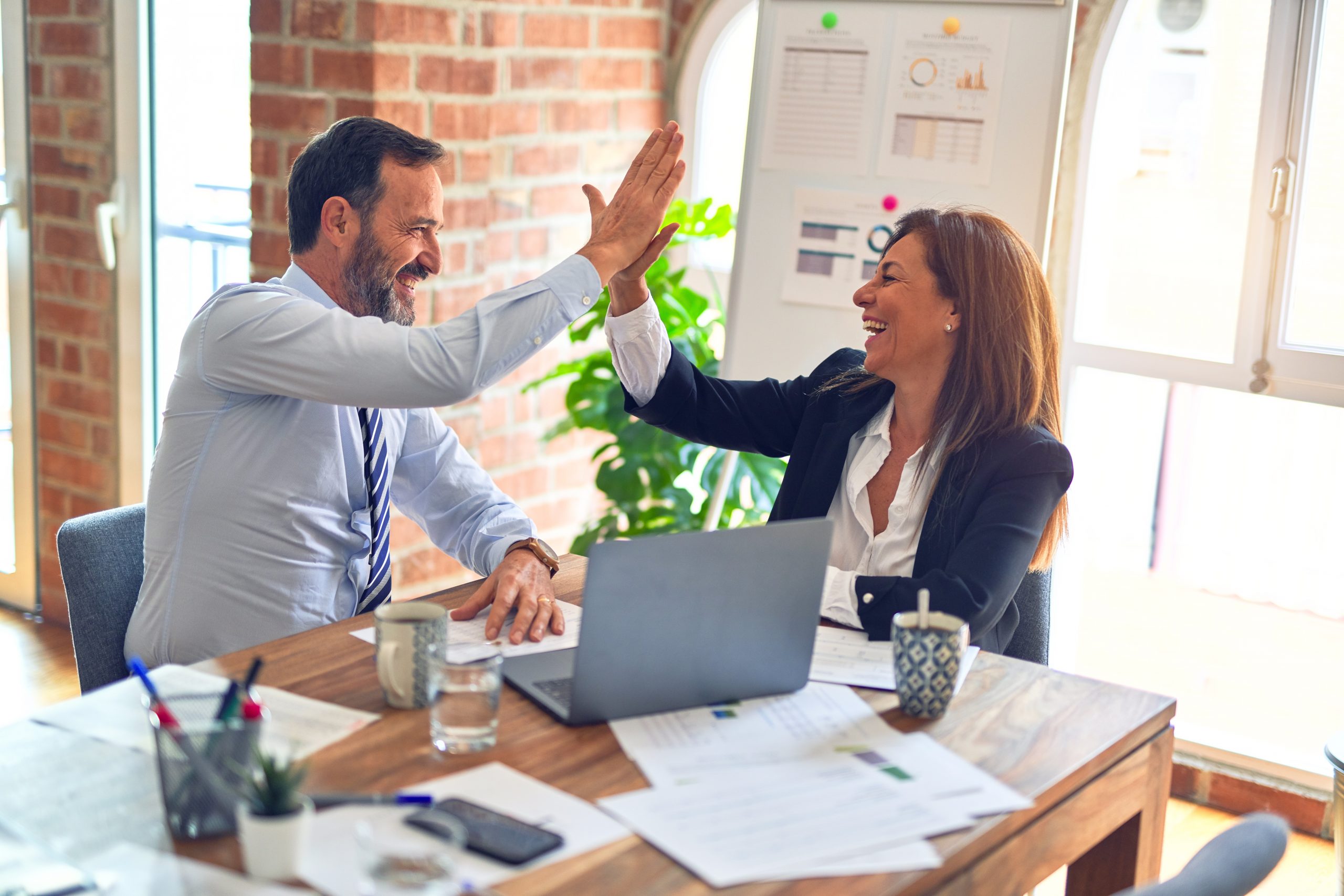
Service, or transactional, Six Sigma has sometimes struggled to keep up with its manufacturing big brother in terms of sustainable results. Lean Six Sigma is currently the approach of choice for many service organizations, but that methodology is under pressure as businesses look to cut costs aggressively to survive the recession. In more than 15 years as Master Black Belts, we have seen hundreds – if not thousands – of transactional processes improved, yet almost all still end with a significant amount of waste, perform at no better than 3 to 4 process sigma and gradually degrade again over time. Another issue in the service sector is that solutions developed in a project’s Improve phase sometimes conflict with various information technology (IT) systems, business changes or desired objectives and therefore cannot be implemented on the grounds of budget or time.
In the ongoing evolution of process improvement and design, Lean has focused on getting the flow and value right, while Six Sigma has focused on customer service and eliminating defects. The next generation of practitioners must build on these achievements and allow for more rapid optimization and automation of the business process. To do this, practitioners can turn to Agile and business process management (BPM) techniques. With Agile Lean-Sigma, organizations can quickly and consistently achieve radical improvements in both cost and process sigma operating performance.
A Challenge to the Accepted Methodology
The Agile Lean-Sigma approach to process improvement is outlined in Table 1. What Agile Lean-Sigma seeks to do is rapidly capture a key business process, optimize it to remove all waste and error, and then automate the process. This work is done using modern Agile development methods and BPM tools.
Table 1: Agile Lean-Sigma Approach to Process Optimization and Automation
Playback | Process Step |
0 | Define process: Optimize process to meet objectives while eliminating waste and re-work |
1 | Build process |
2 | Connect IT infrastructure: Connect process to applications; build applications and databases where they are needed |
3 | Refine: Final configuration and install |
Agile BPM is the antithesis of the sometimes long-winded DMAIC projects that some organizations may consider too time-consuming. Rather than wait for the Improve phase or rely on “quick wins” to provide a solution, practitioners using Agile BPM can capture the process, make radical improvements and go to an executable demonstration of the improved process within a matter of days.
After much experimentation with the Agile Lean-Sigma approach, we have found that the timing for a process improvement and automation is about four weeks. Here is a breakdown of the expected time it takes to complete each step:
- Project initiation: 2 days – standard Define project management
“Playback Zero”:
- Process capture: 2 days – using enterprise collaborative process mapping tools
- Optimization (Lean Six Sigma focus): 3 days – removing all the non-value-added work and designing the new process
- Demonstration: 1 day – putting the process into a BPM tool and showing the outline process flow, roles and decision paths to gain agreement about the new process structure and behavior (The process can be executed, but it is not yet applied to real-world processes.)
“Playback One”:
- Human service coding: 2 days – designing web screens to interface with process actors, capturing and presenting key data fields. This iteration step develops a “working process” so practitioners and process owners can gain agreement about the look, feel and functionality of the process
“Playback Two”:
- Systems integration coding: 5-10 days – this iteration requires that calls be made to the necessary systems so that the human web services can accept and process real data. At this point the process can be executed in full.
The radical nature of process improvement comes from the fact that BPM tools manage all of the process workflow and audits, and because much of the remaining manual work can be readily automated. Lean Six Sigma, on its own, often looks to remove some but not all of the non-value-add work, and does not always make any impact on the business value-add or required work. With BPM, practitioners can sweep away the non-value-added work and let the BPM tool manage the business-required tasks.
BPM Tools Ease Optimization
Some companies avoid deploying Six Sigma and Lean in IT because large system rebuilds are usually run as separate design projects, and small-scale automation or change still tends to be driven from IT rather than the business. How often have you seen a “process” diagram from IT that was more correctly a “data flow” diagram or list of applications?
BPM tools allow organizations to capture and design optimized target processes that are then directly executed using standards-based integration technology. The BPM target process can include read-and-write interfaces to legacy IT systems, and integration with rules engines and human interfaces using web pages, email, social media and Web 2.0 apps.
This BPM ecosystem and IT services toolkit allows anyone, including the Lean Six Sigma or business architect, to assemble an automated process rapidly by using the IT services provided, and as a natural follow-on to the process capture and optimization.
Figure 1: Implementing a BPM Process Layer
IT systems typically also have a large number of process elements (rules, data validation, even workflow) embedded in the code, which can remain outside the control of the organization’s Lean Six Sigma community. BPM enables these elements to be lifted back into the process layer.
For example, in a recent BPM engagement, we automated a finance department’s vendor record change process. Changes to finance records were normally done via paper forms, which were then entered into an electronic database. Because the IT system required specific data codes and had its own structure, validation and rules, the business process had been adapted to fit the system rather than the other way around. We were able to capture and re-design the true business process by building in new business rules to match this process and this data exactly, not the data of the underlying IT system. The interface with the existing IT system was hidden within the BPM layer, where the electronic database rules could match up.
Six Sigma and Lean tools can generate conceptual process models that may be difficult to enforce and measure when implemented. BPM, however, integrates these processes and controls with the IT systems that dictate staff behavior, ensuring that processes are enforced and business rules are applied. BPM also provides real-time reporting on process compliance with statistical information for ongoing process optimization.
Again, in the above example on finance record changes, Sarbanes-Oxley guidelines require that one person requests the change, another person approves the change and a third person makes the change. The primary business rule is: a) do the work in that order, b) no two roles can be taken by the same person and c) make a record of who has done what. By executing the process using BPM software, we cannot only save the effort of moving the work around and auditing who is doing what, but we can also ensure the work goes to the right people in the right order. In addition, because these rules are running in the light BPM layer, they can be changed easily without the need to apply lengthy IT changes.
Benefits of Integration
In our experience, Agile Lean-Sigma supported by BPM provides three key benefits over traditional Lean and Six Sigma: 1) speed and agility, 2) business ownership and 3) process enforcement and compliance. With online process documentation tools, mapping a process can be achieved collaboratively in real time, even with a geographically dispersed team. With this one tool, the same business team can provide supplier, input, process, output, customer (SIPOC) diagrams, process mapping, failure mode and effects analysis, activity documentation, review and feedback, and most of the value stream analysis.
Because the entire end-to-end process is, in effect, being executed by the BPM layer, practitioners can maintain full control of the process, which can be audited through a monitor that captures and reports process metrics. The BPM layer contains the process design and the necessary instructions for execution, which means that the process is always executed as described. There should be no issues with making sure the process runs as it should.
Agile Advantages
Agile development methods enhance Lean Six Sigma in two very important ways. First, Agile accelerates delivery using iterative and collaborative approaches that IT staff typically employ on a daily basis. Second, by disassociating the process from underlying IT systems, Agile enables business to define and change the process with little or no impact upon the IT department. This integration is an outstanding opportunity for process improvement professionals to design and write the process execution without having to hand over control to an IT department.
Borrowing from the Agile (software development) manifesto, we value:
- People and interaction over tools and methodology
- Business/customer collaboration over contracts and negotiation
- Working solutions over detailed documentation
- Responding to change over adherence to a plan
Put simply, this approach means that Agile practitioners can drive BPM work around proactive gemba visits and collaboration, putting a working solution in front of clients quickly – with short, repeated work cycles of weeks or days – and encouraging change and adaptation at all stages. This is not to say that tools, methodology, planning and project charters are wrong; we just find more value in using the iterative Agile approach than using a waterfall approach or adhering strictly to DMAIC tollgates, workbooks and tools.
What Is Ahead
Think of all the transactional process problems that are faced by quality and process improvement teams today: manual tasks, process and workflow that switch between various legacy IT systems, re-keying of data, and rules and decision points that sit outside of systems or cannot be changed easily. Worst of all, many organizations lack automated measurement, monitoring and control systems, so any system changes typically involve a long wait.
These problems can be fixed using the BPM layer approach. This approach not only embraces and knits together the complete business process, but also provides control over data management, decisions, flow, and quality control and measurement. With all process instances being fully tracked, things like audit control, compliance reporting, key performance indicator measurement and collecting information for on-going process improvement can be implemented. Plus, this work can all be done by the Lean Six Sigma team, not simply passed on to technical specialists in the systems function.
The ability to extract and define a process, and then almost immediately execute it using BPM and Agile Lean-Sigma, will likely revolutionize the continuous process improvement businesses over the next few years. Lean and Six Sigma have a part to play, but not in their current shape and format. Organizations can get better results by being clever with BPM technology, and by being Agile with their Lean Six Sigma approach.