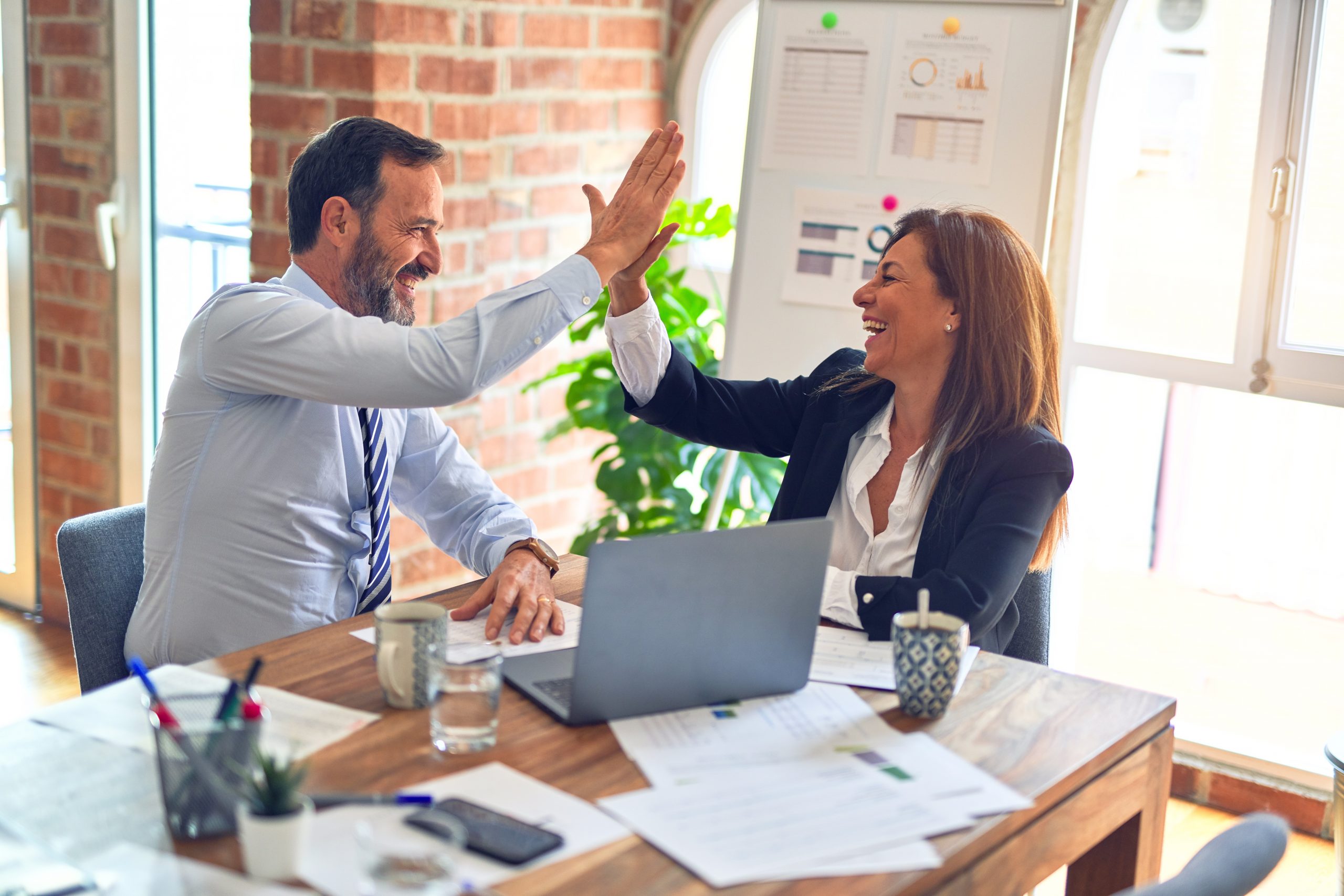
I have been thinking a lot lately about how the Toyota Production System was developed. Unlike those of us who have books, websites, and training programs in abundance, Toyota engineers took their process of assembly-line manufacture of automobiles and created, in incremental steps, the methodology that’s now known as Lean. It took shape over a long period, as different contributors added their ideas to create a strong “House of Quality” for the Toyota Motor Company.
But – what if these bright people had not come from automotive manufacturing? What if they had come from (for example) healthcare?
I know that this is akin to imagining what the earth would be like today if there were no moon. (Just think – no tides. Different air and water currents. Little shore erosion – no sand? Hard to imagine!)
- What if their initial process studies were not based on repetitive motions that could be adapted to robotic or at least automated mechanisms?
- What if their major source of variation was not the mechanical devices, but the people who provided the process?
- What if their processes were not amenable to on-the-job training, but required differentiation of skill and ability at the level of advanced education and training?
- What if their product was not someone who “ordered” a tangible object, but someone who showed up unannounced with a mysterious problem that couldn’t be solved by just looking at it?
It made me think that if those bright young engineers had worked in healthcare, that what we now call Lean would be vastly different than what was developed by Toyota.
And, as a related thought, it made me wonder what we are doing by applying lean manufacturing principles to healthcare.
Now, I’m not the healthcare equivalent to Eiji Toyoda. Or Shigeo Shingo. Or Genichi Taguchi. Or any of the other brilliant minds that helped to develop the Toyota Production System.
But, am I doing a disservice to my providers and customers, when I try to fit lean manufacturing methods to a highly technically-skilled service environment?
I’ve heard over and over againthat lean can be adapted to any process, anywhere, in any industry or branch of service. I’ve done manylean projects myself, and seen the very tangible benefits that value-stream thinking and creation of flow can produce, along with level loading and consideration of takt time.
But are we only seeing the tip of the iceberg? What further benefits might we see if we developed a “service system” that used tools uniquely intended for service processes, rather than adapting manufacturing tools as best we can?
Just asking!