
© Sun Shock/Shutterstock.com
Key Points
- Lean Six Sigma tools like Value Stream Mapping and predictive analytics help organizations identify inefficiencies, optimize inventory, and establish resilient supply chains to mitigate risks from delays and shortages.
- Digital tools and virtual Lean Six Sigma practices, such as online Kanban boards and virtual Kaizen events, ensure effective collaboration, transparency, and communication in remote and hybrid environments.
- Lean Six Sigma integrates seamlessly with digital initiatives by streamlining processes, identifying automation opportunities, and leveraging data-driven insights to ensure efficient adoption of technologies like AI and RPA.
- Using tools like Voice of the Customer (VoC) and root cause analysis, Lean Six Sigma enables organizations to enhance product quality, reduce delivery times, and adapt processes to meet heightened customer demands for speed and customization.
Introduction
The COVID-19 pandemic disrupted global operations, forcing organizations to reevaluate traditional business practices and adapt to an unpredictable environment. Lean Six Sigma (LSS), a methodology focused on reducing waste and improving quality, has proven to be a critical tool in navigating these challenges. By emphasizing data-driven decision-making, continuous improvement, and flexibility, Lean Six Sigma can help organizations meet the demands of a post-pandemic world. This paper explores how Lean Six Sigma methodologies can be adapted to new operational realities and provides specific examples and recommendations for businesses.
New Operational Realities in a Post-Pandemic World
Organizations are facing several key challenges and opportunities in the post-pandemic landscape:
- Supply Chain Disruptions: Global supply chains have become increasingly fragile, with shortages, delays, and rising costs creating bottlenecks.
- Remote and Hybrid Work Models: Flexible work arrangements have become standard, impacting collaboration, communication, and productivity.
- Increased Demand for Digital Transformation: Businesses are leveraging technology to automate processes and enhance efficiency.
- Heightened Customer Expectations: Consumers now demand faster delivery, personalized experiences, and higher-quality products.
- Economic Uncertainty: Organizations must remain agile to navigate inflation, shifting markets, and geopolitical risks.
Lean Six Sigma offers a structured approach to address these challenges while fostering resilience and adaptability.
Adapting Lean Six Sigma to New Realities
1. Addressing Supply Chain Disruptions
Lean Six Sigma can help organizations build more resilient supply chains by identifying inefficiencies, optimizing inventory management, and reducing lead times.
- Example: A manufacturing company facing raw material shortages conducted a Value Stream Mapping (VSM) exercise to identify bottlenecks. By implementing just-in-time (JIT) practices and partnering with multiple suppliers, the company reduced delays and minimized dependency on a single source.
- Recommendations:
- Use Lean tools like VSM and Fishbone Diagrams to pinpoint supply chain inefficiencies.
- Implement predictive analytics to forecast demand and manage inventory levels effectively.
- Establish contingency plans with alternative suppliers to mitigate risks.

©Greens and Blues/Shutterstock.com
2. Enhancing Collaboration in Remote and Hybrid Work Models
The shift to remote and hybrid work requires Lean Six Sigma practitioners to adapt their approaches to ensure effective collaboration and communication.
- Example: A financial services company struggled with delayed project deliverables due to poor coordination in hybrid teams. By implementing virtual Kanban boards and scheduling regular stand-ups, the team improved transparency and reduced cycle times.
- Recommendations:
- Leverage digital collaboration tools like Trello, Miro, or Microsoft Teams to facilitate remote Lean Six Sigma projects.
- Conduct virtual Kaizen events and use breakout rooms for brainstorming sessions.
- Establish clear communication protocols and accountability frameworks.
3. Driving Digital Transformation
Lean Six Sigma can support digital transformation by streamlining processes and ensuring successful technology adoption.
- Example: An e-commerce company adopted robotic process automation (RPA) to handle order processing. Lean Six Sigma’s DMAIC framework was used to identify redundant steps, measure process improvements, and ensure seamless integration.
- Recommendations:
- Use Lean tools like SIPOC (Suppliers, Inputs, Process, Outputs, Customers) to map workflows and identify opportunities for automation.
- Combine Six Sigma’s data analysis techniques with Agile methods to implement digital initiatives iteratively.
- Monitor digital KPIs (e.g., error rates, processing times) to assess the impact of new technologies.
4. Meeting Elevated Customer Expectations
Organizations must adapt to changing customer demands by prioritizing quality, speed, and customization.
- Example: A logistics company received customer complaints about delayed deliveries. By applying Lean Six Sigma’s root cause analysis and implementing process changes, the company reduced delays by 30% and improved customer satisfaction scores.
- Recommendations:
- Use Voice of the Customer (VoC) tools to gather and analyze customer feedback.
- Implement Continuous Flow and takt time calculations to ensure consistent delivery speeds.
- Use Poka-Yoke (error-proofing) techniques to reduce defects and improve product quality.
5. Building Agility to Navigate Economic Uncertainty
Lean Six Sigma can help organizations remain agile by fostering a culture of continuous improvement and rapid adaptation.
- Example: A retail chain facing declining sales due to economic downturns applied Lean principles to reduce operational costs. By streamlining store operations and optimizing inventory, the company was able to maintain profitability despite reduced revenue.
- Recommendations:
- Conduct frequent DMAIC cycles to address emerging challenges and identify quick wins.
- Use Monte Carlo simulations to evaluate risks and develop robust contingency plans.
- Foster cross-functional collaboration to ensure organization-wide alignment.
Specific Examples of Lean Six Sigma in Action
Example 1: Reducing Waste in Manufacturing
A food processing company experienced significant material waste due to inconsistent production processes. By applying Six Sigma’s statistical tools, the company identified variations in equipment settings as the root cause. Standardizing machine settings and training operators reduced waste by 25%, saving $1.5 million annually.

©Ground Picture/Shutterstock.com
Example 2: Optimizing Healthcare Operations
A hospital faced long patient wait times in its emergency department. Using Lean Six Sigma’s Value Stream Mapping, the hospital identified inefficiencies in patient triage and registration. Streamlining these processes reduced average wait times by 40%, enhancing patient satisfaction and throughput.
Example 3: Enhancing IT Support Services
An IT company’s help desk faced high ticket resolution times. Applying Lean Six Sigma’s DMAIC methodology, the team analyzed data to identify recurring issues and implemented automated workflows for common requests. Resolution times decreased by 50%, improving service levels.
Recommendations for Implementing Lean Six Sigma Post-Pandemic
- Embrace Technology: Integrate AI and IoT to enhance data collection, process monitoring, and decision-making.
- Focus on Workforce Development: Provide training in Lean Six Sigma and digital tools to equip employees with the skills needed for modern operations.
- Adopt a Customer-Centric Approach: Continuously gather and act on customer feedback to ensure alignment with market demands.
- Measure and Monitor: Use dashboards and control charts to track key metrics and identify opportunities for improvement.
- Foster a Culture of Innovation: Encourage employees to suggest and experiment with new ideas for process improvement.
How AI Can Support Lean Six Sigma in Adapting to a Post-Pandemic World
AI enhances Lean Six Sigma by providing real-time insights, automating processes, and enabling data-driven decision-making. In a post-pandemic world, where agility and efficiency are critical, AI helps identify inefficiencies, predict trends, and optimize workflows with precision. Machine learning algorithms can analyze large datasets quickly, pinpointing areas for improvement and supporting DMAIC phases. AI-powered tools improve remote collaboration through virtual dashboards and automated reporting, enabling teams to adapt to hybrid work models. By integrating AI, organizations can streamline operations, enhance process control, and respond effectively to shifting customer demands and supply chain disruptions, ensuring resilience and continuous improvement.
Similar Concepts
Although the COVID pandemic has been over for a while, many organizations still have not returned to doing business as usual. Issues of dealing with remote and hybrid teams are still of concern. These two articles discuss how to handle remote and hybrid teams in the context of Lean Six Sigma.
- This article discusses how to overcome the barriers of communication while trying to drive Lean Six Sigma through a hybrid organization.
- Maintaining the company culture in a remote work environment can also be challenging. This article presents some ideas on how to do that.
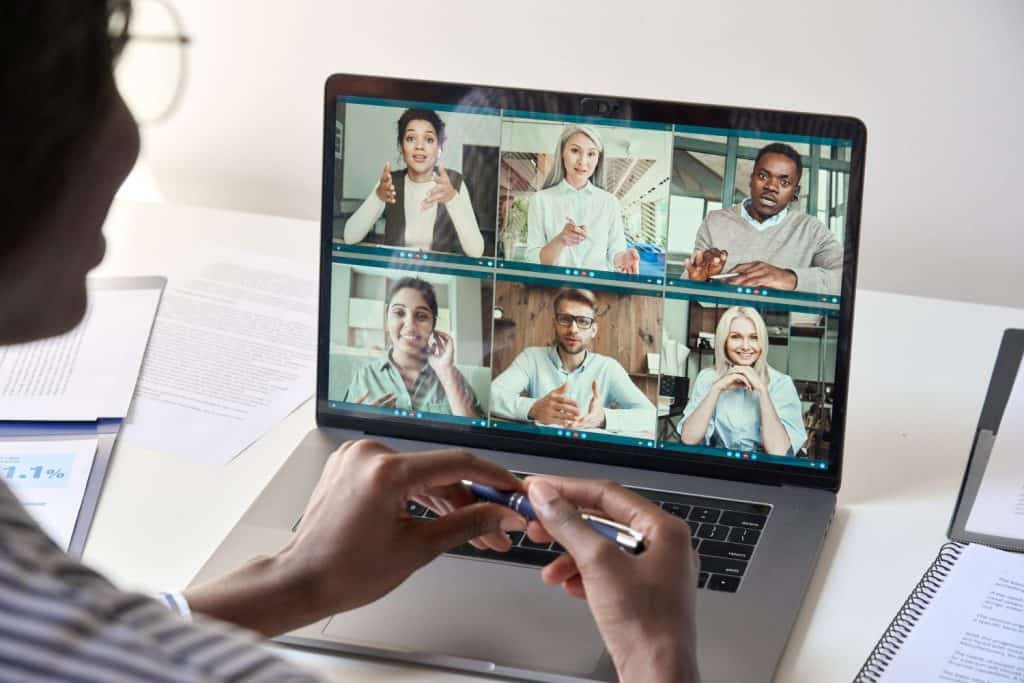
©Ground Picture/Shutterstock.com
Wrap up
Lean Six Sigma is more relevant than ever in a post-pandemic world. By adapting its principles to address supply chain disruptions, remote work challenges, digital transformation, and shifting customer expectations, organizations can navigate the complexities of the new normal. The examples and recommendations outlined in this paper demonstrate how Lean Six Sigma can help businesses enhance efficiency, improve quality, and build resilience in an era of constant change. By embracing this approach, organizations can thrive and maintain a competitive edge in the face of evolving operational realities.
The image featured at the top of this post is ©Sun Shock/Shutterstock.com.