
So what is the real difference when looking at Cpk and Sigma Level? If you’re new to Six Sigma, there is no shortage of acronyms and calculations to keep in mind as you work on your knowledge base. Both Cpk and Sigma Level are valuable tools when looking at your processes and production. So, let’s demystify these elements and get you up to speed.
What is Cpk?
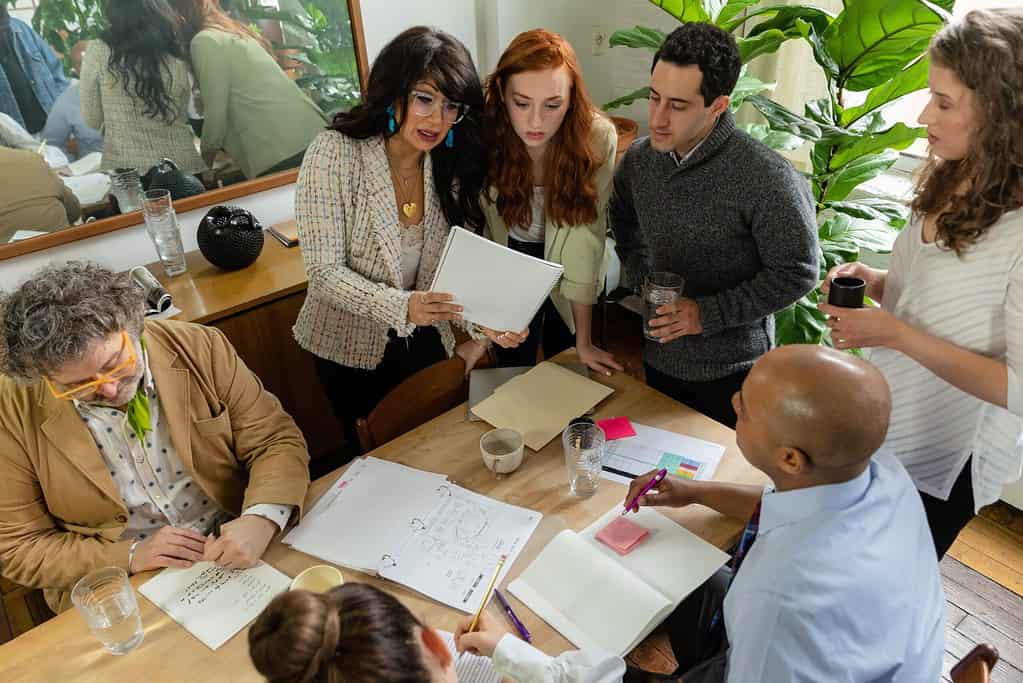
Cpk is short for Capability Index. It is a measurement of the capability of a process to deliver output that is within the specification limits of a process.
The Benefits of Cpk
With Cpk, you can determine how closely a process can meet overall specifications in its ability to produce output. It acts as an indicator of how consistent a process is with the average performance.
How to Calculate Cpk
Cpk is expressed in equation form as:
Cpk = min(USL-mean/3σ, mean-LSL/3σ)
This means that Cpk is equal to the minimum value of these two calculations. For example, if USL-mean/3σ gives you 1.16 and mean-LSL/3σ gives you 1.25, your Cpk is going to be 1.16. That is because 1.16 is the lower of the two amounts and is therefore used as the minimum value.
σ is a symbol that is used to represent the standard deviation.
LSL means the Lower Specification Limit and USL means the Upper Specification Limit.
Here is how you would use this equation to find the Cpk using real-world data:
A high-end home furnishings company has launched a line of handmade ceramics to be stocked in all of its stores nationwide. As part of the line, handmade ceramic bowls are being made and manufactured for the company and delivered through several suppliers. Obviously, with the bowls being handmade and coming from various suppliers, some deviation is to be expected. To manage quality control, the home furnishings company has set parameters.
One of the parameters set is that the mouth rim for the largest of the decorative ceramic bowls must have a Lower Specification Limit of 39 millimeters and an Upper Specification Limit of 49 millimeters. The standard deviation for the mouth rims will be 2 millimeters, and the mean value for the mouth rims, given the quantity count, should be 40 millimeters. Plugging this information it looks like this:
(USL-mean/3σ)
(49 – 40)/3 x 2
9 / 6 = 1.5 mm
(mean-LSL/3σ)
(40 – 39)/3 x 2
1 / 6 = 0.16 mm
The solutions are 1.5 mm and 0.16 mm. Of the two solutions, 0.16 is the lowest, so that will be the minimum value.
Cpk = 0.16 mm
What is Sigma Level?
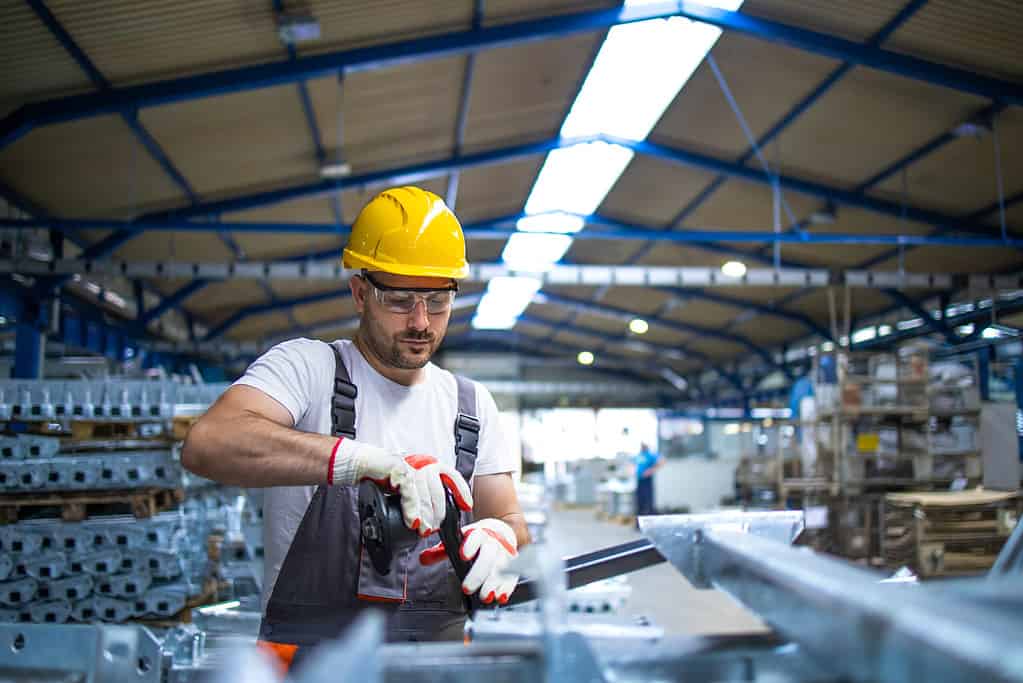
Sigma Level is a baseline metric that is utilized to understand the capability of a process to meet customer requirements.
The Benefits of the Sigma Level
With Sigma Level, you can better understand the quality capabilities of a process under the current conditions. You are also able to gauge how these findings match up against the expectations of your customers. Sigma Level also acts as an indicator of where there are possibilities for improvement as well as a verifier of the strength of process improvement efforts.
How to Find the Sigma Level
Sigma Level is based on the number of defects that occur in a process per million opportunities. There are six levels, with the sixth being the best.
- 1 Sigma: This Sigma level allows for 691,462 defects per million opportunities.
- 2 Sigma: With this level, there can be 308,538 defects per million opportunities.
- 3 Sigma: In this Sigma level, 66,807 defects are allowable per million opportunities.
- 4 Sigma: 6,210 defects per million opportunities are permissible at this level.
- 5 Sigma: At this high of a Sigma level, 233 defects are allowed.
- 6 Sigma: At this highest Sigma level, only 3.4 defects occur per million opportunities.
To calculate the Sigma Level for a process, you must first find the Defects Per Million Opportunities (DPMO). This is found by dividing the Defects by the Product x Opportunities.
Defects / (Product x Opportunities) = DPO
To find the DPMO, you then multiply the DPO by a million.
DPO x 1,000,000 = DPMO
You can now compare your DPMO against Sigma Level requirements to determine your Sigma Level. For example, if you have a DPMO of 175, you would fall within 5 Sigma.
You can also easily find the Sigma Level if you know the value of your Cpk. You need only multiply the Cpk value by 3 to find the Sigma Level. For example, if you have a Cpk of 2, then the Sigma Level would be 6.
Cpk(3) = Sigma Level
Cpk = 2
2(3) = 6
Sigma Level = 6
Cpk vs. Sigma Level: What’s the Difference?
Cpk and Sigma Level are so closely related that you can find the value of Sigma Level simply by multiplying the value of your Cpk by 3. Both Sigma Level and Cpk are index numbers that are used as indicators of the capability of a process to meet the needs of a customer.
They are also both calculated in similar simple ways. They are further similar in that they both use the standard deviation and the mean average. The difference in values is key, though. Sigma Level can be a number as large as 6 while Cpk will never be a number larger than 2.
Cpk vs. Sigma Level: Who would use Cpk and/or Sigma Level?

Any company that wants to know the capability of its process to meet the expectations of its customers could use either Cpk, Sigma Level, or both. The concepts are so related that it is unlikely that one would be used and not the other.
Cpk vs. Sigma Level: Real World Scenarios
A manager of a processing plant is working towards getting the plant up to at least 4 Sigma. The latest results from testing process capability show a Cpk result of 1.16. By multiplying that value by 3, the manager knows that the Sigma Level is 3.48. Some further improvements will still need to be made to processes to reach 4 Sigma.
Subsequently, having both of these measurements readily available gives the production manager data. We’ll harp on and on about the data-driven approach to Six Sigma, but that is for a good reason. Having the means to see where you can make improvements and refinements is a powerful tool. This same general scenario is playing out with businesses that’ve adopted the data-driven approach to quality around the world.
Other Useful Tools in Lean Six Sigma
While we’ve discussed the similarities and differences in the Cpk vs. Sigma Level debate, there is still plenty to explore. If you’re still hankering for a little more information regarding these sorts of measurements, I heavily recommend you check out our guide on Sigma Level.
Further, the Six Sigma methodology is rooted in a drive toward quality and performance. As such, why not take a moment and read about how your organization benefits from aligning with the performance metrics at the heart of the methodology?
Closing Thoughts
Cpk and Sigma Level are both powerful and simple indices to use to determine the capability of your process to meet the needs of your customers. If you know the value of one, it is very easy to determine the value of the other.