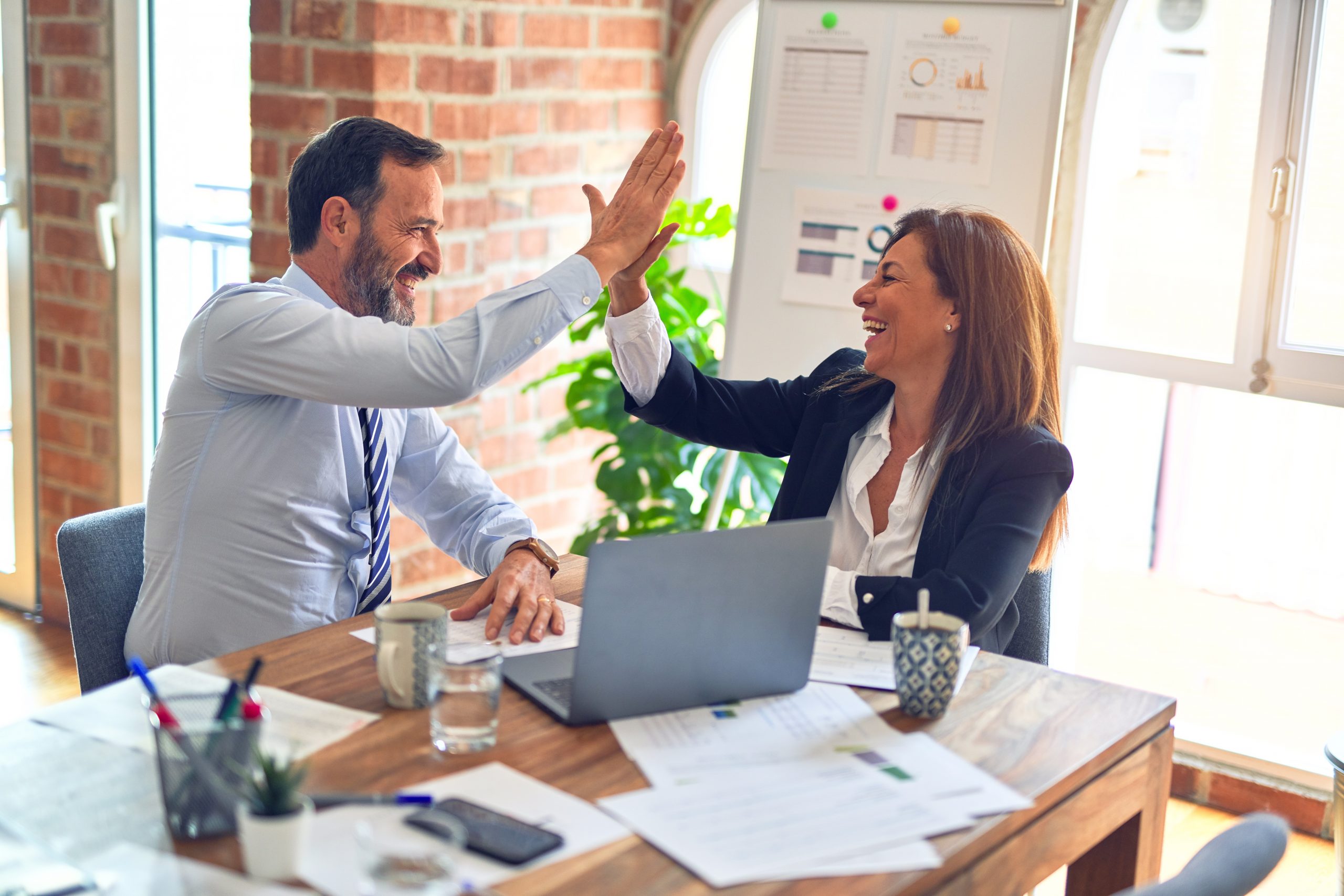
There are many process improvement methodologies – Six Sigma/DMAIC (Define, Measure, Analyze, Improve, Control), Lean, Design for Six Sigma (DFSS) and innovation to name merely a few. But with so many choices, it makes applying an improvement methodology difficult. There are questions such as: “What makes this toolset unique?” and “Which one should I be using?” and “Do I need to use more than one?” The good news is that it is possible to take advantage of the interaction between these methodologies to create better improvement opportunities and deliver better results for the end process.
The improvement methodologies discussed here are DMAIC, Lean Six Sigma, DFSS and innovation (other opportunities may exist but are beyond the scope of this article). To some, the above methods are synonymous. Their names can be used interchangeably to describe a company’s desire for continuous improvement – whether it be with processes or products, in manufacturing or transactional settings. Each of the aforementioned methodologies, however, provides a different toolset that complements the others. This complementary nature provides the practitioner with an enhanced ability to solve many different problem sets.
Strategic or Tactical?
A simple approach for understanding how to integrate multiple methodologies is to look at their adoption on two levels:
- Strategic. The strategic level is directed toward improvements made within the overall lifecycle of a process. It specifically addresses the question of “What methodology should I start with given the current state of my process?”
- Tactical. The tactical level is directed toward short-term improvements or the execution of a particular improvement project. This level addresses how to incorporate various toolsets simultaneously during a single improvement project.
The Strategic Level
Starting from a strategic approach, the overall continuous improvement framework needs to be clear (Figure 1).* It provides an overview of the stages (each of which can be viewed as a project) that a process may go through in its lifecycle. As seen in Figure 1, the continuous improvement framework has six stages –
- Opportunity exploration
- Front-end innovation
- Back-end exploitation (or back-end design)
- Operationalization
- Daily management
- Continuous improvement
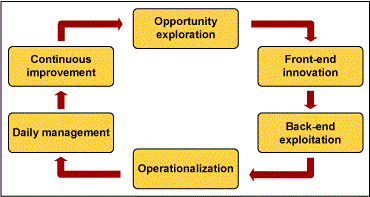
This continuous improvement framework provides an overview for the complete lifecycle of a process. Consequently, it allows practitioners to determine what process improvement methodology to start with by asking the question where on this cycle does a process currently lay?
Figure 2 shows the framework broken down into two categorical areas – existing process optimization and new process development. Pick the appropriate side by asking, “Is there room to optimize the existing process or is a new process needed?”

At a high level, the answer is based on an improvement concept known as the s-curve (Figure 3). The s-curve shows the common progression of processes as they develop over time. Processes are first created, commonly through some form of innovation. They are then improved over time until they hit their entitlement (the best a process can perform over a short-term period), after which they either hold steady or decline. The location that a process fits on the s-curve largely determines which side of the process improvement cycle to start on. If a process has just begun and still has room for growth within its maximum capabilities, then continue with process optimization as seen on the left side of the framework. If a process has peaked, however, and there are steady or declining results despite continued improvement efforts, then new process development (or the right side of the framework) is likely required.

Once it is understood where a process sits, the methodology that should be used becomes clearer. By definition, the Six Sigma and Lean methodologies are intended to optimize an existing process. They reside in the process optimization side of the framework. On the other hand, innovation and DFSS are designed to enable the practitioner to develop new processes with greater process capabilities. They reside on the new process development side of the framework.
Example: Production of Widget A
Consider working for a manufacturing company; the best way to increase production of Widget A needs to be determined. The largest bottleneck in the system has to do specifically with the process for packaging Widget A after it is produced. Looking at the continuous improvement framework, opportunity exploration seems the place to start – determining where the best opportunity for significant improvement is within the existing process. Metrics are then established for the improvement opportunity and four to six months’ worth of historical data (or however much will provide an accurate representation of the capabilities of the process for baseline analysis) is pulled. This establishes a baseline of information to determine where the opportunity for the process stands.
Here, the primary metric – the improvement opportunity for the Widget A packaging problem – was “number of bad wraps (defects) per 10,000 units produced” with two control charts representing possible baseline data (Figure 4). The top chart shows an in-control process, whose average is significantly higher than the best weekly rate(s) it achieved during the baseline period. This chart shows an opportunity for growth within the current process (i.e., at the start of the upward progression on the s-curve). There are two weeks that are each near zero defects, indicating that the process is capable of reaching the ideal state, but only for a short period of time; creating a new process is not necessary. A more efficient means of significantly improving the process is to start on the optimization side of the framework.

Choose the Path
The methodology choice can now be narrowed to either a Six Sigma or Lean improvement approach because both of these methodologies are designed to optimize an existing system.
One way to choose the right direction is by asking, “What is the goal of the improvement?” If the goal is to “reduce variation toward an ideal mean,” then DMAIC is recommended because its toolset is specifically geared toward achieving this end state. If the goal, however, is to eliminate waste and generate flow (commonly done through the use of value analysis) then Lean or Lean Six Sigma (Lean Six Sigma is the implementation of a toolset while Lean is the institutionalization of Lean culture) is the preferred template.
An alternative way of picking which optimization toolset to use starts by asking whether the root cause and/or solution is already known. If the root cause and solution are known, then it is a “just do it” situation. The process owner can usually handle this type of situation without starting an improvement project. If the root cause is known, but the solution is not, then use a Lean approach – specifically, a Kaizen event structure – and consider using innovation at a tactical level. If the root cause is unknown, then the use of DMAIC may be most appropriate since Lean typically relies on the Define, Measure, and Analyze phases of traditional Six Sigma in order to determine the root cause.
Now look at the second set of control charts (Figure 5). They are also in-control, but show a baseline where the average and the entitlement are nearly the same. This indicates the room for optimization is fairly limited (assuming baseline data is truly representative of the process). In this case, the best means for significant (noticeable and lasting) improvement is to create a new process. The existing process is likely at the latter end of the s-curve and already seeing diminishing returns through process optimization. The process has been optimized to obtain consistent results with little variation, but the overall capability of the process (as shown by the mean value) still requires a shift. In cases where the current entitlement is no longer good enough, it is often necessary to develop a new process.

Develop the New Process
Next, it is time to choose how to develop the new process – using innovation or DFSS. The key question is, “Is there already a specific solution for the new process (or a well-defined realm from which the solution resides)?”
If the answer to this is “no,” then innovation is the correct starting point. This is because in order to have a new process, a new solution must be generated – and then its validity for solving the problem must be understood. Both of these are tasks that innovation methods are designed to help achieve.
Follow the Path of Innovation
Innovation can be viewed as a structure that helps teams, organizations and companies think beyond their current paradigms and explore new ways of solving problems. It does this through first understanding what the solution needs to achieve – think of phrases like “jobs to be done” and “outcome expectations.” Then a team can take that understanding and rapidly generate ideas using specialized toolsets to assist with overcoming psychological boundaries (the limits of individual, team’s, or company’s knowledge base and experience). This is followed by development of the solution concept(s) and, finally, testing to validate that the concept achieves the assumed results.
Innovation, in many ways, is not intended to get all the details to integrate the new solution concept into an existing permanent system. It is intended to allow a team to learn fast and cheap. This mindset creates a new solution foundation that can later be strengthened and made more robust for long-term sustainment through tools such as DFSS. (These problems can either start as a new product development required to fit an external customer’s unmet need, or can be a new process development needed to fit an internal customer’s unmet requirements in the form of a poor or underachieving current process. In either case, the follow-on step to innovation is back-end design.)
DFSS for Refinement of Solution Concept
If there is already a specific solution for the new process, then back-end design or DFSS is the first step. The reasoning is simple. If there is already a specific solution (one assumed or proven to be feasible), then it is not necessary need to go through the time and effort associated with front-end innovation. Rather, if an organization starts with an accepted solution concept then the focus is to rapidly evaluate, analyze and strengthen a solution in order to build quality into the design. DFSS provides a robust process for achieving this before the process is put into action.
As with innovation, there are several different methods or roadmaps for going through DFSS, but a common one is DMADV (Define, Measure, Analyze, Design and Verify). DFSS is valuable because it provides structure to solution refinement and development. For example, there are some people who think in details. They naturally generate many what-if scenarios of possible design failures, create contingency or alternatives that mitigate this risk, use Pugh matrices to compare design options, etc. Most people, however, do not. Most people just figure it out afterward when the new process is unveiled and the failures in the design start to appear (naturally driving DMAIC or other process optimization work). The toolkit and model of DFSS is designed to force the generation and evaluation of critical details often overlooked in new process development. Most importantly, it also ties them back to the voice of the customer (VOC).
At a high level, DFSS starts by directing the understanding of what the customer cares about (Define phase). It then determines what is needed in order to quantify that understanding (Measure phase), and evaluates how well the design meets that customer need or what gaps exist (Analyze phase). DFSS then generates and implements solutions for filling those gaps (Design phase), and is followed by a confirmation that the solution implemented performed as expected (Verify phase).
By starting with DFSS, a new process will ideally begin much further along in the s-curve diagram. This results in fewer process optimization efforts down the road and more immediate improvement to an overall process performance.
Continuous Improvement Framework Informs Strategic Level
Figure 6 summarizes the strategic-level approach with a combined overview of the continuous improvement framework. By understanding where a company or process is in the framework, it is possible to gain critical insight into which methodology is the best first step in getting to the desired improvements. In this same light, the continuous improvement framework also helps with the strategic understanding of what the next step for improvement will look like for the process. It is important to note the direction of the arrows on the framework. They rotate clockwise because no matter where an organization starts the process, the continuous improvement development steps move in that direction.

For example, if starting with innovation, a team is creating potential solutions for a new process. The front-end innovation step ends by demonstrating that the solution(s) created is feasible for achieving the process goals. The next step is to move into back-end design or DFSS, which allows for the integrations of a newly developed process solution into an existing process environment. For example, incorporating a new packaging design into the overall process of making Widget A. Once DFSS is complete and the process is in place, the next step is to take it through the commissioning or operationalization phase and into daily management where the process owners are comfortable using the new process on a regular basis.
After the daily management step, the process is at the beginning point of its new s-curve. In most cases, there will now be room for improvement within its new (higher) capabilities. As such, a group moves into the continuous improvement step and process optimization techniques are used to continue pushing the performance of the new process. After a process optimization project is complete, a team comes back around to opportunity exploration – again examining the process in place and determining where it lies in terms of capabilities. If the process still has room for optimization, it is time to re-engage the continuous improvement step and repeat this cycle until the process looks like the second set of control charts (Figure 5). When it does, new process development is initiated and a new process lifecycle is established.
The Tactical Level
As discussed previously, the tactical level focuses on short-term process improvement. It specifically relates to a project that is completed within a single step of the continuous improvement framework. These projects are the heartbeat of any good process improvement program. The overall quality of a process improvement is often only as good as the quality outcomes derived from the tactical gains. Consequently, understanding how different improvement methodologies can work together within the structure of a single project can serve to enhance the achievements of both a project and a program.
To illustrate how this approach works, refer back to the Widget A packaging process example. Looking initially at where to begin the process improvement, baseline data was collected over a four-month period and the primary metric resembled the control chart found in Figure 4.
This control chart is in control, but has a wide range between the entitlement and the baseline average. Because of this, the team decides that the best way to attack the opportunity is through a process optimization methodology. The group selects DMAIC because the root cause of the systemic error is yet unknown.
DMAIC: Root Cause Analysis and Identification
The primary focus of DMAIC is on root cause analysis and identification; DMAIC is what is used when it is unclear what is wrong with a process. While DMAIC is powerful for root cause analysis, it also has somewhat limited means of solution generation. If the solution is not something that can be modeled or optimized within the current paradigm, usually through some form of design of experiments (DOE), practitioners can be left looking for solution options. This is where the knowledge of other improvement methodologies becomes especially useful.
Figure 7 illustrates a simple way to integrate multiple toolsets in the same project by leveraging each of their strengths to the advance of said project. As the diagram shows, start with the DMAIC tools. These allow for root cause identification and set a solid foundation for what problems will need to be solved. If done properly, the project leader will then be able to select from a number of different methodologies or toolsets to generate solutions as a team moves into the Improve phase, some of which are designed to do so better than DMAIC in certain applications.
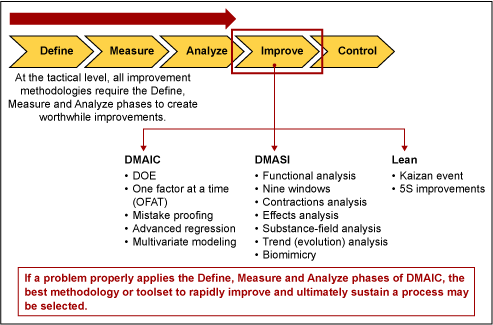
For example, as shown in Figure 7, DMAIC has a number of different tools available to help generate solutions. There may be times, however, when they are not able to do so as effectively as is needed. One case is when select subprocesses are simply not capable of meeting an overall goal; using tools to optimize those subprocesses (like DOE) will not be sufficient. Leverage a more robust solution generation toolset such as the DMASI (Define, Measure, Abstract, Solve, Implement) model.
DMASI: Solution-generation Toolset
DMASI, in many ways, is the polar opposite to DMAIC. Whereas DMAIC’s strengths lie in root cause analysis, DMASI is primarily a solution-generation toolset. It has some analysis tools, such as function analysis, but the tools in DMAIC are limited in their ability to identify the root cause issues and geared more toward identifying different solution areas within an already-known problem set. For solution generation, however, DMASI has a multitude of different tools such as nine windows, contradiction analysis and su-field analysis. These are all designed to enable the generation of solutions outside of existing paradigms, or the limitations of a team’s collective experience and knowledge base. Simply put, the DMASI model is what is used when it is clear what is wrong, but it is unclear how to solve that problem. This makes it a perfect fit to use in conjunction with DMAIC when new subprocesses need to be created in order to achieve the performance goals of a larger process.
Lean Six Sigma Toolset
In a similar fashion to DMASI, the LSS toolset can also be useful for solution generation after root cause identification is complete. Lean is a particularly effective toolset when several different forms of waste exist within the current process or when there are deficiencies in areas that do not allow other solutions to provide full benefit.
For example, when analyzing the packaging problem, it may be that the sources of the defects are the result of several systematic mechanical equipment failures. To compound this, the equipment failures exist because down day operations are not efficient and require 50 percent more time than required. This, consequently, does not permit all of the identified potential equipment failures to be fixed before Widget A goes out. The excess time could be the result of mechanics having to wait for power to be cut before they can safely work on an area, having to walk numerous times to the storage room during jobs to get parts, time spent searching for tools because they are not in a set location or not having standard work plans for conducting each job. When these types of problems exist, the DMAIC toolset again becomes largely ineffective and the incorporation of Lean tools such as 5S and Kaizen are ideal.
Once improvements are implemented, refer back to the Control phase tools of DMAIC. This ensures that any solutions generated (whether from the DMAIC, DMASI or Lean toolsets) are properly tracked with support processes created so that their results hold over the long-term. This final step completes the integration of multiple methodologies at a tactical level and allows gains to be built upon as a team moves through the continuous improvement framework.
Summary
The incorporation of multiple methodologies can provide significant enhancements to a process improvement program, whether it is a Six Sigma-, Lean- or innovation-based initiative. The key is to leverage the strengths of each methodology and apply them toward the framework of the needs of the process. Process improvement methods were made to complement one another, not compete. With this in mind, the possibilities for improvement in an organization will expand.
* Dr. Phil Samuel is the chief innovation officer for BMGI. Though not referenced directly in the text, the “continuous improvement framework” referred to in this article was derived in concept from Dr. Samuel’s co-authored book entitled The Innovator’s Toolkit along with other teachings from his various courses and seminars.