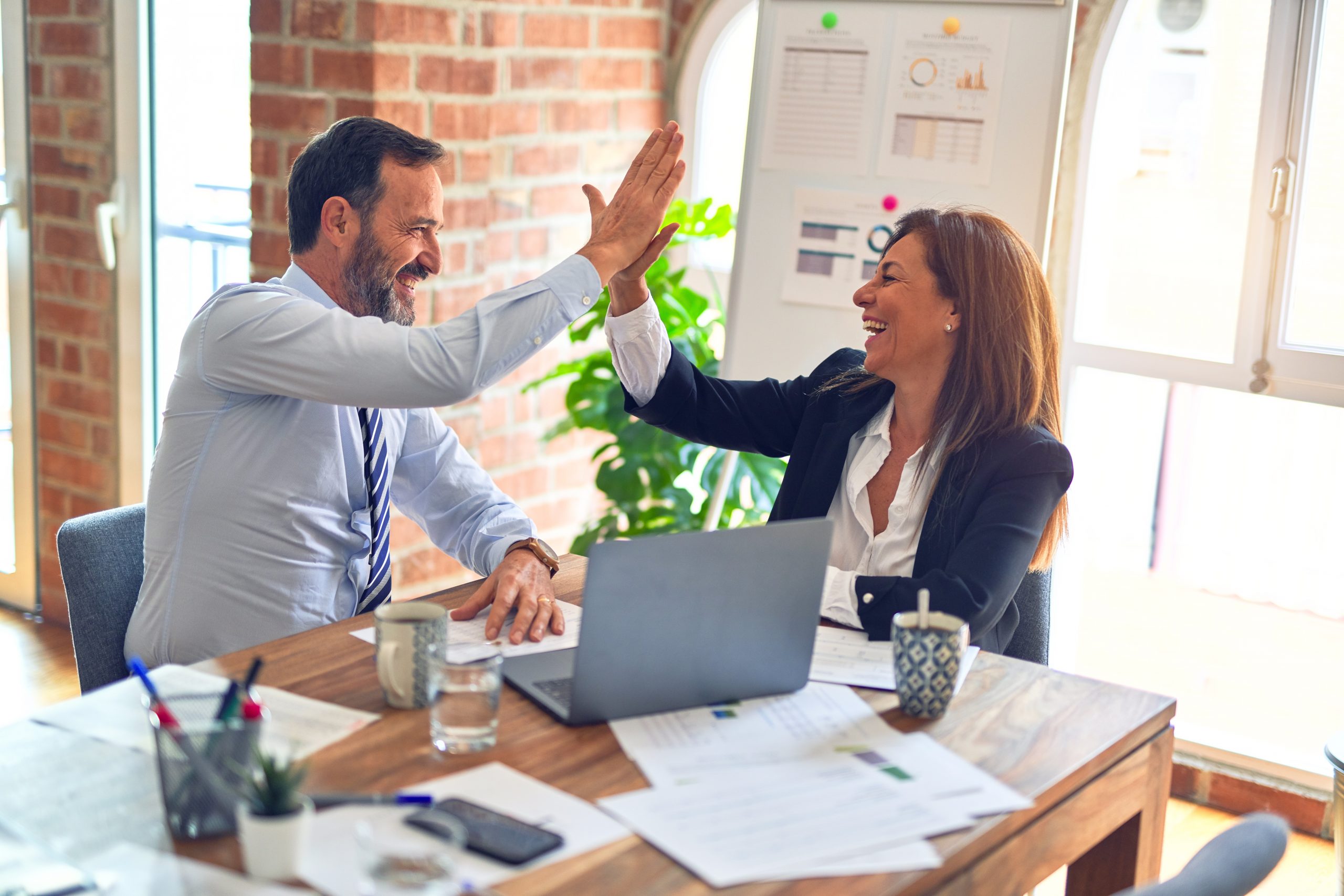
Having found that lab results assist clinicians in more than 70 percent of their patient management decisions, Virtua Health recognized that improvements made to lab processes would have a ripple effect on patient wait times in critical departments. For instance, blood work determines many emergency department (ED) decisions, and lab test results influence patient discharge. The importance of fast turnaround times could be crucial in many cases.
Virtua, a non-profit multi-hospital system headquartered in Marlton, New Jersey, employed Lean Six Sigma methodologies at its Voorhees campus laboratory to discover where bottlenecks and waste occurred and to streamline its specimen collection process.
As a result of the Lean effort, the project team implemented Kaizen improvements that:
- Decreased patient wait time.
- Decreased the distance staff needed to travel to complete tasks.
- Increased patient touch time.
- Improved lab turnaround time.
Bottleneck in the Process
The daily specimen collection run at the hospital began at 6 a.m. The majority of the volume occurred during this hour. This created a bottleneck (Figure 1) that affected all parts of the process.

Lean Analysis Reveals Opportunities
The Lean philosophy zeroes in on value from the customer’s perspective. It is designed to remove steps from a process that the customer does not deem valuable. The goal is to shorten the time between the start of a process (in this case, the lab order) and the end of the process (results available) by eliminating waste.Â
The Kaizen team observed specimen flow throughout the collection process. The observations were used to develop a spaghetti diagram, a time value analysis, and a value stream map. The value stream map of the specimen collection process (Figure 2) showed that only 44 percent of the time spent during the morning collection run was value-added from the patient and physician perspective.

The Lean tools highlighted several opportunities to reduce non-productive time:Â
- Phlebotomists were deploying in the morning, completing their floor assignments, and then searching floor to floor for their coworkers. The result was great teamwork, but a lack of efficiency.
- Specimens were waiting on the floors (an average of 44 minutes, and a maximum of 73 minutes) until the entire phlebotomy team returned together from their morning collection run.
- The batch of 200-plus specimens created a bottleneck that moved from the collecting process to the receiving process to the analysis process.
Kaizen Changes Decrease Wait Time
The team decided that level loading work among the phlebotomists and sequencing their activities were two key improvements necessary for success.Â
The team used the Lean principle of heijunka to approach this opportunity. Heijunka is the process of leveling and sequencing an operation. Instead of having phlebotomists hunt for their next patient, the team needed to consider the original deployment plan and implement more accountability into the process.Â
The first step was to re-evaluate the morning assignments. The team tried several different deployment strategies throughout the Kaizen week. Each new strategy implementation (called “trystorms”) produced opportunities for learning, ideas for improvement and reductions in the batch size.Â
Through the process changes, the lab supervisor now had a pulse on all of the collection activities and could act quickly when help was needed. Phlebotomists finished their initial morning assignments, brought their specimens to the lab for processing and were redeployed by the supervisor.Â
The Kaizen process changes resulted in a 70 percent reduction in the average specimen wait time (Figure 3).

Reducing Steps and Increasing Touch Time
The improvements to the collection process were taking shape, but the streamlined process highlighted confusion in the receiving department when the phlebotomists returned from their morning runs. The reconfigured assignments helped to sequence the phlebotomists’ arrival, but there were issues during tray restocking. Supplies were located in five different areas. In addition, staff moved throughout the department to retrieve supplies, adding on time and distance to the process while also contributing chaos to the already busy department workflow.Â
The solution: The team moved all of the phlebotomy supplies to one location just outside of the department. This resulted in several wins:
- Elimination of obsolete inventory
- Tighter inventory controls
- A 40 percent reduction in the distance traveled to restock trays
In addition, the Kaizen improved patient satisfaction by tripling touch time.Â
The Virtua Voorhees lab staff saw great wins in terms of reduction in travel distance, time saved and increased patient touch time. The real excitement, however, came when the staff started to see a reduction in its overall turnaround time. Chemistry cycle time from draw to report ready was reduced by 35 minutes. The lab director was pleased, noting, “This is a win-win situation. We will take these learnings and apply them at our other Virtua sites.”