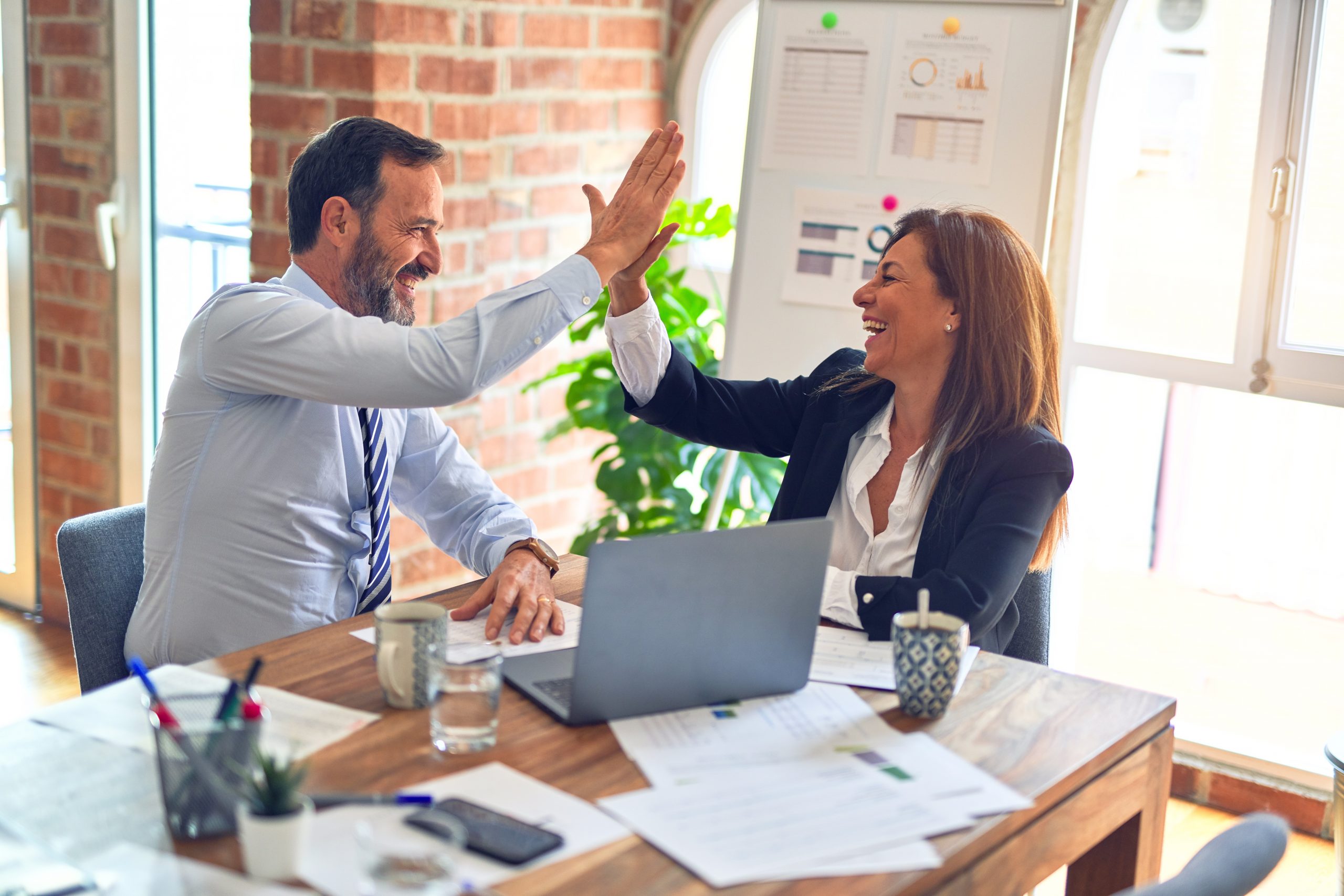
Process improvement. By now anyone involved in any type of manufacturing or service industry is familiar with this term. Although there may be a vast array of particular meanings that may be assigned to the term, everyone agrees process improvement is a necessary part of maintaining a viable business.
While most of the readers of this article are likely to be users of the Six Sigma methodology, many process improvement methodologies, when applied correctly, achieve comparable results. What is important to know is those common threads that run through all process improvement efforts that succeed or fail.
Improving Versus Certifying a Process
Some think that achieving some type of ISO 9000 certification is analogous to a process improvement effort. While ISO certification is a necessity in some industries, put on suppliers by their customers or regulatory bodies, it primarily verifies that a particular process is followed over and over again per controlled and documented procedures. So, theoretically, even if a process is regularly producing scrap and not capable of meeting customer requirements, it can be ISO 9000 certified. What matter is that the same documented procedures are constantly followed. So what is being certified is that the process will produce the same scrap rate month after month.
This is not to say that having ISO certification is non-essential to all. And it also can be a good starting point for companies to first get discipline around an existing process before they attempt improvement. The point is that there is a difference between certifying a process and improving a process.
Science and Art of Process Improvement
Process improvement is both a science and an art. Art? Any process involving people always has emotion and subjectivity which call for something much more than a book and calculator. Unless the system to be improve involves only a controlled environment to the point of a vacuum, process improvement will require those seeking to improve it to step out of all the textbooks and into the world of perception versus reality.
Countless companies proclaim, “…our people are our most important resources!” But few really ever take full advantage of their people. Unless a company is lucky enough to provide a service or product without competition, it needs to find ways to stay ahead of the gang of competitors eager to take your customers and market share. So why limit involvement in process improvement activities to a select few? Employing cross-functional teams on projects is a great starting point, not only does the organization gain insights from varying points of view, but it is encouraging a productive engagement between employees. This engagement may not have been possible before, except under less preferable circumstances, such as a sales representative bending the ear of a production supervisor about a late shipment.
This new association then leads to improvement initiatives born out of more informal means, because the person in charge of process improvement opened up communication and lowered animosity and anxiety. This is not to say that adversarial relationships exist between all departments in all companies, but I think some exist in nearly all work environments. So, it is wise for every business to take advantage of its knowledgeable people, not just those feeling the pain of the process, but those who are or may be involved in the solution.
Manage Projects with Measures
Another shortfall that often hampers the completion of a well intentioned project is the lack of any baseline measures. Measures/metrics need to lend a quantifiable view of the process with low subjectivity. Those involved in improvement activities have all attended project meetings that listed objectives like: “Improve accuracy of the quotes” or “Establish a better relationship with the customer” or “Take our service to the next level!” These are admirable goals, but the way to insure everyone is on the same page and working together is to define exactly what improvement means with some measurement. For example, improving the accuracy of quotes may mean bringing our quote accuracy to within 2 percent of the actual job cost 95 percent of the time. Then everyone is striving for a measure that all have agreed is the right one. And when the project is complete, everyone knows the project was successful because the measurement was improved.
Many times projects start off with great energy and enthusiasm, but then languish and lose momentum because it took too long to get to that critical and detailed measure which gives the group direction and common focus. That is why quality is one of the most misunderstood words around. Really. What does quality mean to a company’s quality professional, a colleague in another department, the company’s customer and/or the company’s CEO? “We provide a quality service or a quality product” is a common phrase. However, people expect a significantly different quality level from a disposable pen and a pilot landing a plane they are aboard.
Make Sure Improvement Sustained
And having this critical and quantifiable measure helps accomplish one of the most important elements of process improvement. That is sustaining the improvement to the process. Most people in charge of process improvement in an organization have seen a project bring great gains in productivity or efficiency, only to have the process revert back to the original performance. Why? Most of the time it is because the spotlight is off the process. No one was tasked with maintaining routine checks of this process through some predetermined routine.
Six Sigma talks of “process owners” that anytime in the project timeline are identified and then tasked with insuring the critical few factors/measures or sub-processes are regularly checked to sustain the new performance. Change takes effort and good habits are learned, just like bad ones, through repetition. In more technologically, advanced environments, monitoring of a system may take place automatically, resulting in emails or pages sent to personnel charged with acting on these situations. Whatever the scenario, it is crucial that critical conditions are kept to maintain the critical measure of success (performance level).
So, besides the specific training, experience and expertise required for improvement in each industry, anyone spearheading a process improvement effort should have the following:
- A strong cross-functional team in which participation is highly encouraged.
- A good way to truly measure success, one that is free of varied interpretations.
- A plan for handing off of the monitoring duties necessary to sustain the new level of performance.
By the way, when the project is done and successful, the team should not forget to celebrate. If a project has a long timeline, pick milestones along the way to maintain energy and reward hard work.