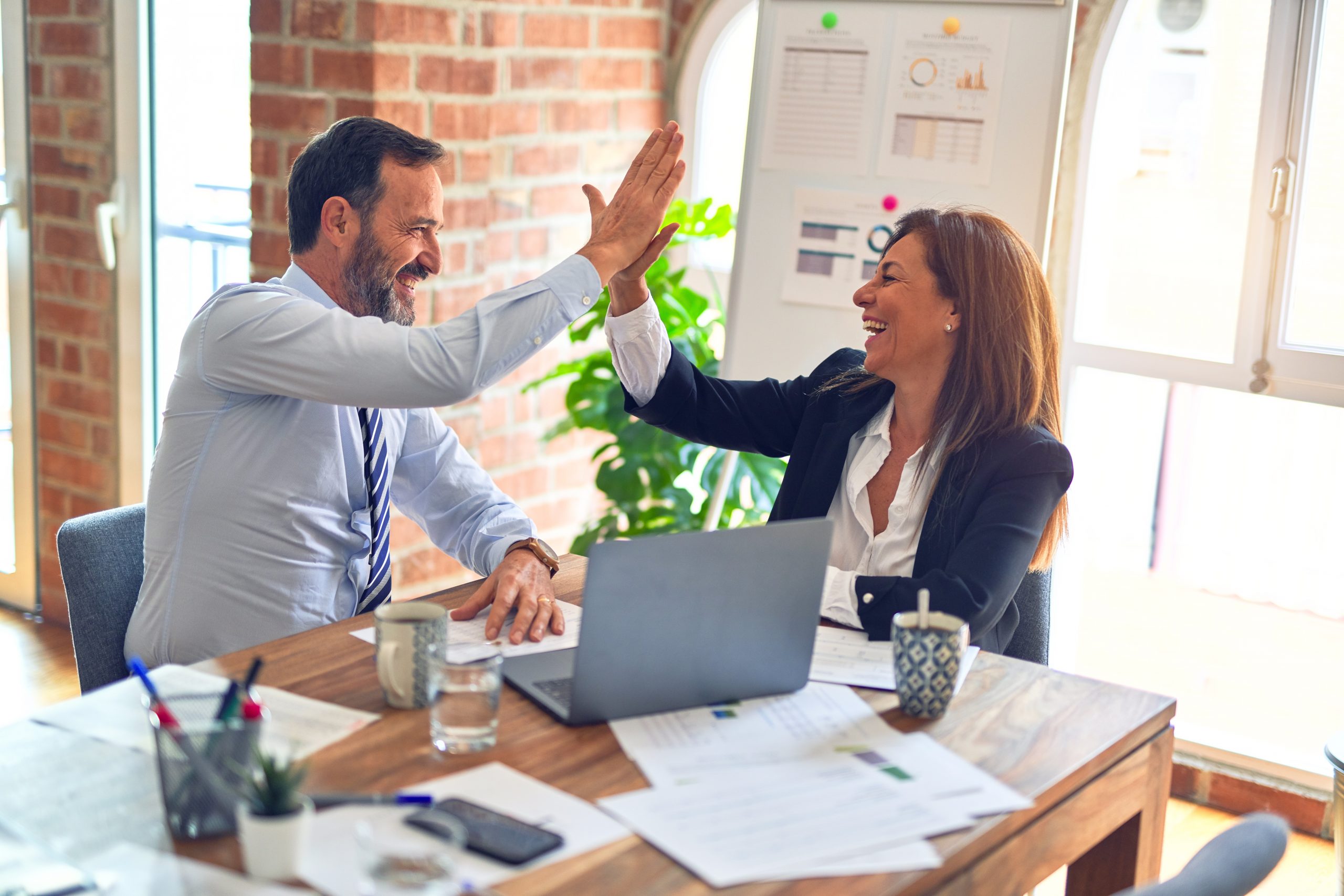
Of considerable interest, this concept often mystifies newcomers to field of Six Sigma. As you already surmised, the referenced charts rely upon the assumption of a unilateral specification (single-sided performance requirement). From a defect accounting point-of-view, it should be fairly obvious that a unilateral (one-sided) specification must be treated as a single defect category. However, a bilateral (two-sided) specification must be treated as two independent defect categories (for purposes of quality accounting), but recognized as only one defect opportunity (per unit). It is the latter case that most often causes the confusion.
To illustrate, let us consider a simple example. Suppose we have a certain critical-to-quality characteristic (CTQ) called weight. We shall say that this particular performance variable has been assigned a bilateral performance tolerance – an upper specification limit (USL) and lower specification limit (LSL), respectively. Given this, we naturally recognize that a violation of the USL would represent an overweight condition, while a failure of the LSL would constitute an underweight condition. Of course, any given unit of product can only fail one specification or the other, but not both concurrently. For this reason, it can be said that the two requirements are mutually exclusive.
Now, let us hypothesize that we just produced and evaluated 100 units of product. For the sake of discussion, it will be known that 2 of the units violated the LSL and 3 units failed the USL. Consequently, we fully acknowledge the occurrence of 5 defects. However, we only recognize 100 defect opportunities. This holds true because the given specification limits (USL and LSL) are mutually exclusive. With this mind, we compute the defects-per-opportunity as DPO = D / (U * O) = 5 / 100 = .05. By way of transformation, we discover that the computed DPO is equivalent to 1.65s sigma (one-sided). By factoring the 1.50s shift we are able to approximate the equivalent short-term capability as 1.65s + 1.50s = 3.15s.
So as to extend our example, let us consider the addition of another CTQ, say thickness. For the sake of argument, we will let it be known that this particular performance variable has been assigned a unilateral specification. In this instance, the CTQ was given an upper specification limit (USL). For the same 100 units of product, it will be accepted that only such one unit violated the thickness requirement. Thus, for this defect category, we observe DPO = 1 / 100 = .01. With this quantity as a backdrop, we determine the equivalent short-term capability to be 3.82s.
In an effort to define the overall level of quality, we must first recognize that a total of 5 + 1 = 6 defects were discovered during the course of producing the given 100 units. Furthermore, we must concede there exists 2 independent CTQs per unit. Owing to this, we understand that 100 * 2 = 200 total defect opportunities were created. Hence, we assert that DPO = 6 / 200 = .03. Again, by transformation, we are able to establish the equivalent short-term capability as 3.38s. Thus, we now recognize that the overall capability can not defined by the simple average of subordinate capabilities.