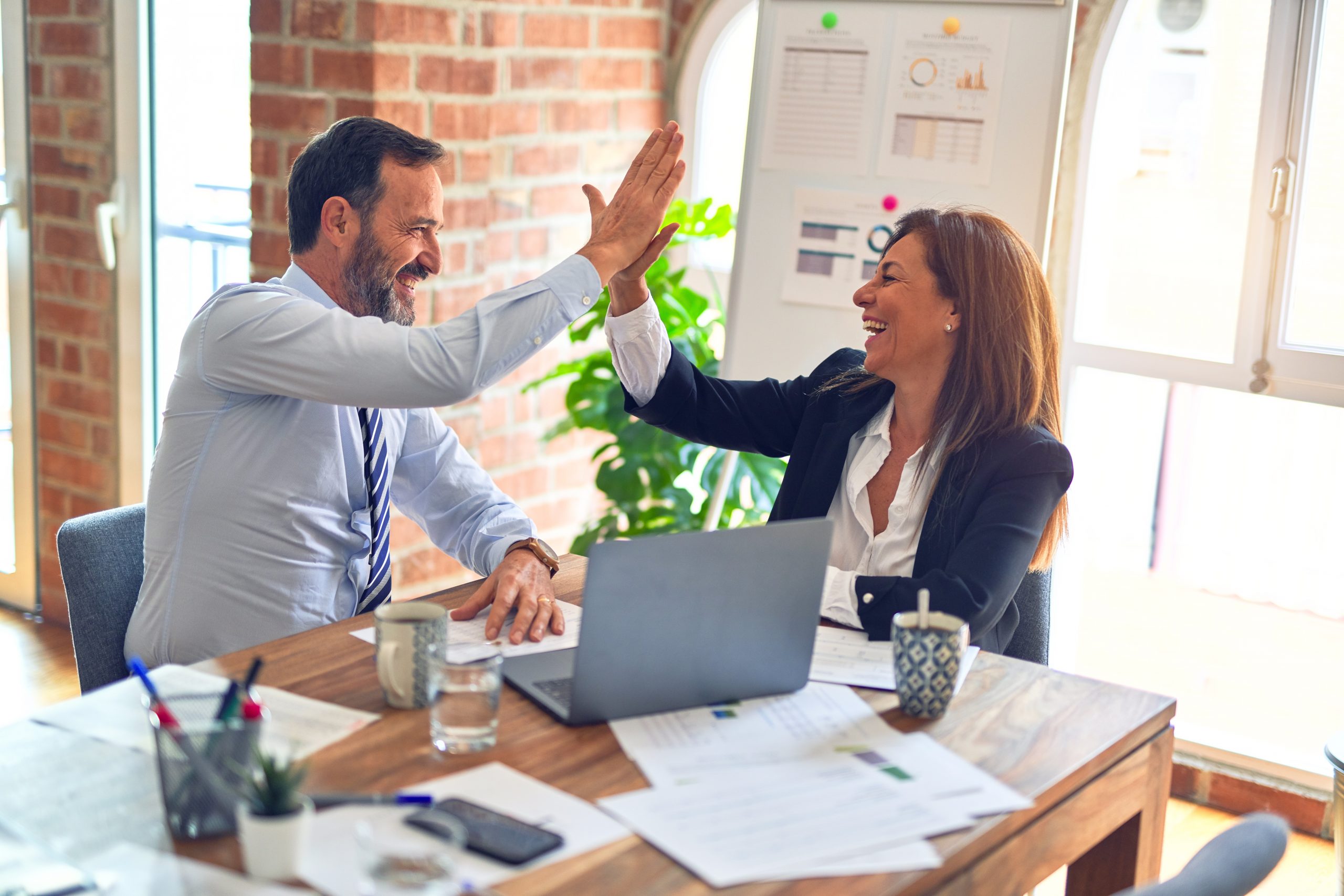
Message: 16306
Posted by: Eric
Posted on: Thursday, 25th July 2002
My company is actively deploying Lean Mfg principles. To this point, we have not been heavily involved with Six Sigma. Although recently our Customers have heightened our awareness of Six Sigma by asking/ requiring us to participate in their Six Sigma efforts – including becoming certified.
Side-by-Side there appears to be a relationship between Lean and Six Sigma. But, I’m really not sure of the SPECIFIC differences/ benefits of each effort? Which is why I’m posting this note.
I see Lean to be more Mfg/ Operations focused – although the principles can be applied across the company. I see Six Sigma to be more focused on “white collar” processes, although it too can be applied across the company. Six Sigma feels like the right approach. It also feels like it NEEDS to co-exist with Lean; but, not replace Lean or vice versa.
Which approach is better? Do you need both? How should I respond to my management that want to know the hardline differences/ benefits?
Message: 16310
Posted by: Erik L
Posted on: Thursday, 25th July 2002
Eric,
Lean or Six Sigma? Six Sigma or Lean? I have seen this endless debate about which should be used first or which should replace the other. In my opinion, you need both working in unison. I’ve been involved with past implementations of Six Sigma that strove to develop Belts specialized in the respective disciplines. I believe it resulted in sub-optimal project results and resulted in mass confusion and turf wars between the disciplines. SS BBs would go overboard looking to use statisitical sledgehemmers when there was a practical solution out there with minimal effort and/or a simpler analysis-albeit this was being driven by the requirements for certification, but that’s another discussion. Lean Belts would work a project and leave it sub-optimally improved and do little to attack variability. I don’t know if it was intentionally communicated, but there was this feeling that Lean was more “simple” and that it was primarily for the grunt on the line while Six Sigma was more for the professional engineering ranks. The two methodologies did seem at opposite ends of the normal curve. Yes, ideally MBBs were to have oversight for the conduct of the project and look at the optimal time to match SS BB assets with Lean assets. Reality never quite worked that way. Each community closed on its self and would not support the other or they committed themselves so much that they did not have the bandwidth to support the other. Belts need to be trained in both arms to solve process issues. It extends the training pipeline for a SS BB by about 1-2 weeks to incorporate Lean, but the ROI for that minimal amount of time is significant. If it doesn’t happen, and you’re indoctrinated in a certain discipline, that’s the only thought process that you can use to solve a problem. I came up as a SS BB and MBB, and of course initially thought that I had the panacea for all of the process ills of the world, it wasn’t long before I matured my vision and incorporated Lean into my tool box. I look at is a responsibility that I have to those that I mentor and to the Process Owners that I impact with my projects. I always communicate to the GBs and BBs that I mentor to use a Practical, Graphical, and Analytical (PGA) approach to the DMAIC thought process. Embodied within that progression of tool application is the applicability of Lean tools.
Sometimes the issues will be very prevalent and easy to see and one or the other methodologies is obviously the choice. Other times it requires a thorough baseline assessment of the key processes that are driving the process. Lean is good at this process and dropping the waterline so that the true landscape of projects is obvious to all. It all comes back to the ubiquitous phrase, ‘it depends…’
If you’ve been implementing Lean that’s great. But that’s only going to allow you to harvest a fraction of the fruit that’s higher up the sigma tree. Six Sigma will take you to the next level and then DFSS will close the final gap. If you’ve leaned your processes, understand the key processes that drive your business, attached balanced scorecards, have management support, and a clear communication plan, it sounds like you’re ready to take off. Hope this has helped.
Regards,
Erik
Message: 16316
Posted by: Ron
Posted on: Thursday, 25th July 2002
The debate is purely pedantic. Lean has a tool set that is geared to improve process flow. Six Sigma was designed to specifically focus on process variation.
As someone who has been certified in both disciplines I prefer to think of Lean Sigma as a complete toolkit. I use the tool interchangably as I approach a process. Instead of a process map I use a Value Stream Map it tells me more.
Once you lean out a process you won’t have to wait long until you find the sources of variation.
Don’t separate them combine them. The only people that are not combining these two important tool sets are consultants – both internal and external as a territorial battle.
Message: 16400
Posted by: Mike Carnell
Posted on: Monday, 29th July 2002
Eric,
For some reason people have got it locked into there heads they can only do one initiative at a time, they like to use the term “my plate is full” which when it comes to interpreting it does not mean anything. Something is full but it isn’t a plate. If they can only do one thing then you need to roll some people over because there are several people out there who can actually focus on more than one thing at a time.
The two are complimentary and synergistic. Anyone who belives that Lean fixes everything has never run into a real complex problem and anyone who has done a poorly selected SS project and not had to deal with workplace organization and standardized work just didn’t realize they were doing it. The two were launched together at Motorola in 88 and Allied in 95. GE did DFT before it did SS and it helped tremendously.
There are books available on the integration. Several groups would like you to believe it is their idea and it is new and they invented it. It isn’t new. It has been done for at least 12 years.
Watch the movie “Tin Cup.” There is a scene where Kevin Costner breaks all his clubs except a 7 iron. His caddy (Cheech) walks off and Costner wins the tournament with just a 7 iron. When he brags about it to Don Johnson rather than be impressed he just asks him “Why.” Best analogy I have ever seen to trying to fix something when a person is so stricken with “Intellectual Bigotry” that they refuse to be intelligent in their deployment. You are allowed to use more than one club (tool) and since it isn’t tournament play there isn’t a limit on the number of clubs you can carry in your bag – you can actually bring a couple bags. At the end of the day the CEO is not going to ask to see what tool you used to fix the problem. They only care about whether it got fixed.
Nobody working for Womack is going to call you up and place you on a pedistal for being a pure Lean guy. Nobody at ASQ will reward you for being a pure SS guy. Your customer is the company you work for. You owe them the most efficient and effective deployment they can get. That methodology has been through the integrated approach not through dedication to some set of tools.
Good luck.
Message: 17126
Posted by: Owen
Posted on: Monday, 19th August 2002
Eric,
The advice you have been given is sound. I’m a bit suspicious about the term “Lean Sigma”. It seems another slick way of the vast army of Snake-oil salesmen to seaprate you from your wedge of cash.
I see no difference between Lean and 6-Sigma. They share the same parents. I see Lean as a powerful management philosophy with 6-Sigma as a good tool. Unfortunately most people’s appreciation of Lean extends only to the well-known bag of tools (there are some which are obscure).
Having studied Lean for sometime, I’m convinced you cannot implement Lean and sustain the gains unless management are willing to change both their attitudes and skills. The organisation needs to move from a traditional bureaucracy to becoming a Learning Organisation which values its human capital. If this is not happening Lean will fail in the long run.
The myth that Lean focuses on flow and 6-Sigma on variation is not quite correct. Take a look at any Lean tool (kanban, error proofing, work balancing, 5S, etc.). They all have one thing in common: differentiating the abnormal from the normal, and making it visible so it can be addressed immediately. To me that is attacking variation.
There was a suggestion that Lean was for “grunts” and 6-Sigma for the “white collar”. That may be the case, but if it is so, I fear we will travel back in time to the days of Scientific Management separating the “thinkers” from the “doers”. The whole thrust of Lean is to break down that division, and that is usually not appreciated by those considering it implementation. To implement any Lean tool, you must commit to learning from the experience and using the brains of those on the floor. Most automotive manufacturers now have andon (or process-control boards) which were pioneered by Toyota. At Toyota, the line worker has an obligation to call for help or even stop the line if there is a problem because Toyota sees each of these incidents as a learning opportunity. This fact is one that has been hard to swallow by the other manufacturers (culture is tough to change), and so the line worker is asked to pull the chord only if the problem is considered to be serious. We have 100-year traditions of not asking line workers for their opinions, and now we are asking them to make decisions about problem severity?
Toyota hates variation with a passion only matched by the best 6-Sigma organisations, probably. They are also obsessive about standard work (defined and refined by the people who do the job, not consultants). They are obsessive about continuous improvement and see this as the third apex of a virtuous triangle (the others being people and standards). And this leads to my concern: how can we measure variation when our “white collars” see themselves as “knowledge workers” and do not have standard operations? Most transactional or business Black Belts struggle.
As with Lean, 6-Sigma will not be self sustaining unless the organisation values its Green Belts and encourages them to improve continuously. Black Belts alone won’t hack it.
Hope this helps.
Message: 17130
Posted by: Ron
Posted on: Monday, 19th August 2002
Huge difference between “lean Tools” and Six Sigma tools.
Lean = Improved process flow
Six Sigma = Reduced process variaiton
Lean Sigma means to merge these two separate disciplines into a single entity. Lean Sigma is the next logical step in the continuous improvment journey.
Message: 17222
Posted by: Owen
Posted on: Thursday, 22nd August 2002
With due respect, I’m not sure how an organisation can improve flow without tackling variation.
From my research, Toyota seems to have a visceral understanding of variation. They have DPMO’s for which others would sell their grannies. And through their coaching their suppliers are either not far behind or disappear.
My concern is that we have way too many snake-oil salesmen trying to sell industry the latest miracle cure. But what is sad is the number of gullible managers who buy just about anything rather than think for themselves. In about six months time either Business Week or HBR or the National Enquirer will publish an article titled “Beyond Lean Sigma”. It may signify significant advances in thinking or it may be another scam, but it will confuse and frustrate hard-working people and may cause another strategic detour: “Drop Lean/6-Sigma and start BrandX!”
Each of these tools/ideas/methodologies/philosophies only has value if it harnesses the intelligence of the whole organisation, not just the annointed few. That is the essence of Lean, not kanban, error proofing, JIT, 5S, Visual Factory, …
Message: 19787
Posted by: Mark Siem
Posted on: Thursday, 31st October 2002
Folks,
I work at a Scientific software company and we are considering whether or not to undertake either Six Sigma, Lean, or some combination. I am new to this area, but have experience in ISO 9002 certification. Since SS programs were originally designed for manufacturing environments I was wondering if any of you could comment about applicability to a software company or point in a direction to conduct a solid evaluation. Thanks for the help.
Mark
Message: 19797
Posted by: Mike Carnell
Posted on: Thursday, 31st October 2002
Mark,
You have now bought into the two of the biggest crap sandwichs being sold today. Six Sigma at Motorola was “Six Sigma in everything we do” since 1988 and they do a fair amount of software.
The second sandwich is that you need to choose between SS and Lean. We deployed Lean (then called Cycle Time reduction – 50% per year) at the same time we did SS. Allied concurrent deployments. GE did DFT before we did the SS deployment.
We have seen the “we’re different” thing for quite a while on this site. Read Demings “deadly diseases and obstacles.”
Good luck.
Message: 19805
Posted by: John Flaig
Posted on: Thursday, 31st October 2002
Eric,
There was a nice article in March 2002 issue of Quality Progress comparing Lean, Six Sigma, and the Theory of Constraints.
Regards,
John J. Flaig, Ph.D.
Applied Technology (e-AT-USA.com)
Message: 61189
Posted by: James D
Posted on: Thursday, 16th December 2004
Hi
Interested by your comment towards the end – that knowledge workers claim not to have “standard operations”. If you take Drucker’s definition of a knowledge worker (someone who has to define their work before they can do it), then I guess you have to concede that you can’t specify in advance what output is going to be produced in any given context – the deciding has to be done first.
But all that aside, knowledge workers most decidedly do have “standard operations” – they’re found at the level of physical actions, not outcomes. The “standard operations” of a knowledge worker are things like “pick up phone”, “reply to email”, “schedule meeting”, “draft agenda”.
I coach knowledge workers in improving their productivity. One of the key things we get across is to distinguish between the outcome (which is often a sequence of “next actions” which cannot reliably be predicted more than one or two steps ahead) and the very next action. Both have to be decided as soon as possible after anything that could be new work shows up. Deciding on the next physical action has the effect of “intelligently dumbing down” the work and tends to cut through procrastination. We also teach people to “do it now” if the next action is something that can be done in under 2 minutes (assuming they’re ever going to do it at all).
The combined effect of this is usually that organisational as well as personal throughput get faster and smoother. A bit like white-collar “lean” manufacturing (to stretch a metaphor).
You seem to see a link between the lack of standard operations for white-collar workers and a difficulty in measuring variation (though I’m not sure which variations you have in mind here). I’m interested in how that might relate to what we see happening in our coaching process. Can you explain more about what you believe that link is – ie how does a lack of standard operations for white collar workers prevent the measurement of variation?
J
Message: 80117
Posted by: StevenK
Posted on: Monday, 26th September 2005
I have that article of Lean vs Sigma vs TOC. It is very resourceful. I’ve been trained in Six Sigma & Lean tools. But it is more than just that. It comes down to using Both Lean & Six Sigma. Lean is very visual in mapping out the value stream, setting things in order with 5S, and taking control of your materials. Start off in Lean & let Six Sigma follow. The organization needs to think long-term results, as short-term you’re cleaning out the ‘garbage’.
Six Sigma really helps develop any understanding of process complexity and an importance of ‘preventive’ in not allowing defects to occur. DMAIC is the backbone of Six Sigma.
I’ve benefited from both and they can be used throughout the organization. You need discipline, commitment, and teamwork. Realize your employees are your greatest asset.
Hope this helps,
Steven
Best to all,
Charles H.
Message: 82824
Posted by: Charles H
Posted on: Wednesday, 9th November 2005
Sorry, the link I posted in the previous message didn’t work when pasted into the search engine. To find the article, go to the LEI website, log in, click on “Library” and then run a search for “Nave” and it should come up in the website search results
Best of luck,
Charles H.
Message: 82828
Posted by: StevenK
Posted on: Wednesday, 9th November 2005
I’ve sent an email to the isixsigma (forum-downloads). Hopefully they will post it soon. If not soon, then I would need an email address to send it to.
Also, here is a great link to http://www.asq.org on a pdf about Lean & SixSigma.
http://www.asq.org/pub/qualityprogress/past/0403/qp0403smith.pdf
Message: 82831
Posted by: Dave Nave
Posted on: Wednesday, 9th November 2005
ASQ owns exclusive copyrights to the article I wrote. The full title and master location are:
“How to Compare Six Sigma, Lean and the Theory of Constraints: A Framework for choosing what’s best for your organization” …Dave Nave, Quality Progress, March 2002, Volume 35 Number 3, American Society for Quality
http://www.asq.org/pub/qualityprogress/past/0302/qp0302nave.pdf
I am glad this article is of interest.
Dave
Message: 82851
Posted by: Charles Hannabarger
Posted on: Wednesday, 9th November 2005
Thanks, Dave. I knew the ASQ owns it, but Womack somehow got them to agree to let him put it on his website as a pdf download. As always, it is for personal use only.
Take care,
Charles H.
Message: 82854
Posted by: Dog Sxxt
Posted on: Wednesday, 9th November 2005
I do not understand why TOC is separated as a standalone subject.
Any IE either trained in the western countries or Japan shall know how to identify bottleneck or some geniues like Goldrat called it a constraint. TOC is just a subset in IE or lean and it does not qualify to be put side by side with six sigma and lean.
Message: 83857
Posted by: Kent
Posted on: Thursday, 24th November 2005
When we did not have enough Lean-Sigma folks trained to do the “Lean Fits Everywhere – Do Lean Everywhere” approach some consultants wanted us to take, we used Theory of Constraints to help us focus and prioritize those Lean efforts to get more capacity out of the constraint. One time the constraint was actually the fact that it took too long to do a particular process. We held a rapid improvement event to improve the process by only doing what provided value. When an organization matures to the point that they can let loose of the emotional ties to particular methods and just do the right thing to improve the bottom line it is possible to get 25-40% step jumps in performance. Some things done to re-evaluate the current business rules that have developed over time can also assist in maintaining the higher level of flow. Such methods as going from monthly to daily reporting, using buffers to ensure the constraint is never starved for work, and making sure that the sales folks are coming up to speed with new offers to improve plant throughput when the hidden capacity is unveiled.
A seasoned Certified Quality Manager does not place emphasis on the category of changes being pursued for the sake of whether it is Lean or Six-sigma, but logically moves his team forward using a systems approach to remove waste, improve flow, and increase throughput against conditions of variation and uncertainty. When the constraint is in the market, few beneficial improvements can trigger a step jump to help the bottom line, but a company having developed a ‘Solution For Sales’ is poised to advance in market share. When faster flow is combined with better reliability in schedule and scope, new opportunities to please the customer rise, ensuring that both the company and the workers prosper as a result of the process changes. So it is the holistic approach of system process improvement that brings the fastest return on investment and improved camaraderie among the employees of all departments. Solve a core conflict or root problem and the people will love you; push a new methodology because corporate says to do so and you will be despised. May those of you who understand how to solve real problems achieve multiple successes as you seek to make a better world.
Message: 83921
Posted by: Simon
Posted on: Saturday, 26th November 2005
In a word:
“Lean is Art.
Six sigma is Science”
Simon
Message: 83927
Posted by: Stan
Posted on: Saturday, 26th November 2005
That’s more than a word and it’s BS.
Lean is the foundation and the stability.
Does it surprise you that companies like Toyota achieve better results than the Six Sigma companies?
Message: 83928
Posted by: Stan
Posted on: Saturday, 26th November 2005
The consultants are wrong and TOC is just what you described – a prioritization tool.
Message: 86786
Posted by: Bert
Posted on: Wednesday, 18th January 2006
This is a very Interesting thread. I am a practicing TOC Consultant and for that I will apologies up front. Please don’t hold it against me too much. If it helps, I offer that I am also a graduate of the fine IE program at the University of Michigan.
What prompted me to comment on this thread is the following question; “I do not understand why TOC is separated as a standalone subject” posed by “Dog Sxxt.” On the surface, this question is nothing but a genuine appeal for clarity, an attempt to understand better. On the other hand, it also reminded me of my initial reaction when I was introduced to Lean Manufacturing at Boeing. For the longest while, I had a difficult time identifying myself as a Lean Practitioner.
I had never heard the term Lean at UofM and it seemed like so much less than the breadth and depth of what the Industrial Engineering Profession had to offer a company. It didn’t help that most of what I was learning came across as an academically inferior version of what I had been exposed to at UofM. It was beyond me why companies where jumping on this Lean bandwagon while dismissing IE practices as the root cause for inefficiencies.
When the Six Sigma program was later introduced to Boeing I had my hands full with TOC so I didn’t pursue the Six Sigma certification opportunities. However, I bought the books to satisfy myself that not much had changed since college. To my surprise, going through the material for a second time and after some real world experience I was better able to comprehend and internalize the material.
I first discovered TOC at the same time I received my lean training. For some reason, I found TOC more appealing at the time and thought it was a good compliment to the material I had learned in IE. However, when I tried to get my professors back at UofM interested, I discovered a very strong anti-TOC / anti-Goldratt sentiment through-out the department. The Japan Institute established by funding from the Big Three auto manufacturers had become the single biggest private-sector initiative in the department.
The interesting thing is that one of the main reasons given at the time for why TOC couldn’t find a place at such a prestigious institution was that TOC wasn’t academically rigorous enough. It tended to oversimplify the challenges of managing a company (as opposed to Lean – which had clearly shown that real improvements can only come after a long and difficult journey – my words, not theirs.) Most of the professors by this time had jumped en mass onto the Lean bandwagon. Curriculums were updated to include Lean language in practically every basic IE course. Less than five years had elapsed since I had graduated. Needless to say, I was more than just a little confused at the time. Recently, it has become more acceptable to claim TOC as a subset of Lean. Ironic, isn’t it?
Years and many implementations later, I am thankful for the different perspectives that exist today. Had I known I was preparing for the awesome responsibility of helping to save companies from bankruptcy or surviving the pressures of global competition, I might have paid more attention to each learning opportunity.
So, to the comment “I do not understand why TOC is separated as a standalone subject. “ I respectfully submit that you are on the right track. If I may quote Covey, “seek first to understand…” In the end, you may decide that you wasted your time, but on the other hand, you too may discover something beneficial to you or your customers.
Bert
Message: 99024
Posted by: Peter
Posted on: Thursday, 17th August 2006
I know the thread from Simon “LEAN is Art” and “Six Sigma is Science” is Nov05…its just I couldnt help myself to add to it even it is almost a year on – it brought such a feeling of WOW! somebody actually managed to hit the nail on the head. CONGRATS! if there was a price I would give it to you Sir Simon! Allow me to embroil further just a little! “LEAN is Science in Art Form” – probably the reason why so many companies fail to copy it. It CAN’T be copied! Its an art form. You have to become an ARTIST, not just you, everybody in the company, not just any artist, but an ARTIST, like Rembrandt. Toyota is a painting like “Die Nagwag” from Rembrandt, and it gets worse folks! its evolving, it gets better and better (almost like us humans species, if you are a sucker enough to believe that amantra which is called evolution, but thats a completely different thread and day) all the time (have you seen the Lexus? just the only of its kind in the world, and its selling). Toyota is light years ahead of the pack (thats you and me so by the way)…number 8 in the world…only second to the oil giants, the retail giant, General Motors (which is struggling so by the way – we’re all waiting in anticipation to see wheter Carlos “The Great” will come to its rescue), Chevron and DaimlerChrysler. Have any of you folks actually ever visited Toyota Japan website? There’s some info on the TPS and some VIDEOS of the plant in ACTION. Go watch it! You might understand Sir Simon’s revelation re LEAN…It is art. Six Sigma on the other hand is STATS on STEROIDS…if you folks don’t mind me saying so…which I guess is science or business science or whatever. The importent thing is, it can be COPIED. It was designed to copy…still require intelligence. For you folks who still can’t make head nor tail between LEAN, Six Sigma and TOC, I recommend “The NEW LEAN Toolbox” by John Bicheno. The most important thought I would like to bring home via this thread is that LEAN is not tools! “It is an end-to-end value stream that deliver competitiveness” by your man Bicheno, and “LEAN become even more powerful concept as it integrates with ‘fast flexible flow’, with TOC, with ‘factory physics’, with service concepts, with much of Six Sigma, and with ERP. And LEAN is expanding into NEW areas far removed from repetitive manufacturing – LEAN construction, LEAN project management, LEAN health, LEAN service, and even, wait for it, LEAN defence and LEAN public service.” just to warm up your taste budds. Maybe just a little bit more, Six Sigma and TOC as what I can figure out, come strongly into play, after according to Bicheno, the first 6 steps of his LEAN framework, the 6th being “Implementing the Lean Foundation Stones”, within the 7th step, which is “The Value Stream Implementation Cycle”, consist of 15 steps, the 8th being “Future state workshop”, and its within this particular step which consist of various relevant tools, one of which consist of two STEPS, the first “Designing a Pull System with Heijunka, and the second “Cell and Line Design”. The first step consists of 19 substeps, of which the seventh substep is described as “Identify constraints convergences and variation” for which the relevant tools are TOC, Factory Physics and Six Sigma. LEAN is evolving science in ART form. NOT to be taken lightly or to be sniffed at (as a white collor). Hint of Caution! The likes of Jeffrey Liker will prob tell ya in re to LEAN “Go find a sensei to learn from and enjoy the yourney!” Well I think we all now that there are no senseis out there! Only idiots who think they know everything about everything, and are quick to tell you all about it. So allow me to revise slightly “Research LEAN (Six Sigma and TOC cause you’re gonna need it also), study it, UNDERSTAND it, do it and enjoy the yourney!” Become a Specialist in all three! Become an ARTIST! And make a difference or DIE trying! Go know! Don’t just sit there with your mouth open! Go! Go! Go SERVE mankind!
Message: 99026
Posted by: Hans
Posted on: Thursday, 17th August 2006
Bert,
I assume as a practical consultant you have been certified as a “Jonas” by the Goldratt Institute. So you probably have gone through some rigorous training and certification, i.e. no need to apologize for not being a “Six Sigma” professional!
If I understand Goldratt correctly, he has a very pragmatic approach which uses a combination of his own earlier work on systems theory and constraints, and lean and defect reduction tools as needed. He has also contributed some interesting and simple formulas that apply learnings from Johnston and Kaplan on the limitations of cost accounting, i.e. his defiinition of throughput accounting etc. He also realizes (with the old Japanese quality gurus) that most process problems can be solved using logic (including the logic of lean “principles” … he may use the current and future reality trees, which differ somewhat from the Fishbone, but in the end, they have the same purpose). Finally, while he admits that one-piece flow may be optimal, he also sees that many real-world organizations will probably never do better than batch optimization, leaving it to Toyota to be the “shining light” and change existing organizations as much as needed to move the constraint to where it where it ideally is: the market (which is the premise of all micro-economics that it is better for an organization if the demand exceeds the supply … go figure).
I think that rather than putting up these somewhat arbitrary barriers between TOC, lean and quality it is time to become pragmatic (rather than ideological) in applying an approach that best suits the needs of an organization. Motorrola did what was best for it. Toyota did the same. What companies can learn from them is to be innovative and realistic about their challenges rather than look for that silver bullet and “template” that will resolve all issues. In the end, we all agree that the best way to solve a problem is to “look for yourself” (use your brain and the formula when needed). Have a good evening!
Message: 99027
Posted by: Peter
Posted on: Thursday, 17th August 2006
Just in case you all think i’m mad…I’m not really…Just an industrial engineer currently doing my MASTERS in wait for it “Implementing BEST PRACTICES against the unique sosio-political background of South Africa”…I’m gonna have to recommend either or, or a combination of the three animals (LEAN, SIX SIGMA & TOC), or I might even have to develop a customized model myself of either or, or a combination of the three. Currently doing research on all three when I accidently stumbled upon Simons thread, unlucky/lucky for you all!!
Currently, I actually have no opinion as to which route to follow when it comes to these three animals. I just know that LEAN is extremely misunderstood, undervalued and its complexity downplayed in the industry, its a LOT more complex folks then what people make it out to be. LEAN is not simple, but simplicity pervades. Furthermore, it’s not so much an issue of complexity, as it is an issue in that it’s about tacit knowledge, not explicit procedural knowledge, a craft type, unlike the other two animals. A lot of myths out there re LEAN folks! Be aware! I also know that Six Sigma is made out to be a lot more complexed then it really is. Its just strait forward stats folks, not advance stats for engineers! Plain stats, wrapped in Demings DMAIC. Six Sigma for me is relatively straight forward and lacks complexity (even substance – localized optimization), to me its like a bull in a china shop! Lacks people skills! Not to mention sustainability! But if you are a Bull or an American for that matter, with plenty of people skills, and wants immediate impressive looking results, you’ll achieve it with Six Sigma…through localised bull like improvements. But I have a feeling cause it’s localised the problem is gonna raise its ugly head somewhere down the line in a different form. And TOC is also for me a little bit lacking in substance, and though it also lacks worker involvement or empowerment, its probably handy if your in a company or culture where you don’t want to value the workers opinion for whatever reason…as you can see I actually dont have much clear direction either, it seems to me however at this junction that the answer lies in LEAN as the foundation, integrating at certain points, with among other animals, the likes of Six Sigma and TOC…One thing I do know at this point in time and that is that LEAN is at the CORE!!…will let you all know my conclusion/finding on this matter in oh! another year down the line…
Message: 99032
Posted by: Bert
Posted on: Friday, 18th August 2006
Hans,
Thank you. You might find this study of interest.
http://www.advanced-projects.com/APICS_study.htm
It describes one company’s experience implementing Lean, Six Sigma and TOC separately, and in combination and different plants that were sufficiently similar in circumstances as to represent a reasonably accepatable basis from which to draw some interesting conclusions. One obvious question was never addressed by the study. Can you tell which question I am refering to and why it might not have been addressed? It isn’t too difficult to use an ANOVA approach to deduce the isolated effect of TOC alone. What do you think?
If you want to continue this one-on-one, contact me at let me know in your reply.
Message: 99037
Posted by: BGBB
Posted on: Friday, 18th August 2006
My $0.02 in this debate is a keep it simple one- and I make no apologies for recounting this, as its not my idea, but that of the guy who trained me to Black belt, but does a great job in defining the how Lean and Six Sigma go together.
Think of Six Sigma and Lean (include TOC here, like I said, KISS) as two separate sets in a Venn diagram. The commonalities (tools, approaches etc) in each set is where the 2 sets overlap. If your look critically, you will see that:
1) That the area of the intersection is greater than either of the remaining areas left outside the intersection.
2) The intersection area contains the most practical and pragmatic approaches to Conintuous Improvement.
3) Tools and techniques left outside the intersection, are still valid and should not be dismissed. Its just that they probably dont get used that often.
Lastly and IMHO most importantly, Lean (and TOC) is about ‘Doing the right things’ (WIP and Leadtime reductions, JIT etc), and Six Sigma is about ‘doing them right’ – using the data to drive the improvements and to know when you’ve made a change (+ve or -ve).
BRgds
BGBB
Message: 99065
Posted by: Peter
Posted on: Friday, 18th August 2006
Andy,
Good on ya mate!
Did it look something like the following?
I know the thread from Simon “LEAN is Art” and “Six Sigma is Science” is Nov05…it’s just I couldn’t help myself to add to it even if it is almost a year on – it brought such a feeling of WOW!
Somebody actually managed to hit the nail on the head.
CONGRATS! If there was a price I would give it to you Sir Simon!
Allow me to embroil further just a little! “LEAN is Science in Art Form” – probably the reason why so many companies fail to copy it. It CAN’T be copied! It’s an art form.
You have to become an ARTIST, not just you, everybody in the company, not just any artist, but an ARTIST, like Rembrandt. Toyota is a painting like “Die Nagwag” from Rembrandt, and it gets worse folks! It’s evolving, it gets better and better all the time (almost like us humans species, if you are a sucker enough to believe that mantra which is called evolution, but that’s a completely different thread and day).
Have you seen the Lexus? Just the only of its kind in the world, and its selling.
Toyota is light years ahead of the pack (that’s you and me so by the way)…number 8 in the world…only second to the oil giants, the retail giant, General Motors (which is struggling so by the way – we’re all waiting in anticipation to see whether Carlos “The Great” will come to its rescue), Chevron and DaimlerChrysler.
Have any of you folks actually ever visited Toyota Japan website? There’s some info on the TPS and some VIDEOS of the plant in ACTION. Go watch it! You might understand Sir Simon’s revelation re LEAN…It is art.
Six Sigma on the other hand is STATS on STEROIDS…if you folks don’t mind me saying so…which I guess is science or business science or whatever. The important thing is it can be COPIED. It was designed to copy…still require intelligence.
For you folks who still can’t make head or tail between LEAN, Six Sigma and TOC, I recommend “The NEW LEAN Toolbox” by John Bicheno.
The most important thought I would like to bring home via this thread is that LEAN is not tools! “It is an end-to-end value stream that deliver competitiveness” by your man Bicheno.
“LEAN become even more powerful concept as it integrates with ‘fast flexible flow’, with TOC, with ‘factory physics’, with service concepts, with much of Six Sigma, and with ERP.”
“And LEAN is expanding into NEW areas far removed from repetitive manufacturing – LEAN construction, LEAN project management, LEAN health, LEAN service, and even, wait for it, LEAN defence and LEAN public service.” just to warm up your taste butts.
Maybe just a little bit more, Six Sigma and TOC as what I can figure out, come strongly into play, after according to Bicheno, the first 6 steps of his LEAN framework, the 6th being “Implementing the Lean Foundation Stones”, within the 7th step, which is “The Value Stream Implementation Cycle”, consist of 15 steps, the 8th being “Future state workshop”, and its within this particular step which consist of various relevant tools, one of which consist of two STEPS, the first “Designing a Pull System with Heijunka, and the second “Cell and Line Design”. The first step consists of 19 sub steps, of which the seventh sub step is described as “Identify constraints convergences and variation” for which the relevant tools are TOC, Factory Physics and Six Sigma.
LEAN is evolving science in ART form. NOT to be taken lightly or to be sniffed at (as a white collar).
Hint of Caution! The likes of Jeffrey Liker will probably tell you in re to LEAN “Go find a sensei to learn from and enjoy the journey!”
Well I think we all know that there are no sensei’s out there!
Only idiots who think they know everything about everything, and are quick to tell you all about it.
So allow me to revise slightly “Research LEAN (Six Sigma and TOC cause you’re gonna need it also), study it, UNDERSTAND it, do it and enjoy the journey!”
Become a Specialist in all three!
Become an ARTIST!
And make a difference or DIE trying!
Go know! Don’t just sit there with your mouth open!
Go! Go!
Go SERVE mankind!
Just in case you all think I’m mad…I’m not really…Just an industrial engineer currently doing my MASTERS in wait for it “Implementing BEST PRACTICES against the unique social-political background of South Africa”…
I’m gonna have to recommend either or, or a combination of the three animals (LEAN, SIX SIGMA & TOC), or I might even have to develop a customized model myself of either or, or a combination of the three.
Currently doing research on all three when I accidentally stumbled upon Simons thread, unlucky/lucky for you all!!
Currently, I actually have no opinion as to which route to follow when it comes to these three animals.
I just know that LEAN is extremely misunderstood, undervalued and its complexity downplayed in the industry, its a LOT more complex folks then what people make it out to be.
LEAN is not simple, but simplicity pervades.
Furthermore, it’s not so much an issue of complexity, as it is an issue in that it’s about tacit knowledge, not explicit procedural knowledge, a craft type, unlike the other two animals.
A lot of myths out there re LEAN folks! Be aware!
I also know that Six Sigma is made out to be a lot more complex then it really is.
Its just strait forward stats folks not advance stats for engineers!
Plain stats, wrapped in Demings DMAIC.
Six Sigma for me is relatively straight forward and lacks complexity (even substance – localized optimization), to me it’s like a bull in a china shop! Lacks people skills! Not to mention sustainability!
But if you are a Bull or an American for that matter, with plenty of people skills, and wants immediate impressive looking results, you’ll achieve it using Six Sigma – through localised bull like improvements.
But I have a feeling cause it’s localised the problem is gonna raise its ugly head somewhere down the line in a different form.
And TOC is also for me a little bit lacking in substance, and though it also lacks worker involvement or empowerment…it’s probably handy if you are in a company or culture where you don’t want to value the workers opinion for whatever reason…
As you can see I actually don’t have much clear direction either, it seems to me however at this junction that the answer lies in LEAN as the foundation, integrating at certain points, with among other animals, the likes of Six Sigma and TOC…
One thing I do know at this point in time and that is that LEAN is at the CORE!!
…will let you all know my conclusion/finding on this matter in oh! Another year down the line…
By the way I have no idea what Lean Six Sigma is yet!
Not conspired/concocted by the Japs, that much I can tell ya!
Books are huge and very intimidating looking, almost like the Six Sigma textbooks!
Maybe the Americans realized Six Sigma cant stand or exist by itself, therefore needs to lean on something (Joke)!
Happy trailing!
Message: 99066
Posted by: mikel harry
Posted on: Friday, 18th August 2006
LEAN focuses on waste while SIX SIGMA focuses on minimizing the variation after waste have been reduced. Both concerns improvements
Message: 99070
Posted by: Peter
Posted on: Friday, 18th August 2006
LEAN focuses on waste = Nr 1 Biggest myth re LEAN
Waste elimination is a means to achieving the LEAN ideal – it is NOT an end in itself!!!
Allow me then to quote from Bicheno’s new book (“” “”):
“”George Davidson, retired manufacturing director of Toyota South Africa, says that the first principle of the TPS (LEAN) is “the customer first”. And, George, how do you do that? “By creating thinking people”, says he. And how do you do that, George? “By creating workplaces and organizations that are more human”.
Note what Davidson is NOT saying.
It is not primarily about waste; waste is removed because you want to improve benefits to the customer.
Hence Toyota is not averse to adding inventory where necessary – as indeed they have done recently.
It is not about 5S – 5S is just a tool for consistency and quality.
It is not about SMED – SMED is just a tool for improving response time and service to the customer.
LEAN developed from first principles, with the customer in mind.
In fact NON-LEAN systems do just the opposite. For instance, through “economic order quantities”, “mass-production”, long lead times, reduced variety, “push” systems, and the location of plants in China purely for cost – all of which are designed with the producer in mind, not the customer!
One way of understanding LEAN is to view it as a (proven) approach to dispense with increasingly inappropriate ‘economies of scale’ and to adopt ‘economies of time’.
LEAN is not tools!!””
LEAN focuses on Waste Prevention
LEAN focuses on Value
LEAN focuses on System
LEAN focuses on Process
LEAN focuses on Revolution and Evolution
LEAN focuses on Distributed Decisions
LEAN focuses on Service
LEAN focuses on Built to Order
LEAN focuses on Green
“”LEAN is only beginning
LEAN is Core
Hopefully the days of arguing between “LEAN vs AGILE”, “LEAN vs APS”, “LEAN and Six Sigma”, “LEAN and TOC”, “LEAN and Manufacturing Strategy”, and the practice of including one chapter on LEAN (or JIT) in operations management textbooks, is passing.
Perhaps not – academics are often the last to change!
LEAN is at the CORE. The principles are universal. It is merely a question of the extent to which other concepts can add to the central developing CORE of LEAN, and vice versa.
Furthermore, there are 20 characteristics of LEAN, but I think you all get the picture.
Finally re LEAN & Six Sigma:
They are no longer at odds, nor should they be. LEAN is better at the big picture, at establishing the foundation through activities such as 5S and standard operations, whilst Six Sigma offers a powerful problem solving methodology through DMAIC. The LEAN value stream mapping tools are generally superior but synergistic with those used in Six Sigma, and concepts such as cellular manufacturing, quality at source, pokayoke, and TPM are entirely synergistic. Six Sigma has shown a lead in the costing of projects, something that is under-developed in LEAN. There are however also doubtful practices in Six Sigma, as pointed out by one of the originators, Keki Bhote ex-Motorola quality guru.
However, much of Six Sigma itself is waste! What can be done to reduce or eliminate that variation before it even arises should be the prime question.
Why is Toyota not falling over itself to get after Six Sigma or alternatively how is it been able to achieve Six Sigma levels of performance without legions of black belts and statistical software?””
Message: 99090
Posted by: EdG
Posted on: Friday, 18th August 2006
I was looking at all that you wrote and thought in short could this summarize your work.
Lean is an interpretation or representation of the Toyota Production System. Given everyone can interpret what he or she sees differently, no wonder there are those that say; “Lean is about waste elimination”, “Lean is about 5S”, or “Lean is about ____”.
Rather, Lean is a part of the whole (the TPS). So all that is considered Lean can be found in TPS, BUT all that is the Toyota Production System is not found in Lean. TPS is the complete system, not an interpretation of another system or a part of the whole.
I sat in a presentation by John Shook and he commented, TPS is about
Creating an environment in which the abnormal can be distinguished from the normal,
Developing a workforce that knows what the right thing is to do when they encounter the abnormal, and (I believe this is why there are those at Toyota that refer to TPS as the Thinking Production System.)
Empowering your workforce to do the right thing.
Notice there is nothing in there about waste. However, if you think about every tool within the Lean toolbox it applies to a part of this statement (primarily #1). And for those that are successful in implementing Lean, numbers 2 & 3 were applied. But where it failed, they forgot about numbers 2 and/or 3.
Message: 99096
Posted by: Paul
Posted on: Saturday, 19th August 2006
EdG: Thanks for sharing these three points of TPS, Thinking Production System. But, when you reduce the thinking from this TPS, what is left, Lean Thinking, or the Lean System, one without thinking, just doing.
That’s why TPS discourage layoffs, while with Lean Thinking, layoffs is the first expectation.
Paul
Message: 99106
Posted by: EdG
Posted on: Saturday, 19th August 2006
Paul,
This is why I stressed that all that is Lean is found within TPS but not all that is TPS is within Lean. Those that are truely successful with Lean look to the source, TPS, and add to it that which they realize they are lacking. Those that are not successful merely take it at face value, given whomever taught them, and then screw it up with layoffs and the like.
To really be successful one must study and follow the original, TPS. Don’t get me wrong, my company has brought in “Lean consultants” to help. But I don’t only listen to them, I still keep going back to TPS (via many sources) and try to add to that which is missing.
Just a little advice. No one has to listen if they don’t want to…
EdG
Message: 99107
Posted by: Peter
Posted on: Saturday, 19th August 2006
LEAN = TPS = The TOYOTA WAY = the source.
The moment you place a verb after, or an adjective before LEAN, you are busy with segregation. Think about it. Hence the reason for the hybrid between Six Sigma and TPS is called LEAN Six Sigma (if that is what Lean Six Sigma is supposed to be).
Further, on the topic of segregation (which so by the way should take the blame for when LEAN doesn’t bare fruit), according to Bicheno Mechanical LEAN is the implementation of LEAN tools in a piecemeal fashion. Managerial LEAN is the implementation of LEAN tools in an integrated manner. Innovation LEAN takes LEAN beyond the shop floor, beyond the organization to create new opportunity, value and customers. LEAN often begins with Mechanical (Demonstration) and since piecemeal benefits are small, executives may then decide to abandon the LEAN initiative, claiming they have done LEAN and it didn’t do them much good.
LEAN = End-to-end evolving value stream that delivers competitiveness.
Another point to ponder is that the missing ingredient in most companies trying to implement LEAN is the principle which is the foundation for all the other LEAN principles namely PHILOSOPHY. Toyota gives us a glimpse of an alternative, provides a model of what happens when tens of thousands of people are aligned toward a common purpose that is bigger than making money.
Message: 99118
Posted by: EdG
Posted on: Saturday, 19th August 2006
I disagree with LEAN = TPS.
Lean is not ALL that TPS is. It is a copy but it is not the ORIGINAL. You go to Vegas and see Elvis impersonators all around. Some may be very good and some may be terrible, but NONE is the original.
Lean would be comparable to that. It is an impersonation, but it is not the original.
Message: 99120
Posted by: Marlon Brando
Posted on: Saturday, 19th August 2006
I believe Lean is Lean and TPS is TPS,we should not mix them up.Human Mind is usually like to make comparisons all the way without any useful conclusion (in some cases).
Message: 99122
Posted by: Peter
Posted on: Saturday, 19th August 2006
Ed,
…But surely then you don’t…disagree.
…in the ideal state LEAN = TPS, in reality, sadly, it’s not the case due to mankind’s nature to loose sight of the original message and drift away from it (exactly like the Gospel).
You’ve mentioned that every now and again you go back to the source, can you kindly elaborate (titles/authors)? Will help with my thesis on this matter (don’t mind if i have to add TPS as a fourth animal, along side LEAN – just would like to get to the bottom of what has suddenly become bit of an issue for me).
Peter
Message: 99123
Posted by: Peter
Posted on: Saturday, 19th August 2006
Marlon,
Where is TPS documented, other then Jeffrey Liker’s “The Toyota Way” and the sequel “The Toyota Way – Fieldbook” (I presume these 2 books qualify)?
Peter
Message: 99125
Posted by: amagdalon vs cerebrus
Posted on: Saturday, 19th August 2006
If you go to amazon.com and do a quick search, you’ll find sufficient documentation written by Toyota engineers and Japanese academics that will give you a detailed historical overview of the TPS system. I always thought that the literature research was a prerequisite for a successful thesis. I, for my part, get pretty annoyed by the ramblings of an amateur intellectual who has neither academic nor professional experience nor credentials.
Message: 99126
Posted by: Paul Gibbons
Posted on: Saturday, 19th August 2006
Peter,
You write as though you are an expert on lean. Are you? What is your thesis about, I would be really interested. I am interested in lean myself and it would be great to share some references etc.
Thanks
Paul
Message: 99129
Posted by: Peter
Posted on: Saturday, 19th August 2006
Paul,
Hardly! As my new found fan has so sweetly and lovingly pointed out.
Bachelors in Industrial Engineering, with 3 years experience in Construction Project Management (Anglo America & Intel) and 2 years in FMCG (SMT & PCB Fabrication), who recently embarked on a thesis in relation to “Implementing BEST PRACTICES against the unique social-political background of the Republic of South Africa”,
Just recently started with Phase 1 – Literature Research,
LEAN, Six Sigma and TOC will be my focus…and from what I now gather from EdG, I should treat TPS separate from LEAN…still trying to get 2 the bottom of that aspect…I was/am under the impression they were/are the same.
Would love to exchange references – one of my many personal local e-mails (which I can delete, just in case I get harassed by fans) is pietersburgerwebmail.co.za, this site probably not the vehicle for that…
Peter
Message: 99130
Posted by: EdG
Posted on: Saturday, 19th August 2006
Although I like Dr. Liker’s book, he doesn’t have the corner market on TPS.
There is Toyota Production System by Taiichi Ohno, A Study of the Toyota Production System by Shigeo Shingo, The Evolution of a Manufacturing Systems at Toyota by Takahiro Fujimoto, and Toyota Production System by Yasuhiro Monden.
I could go on but I think you get the message. Like I said I also like Liker’s book. And I also like Dr. Steven Spear’s works.
Message: 99138
Posted by: EdG
Posted on: Saturday, 19th August 2006
Peter,
Lean is a copy of TPS. Some come to a more close representation than others…
By the way, I would offer up as you understand more of TOC you may see similarities between it and Lean. I would say that they (both Lean and TOC) are different interpretations of the same system, the Toyota Production System. Just Goldrath latched on to the supply chain/constraints aspect and Womack was more focused on waste elimination and problem solving. There are many that would say I am wrong, but it is just my opinion.
Good luck…
Message: 99144
Posted by: Peter
Posted on: Saturday, 19th August 2006
Ed,
So who have the corner market on TPS? Ohno, Shingo, Fujimoto & Monden? U said u could go on? Does Spear fall in the group that has the corner market? And do I then classify “The Toyota Way” and “The Toyota Way Fieldbook” by Liker together with the rest (Womack) under LEAN? Are there books re specific TPS tools that belong in the corner market on TPS like for example maybe “Just-In-Time 4 America” by Kenneth Wantuck and “One-Piece-Flow” by Kenichi Sekine? I’m not 2 faced with titles (2 daunting a task) – it’s the authors that I’m after (the people with the, know how). Thanking you in advance. My private e-mail address pietersburgerwebmail.co.za
Peter
Message: 99152
Posted by: Amagdala vs. Cerebrus/Explanat
Posted on: Sunday, 20th August 2006
Peter,
You may wonder why you created such as strong reaction. What caught my attention was the tone of your first postings and your responses. We see a lot of “novices” on this site, but few of them start out with such strong opinions supported by so little knowledge.
So I wanted to know more about you and your background, and what better way to do that than to put someone into an emotional state and see their reactions. What I saw was less than flattering. Even though I do apologize for using the terms “fool”, “bigoted” and “hippocritical”. Egomaniac to some degree is more to the point. You’ll have to live with your religion, your atttitude towards America and to women and the gay population in general. I think you still have some growing up to do in this area but that is is just my personal opinion.
Now to my point: You wondered why I did not contribute “substantially” to your discussion thread. Reason: You were (and maybe are) not ready for the key message.
Any of the initiatives (Six Sigma, Lean or TOC) requires personalities with a strong yet flexible background in the art of changing a business. Work in this area is more like a boxing match or bushido where you don’t just walk into the ring as an amateur telling everyone they have no clue and expect to walk away without getting bruises in the real fight. This is what many consultants do, and currently we see a wave of online certifications that does not prepare the so-called GBs and BBs for the real job.
Starting from this premise you can look at them as different fighting techniques such as Tae Kwon Do, Karate, bare knuckle boxing etc. You’ll gain much more insight into the different approaches when you look at them as different techniques to stay competitive in a specific environment. In a street fight (and true businesses are more like street fights than like regulated boxing matches) you’ll do what you can do to win and survive. I hope this exchange has focused you more on the true goal and essence of the techniques.
Master Black Belts are Master Black Belts for a reason: they train and coach the BBs and GBs through the brutal game of corporate change initiatives. A Jonas has gone through the excruciating training of Elias Goldratt. He is well known for tearing people apart who are not up to the game. And for a good reason. You don’t ever want to look like a fool in front of a CEO.
Maybe your first step in your thesis may be to try to understand what these methods are about and what professionals in this area are up against. After that you can start criticing the different approaches in terms of which is most effective in the street fights of Corporate competition.