isixsigma.com

Risk Priority Number (RPN): Learn How to Prioritize Risks and Focus On What Matters
Published:With ever more complex products, processes and services the potential for high impact failure modes increases. Risk management is crucial for business success and the calculation of Risk Priority Number with mitigation and correction actions is an industry standard methodology that helps achieve your quality goals.
Read more ยป
Standardized Residuals: Insights into Calculations, Interpretations, and Applications
Published:Residual, standardized residual, studentized residual — what do they mean, and how do I use them?ย
Read more ยป
Tukey’s (1-way ANOVA): See the Difference in Your Data Sets
Published:ANOVA will tell you whether there is a statistically significant difference in the population means of three or more groups of data. But which means are different? Tukeyโs will tell you that. Analysis of Variance (ANOVA) is used to determine whether the population means of several sample data sets are statistically different or not. If […]
Read more ยป
Categorical vs. Continuous Data: Whatโs the Difference?
Published:Data analysis is a fundamental process in any project. However, data can be lumped into different types, with categorical and continuous data seeming almost opposed at first glance. That said, mastering these data types and understanding when and where to use them can lead to far more precision during data analysis as a whole. What […]
Read more ยป
The 7 Best Tools to Support Change Management Efforts
Published:What are the best tools for supporting change management? Change management is a principle that helps guide organizations and projects through periods of change. On the surface level, it is an entirely separate discipline from project management. That said, you’ll want the right tools to make the most of your efforts. The best […]
Read more ยป
How to Lead Organizational Change in a Fast-Paced Digital Environment
Published:How do you enact lasting organizational change in a digital environment? Much of what is written about organizational change existed before the advent of the far-reaching digital transformation we’ve experienced in the last five years. However, you can still impact this concept by keeping pace with other organizations. Understanding the changing environment is […]
Read more ยป
Lean Six Sigma in a Post-Pandemic World: Adapting to New Operational Realities
Published:Introduction The COVID-19 pandemic disrupted global operations, forcing organizations to reevaluate traditional business practices and adapt to an unpredictable environment. Lean Six Sigma (LSS), a methodology focused on reducing waste and improving quality, has proven to be a critical tool in navigating these challenges. By emphasizing data-driven decision-making, continuous improvement, and flexibility, Lean […]
Read more ยป
Cpk vs. Sigma Level: Whatโs the Difference?
Updated:So what is the real difference when looking at Cpk and Sigma Level? If you’re new to Six Sigma, there is no shortage of acronyms and calculations to keep in mind as you work on your knowledge base. Both Cpk and Sigma Level are valuable tools when looking at your processes and production. So, let’s […]
Read more ยป
A Comprehensive Guide to Input-Process-Output Models
Published:Creating and mapping business process models can sound like a daunting task with little tangible value. With input-process-output models, we debunk these myths and introduce a versatile, straightforward methodology that can be used to transform your business.
Read more ยป
Critical To Quality: The Key to Meeting Customer Expectations
Published:Critical of quality is the path to customer satisfaction. Learn how Critical to Quality impacts the ability to satisfy your customer, the benefits of addressing CTQ related issues, and see an example.
Read more ยป
Getting to the Bottom of Your Problem: How to Use the 5 Whys
Published:Asking “Why?” may be a favorite technique of your 3-year-old child in driving you crazy, but it could teach you a valuable Six Sigma quality lesson. The 5 Whys is a technique used in the Analyze phase of the Six Sigma DMAIC (Define, Measure, Analyze, Improve, Control) methodology. It is a great Six Sigma tool that […]
Read more ยป
Variable vs. Attribute Data: Whatโs the Difference?
Updated:Throughout any project, you’re going to gather up quite a bit of data. Now, this can be broken down into two categories: variable and attribute data. Understanding the difference and learning how it is applicable during the analysis stage can be crucial for future decision-making. So, with that in mind, let’s take a deeper dive […]
Read more ยป
Understanding the 6Ms: A Powerful Tool for Problem-Solving
Published:Are you confused yet? Is it the 6 Ms? Is it 5 Ms and a P? How about 4 Ms, 5 Ms or 8 Ms? Letโs explore some of these and figure it out.
Read more ยป
F-value (ANOVA): Get the Most Out of Your Data Analysis
Published:Whether you are talking about the F-value, F-test, F-statistic or F distribution they all revolve around the same concept of using variances to make statistical decisions about your data.
Read more ยป
Streamlining Six Sigma Projects with the 7 QC Tools
Published:The seven basic tools in my home tool chest are a hammer, screwdriver, wrench, saw, drill, pliers, and duct tape. What basic QC tools do you have in your continuous improvement tool chest? Letโs check it out.
Read more ยป
Get Your Team Up to Speed with the SIPOC Diagram
Published:There are a few different ways you can improve a process in your business. Before you get to work with implementing these changes, it does help to visualize the entire thing. A SIPOC diagram is a highly useful tool for mapping out the steps of a process. Processes and projects are complex, but a SIPOC […]
Read more ยป
Measuring Success: How to Track the Impact of Change Management Initiatives
Published:How do you track change management initiatives? The modern business relies on data to guide many of its actions. However, when enacting something as wide or broad as change management this can be difficult. That said, you aren’t without recourse when looking at your change management initiatives. There are some ways to track […]
Read more ยป
FMEA (Failure Mode and Effects Analysis): A Quick Guide to Minimizing Defects and Faults in Your Projects
Updated:FMEA — failure mode and effects analysis — is a tool for identifying potential problems and their impact.
Read more ยป
Top Automation Tools Businesses Are Using to Streamline Processes
Updated:What are the top automation tools in use today? Automation is one of the hot buzzwords of modern business, but how it is implemented differs from industry to industry. There isn’t necessarily a universal approach to how an organization should use it to gain the best results. That said, some stellar tools can […]
Read more ยป
The 7 Industries That Benefit The Most From Automation
Published:Which industries benefit the most from automation? Automation is a hot topic in business, with many organizations opting to automate something. This is partly understandable, as you can simplify more grueling or tedious tasks by having them handled from the get-go. However, not every industry is suited to automation. Being aware of where […]
Read more ยป
The 10 Different Change Management Models In Use
Published:What change management models are in constant use today? Change management is one of the vital components needed for enacting lasting, viable change. However, it always helps to have a guideline or framework within which to operate, hence the need for models. That said, there is more than one way to approach change […]
Read more ยป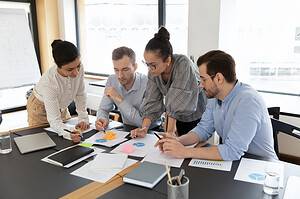
Case Study: Optimizing Fill Weight to Enhance Profitability for a National Coffee Producer
Published:Background A large national producer and distributor of canned instant ground coffee faced a significant challenge with product weight variation on their primary production line. The companyโs specifications for fill weight included both an Upper Specification Limit (USL) and a Lower Specification Limit (LSL) to ensure compliance with regulatory standards and customer satisfaction. However, 13% […]
Read more ยป
Integrating Lean Six Sigma with Agile: The Future of Process Improvement
Published:Introduction Lean Six Sigma and Agile are two powerful methodologies widely used to improve processes and deliver value. While they originate from different domains, Lean Six Sigma focuses on reducing waste and improving quality, and Agile emphasizes flexibility and iterative development. Their integration offers organizations a dynamic framework for process improvement. Together, they […]
Read more ยป
Continuous Improvement Meets Sustainability: Lean Six Sigmaโs Role in Green Business Practices
Published:In todayโs business environment, sustainability has become a critical focus for organizations aiming to reduce their environmental footprint while maintaining profitability. One of the most effective frameworks for achieving this balance is Lean Six Sigma (LSS), a methodology rooted in continuous improvement, waste reduction, and efficiency. By integrating Lean Six Sigma principles with […]
Read more ยป
Why Change Management Is Critical for Digital Transformation
Published:Is change management important for digital transformation? We’re present for an interesting time in the business landscape. Many traditional organizations are modernizing, joining with the times as it were. In part this is thanks to the advent of more advanced technological developments. Some companies embrace them as a matter of their foundation, but […]
Read more ยป
9 Remote-First Companies That Made It Work
Published:What are the remote-first companies that made it work? There are plenty of success stories throughout the history of business. However, little has been said about the remote companies that are making a mark on the landscape of business right now. If you’re looking to lead your remote team, some organizations can serve […]
Read more ยป
Leveraging Process Capability Analysis to Outperform Competitors
Published:Background In a highly competitive market, a plastic parts company leveraged Lean Six Sigma methodologies, particularly Process Capability Analysis (Cpk and Ppk), to analyze supplier performance and strategically improve their product offering. By selecting the most capable supplier and tightening component specifications, the company not only outperformed competitors but also created value for its customers, […]
Read more ยป
The Best Tools For Remote Teams
Published:What are the best tools for remote teams? You can often skip several of the latest and greatest software tools for in-person positions. However, remote teams have specific technological needs, partly thanks to the distance between employees and the workplace. As such, tools come in handy for managing time, communicating, keeping track of […]
Read more ยป
Driving Lean Six Sigma in Hybrid Workplaces: Overcoming Communication Barriers
Published:The workplace landscape has undergone a dramatic transformation with the widespread adoption of hybrid work models. This shift, accelerated by the global pandemic, combines remote and in-office work, offering employees flexibility and autonomy while enabling organizations to reduce operational costs. However, this model also presents unique challenges, particularly in communication, collaboration, and process […]
Read more ยป
Future of Remote Work: Trends and Predictions for the Hybrid Workforce
Published:What does the future of remote work hold? The shift to remote work has been rather abrupt. While it seems somewhat gradual in retrospect, the numbers behind it don’t lie. That said, the future seems promising for remote work. While we don’t have access to a crystal ball here, we certainly have no […]
Read more ยป
Maintaining Company Culture in a Remote Work Environment
Published:How do you maintain company culture when your entire team is remote? Going hybrid or fully remote doesn’t mean you have to forego maintaining a company culture. Some organizations realize and maintain a vibrant company culture despite the challenges of remote work. It is a matter of simply balancing and planning how to […]
Read more ยป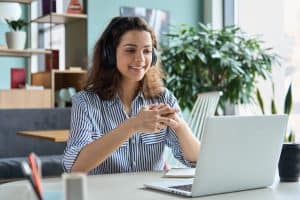
Common Challenges of Remote Work and How to Overcome Them
Published:What are the common challenges of remote work? Remote work itself has become a regular part of many offices. However, there are some drawbacks to this hands-off workflow. When remote work started becoming more prevalent at the start of the pandemic, these drawbacks weren’t given much thought. That said, you give anything significant […]
Read more ยป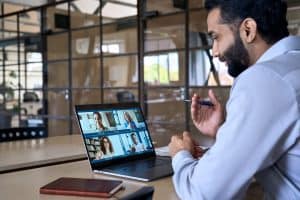
Tools and Platforms to Boost Productivity in Remote Teams
Published:What tools can boost productivity in remote teams? Finding the right workflow for remote teams is paramount to their continued success. As such, planning to use the right tools and developing a solid workflow is a great way to ensure your team stays on track. Finding the right blend can be challenging, but […]
Read more ยป
How to Build a High-Performing Remote Team
Published:How does an organization build a high-performing remote team? Remote work has become all the rage over the last few years, with organizations without a heavy need for on-site personnel switching to the model. The benefits have been discussed ad nauseam, like the lower rent for many organizations and reduced overhead. However, little […]
Read more ยป
How to Implement Design Thinking in Cross-Functional Teams
Published:How does design thinking apply to cross-functional teams? We’ve spent a fair bit of time here discussing the benefits and reasons why you want to use design thinking in product design. However, little has been said about how it applies to cross-functional teams. Thankfully, this approach benefits from multiple disciplines and specialties collaborating. […]
Read more ยป
Determining the Best Collections Script Using Mood’s Median Test Increased Revenue by $800,000
Published:Background In a bustling corporate office, Sarah, a finance manager at Apex Financial Solutions, was tasked with optimizing the collections process. With a portfolio of clients from various industries, the company’s success relied heavily on its ability to recover overdue payments. Sarah suspected that the effectiveness of the phone scripts used by collections associates varied, […]
Read more ยป
The 9 Industries That WIll Lose The Most From AI
Published:Artificial intelligence (AI) has proven to be a transformative force, reshaping industries, enhancing productivity, and opening doors to innovation. While it has brought benefits to many sectors, the rapid evolution of AI also threatens some industries, particularly those reliant on repetitive tasks, manual labor, or human-driven decision-making. A recent article was published on […]
Read more ยป
Design Thinking in Practice: How Leading Brands Innovate
Published:What does design thinking in practice look like? There has been much talk about its power and efficacy. However, when you peruse the many online resources available, the picture is incomplete. We know it’s a human-centered take on product design, but what does that look like in motion? Design thinking in practice isn’t quite what […]
Read more ยป
The 5 Phases of Design Thinking: A Step-by-Step Guide
Published:What are the 5 phases of design thinking? Design thinking is a human-centric approach to product development. However, it operates in five distinct phases when broken down into its core elements. As this is an iterative approach, some phases bear repeating, provided the product hasn’t met its design specifications. So, with that in […]
Read more ยป
Design Thinking Tools to Enhance Creativity and Problem-Solving
Published:What design thinking tools are companies using to make the most of their work? Design thinking isn’t a new concept, but it has caught in a big way over the last decade. As such, a whole cottage industry of software and other tools has sprung up to accommodate the needs of teams. Good […]
Read more ยป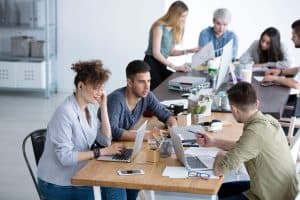
The 10 Companies That Do Design Thinking The Best
Published:Which companies do design thinking the best? Design thinking is a relatively new approach to the likes of product delivery. While products are often drummed up with the customer in mind, few approaches consider the customer’s needs before even analyzing the problem and developing a solution. That said, some companies are embracing design […]
Read more ยป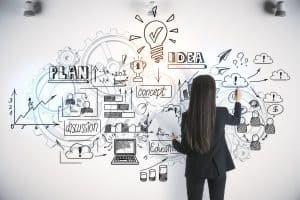
The Industries That Benefit Most from Design Thinking
Published:What industries benefit the most from design thinking? Design thinking is a growing approach to the entire conceptualization and execution of new products to market. However, despite its increasing popularity, it is better suited for certain industries. Now, that isn’t to say your organization should forego implementing design thinking. It all depends on […]
Read more ยป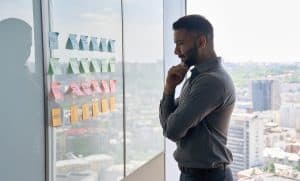
Key Digital Tools Driving Business Agility
Published:What tools are needed to create business agility? An agile business can adapt and roll with the punches. I don’t mean a momentary setback but events that a business can easily adapt and overcome. In software development, this methodology is known as Agile and is one of the driving forces behind modern development […]
Read more ยป
The Most Popular Tools For Data-Driven Decisions In Business
Published:What tools are businesses using for data-driven decisions? There is plenty to be said about the proliferation of data in the workplace. However, one thing is clear: it is here for the long haul. As such, learning how to manipulate this data for your organization’s well-being is simply part and parcel of the […]
Read more ยป
How to Build a Data-Driven Culture in Your Organization
Published:Is it easy to build a data-driven culture for your business? Data is a driving force in any modern organization. Even mom-and-pop stores are leaning on what they can glean from the digital revolution. As such, it is more important than ever to take the steps to create a data-driven culture to take […]
Read more ยป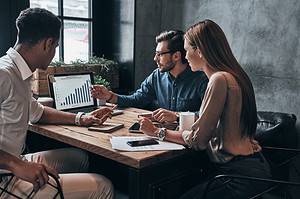
Big Data vs. Small Data: Which Is Right for Your Business?
Published:Big data vs. small data, which one are you choosing for your business? Data is a big market right now, something that it has held the distinction of for the last decade or more. Data drives business decisions, calls forecasts for future trends, and so much more. As such, it helps to have […]
Read more ยป
Step-by-Step Guide to Conducting an FMEA
Published:What’s the best process for conducting an FMEA? If you want to start implementing lasting changes into your production line, FMEA is one of the top ways to get things rolling. However, there is a certain procedure you’ll want to follow to make the most of your efforts. If you’re new to the […]
Read more ยป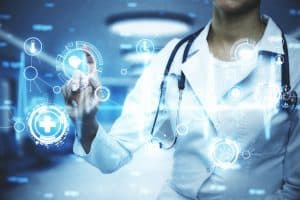
The 9 Industries That Will Benefit The Most From AI
Updated:Artificial intelligence (AI) has emerged as one of the most transformative technologies of the 21st century, reshaping industries, revolutionizing processes, and unlocking unprecedented opportunities. As AI continues to advance, its impact on various sectors becomes increasingly evident. Some industries stand to benefit more significantly than others due to their reliance on data, automation […]
Read more ยป
Preparing Your Workforce for the AI Revolution
Published:The advent of artificial intelligence (AI) is reshaping industries, transforming workflows, and altering the future of work. As AI continues to grow in sophistication and application, organizations must act proactively to prepare their workforce for the opportunities and challenges this revolution presents. Reskilling and upskilling employees isnโt just an operational necessity, itโs a […]
Read more ยป
Reviving a Restaurant Chain: How Kano Analysis Transformed Sales
Published:Background The COVID-19 pandemic brought unprecedented challenges to businesses, and the food and beverage industry was among the hardest hit. For TasteTown Bistro, a medium-sized restaurant chain known for its casual dining experience, the pandemic decimated customer traffic. As restrictions eased, TasteTown hoped for a strong recovery, but they faced a new challenge: traffic and […]
Read more ยป