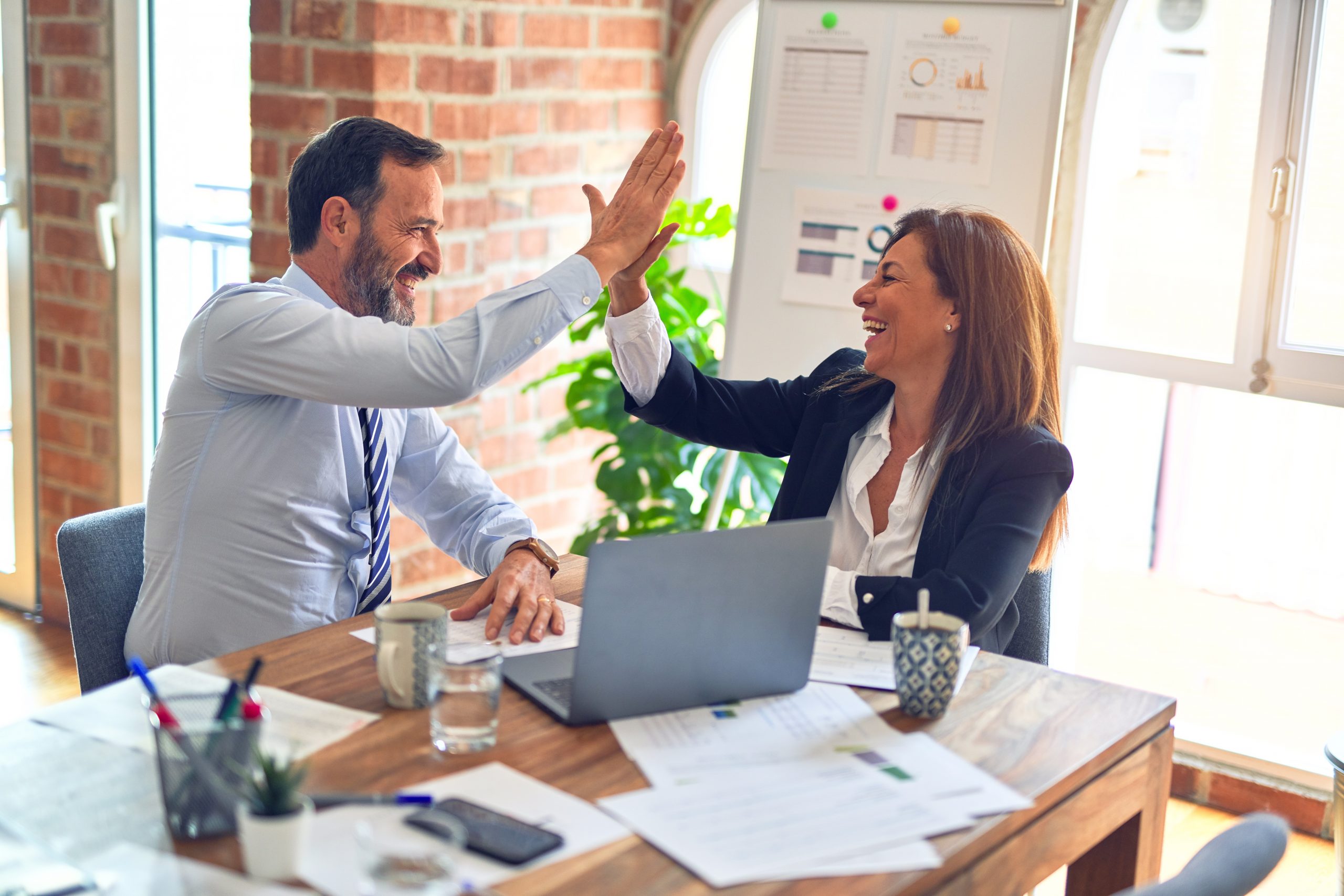
Lean and Six Sigma applications are different between service industries and manufacturing industries.
Is that statement really true?
There is no straightforward answer. The answer is ambiguous. It can be: no, there is no difference. But it can be: they are the same to certain extend. The answer can also be: yes, the application is different. An additional possible answer might be : it depends on the kind of activity.
No, there is no difference. Regardless if you are in a service of manufacturing environment, the work unit in progress is transformed from an input to an output ready to meet customer demands, using a process. Regardless if you are in a service of manufacturing environment you need universal “core processes”: a process to develop products/services, a process to bring them to the market, a process to produce them, a process to cash in revenue generated by them and a process to take care of your customers during use of them. Of course, you also need processes that support the “core processes”. If you have a process, you can apply Lean and Six Sigma principles and tools.
They are the same to certain extend. In theory the universal processes needed in service and manufacturing organizations are perhaps of a similar nature, in reality they are not fully comparable. An example: the typical life time of a car generation in the automotive industry is about 4 – 6 years. The typical life time of a communication product generation is a couple of months, 2 years maximum. There is clear difference in product generation turnover. Consequently, processes need to be designed and put into production a lot quicker, there is less time to optimize and lean them out to the full extend. This would suggest quick changing service industries should get their products and processes as defect free as possible before launching them. As this is certainly not always the case, service organizations may end up in endless loops of fire fighting. It might explain the current success of DMAIC and DFSS in service industries. (At least if success can be measured on the amount of white papers and book publications on this subject)
Yes, it is different. In manufacturing industries you can see the raw materials or semi finished product transform into the final product along the production line. In a service environment at best you can follow a paper flow, but in most cases you’ll need to trace the production history of the service in the computers. This creates certainly differences in the application of some of the tools. Take Value Stream Maps as an example. In manufacturing you can go see the shop floor and count the work in process in between the different work stations. In service industries you’ll need to dive into the computers and torture them until they give away their secrets and tell you where the work in progress is waiting to be processed. This can be a discipline in itself.
The type of data is different. Sure, you’ll find continuous and attribute data in service and in manufacturing, but not in the same amounts. In manufacturing, most of the data is continuous. In service the data I come across mostly is attribute. This has consequences on the application of many analysis tools (graphical tools and hypothesis tests), determining process capability and control charts.
It depends on the kind of activity. There is no such thing as the service industry and the manufacturing industry. A car glass repair specialist with workshops and mobile workforces is a total different kind of service then banking or insurances. Chemical process industry is a totally different kind of manufacturing industry then automotive assembly. Consequently, there might be big differences in the application of Lean and Six Sigma principles in service and manufacturing industries, depending on the type of activity.
Please feel free to comment on my thoughts and elaborate further on them, especially if you have had the opportunity, like me, to gather experience in both types of industry.