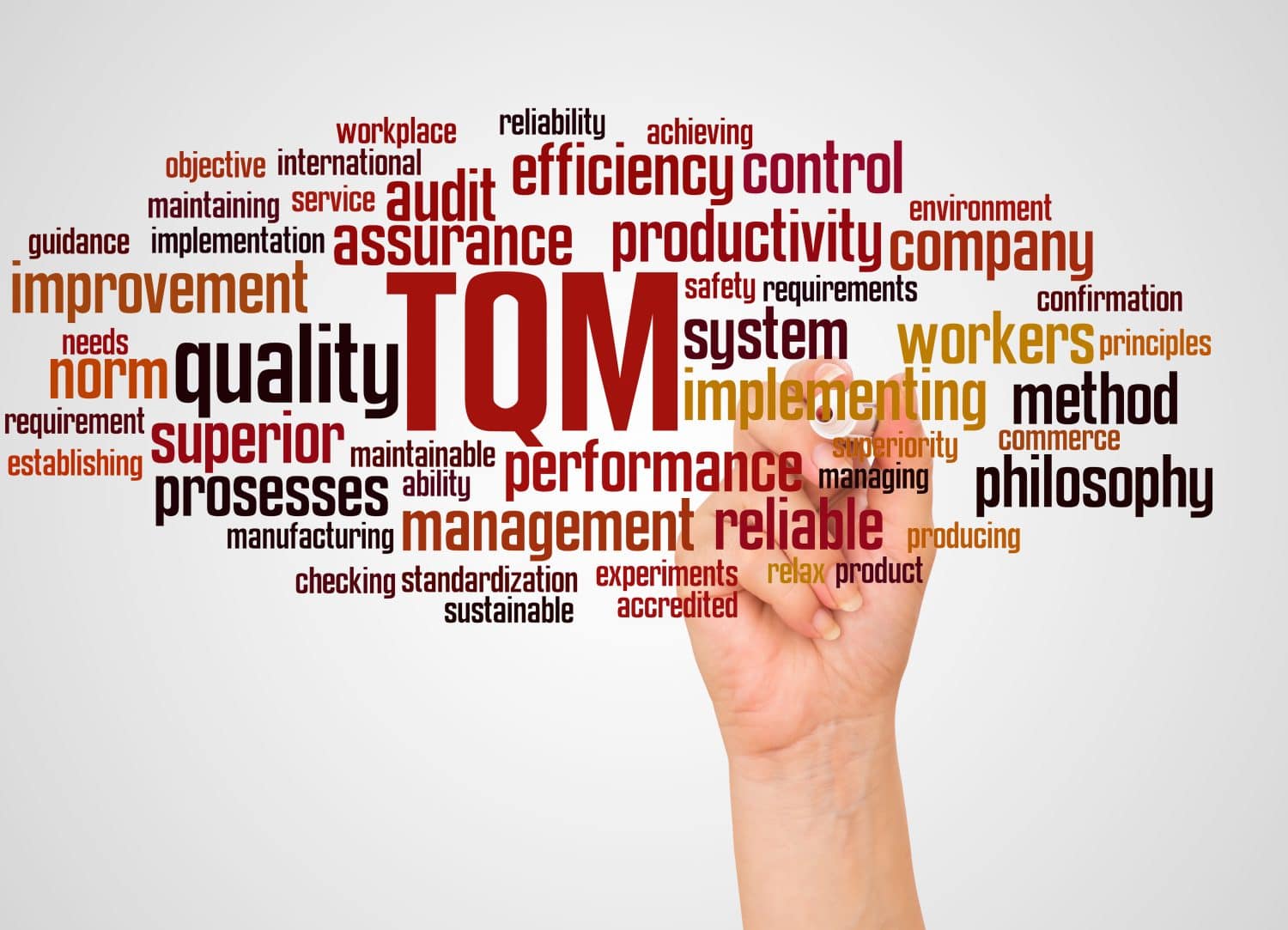
© Pedal to the Stock/Shutterstock.com
A large, Indian, fast-moving consumer goods company had completed successful total quality management (TQM) projects to improve its manufacturing efficiency, expedite vendor payments, and increase the availability of finished products. For its next project, the company wanted to address problems in human resources (HR). By working with HR process owners, a focus for the project emerged – the payroll process.
The following case study details the company’s experience using the TQM methodology’s seven steps of problem-solving to address the issue.
Pre-step 1: Select the Problem
After attending an introductory two-day training program in TQM, the project leader asked the company’s HR employees to brainstorm key problems in human resources. They also considered the results of each problem (Table 1).
Problem | Result 1 | Result 2 |
---|---|---|
Accuracy of data | Delay | Errors |
Delayed output | Delay | |
Functioning of payroll centralization process | Delay | |
Manual data generation | Delay | |
Follow-up on data | Delay | |
High recruitment turnaround | ||
Lack of standard operating procedures (SOPs) | Delay | Errors |
Communication | ||
Delayed response to employees | Delay |
From this list, the group could see that the real problem was that internal customers were facing delays and errors. The group went on to brainstorm and prioritize the major areas of errors and delays within HR (Table 2).
Problem Area | Score |
---|---|
Employee database | 169 |
Payroll | 139 |
Separation | 125 |
Recruitment transfers | 117 |
Budget | 114 |
Talent development | 113 |
Performance management | 98 |
Communication | 90 |
Training | 64 |
Reimbursements | 63 |
Discussion revealed that the employee database is not a problem in itself; the team decided to tackle the payroll process instead. HR employees told the group that completing their jobs each month without delays or errors required a lot of pressure and running around.
A representative group from the finance department, the payroll manager, key payroll personnel, and the four regional HR managers were selected for the project team. A leader and secretary were nominated, and the team began meeting every other week.
Step 1 – Defining the Problem
In TQM, a Problem = Desire – Actual Status; problems also must be measurable. The team faced the challenge of measuring “undue pressure” on behalf of the payroll employees. They decided that the metric of employee overtime could represent this pressure.
The team set out to record how much overtime (OT) each employee was incurring daily and what activities they worked on during that overtime. Measurements during the first month yielded an average of 36 minutes of overtime per person per day.
This average did not appear so bad. In reality, however, the problem was the peaks rather than the average. Employees tend to remember the stressful days when overtime is high. To get a better picture, the team calculated a standard deviation of 18.8 minutes. This meant that on the worst days, overtime was an average of 92 minutes per person (average + 3 standard deviations) – and on those days, there were two or three employees whose overtime was much higher than 92 minutes.
Therefore, the team decided to work to reduce the average + 3 standard deviation limit to address the problem. They set a Phase 1 target to reduce the average + 3 standard deviation time by 50 percent.
Step 2: Finding the Root Causes
The team mapped overtime activities in a Pareto diagram to ascertain the vital causes (Figure 1). Table 4 shows the top 7 causes accounting for 81 percent of the OT.

Problem | Overtime Percent |
---|---|
Recruitment | 17 |
Meetings | 16 |
Data crunching | 14 |
Employee relations | 14 |
Master changes in SAP | 10 |
Special projects | 5 |
Head office formats | 5 |
Recruitment necessitated after-hours interviews, while meetings involved other departments not yet trained in TQM. The causes that the team could change were data crunching, master changes in SAP (the enterprise resource planning program), and repeated changes in data formats requested from the head office. These three areas constituted 29 percent of the overtime and were addressed first.
Sixty percent of the overtime in these areas emanated from two regions; another 35 percent came from two employees in the head office. Why? The other region representatives explained that they had put in a special one-time effort to develop data entry and storage formats for the diverse information requested by the head office to reduce future data crunching. They shared this standardized formatting with the two lagging regions to reduce their overtime.
But why were the regions developing formats in the first place? Were the formats not present already? The team mapped the current process steps:
- Regions enter changes to be made in the SAP personnel master into an Excel sheet
- Excel sheet sent to head office
- Head office employees enter data into SAP before the payroll each month. The payroll employees face intense pressure due to gaps and errors in the data entry.
Step 3: Countermeasure Ideas
The team suggested a two-phase process change using just-in-time principles:
Phase 1: Replace batching with flow processing. With this method, regions enter and send data weekly, and the head office enters weekly, without waiting until the end of the month.
Phase 2: Eliminate non-value added stages. Eventually, the regions should be able to enter data directly into SAP weekly, and the head office will enter its entries weekly.
Steps 4 and 5: Testing Ideas and Checking Results
The countermeasure ideas took two months to test. An X-bar control chart was introduced to track the average overtime per person per day. The chart showed a 48 percent reduction in average time + 3 standard deviations, from 92 minutes to 50 minutes.
Step 6: Standardizing Operations
The 3 standard deviation limit was maintained. Simultaneously, however, employees were also experiencing stress and working overtime due to errors or incomplete entries during the payroll run and frantic queries for the correct information. Finding the most frequent errors, their root causes, and countermeasures would eliminate this problem.
The team selected the metric errors per query per payroll. There were 65 in the first run. Following is an example of an error, its cause, and the countermeasure the team developed to resolve it:
- Error: Incorrect deduction of lunch coupons
- Number of occurrences: 11 in two months, or 15 percent of total errors
- Root cause analysis: All errors occurred in one region. The region with errors gave lunch coupons at the beginning of the month, while other regions gave them at the end of the month, thus making the accounting foolproof.
- Countermeasure: Adopt standard process
- Check the result: No errors post-implementation. Within three months, errors and queries were reduced by 98 percent from 65 per payroll run to 1. Regular progress tracking was introduced (Figure 2).

Step 7: Maintain Improvements
The team compiled the improvement results and presented them to management. In the future, the payroll manager will meet with the staff after each payroll run to analyze and address any errors that are occurring. The overtime control chart will be plotted every day, and any unusual spikes will be analyzed and addressed.
The project also led to changes in the mindsets of the employees involved. For instance, after the project, the human resources director remarked how one of the participants made an error in his work and reported it, along with a 5-whys and countermeasure analysis – something that would never have happened earlier.
The image featured at the top of this post is ©Pedal to the Stock/Shutterstock.com.