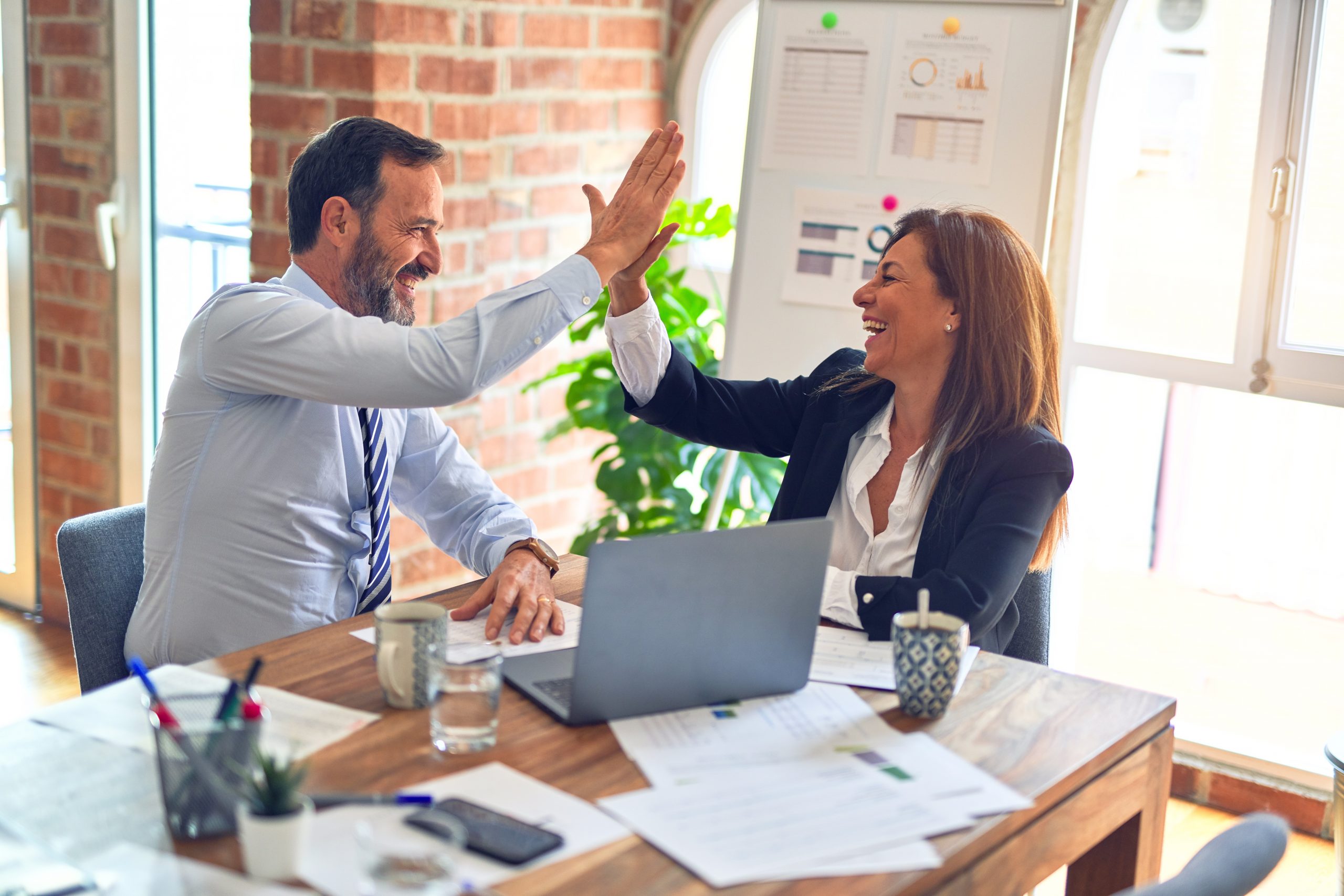
Tri-State Industries was founded by Don Keller in 1980 as a manufacturer of industrial pipe guides and slides. In the 1990s, the company adopted the principles and practices of Lean manufacturing.
Since its founding, Tri-State has grown to three product lines with a fourth in process. Along with pipe guides, Tri-State is a manufacturer of industrial trailers for two Fortune 500 original equipment manufacturers (OEMs) and also is a component supplier for the rail car industry. Its newest division, Tri-State Automation, is putting lessons learned within Tri-State’s own manufacturing facility to use for others in the automation of welding and material handling using robotics.
Improving the Trailer Product Line
As is the case with any Lean organization, Tri-State works to keep the lessons of the methodology fresh – continuous improvement is a journey rather than a stand-alone event. Such is the case for the trailer product line, which represents one of the more complex elements of Tri-State’s business. Tri-State manufactures an estimated 4,000 trailers each year with 95 percent of volume represented by six models. The remaining 5 percent of the business is comprised of several specialty models. Customers expect delivery within two weeks of order placement and often sooner. Considering the challenges of mix, volume spikes and aggressive lead time expectations, Tri-State maintains excellent supplier ratings including a 12-month perfect supplier scorecard for quality and delivery with one of its key OEMs.
So why the need to take continuous improvement to the next level for trailers at Tri-State? While the performance results remain strong, the effort to maintain such strong performance is not as systematic as desired. There are occasional material expedites, gaps in standard work, and both 5S (sort, straighten, shine, standardize, sustain) and safety performance remain opportunities for improvement. The trailers team has gone to work in early 2014 to review this value stream for improvement. Many of the structural process improvements will be applied to the other business units as well.
Starting with Safety
As a starting point, standard work has been developed for Tri-State’s safety process. This process outlines all of the requirements for an annual program that consists of training, an updated first aid management process and performance metrics that are part of every team member’s merit objectives.
The team has been on a streak of work days without lost time due to injury and is working to keep this streak ongoing. An updated 6S (the usual 5S plus safety) process was initiated in April 2014. This process is simpler than a traditional 1-to-5 rating scale for each element; it deploys a red-yellow-green (poor-average-outstanding) rating system for each category. Safety standard work scorecards for each business unit reinforce the need for daily tracking of safety performance including first aid occurrences, timely completion of accident reporting and implementation of monthly prevention-oriented job hazard analyses in Figure 1.

Seasonal Mix
The next challenge for Tri-State was to simplify the management and execution of the seasonal mix elements of the trailer business. The team began by implementing a new visual master schedule. After several attempts, the team concluded the schedule could only be managed in two-week buckets due to the dynamic nature of customer requirements. Review of the master schedule revealed patterns and trends which supplemented the development of the future state map.
The current state process for component parts was mapped, including quantifying the baseline production rates for individual components. This data will become important during future state process design as “make” quantities are “smart”-sized against market demand trends.
Development of the future state map noted three internal shipping destinations for trailers or trailer components within the facility: a kitted trailer line, a final assembled trailer line and a component kit line. These shipping destinations are supported by a fabrication and welding operation adjacent to shipping destinations. Personnel are not shared between the fabrication and shipping groups but are shared across the three shipping destinations. Each shipping area competes for some mix of common components, however, which often results in conflicts. The process lacked a systematic method for having the visibility for part mix and then allocating to each of the three areas accordingly.
The team performed a market rate of demand (MRD) analysis (or forecast) based on the past four years of sales data. Takt times for each of the three consumption points were developed based on peak seasonality trends. The MRD analysis indicated the peak season can last more than four months each year.
Upgrading Demand-based Pull System
The team then identified the need to upgrade the existing demand-based pull system. The legacy Kanban system used cards as the replenishment signal system. Like many Kanban card-based systems, a one-size-fits-all approach was initially deployed in the spirit of standard work and consistency. While initial results were great, over time the team learned one signal method was not always optimal for each demand-based pull part family.
The main issues facing the legacy Kanban system were lot sizing (too many or too few) and a lack of prioritization processes for different make items manufactured in the same cell or by the same people. In addition, variances in part processing created challenges. For example, some parts come directly from a paint line to assembly, while others require secondary processing. The legacy system had difficulties dealing with these differences and had essentially been abandoned by supervision; a manual system had taken over. The three internal shipping destinations often competed for like components, leading to material shortages and bad feelings within the team.
The new material pull system utilizes returnable carts (as shown in Figure 2), which are dedicated to each of the three end-shipping destinations. Upon consumption, each cart is returned to the appropriate “make” department in a dedicated swim-lane location to facilitate consumption-based replenishment. Cart sizing was determined based on safety considerations, MRD requirements, space constraints and make-part processing times. Multiple carts are used so the system can incrementally replenish and be throttled up or down depending on seasonality. Part families are kitted on the same cart when it makes sense to ensure complete kits for families of parts always remain whole.

Enabling Better Teamwork
This process is being developed by a cross-functional team of senior managers, project engineers, supervision and shop floor team members. The team is starting with a series of four parts and will move to the balance of end items incrementally. The goal is to have the right parts at the right place at the right time – nothing else. A tremendous side benefit of this system is the returnable carts that serve as standard work mechanisms. Cart sizes are in quantities that represent one half or full shift increments. These quantities aligned with MRD requirements with the first parts implemented in the new system. Once “make” items are mastered, the team will move on to the challenges faced by the supply chain.
Another objective of this improvement initiative is to greatly simplify the work and get supervisors out of fire-fighting mode and deeper into process improvement mode. Team metrics boards (as shown in Figure 3) have been created, and weekly Gemba walks have begun focusing on the questions: “How is your business unit performing?” and “How is the team working to improve the business as compared to last week?” All of these efforts are in support of customer initiatives to reduce cost within their own supply chain – of which several Tri-State customers have rigorous and formally established and measured annual expectations.

Harmonic Improvement
Tri-State places a strong emphasis on not only what work is being accomplished but also how the work is being accomplished. The Tri-State quarterly bonus system was amended this year to place a sizeable emphasis on how team members work together in a collaborative spirit. This element of the bonus system is known as the “harmony factor.”
And no Lean journey would be complete without recognition and celebration. Each month that Tri-State meets key business objectives, the team celebrates with a Friday afternoon shutdown complete with creative luncheon events. The results secured in pursuit of savings generated through Lean initiatives keep Tri-State strong and well positioned for growth.