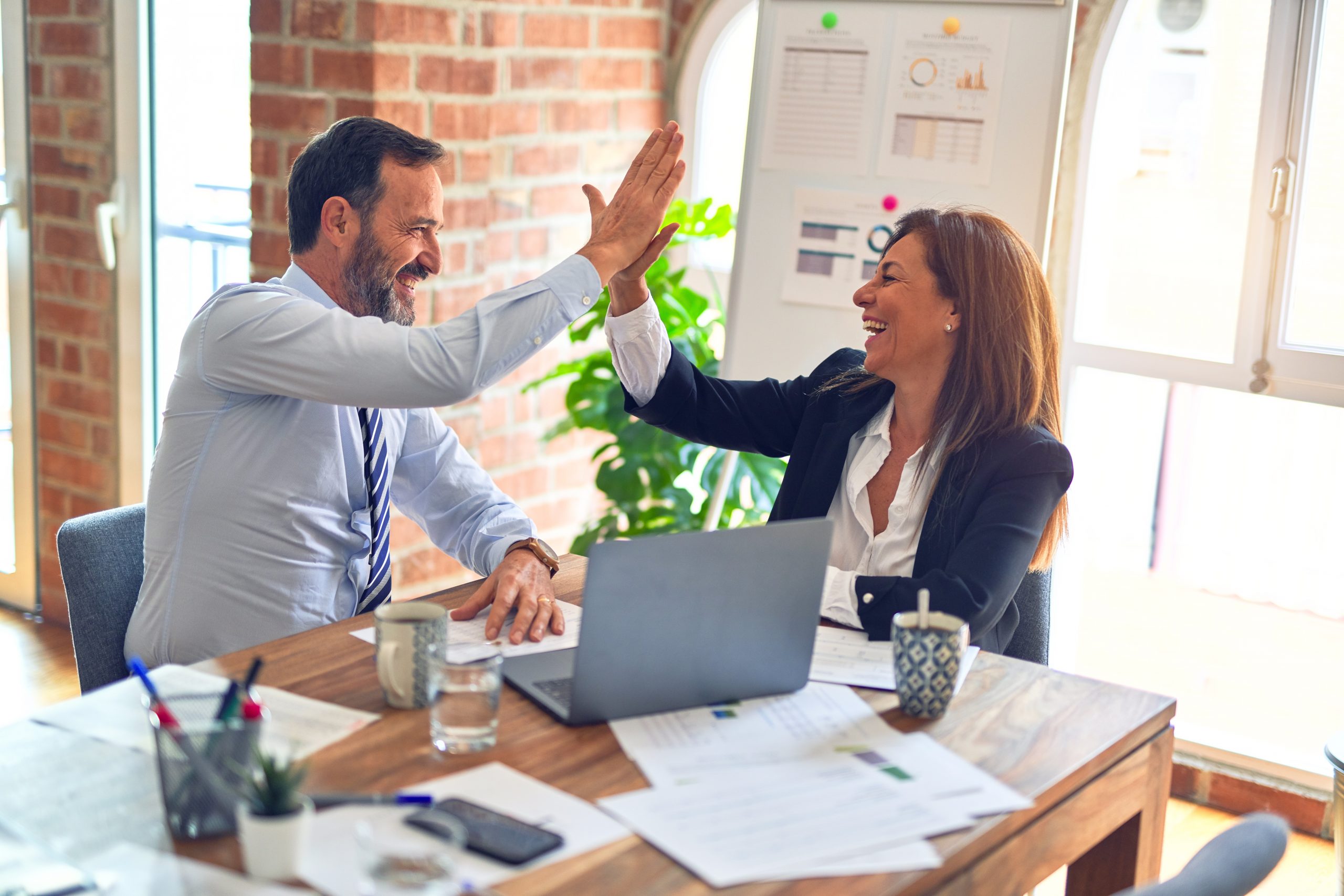
Lean is gaining wide acceptance in these troubled times of recession across the globe. Organizations are striving to be more efficient in order to create more value for their customers. Many are using a project approach to Lean, which means focusing on a specific process and improving that process to achieve a certain output metric.
Lean is based on a simple belief that waste in a system should be identified and removed. But the principles are not always easy to follow and execute. When attempting to complete Lean projects, it is common for new practitioners to stumble in some areas, particularly involving time studies. This article provides solutions to those trouble spots, thus allowing project leaders to achieve their objectives faster.
Question: Is it necessary to calculate takt time when completing a Lean project?
Before making the decision to calculate takt time, it is necessary to understand what takt time is and how it helps project leaders understand the problem at hand.
Takt time is a German word for the beat an orchestra produces. For Six Sigma purposes, it represents the rate at which a customer demands a product. If an organization is not producing a product in the maximum takt time, it will not meet customer demand. The formula used for calculating takt time is:
Takt time = Available working time/Total units demanded by customer
The examples in Table 1 illustrate how takt time is calculated in various real-life scenarios.
Table 1: Takt Time Calcuation Examples | |||
 |
Process |
||
 | Insurance claims clearance (within outsourcing unit) | Computer assembly | Case report form creation for drug testing |
Purpose | Checks are paid on the basis of clearance made | Computers are sent for delivery once assembled | Case report forms are programmed for the type of drug being tested |
Customer Average Demand | 50 claims/day | 200 jobs/day | 5 case report forms/month |
Available Time for Operation | 400 minutes/day | 400 minutes/day | 176 hours/month |
Process Lead Time | 2 days/claim | 75/minutes/computer | 3 months/case report form |
Takt Time | 8 minutes/claim | 2 minutes/job | 35.2 hours/case report form |
Interpretation | Every 8 minutes, the insurance company will get a verified claim | Every 2 minutes, an assembled computer should be available for delivery | Every 35.2 hours, one case report form will be ready for the customer |
Notably, the process lead time has no bearing on takt time and hence is not required for calculating takt time.
Takt time is more applicable to processes that are repetitive in nature and where there is a continuous stream of jobs. Hence, in the processes where the output expected by the customer is few and far between, takt time calculation can be avoided. For instance, in the case report form example above, there is an infrequent customer demand so takt time may not be required.
Once takt time is determined, the next task for process improvement practitioners is to look into the process and adjust processing time for activities so that the organization can meet the customer’s demand.
Question: How do you calculate wait time during value stream mapping when there are 100 jobs sent to the process at once?
This question haunts most people who start a Lean project. The answer lies in understanding the basics of Lean philosophy.
Taiichi Ohno, the father of Lean, prescribed one-piece flow as the ideal condition for a product to be handled. This requires Lean cells where only one piece is worked at a time, thus reducing total lead time from raw material to finished good. Ideally, this condition should be followed for making a system Lean and avoiding all waste, but this may not be possible in the practical world. If one-piece flow is not possible, practitioners should at least make an effort to reduce the batch size and convert batch flow into continuous flow.
If a process receives 100 inputs at a time and there is no way processing can be done for all 100 at once, 99 inputs are sitting idle while the first one is being processed. Calculating wait time for all waiting inputs gives practitioners an idea of how long the job waits before it is processed.
The following example illustrates the value of a time study. In this case, processing time for each job is 1 minute. Hence, wait time for the first job is 0 minutes, while wait time for the second job is 1 minute (including processing time for the first job). Wait time for the third job is 2 minutes (with processing time for the first two jobs), and so on. Thus, wait time for the hundredth job is the processing time for the first 99 jobs.
Wait time for the total n jobs can be calculated as:
Total wait time = Processing time of each job x (n – 1 ) x (n / 2)
To find the average wait time, the practitioner should divide the total wait time by n. Therefore, in this case, where n = 1, and the processing time of each job = 1 minute, the total wait time would be 4,950 minutes. The average wait time for each job would then be 49.5 minutes.
From this calculation, practitioners might determine that the processing wait time is too long and must be changed. This could be done by working with a smaller batch size, which would reduce wait time and make the process more efficient.
Question: What value does time calculation add when we know that the workers are busy and not idling?
Time calculation works as an eye opener. When practitioners are engrossed in the process, they know that workers are always busy – they usually are not idling time. However, time calculations can help practitioners determine whether there might be a better way to utilize the workers’ time.
Maybe there is a way to do something different, where workers spend the same working time but the job moves faster. For instance, in the above example, if the batch size is cut from 100 to 50, the total wait time will be reduced from 4,950 minutes to 1,225 minutes, and the average wait time for the job will go from 49.5 minutes to 24.5 minutes.