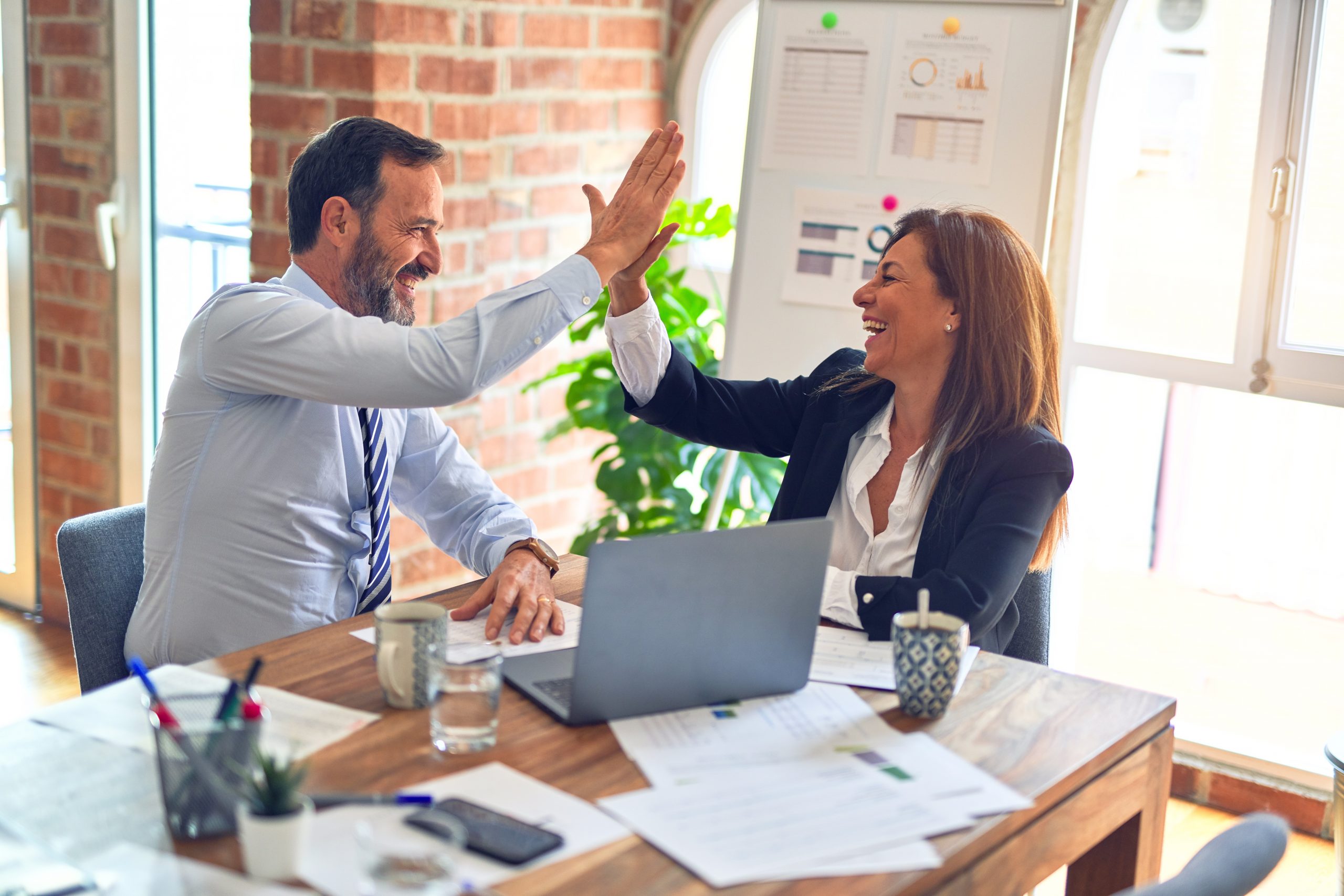
A growing number of organizations are studying the commercial use of radio frequency identification (RFID). Several large companies have invested large sums in RFID development, and companies such as Wal-Mart plan to require RFID compliance from their suppliers. Nonetheless, many companies do not yet have a full grasp of what this technology may mean to them.
RFID Now and Down the Road…
Radio frequency identification (RFID) is a tracking system that uses tags (silicon chips implanted in a product or its packaging) to transmit data to a wireless receiver. One day it could be used to track every commercial product from candy bars to big screen televisions.
The only thing keeping RFID tags from becoming the 21st Century version of the bar code – only much more sophisticated – is the cost of producing them. Until the price of tag chips is just a few pennies each, the use of RFID will remain limited.
Unlike bar codes, which need to be seen to be scanned and require manual effort to be read, RFID tags do not require line-of-sight for data transmission. Within the field of a wireless reading device, it is possible to automatically read hundreds of tags a second.
RFID has been around since the 1940s when the U.S. government began using transponders to “tag” aircraft to tell friend from foe. The government also has used RFID tags to track livestock and nuclear materials.
A number of large U.S. retail companies see RFID as a way to improve supply-chain efficiency and track products from the warehouse to the consumer’s doorstep. It already is used commercially in delivering packages, monitoring rail car locations, handling luggage, tracking food in supermarkets and recording highway tolls.
The trend toward use of RFID is reminiscent of the introduction of ISO9000 certification, which was driven by the major auto manufacturers. Almost all automobile company suppliers ultimately benefited from the ISO implementation through standardization and improvements in quality. Many expect RFID to provide similar benefits.
Of course, the benefits RFID brings to supply-chain management, transportation and item tracking are clearly understood. They are the driving force in the movement toward this new technology. But many companies do not yet realize the value RFID can supply by providing data inputs into a company’s quality management system. RFID data can be expected to be a valuable component of Six Sigma and Lean applications.
Lean is the reduction of waste in a system through consideration of the following categories: overproduction, waiting (man or machine), transportation, process, inventory or work in process, motion and rework. These are areas where a properly managed RFID process can provide usable data for Six Sigma analysis. Figure 1 details a sample three-step process with RFID data collection points.
In this example there are six RFID data collection points representing cycle times within the process. As inputs to the process are received, the items are tagged and collected as RFID data point 1. Between data collection points 1 and 2, the work accomplished in Step 1 is collected at RFID data point 2. A second cycle time is collected to identify the amount of time spent on work in Step 1. This procedure continues through the entire process with data collected at all RFID points.
The data provides insight into:
- The average amount of time spent on work in each step.
- The average amount of time spent on transportation between each step.
- The total time a single item takes to complete the entire process.

This is important as it allows the company to focus on the areas of waste in the process. For instance, if the transportation time between Steps 1 and 2 begins to increase but the time spent on work in Step 2 remains constant and the amount of time spent on work in Step 1 begins to decrease, then Step 1 is in overproduction. Resources can then be leveled by moving some resources to Step 2 in order to reduce transportation time between Steps 1 and 2 and to push through the items waiting for work at Step 2.
As can be seen from this example, RFID data can greatly assist the analysis of a Lean process. This type of data also adds value when applying the Six Sigma methodology to reduce defects in a process. In the example from Figure 1, the work completed in Step 3 represents paint application. The customer identified a smooth coat of paint as critical to quality. Some shipments contained items that did not meet the requirement for quality. An analysis of RFID data from multiple shipments showed that the defective items were created in the same time block across different days.

Figure 2 shows a variation spike in time spent on work during the same time block. The analysis shows that the spike occurs toward the end of the time block.
Further analysis of the RFID data revealed that when the spike occurred all the items were processed by the same employee. The Six Sigma Black Belt determined that the variation was caused by an employee hurrying to complete all work items entering Step 3 before the shift ended, a requirement stated in the standard operating procedures for the process. As a result, less time was spent on each item causing a drop in the quality of the output. The Black Belt also noticed that the number of items transferred from Step 2 increased just prior to the defects occurring in Step 3. A minor change to the standard operating procedures was successful in leveling the product flow between Steps 2 and 3, resulting in the elimination of the defect.
This scenario shows how companies can benefit from the use of RFID data within their quality management system. The application of RFID is limited only by the number of uses targeted by companies. Research is the key to the proper design and implementation of a RFID system. Expending efforts to gain RFID knowledge and simulating its use within the organization will provide the difference between having a RFID system that just meets contractual obligations and having a system that positively impacts the bottom line.