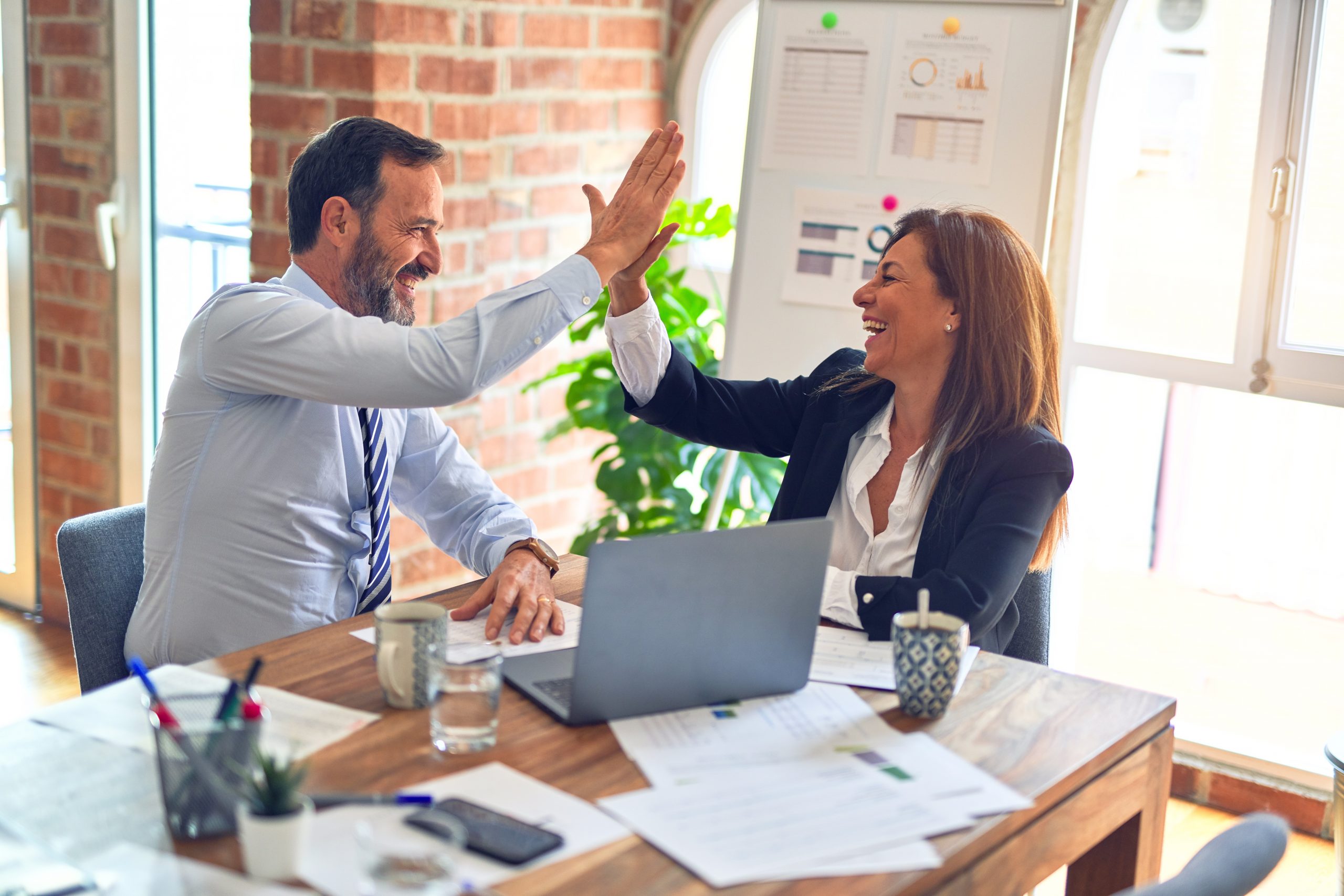
I was privileged to speak at a conference in San Francisco last weekend, sponsored by the American Society for Clinical Pathology. The topics focused on leadership in the clinical (medical) laboratory. After giving a presentation on 6S, I served asa panel member for questions submitted from the audience. One of the questions asked, “What can we do when our leadership tells us we have to do Lean Six Sigma so we can cut employees from the payroll?”
Our panel, in an unrehearsed answer, all chimed in: “That’s not Lean, that’s Mean!!!”
Althoughsome hospitals have been using Lean and Six Sigma for the past several years, it’s stillrelatively new in healthcare. With the threat of decreasing reimbursements from national and private healthcare insurers, and increasing demand for services, you might think lean was a natural fit for improving quality while decreasing costs. However, there were many at the conference who had experience of consultants offering toprove that they coulduse Lean and/or Six Sigma todecrease “the payroll burden.” In those cases, quality seemed to take a back seat to so-called productivity.
Now, my lean training didn’t come directly from a Toyota sensei, but I’ve been informed that, at Toyota, the Toyota Production System is not used to generate layoffs; that the employees who are no longer needed in a certain part of the organization are redeployed, with some becoming dedicated to full-time quality/process improvement.
Can I ask our expert readers to weigh in on this? What should our response be, when confronted by consultants whosell Lean (and Six Sigma) as a way to cut the payroll? Or am I hopelessly naive, in today’s environment, to think that we can retain “respect for people” as an aspect of any process improvement methodology?