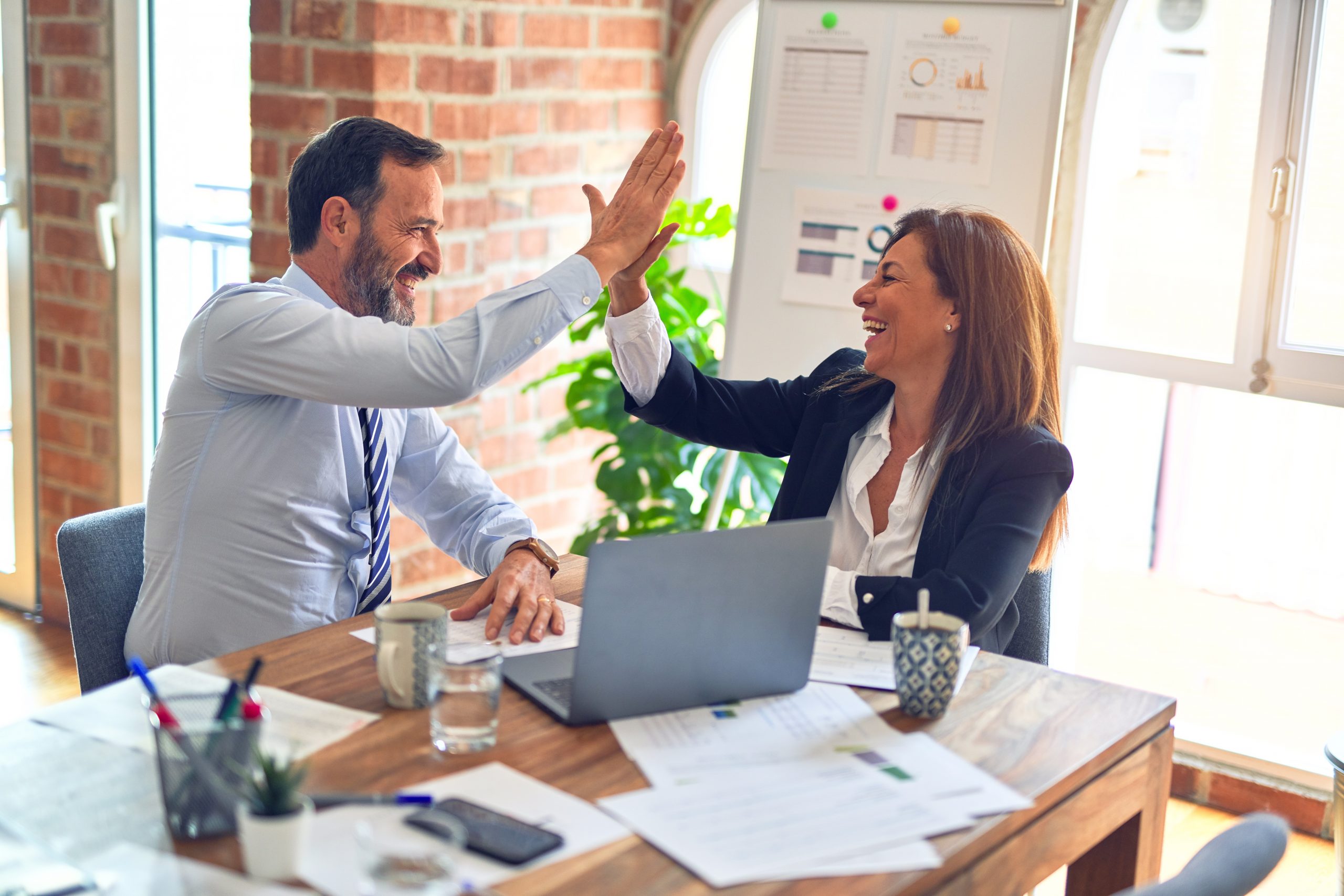
Today, irrespective of industry, corporations must focus on speed, efficiency and customer value to be globally competitive. Lean and Six Sigma are both powerful tools for improving quality, productivity, profitability and market competitiveness. While Six Sigma is focused on reducing variation using a problem solving approach and statistical tools, Lean focuses on eliminating waste and improving flow.
Both methodologies contain a number of process improvement tools. Companies can achieve strong improvements with these stand-alone tools. However, many realize suboptimal results due to poor project selection and inappropriate tool selection. An integrated approach to process improvement using Lean principles and Six Sigma begins with a strategic approach to identifying gaps between the current and future state. The final goal of this integration is to holistically optimize the entire supply chain by eliminating waste and controlling variation. One of the techniques that companies can adopt to systematically make progress in implementing the envisioned process is hoshin kanri. This technique encourages employees to reach the root cause of problems before searching for solutions, creating sustainable plans for implementation, incorporating performance metrics and taking appropriate action for implementation.
The Need for a Systems Approach
Hoshin kanri offers an effective way to tie the long-term strategy of the organization to process improvement efforts. Typically, organizations select their Kaizen events and process improvement projects based on where they currently feel pain. For instance, if they had a recent rash of external defects, they might decide to initiate a Six Sigma project as a corrective action response to the customer. Yet significant time and money is involved in running a Six Sigma project and it may not always be the best tool. In addition, even though this area is currently where the company is feeling the pain, it may not be the true highest priority project in looking at the big picture within the organization or the supply chain.
What is needed is a systems approach that focuses on the long-term vision and strategy of the organization. The time, talents, and money of the organization should focus improvements that will impact the flow of the entire organization and supply chain. As such, organizations should consider systems thinking using theory of constraints to ensure a broad impact on the entire organization and supply chain.
Adopting a systems approach will also greatly increase the momentum of improvement. As improvements are completed, their impact will be noticed by more people throughout the organization and supply chain. More people will experience the effects quicker, which will drive the participation and involvement of more people.
Current State and Practices
Many organizations on the Lean path begin by creating a value stream map. In doing so, they develop a current state map of how they presently create value for their customers. This task is then followed by the creation of an enhanced future state map, wherein practitioners incorporate best practices into their processes through research and benchmarking. The final goal is to optimize the process of value flow throughout the supply chain by eliminating waste and controlling variation.
However, achieving full implementation of the enhanced future state value stream map is far more complex than developing it. Hoshin kanri can help companies to make progress systematically in implementing the envisioned process. Although developed in Japan, hoshin kanri is based on Deming’s classic plan-do-check-act (PDCA) improvement cycle. Japanese Deming Prize winners credit hoshin kanri as being a key contributor to their business success.
In addition, hoshin kanri cascades the overall strategic vision of the organization throughout all levels, enabling employees to see how they fit into the big picture of the organization and through the supply chain. This linkage aligns everyone on the same strategy and vision. By focusing employees on a common direction, the improvements can have a much larger impact in considerably less time. Think about a small team whose members understand what they need to do and how effective they are in working together. Imagine a company of 500 or 1,000 employees or larger all working together to achieve a common goal throughout the supply chain.
Proposed Methodology
The Lean and Six Sigma methodologies both drive continuous improvement. To realize significant improvements, however, Lean and Six Sigma efforts must be linked to the strategic vision and goals of the organization. This will ensure the most appropriate projects are implemented to achieve the greatest gain.
An integrated approach is needed that utilizes long-term strategic planning to identify process improvement activities and then helps practitioners to select the appropriate technique. The following five-phase approach can be used to implement the enhanced future state value stream map using hoshin kanri to expedite the process. A graphical representation of the five phases is given in Figure 1.
Step 1: Deploy formalized training – Start by deploying formalized Lean and variation reduction (or Six Sigma) training. Formal Lean training should include lessons on the technique followed by an implementation project.
Step 2: Hoshin kanri/policy deployment – At the same time as deploying the formalized training, capture the strategic goals of the organization. The goals can then be driven down through the organization and throughout the supply chain and integrated into the daily activities.
Step 3: Value stream mapping – Value stream mapping is performed to identify all value-added and non-value added steps required to bring a product from raw materials to the customer. Map the current state of the supply chain to identify how the process is currently operating.
Step 4: Gap analysis – Perform a gap analysis between the current state, future state and strategic goals to identify Kaizen bursts for areas of improvement. Develop the future state to design a Lean flow. Prioritize the identified kaizen bursts.
Step 5: Perform Kaizen events – Standard work and 5S must be top priority because these techniques lay a foundation by improving consistency. Using the prioritized Kaizen bursts, develop action plans or schedules to perform the Kaizen events or Six Sigma projects.
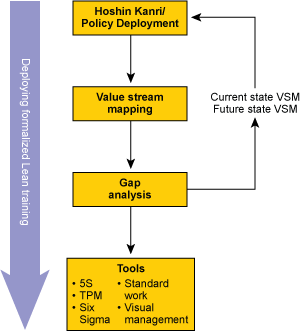
Implementing Hoshin Kanri
Japanese quality thinking began before 1645. Miyamoto Musashi wrote a guide for samurai warriors on strategy, tactics and philosophy called A Book of Five Rings (translated in 1974). Musashi (1584-1645) was a Japanese swordsman who became legendary for his duels and distinctive style of swordsmanship. In his book, Musashi states, “If you are thoroughly conversant with strategy, you will recognize the enemy’s intentions and have opportunities to win.”
A corporation’s strategic plan must be integrated with the macro-level value stream map to identify the optimal improvement opportunities in the supply chain. This promotes strategic thinking. Often improvement activities are identified with silo thinking. The effects on other systems or processes within the organization and the supply chain are not considered. Improvements in one area can have a negative impact on another business area.
Hoshin kanri began in Japan in the early 1960s as statistical process control (SPC) became total quality control (TQC) (Akao, 2004). Hoshin kanri is most commonly referred to as policy deployment. Hoshin means shining metal, compass or pointing the direction. Kanri means management or control. The following is an overview of what policy deployment is and does:
- Policy deployment is a systems approach to management of change in critical business processes.
- It is a methodology to improve the performance of critical business processes to achieve strategic objectives.
- Policy deployment improves focus, linkage, accountability, buy-in, communication and involvement in a corporation.
- It links business goals to the entire organization, promotes breakthrough thinking and focuses on processes (rather than tasks).
- Policy deployment also is a disciplined process that starts with the vision of the organization to develop a three- to five-year business plan and then drives down to one-year objectives that are deployed to all business units for implementation and regular process review.
Policy deployment is a business management system designed to achieve world class excellence in customer satisfaction. The system, beginning with the voice of the customer, continuously strives to improve quality, delivery and cost. The system provides the necessary tools to achieve specific business objectives with the involvement of all employees.
As shown in Figure 2, the voice of the customer is used to drive business targets. Then, using policy deployment as a management strategy, practitioners drive down this strategy throughout all levels of the business, including the supply chain, to focus on safety, quality, delivery and cost. Then using foundational Lean Six Sigma tools such as pull, 5S, SMED, standard work, TPM and VSM, practitioners can focus on continuous improvement. This leads to improved customer satisfaction, which further leads to improved sales growth for the organization.

Achieving Goals
Hoshin kanri is a methodology to capture strategic goals and integrate these goals with your entire organization’s daily activities. Effective planning is critical for the long-term success of a corporation. Hoshin kanri is the system that drives the continuous improvement and breakthroughs. In order for organizations to reap maximum gains from their process improvement efforts, they must link their strategic goals with their business system and use this system to select appropriate Lean or Six Sigma projects.
References
Musashi, M. (1974). A Book of Five Rings: The Classic Guide to Strategy. Translated by Victor Harris. Woodstock, New York: Overlook Press.
Akao, Y. (2004). Hoshin Kanri: Policy Deployment for Successful TQM. New York, NY: Productivity Press.