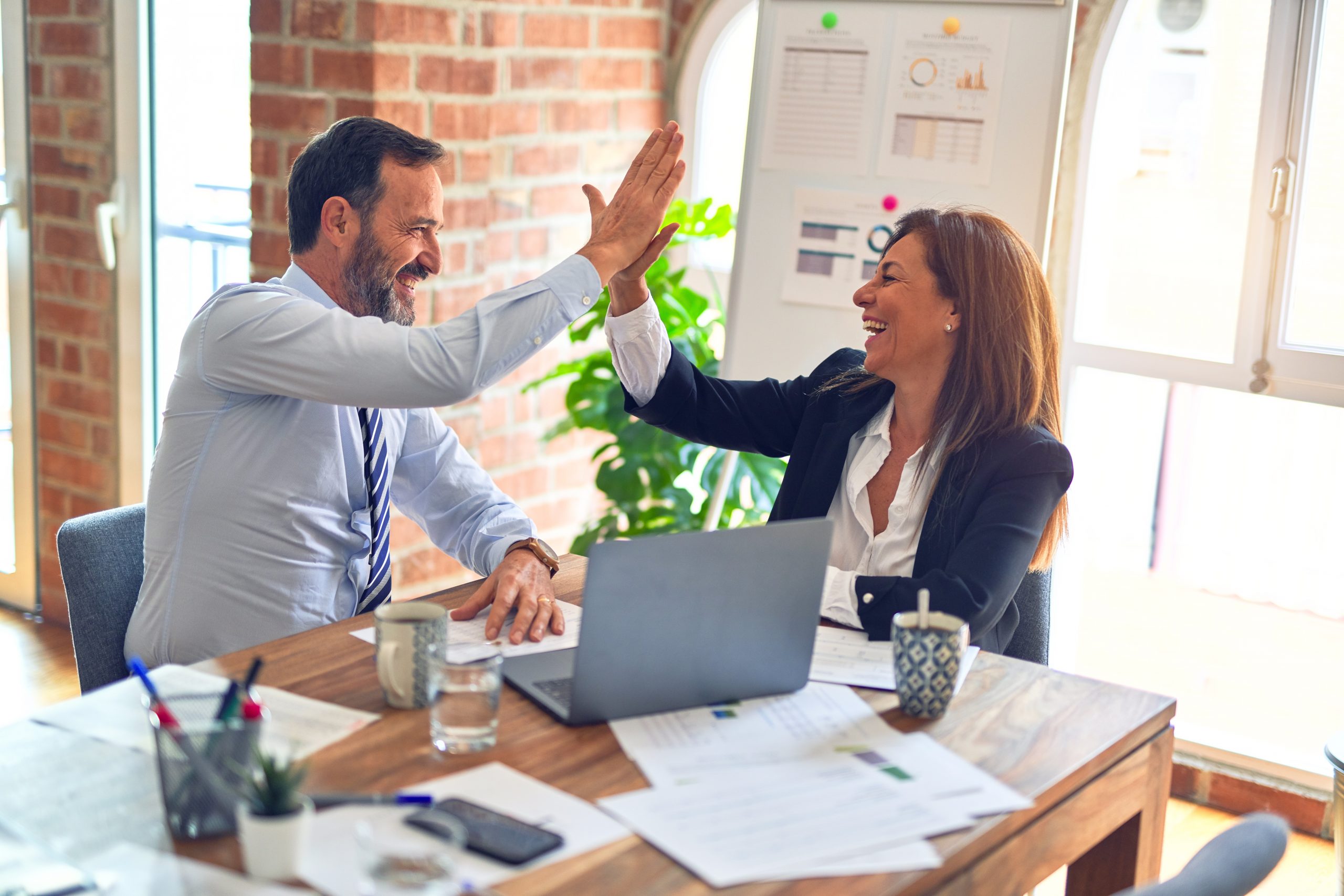
Our health system began its Six Sigma journey about three years ago. We started up in Wave I with three Black Belts at the two largest hospitals (myself among them) who had no real idea of what would come. After a successful round of projects in Phase I, we expanded to hire an additional 12 Black Belts to cover the rest of the hospitals, and moved two individuals up to Master Black Belt positions. We had a great Wave II – ok, there were the usual growing pains, but overall we were feeling pretty good about ourselves. Onward to Wave III!
Then we started learning more about lean. Our executives loved the idea that we could move faster; the concepts and tools were simple to understand and easy to learn. We shifted gears to start doing some lean projects (kiazens or Rapid Improvement Events as you prefer).We had very good success; team members were enthusiastic and executives raved.
Some of our Black Belts, myself included, were happy to learn the lean tools but were notas comfortable with the lean projects as with the DMAIC methodology. I was puzzled because I liked everything about lean, except for the kaizen project structure, and I couldn’t figure out why this might be so. After a lot of reflection, I came up witha theory. It’s based onthe Meyers-Briggs personality types – an assessmentbased on individual preferences in four areas: introvert-extrovert, intuitive-sensing, thinking-feeling, judging-perceiving.
The DMAIC methodology is perfect for intuitive-thinking types. These individuals are called “the Rationals” according to Keirsey, and are highly skilled in strategic analysis. You want to go in there, look at a problem, analyze it, and then pick the right solution. You invest a lot of time and effort into making things right, and the payoff is doing it right the first time. Achieving the goal is the thing.
The lean methodology, on the other hand, is perfect for sensing-feeling types. Keirsey calls these “the Artisans” whose strengths are in tactical variation – that is, trying things out and honing activities until perfection is approached. You want to go in there, look at a problem, and start trying to make things better. If at first you don’t succeed, try try again! You invest a lot of energy into making things get better one step at a time, and the payoff is seeing how far you have come. Making the journey is the thing.
I’m pretty firmly in the intuitive-thinking camp, so that was my “aha” moment of why I didn’t have the same enthusiasm for Lean as I did for DMAIC. Having explained this, at leastfor myself, I started to wonder whether I would have been more comfortable incorporating lean tools if I had approached it from this perspective from the start. Of course, most of us are perfectly capable of using whatever tools are required to achieve process improvements. But I wonder whether knowing our personality preferences is just as useful as knowing the tools of Six Sigma and Lean.
What do you think?