visually display the many potential causes for […]
Read more ยป
The Hidden Factory: Understanding the Unseen
Published:You claim your process yield is 98%. Are you sure? Have you considered your hidden factory? Letโs find out why you should.
Read more ยป
Causal Loop Diagrams: Little Known Analytical Tool
Published:Sometimes it is easy to get into a rut when it comes to doing analysis. It can be hard to stray from those same time-tested analytical tools used in the Six Sigma methodology. The process map, failure modes and effects analysis, cause-and-effect matrix, and fishbone diagram are like well-used tools that feel comfortable […]
Read more ยป
Random Sampling: Key to Reducing Bias and Increasing Accuracy
Published:Random sampling is a statistical method of selecting a sample of data from a larger set in such a way that each data point has an equal chance of being selected so that the sample represents the population from which it was drawn. What Is Random Sampling? Random sampling is a method of […]
Read more ยป
Cost of Quality: Not Only Failure Costs
Published:When calculating the business case for a Six Sigma project, the cost of poor quality (COPQ), which is the cost caused by producing defects, is a commonly used concept. Within the total amount of quality cost, however, COPQ represents only a certain proportion. Costs do not result from only producing and fixing failures; […]
Read more ยป
While Calculating Pp and Ppk, How Do I Determine the Value of Short-Term and Long-Term Standard Deviation?
Updated:One must understand that the short-term standard deviation reports on a process’s โinstantaneous reproducibilityโ whereas the long-term standard deviation reflects the โsustainable reproducibility.โย To this end, the short-term standard deviation comprises the โwithin groupโ sums of squares (SSW).ย The long-term standard deviation incorporates the โtotalโ sums-of-squares (SST).ย Of course, the difference between the two constitutes […]
Read more ยป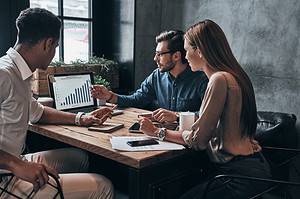
Span: Catching Variation in Your Data
Published:Span is a descriptor of the spread or variation of your data. It is a simple calculation that eliminates the impact of any outliers or unusually high or low values in your data set.
Read more ยป
A Better Inventory Management Strategy Saved This Company $900,000 (and Improved Safety)
Published:Background At Apex Tools (fictional name), a mid-sized supplier of specialized mechanical components, inventory management and safety concerns had long been interwoven issues. As demand surged, materials flowed continuously into the warehouse, often in excessive amounts, cluttering aisles and creating unsafe conditions. This surplus inventory led to various issues: obsolescence, shrinkage, and frequent safety hazards […]
Read more ยป