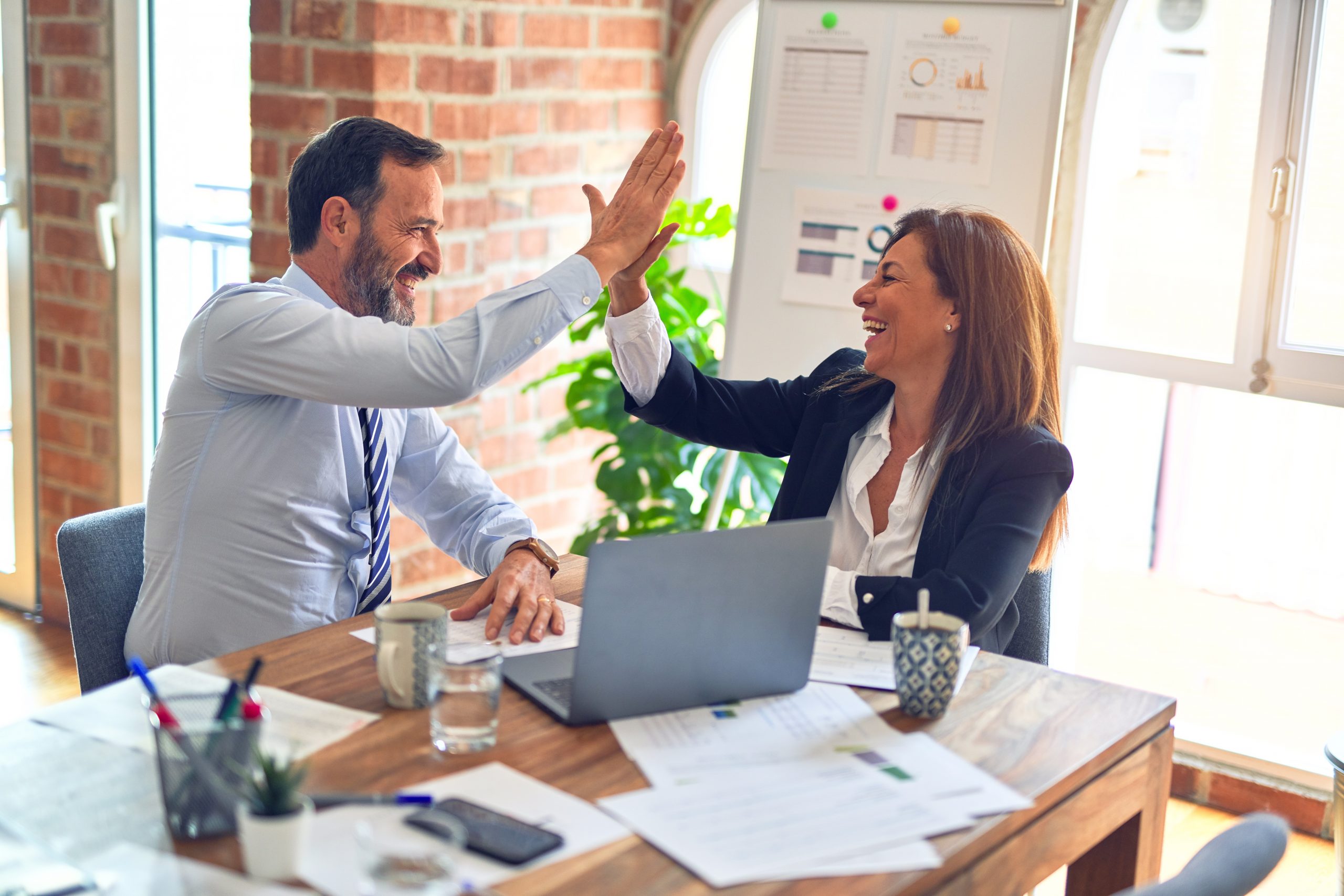
I’ve used the phrase “closest to the customer” when explaining some aspects of lean – for example, starting improvements with the process closest to the customer outcome then working backwards in the process. Lately, I’ve been using the phrase “closest to the worker” to get people to think about removing non-value-added effort from out processes.
For example:a colleague is explaining what happened in a recent “kaizen” event, where office supplies were organized in an area and colored tape was used to indicate the space for every item, such as scissors, rulers, etc. However, they were having a hard time getting people to put things back. The stapler kept being removed to a spot about 20 feet away and being left there – “The people are too lazy to put it back where it belongs.” So I asked a question: What work was being done 20 feet away that needed a stapler? Was it possible that the taped-off space was not located closest to the work, and therefore incurred transportation waste to get the stapler each time? Or, was it possible that there was a need for TWO staplers, one in each area? This question brought up the response that it would be costly to order multiple staplers just to put them everywhere they were needed! It seems to me that if an item is consistently needed in a work area, it’s least wasteful to place it there rather than in a central area.
A similar example involves printers. I know of an organizationthat, in order to save ink cartridge costs, mandated that each department (of 100 – 300 people) have one central gigantic printer; and then they removed all the desktop printers. Now, when you print, you get assigned a code that you take with you to the central printer; enter into the printer; and then it prints your copies. If you are not first in the queue, you don’t know that until you get to the printer. If others are waiting ahead of you, you have the option to wait at the printer, or go back to your station and keep checking. This may indeed save ink cartridgecosts; but what hiddenexpense is being incurred while all those people wait for their printed materials? Not to mention the transportation and motion waste!
Some lean work I have done involved placing printers at each person’s workstation so they don’t interrupt the flow of their work. For example, hospital registration staff who would have to get up in the middle of the registration to copy the patient’s driver’s license an insurance card; or physicians in exam rooms who would have to search out the central printer in order to get a form for a patient (such as discharge instructions, information sheets, or consent forms).
In each case, the hidden costs of waste exceed the supposed savings – the problem is, the expense hits the budget while the hidden costs do not. I think that if we had to pay a dollar for every minute of patient (customer)wait time, or non-value-added worker time, it would soon become obvious where the savings were.
When I was amanager over clerical staff, I saw our office supply costs start to rise dramatically. I was told that people couldn’t find their supplies so theywere coming to the storeroom to check out excess supplies (in order to hoard them, to be sure they always had enough). In the past, I would have mandated some strict supply-sign-out log or allowed people to sign out supplies in a limited fashion (I have seen this done elsewhere). Instead, I bought $1 plastic school supply containers with a snap-close lid. I stocked each one with basic supplies – small stapler, pencils, pens, paper clips, etc. – and gave them to each worker. I ask them to put their names on the boxes and keep them in their lockers, to use each day. And guess what – the supply expenses dropped dramatically and employee satisfaction scores went up. The principle was: place the supplies closest to the worker.
In some ways, this seems like a basic principle to me; but I’ve seensome cases where “lean” has been used to reduce costs as a primary driver, without regard to the hidden costs, so I was motivated to write about this topic.
How about you – can you share some examples of removing wasteful effort from the workers, or do you have a nomination for the “hall of shame?”