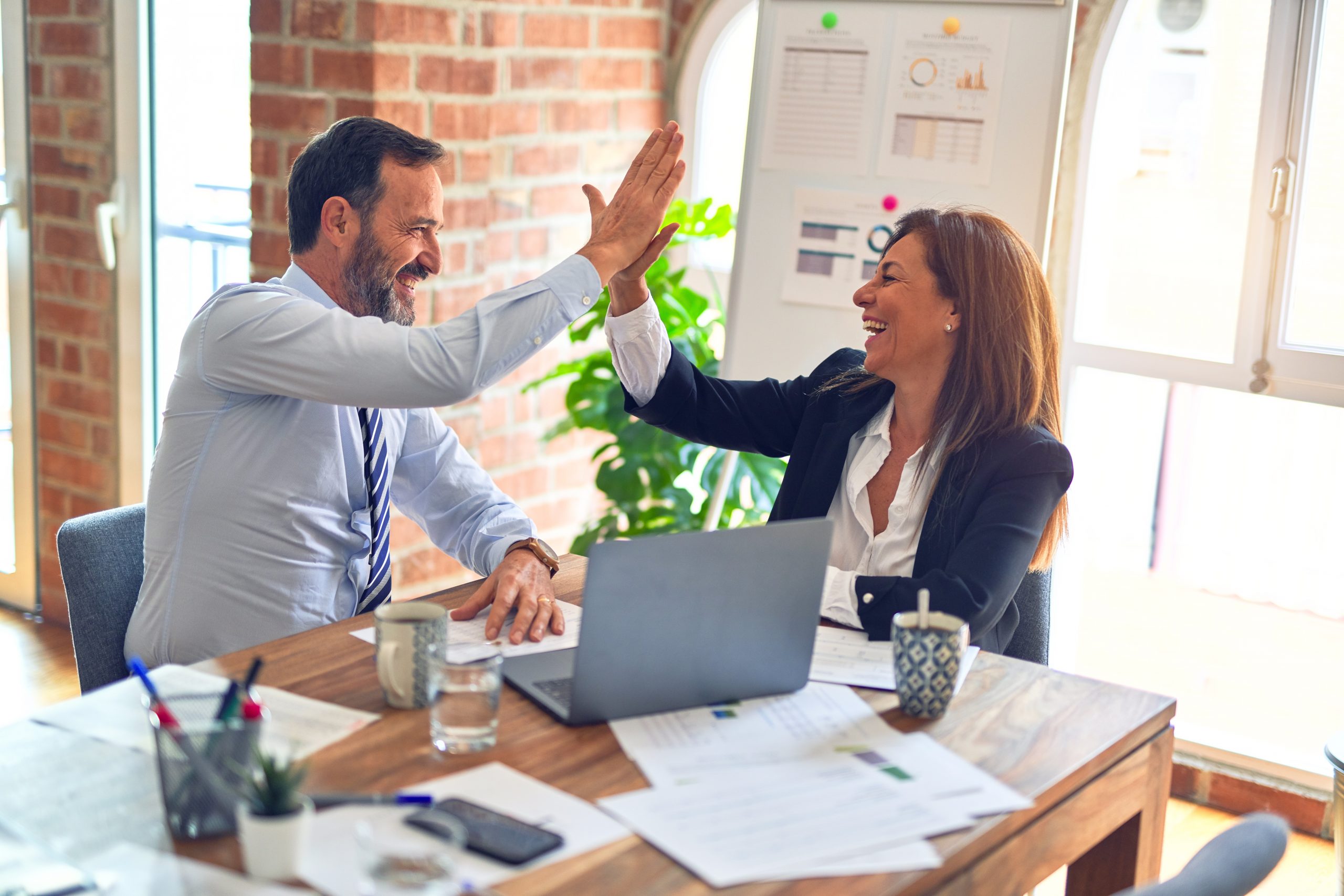
A P&L manager who is preparing a monthly report starts gathering the information he needs. He realizes that this month’s sales figures are not broken out by region, so he calls accounting and asks for the regional split as quickly as possible. He also discovers that he has updates on only three of the four Lean Six Sigma projects in his unit. The Black Belt for the missing project is on the floor that day, so he spends a few minutes tracking her down and getting a verbal update. Then all he has to do is get the month’s wages/benefits figures from human resources, and he’s ready to work on that report.
Dave, one of the more experienced technicians in IT, knows more about PCs than nearly anyone in the company. PCs are used by every department except the graphic design group which uses Macintoshes. So, even though Dave spends 95 percent or more of his time supporting the PC users, he still has to answer a handful of calls each month from the Mac users. He describes the experience as having to “reconfigure” his brain so he can switch from thinking in Windows to thinking in OS X.
Marcie in personnel is the gatekeeper of incoming job applications, which arrive by mail, by fax and via the company’s website. She finds it more convenient to wait until she has a stack of at least 20 applications to log into the database all at once, rather than doing them as they come in.
These examples reflect what happens in most companies – constantly tracking down information to finish a task, mixing duties which are only rarely performed with regular duties, batching work items because it seems more convenient and efficient that way.
Lean Six Sigma practitioners recognize that although each of these job practices are common in service functions – and usually accepted as “the way work is done” – they each represent non-value-added work that increases delays and extends work in progress. Thus, they also impede the quick completion of value-added work.
In Lean terminology, the three situations described above are all considered “setup problems” that delay or interrupt people as they try to complete their value-added work: In the first case, there are delays as the person tracks down the information. The IT support employee is less efficient at work he performs infrequently because of the learning curve, having to switch his brain from one way of thinking to another. Job applications are delayed because the gatekeeper prefers to work in batches.
The Rapid Setup Method
The tool for attacking setup time is the four-step rapid setup method. The principle of this method is to eliminate anything that interrupts or hinders productivity. Here’s how it works in financial services:
Step 1: Identify and tabulate any process-related work that fits into one or more of the following categories:
- that delays the start of
- causes interruptions to value-added activities
- that starts off at reduced output rates (likely due to learning curve issues)
- that is very similar or identical to another task in the process
Category 4 is the hardest for people in service functions because there is so much waste and non-value-added work that is taken for granted. Supervisors, or in the case of a project, team members must learn to objectively observe people as they perform the tasks of a process and note anything that prevents them from performing the value-added work. If it a person is examining their own work, they must try to develop an awareness of when they have to slow down or stop doing value-added work in a process. Then they should ask themselves why they had to stop. There will always be interruptions, but only process-related items are being considered here. For example, a buyer completing a purchase order may get a phone call from another employee requesting information. The processing of purchase order may be interrupted, but that delay is not caused by something inherent in the purchase order process.
As service offerings/features expand over time, tasks may grow up that are nearly identical. When tasks that are similar to other tasks are discovered, the question must be asked: Can they be combined to eliminate a setup? If so, the change should be implemented as quickly as possible.
Step 2: See if any of the interruptive/delaying work can be offloaded – in other words, handled outside the process, so that the information/material is waiting when needed, rather than causing a wait.
The goal is to be able to zip through all the value-added work in a process without any delays or interruptions. Looking at problems identified in Step 1, a project team must ask why those problems appear, and figure out how to eliminate that source of delays or interruptions. The question team members need to answer is: “Why do we have to stop the process to take this step?”
Step 3: Streamline or automate any interruptive/delaying tasks that cannot be offloaded.
In any process, there will be some delaying or interruptive factors that are deeply woven into a process. The team should be creative in trying to find ways to either eliminate or drastically reduce the amount of delays that these tasks inject. For example, many pizza chains today just ask for a phone number the second time a person orders. They have eliminated the need to ask for a name, address and directions a second time.
Several streamlining approaches can be used when the cause of the delay or interruption is a “learning curve” issue associated with infrequently performed tasks. One is to funnel all the requests of a certain type to one person to increase the frequency (e.g., If 10 calls a month for Mac support come into the IT department described above, have one tech handle all 10 calls rather than spreading the calls among all the techs.) Or there are often ways to provide visual or automatic reminders that eliminate the need for people to remember the specifics of obscure processes (such as having pull-down or pop-up menus on a computer screen). Or a third party with the needed expertise might be hired to handle infrequent calls.
On the batching issue: Only batch if the setup problem cannot be solved. Another choice is to reduce process complexity so there are not so many setups in the first place.
Step 4: Bring the process under statistical control.
The setup is not complete until the output of the process is “in spec” and under statistical control. That means the amount of variation in lead time is within predictable limits of +/- 3 . An automatic reporting system should note any deviations outside this limit. As the new process is observed in operation, the team should look for ways to reduce variability in how the steps are complete or in the time it takes to complete them.
Big Bang for Few Bucks
One of the best aspects of the four-step rapid setup method is that the investment can often be almost entirely in intellectual capital (people’s brain power), with little or no financial capital (new equipment, software, etc.). The creative thinking can often be done in one or two brainstorming sessions, with some follow-up tests of the new methods.
But even if there are modest investments, the results are worth it. Process cycle time can be slashed by anywhere from 10 to 60 percent. Imagine how happy an organization’s customers will be if services are delivered in half the time it takes now.