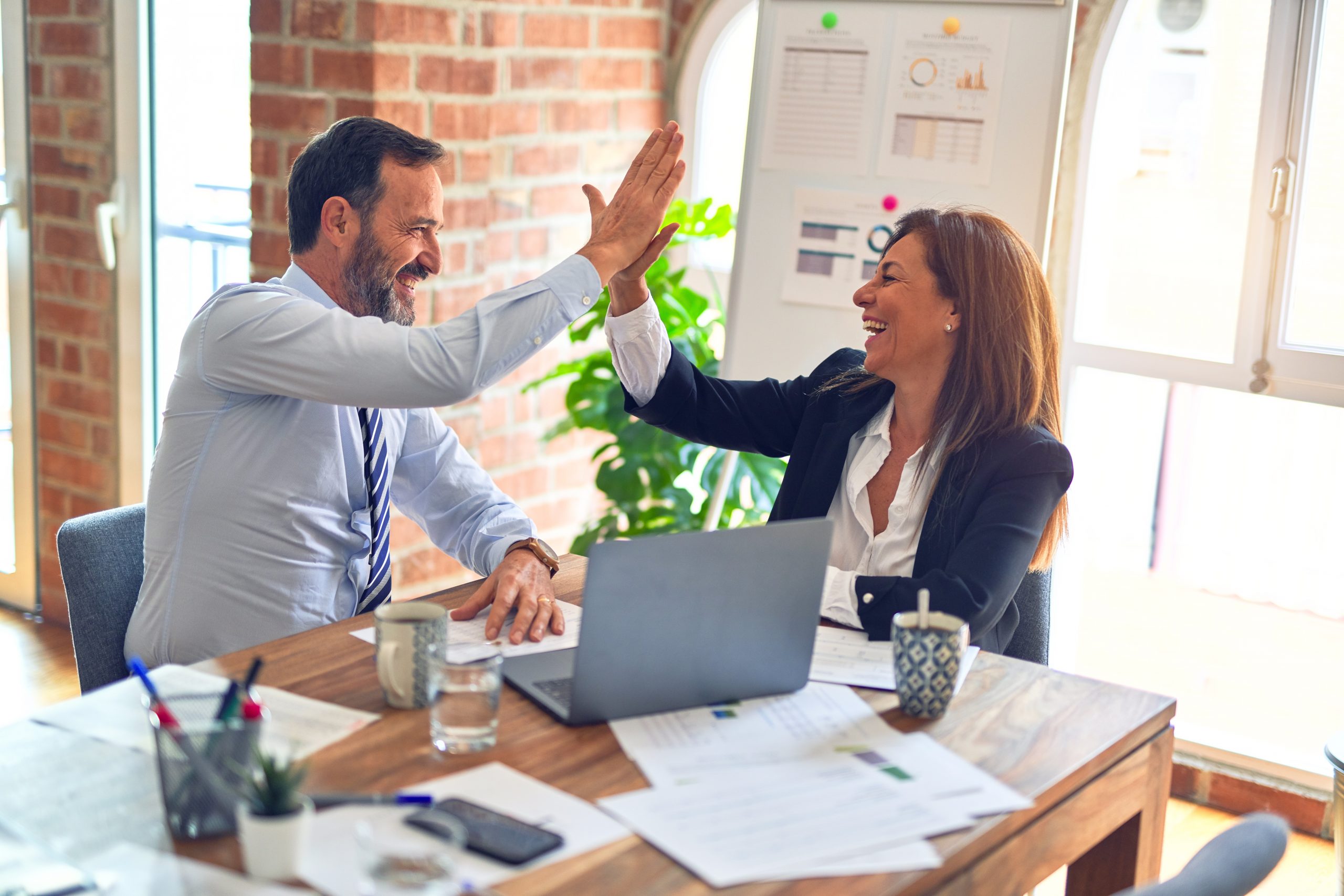
When I started in continuous improvement (CI) four years ago it was via the traditional Six Sigma DMAIC route. I was indoctrinated into the Six Sigma world and have earned my ASQ CSSBB and can do impressive stuff with statistics. Lean was not even on the radar for me, it was just another approach that was used to solve the easy stuff. It did not have the rigour to make lasting improvements.
Then Lean appeared through our training material and we merged it to become Lean Six Sigma. But it was an unequal partnership. We had the DMAIC model with Lean as a bolt-on included in the Analyse phase. It focussed on analysing and removing waste in the process. It was a pretty easy concept; by removing waste you become a Lean business. And that’s how it stayed, everyone understood Lean.
Meanwhile I had nagging doubts that pure Six Sigma did not provide a complete package. There are the obvious issues around needing to include project management, stakeholder management, soft-skills training and deployment program management. There was also the concern that it was too generalist as specialist niches become prevalent, e.g. Customer Experience theory now goes way beyond the VoC approach.
It started with The Goal. I really liked the concept of managing your process around exploiting the constraints & bottle-necks. Then I met a few people who had started their CI journey from Lean who talked about different concepts & approaches. Then I met someone who was a Systems Thinker and they thought Six Sigma was just plain wrong. Give these quotes a go, (more in a follow-up blog as I am still reading the book):
- It starts with ‘define’ so the wrong problems get tackled, not the actual problems, which will only be revealed when you study the organisation as a system.
- Loads of money is spent on training tools, most of which will never be used; and tools are not the means for changing the system.
- The reporting systems ensure benefits are ‘realised’ but they are, most often, spurious e.g. claiming productivity improvements through speeding up part of a process with no knowledge of the impact on the end-to-end process
- It has been used to focus on cost; managers should instead get focused on value as the better way to reduce costs and increasing capacity.
- In short, Six Sigma is a classic packaged invention aimed at gullible managers. The wrong facts are misleading; we should salute its demise.
All good stuff to challenge the orthodoxy. So I have been studying pure Lean. First problem I had was translating the tools out of manufacturing into a service organisation. With things like SMED you seem to have to abstract the concept and look for applications. Or 5S, it’s not a safety issue having a messy desk and I am doubtful on the benefits (I have a clean desk). But as I got deeper I found this doesn’t do Lean justice, the fundamental principles and practises go way beyond “just eliminate waste”. Lean seems to provide much more in terms of the complete package and inparticular around empowering people.
As ever, I still have my doubts e.g. how does break-though innovation happen in a Lean environment? And whatabout the “Lean is just removal of waste” label? But it has definitely shifted my thinking. Now I am “Learning to See” I wonder if there are any other approaches I should be looking at?