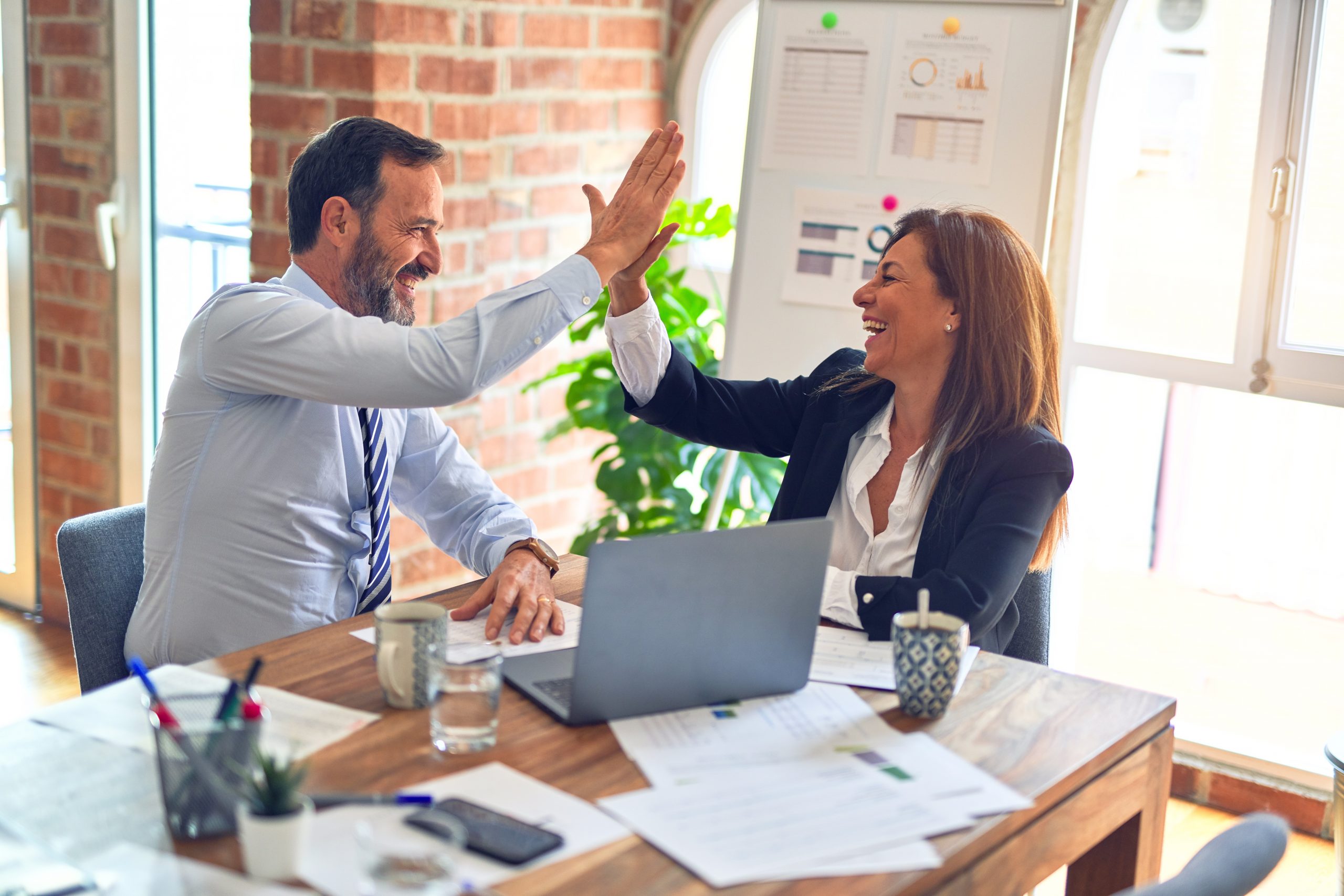
According to Wikipedia, the internet encyclopedia, Kaizen http://en.wikipedia.org/wiki/Kaizenis : “Japanese for “change for the better” or “improvement”, the English translation is “continuous improvement” or “continual improvement.” The goals of Kaizen include the elimination of waste (defined as “activities that add cost but do not add value”), just-in-time delivery, production load leveling of amount and types, standardized work, paced moving lines, right-sized equipment, etc.”
The above implies that Kaizen would only be applicable in a factory-like production environment. Too bad for all of you in service and transactional activities!
But, Wikipedia continues “A closer definition of the Japanese usage of Kaizen is “to take it apart and put back together in a better way.” What is taken apart is usually a process, system, product, or service.” This is interesting as it opens the door for trying it in service, transactional and/or IT driven environments also.
And finally Wikipedia states “The only way to truly understand the intent, meaning, and power of kaizen is through direct participation, many, many times.”
In other words, don’t hesitate if you want to experience the true power of a Kaizen event, just go out and do it, as I have done a couple of times just recently. It delivered us great results and learnings in just a couple of days.
Transactional Kaizen are focused, well scoped, time limited (a couple of days max), business improvement initiatives. The mere fact that one is focusing on 1 subject eliminates mental change-over time. This results in high participant motivation and satisfaction and most importantly, faster, better results then the traditional weekly 1-hour problem solving meetings that tend to go on for ever and ever as scope creeps away over time.