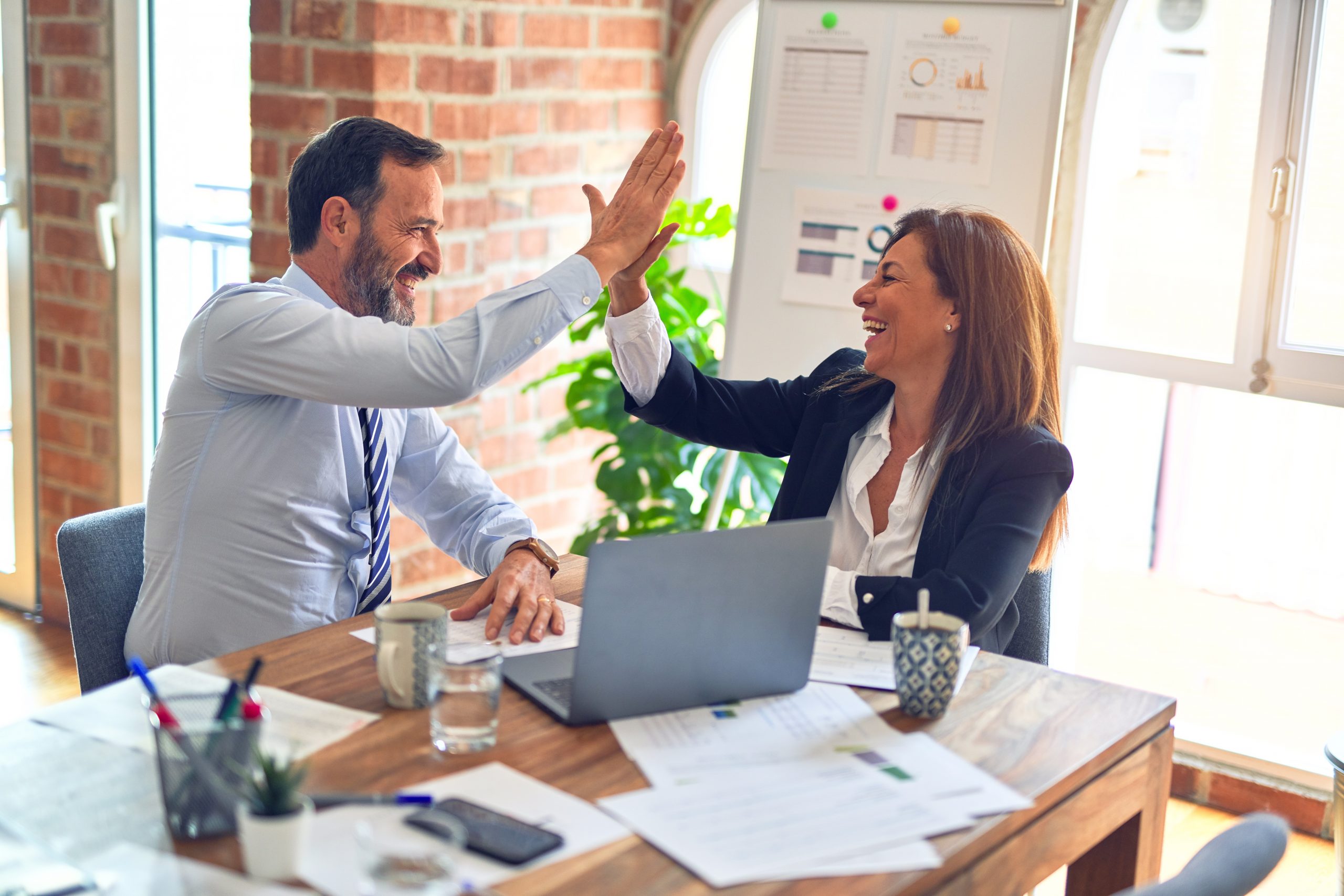
The biomedical world – which includes the equipment used in hospitals, as well as physicians’ and dentists’ offices – is ripe for Six Sigma use. As a senior biomedical engineer and a Black Belt, I embarked on a Six Sigma journey that would provide top-quality service at reduced costs to my customers.
As part of this effort, I implemented a Six Sigma project that involved an upgrade to our preventive maintenance program, which ultimately led to a 79 percent reduction in customer call-backs and a 30 percent increase in customer satisfaction in two years. The following case study explores the development and implementation of that program.
Putting the Pieces in Place
I followed the DMAIC (Define, Measure, Analyze, Improve, Control) model to create the preventive maintenance plan, and gathered as much information as I could during each phase.
Define
A recurring problem in my organization involved customers calling in about medical equipment that had been inspected not more than four months ago based on past preventative maintenance schedule. The purpose of the preventive maintenance was to ensure the integrity and functionality of medical equipment as well as avoid future problems by detecting and resolving any potential issues customers may have encountered. The problems we were encountering caused a displacement in resources (employees, supplies and cost) as well as dissatisfied customers.
I started to wonder: Why aren’t we able to detect and resolve potential future problems while performing preventive maintenance? Why do we have to wait for the problem to occur before we can take care of it? Many of the problems encountered involved medical equipment not holding a charge, such as blood pressure machines or tourniquet systems, and all that needed to be done was change out rechargeable batteries during preventive maintenance. Other examples involved checking for cracked or bad leads in an EKG machine during a preventive maintenance session, rather than simply testing the current for lead leakage. All the problems encountered had the opportunity to be discovered and prevented during a normal preventive maintenance cycle.
Measure
When evaluating a measure, it is important to ensure that the proper metrics are chosen. Valid and reliable metrics are essential to monitor the progress of a project. In this case, several problems were encountered that were all traced back to our preventive maintenance program, so we had to choose metrics that allowed us to measure the level of success of these maintenance sessions.
The metrics chosen were customer satisfaction rate (measured through surveys) and the number of call-backs to the same facility regarding equipment. The plan was to map the entire preventive maintenance process in order to identify the inputs (company resources) and outputs (customer satisfaction). The call-back metric was used because it allowed us to keep track of the number of technicians needed to re-assess and evaluate medical equipment that had already been inspected. Another feature tied into this call-back metric was the ability to monitor time spent on repairs as well as financial losses. These costs were attributable to our inability to bill the customer for equipment that had already undergone a preventive maintenance evaluation within the past four months.
Analyze
This phase involved stratifying the data gathered and then identifying the root causes of the problems. Many of the root causes revolved around the staff’s technical training, defective parts, test equipment calibration, and medical equipment age and usage. Various technicians were assigned preventive maintenance tasks that proved to be outside of their level of expertise, and others failed to report poor quality of parts that were utilized from vendors.
The findings from this Analyze phase illustrate how important it is for senior management to involve all levels of the company when analyzing problems within a clinical setting. In this case, technicians played an important role in helping us identify problems that weren’t discussed previously.
Improve
This phase involved making changes and improvements to our overall preventive maintenance plan. First, we took steps to ensure that our technicians were fully trained and certified. Then we started an annual calibration of test equipment and decided to purchase parts directly from the manufacturer, rather than a third-party vendor. Again, these efforts required all company employees to work as a team and ensure that the processes were properly implemented and the correct tools were used.
The changes that took place involved sending biomedical engineers to medical equipment technical schools for proper training. There, they learned how to effectively troubleshoot, diagnose and repair faulty equipment, as well as how to perform a thorough preventive maintenance. The engineers would then cross-train other technicians to ensure that all staff received the necessary training based on the manufacturers’ recommendations and risk levels. In addition, critical parts such as motors, assemblies and compressor kits were ordered directly from the manufacturer. Other improvements included performing a life-cycle cost analysis, which involved evaluating the medical equipment for clinical effectiveness, patient safety and human factors before making a decision to release it.
Control
In the final phase of the project, we monitored all actions taken to ensure that the process put in place was fully implemented by all members of the company. We purchased a preventive maintenance management software program, which helped keep track of work-order flow, preventive maintenance scheduling, asset histories, and inventory and budget control. The software also monitored metrics such as cost, call-backs, and overall hours and history spent on medical equipment preventive maintenance and repair. The software helped keep a record and history log that was both equipment-specific and employee-specific.
The Final Results
After being in place for two years, the DMAIC-based strategic plan has optimized our preventive maintenance process and assured high yields with minimal losses. Implementing Six Sigma in the biomedical engineering field means more than simply delivering defect-free medical equipment service or inspection. It also entails providing safe, effective and reliable equipment that is able to contribute to the overall improvement of quality patient care.
The DMAIC project consisted of improving operating processes while also maintaining statistical control over input and output variables. These improvements enabled us to maximize our equipment uptime and optimize our overall preventive maintenance schedule. Six Sigma has helped our company expand by not only reducing cycle time, but also – more importantly – optimizing response time to work orders and foolproofing our overall reports.
The updated preventive maintenance program cut the rate of call-backs and improved customer satisfaction. Six Sigma also helped reduce the variability among technicians and engineers and unify the way we do business. Our preventive maintenance program now covers a broader range of services to ensure that we are able to prevent any malfunctions or operational defects from occurring. We now test not only the unit itself but also the accessories, such as leads, wires, cables, vital-sign monitor connections, batteries and other disposable components. This ensures that our technicians will not have to go back in a few months to resolve equipment issues.
The improvements also had a positive effect of the overall satisfaction of our clients. Our call-backs decreased from 512 in to 108 – a 78.9 percent reduction in two years. Based on satisfaction surveys collected from our customers, we averaged a 62.5 percent customer satisfaction level initially. Two years after implementing Six Sigma, our customer satisfaction scores rose to 92.3 percent.