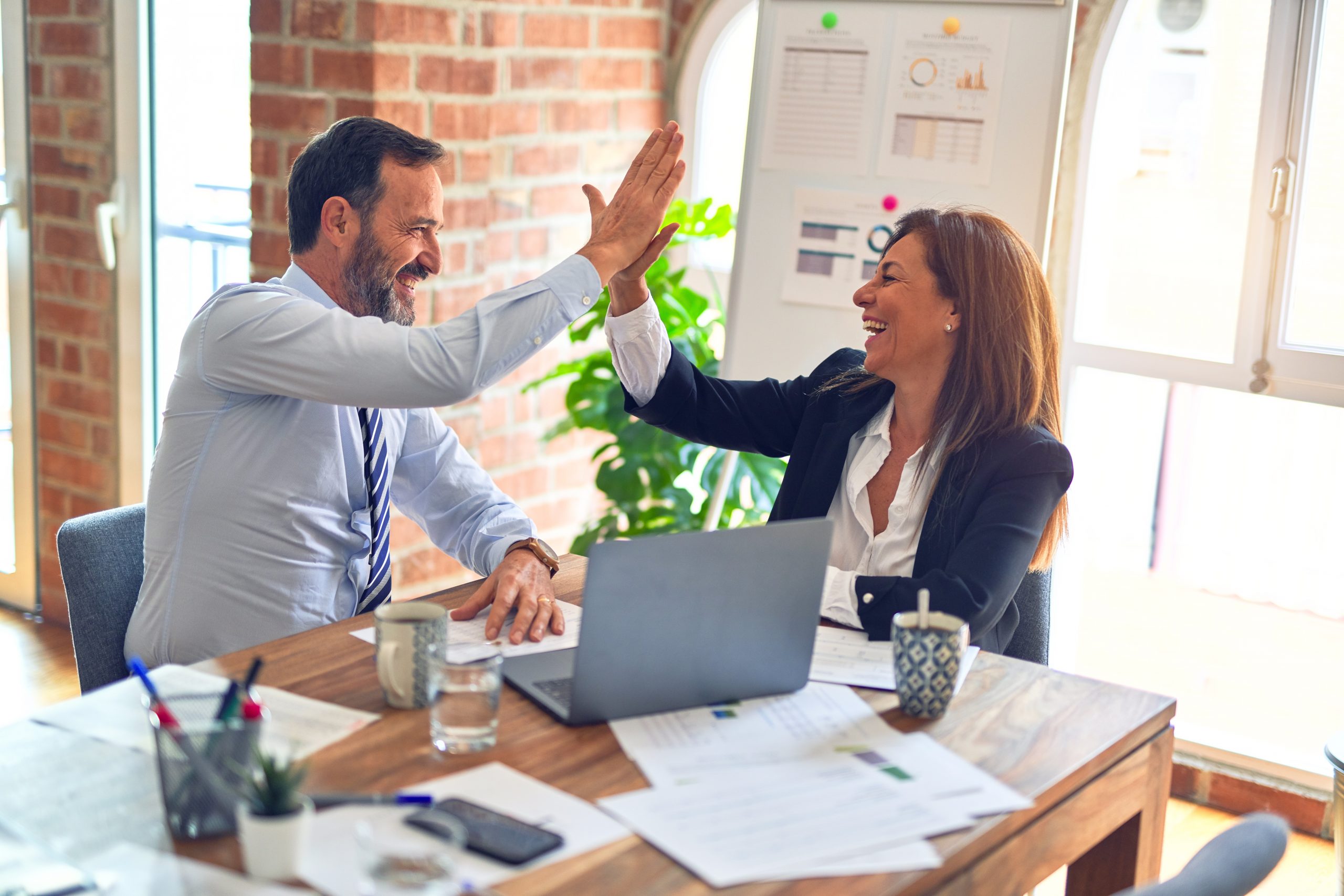
With many companies integrating Lean and Six Sigma methodologies into a single improvement tool kit, value stream mapping has emerged as a preferred tool to identify process improvement opportunities. A number of valuable points can be made about applying value stream thinking to project selection across a range of industries and processes both in the United States and in Europe. They include:
Understand the Overall Goal
The power of value stream thinking lies in looking at an entire business process. With the typical Lean or Six Sigma project focusing on fixing a specific issue in a narrowly defined process, it is critical to have an overall perspective for selecting what projects to tackle. Even more important, value stream mapping not only includes defining the current state, but also includes defining the future state and the gaps between the two.
With a clear picture of how the entire process should operate in the future, it is relatively easy to identify the projects that will close the gap. For discrete manufacturing processes, the ideal of continuous flow often drives the design of the future state. For process manufacturing and administrative processes, the characteristics of the future state are often less well-defined and require a strategic perspective. For example, using value stream mapping for mapping core human resources (HR) processes forces the business leadership team to decide on the future service delivery model – to what extent should the business adopt a self-service approach, what tasks will be performed by HR specialists versus local generalists, etc.
When developing the future state, it is crucial to define the overarching goal for the process that will guide the design. For a staffing process, the goal might be filling a position in less than two months. For a pharmaceutical filling operation, the goal might be to achieve a higher number of fills. A clearly defined business goal for the process provides the perspective that drives the design.
Understand the Real Constraints
When developing the future state, it is critical to understand the real process constraints of the current state and to evaluate to what extent these constraints will remain in the future state. For example, developing the future state for pharmaceuticals manufacturing needs to consider the time required to validate new equipment. A typical future state map describes the state of the process 12 or 18 months from now. If it takes 30 months to get a new piece of equipment in place and validated, the current equipment becomes a constraint for the future state map. Some constraints are real, others are only imagined. For example, headcount should never be a constraint.
Focus on Projects That Help Achieve the Goal
When analyzing the gap between the current and future states, one should focus only on those projects that will help achieve the overall goal. In many instances, the improvement plan is filled with projects that have no clear link to the overall objective. Most companies have only limited resources at their disposal; therefore the available resources should be concentrated on those projects that really need to be done.
Define the Options
In almost every instance, there are several different paths to achieve the future state and meet the overall process goal. For example, when focusing on capacity increase at a bottleneck machine, this goal could be accomplished by reducing process cycle time, unplanned downtime, changeover times or process yield. Defining the alternative “project packages” is helpful to understand the trade-offs and make smart resource allocation decisions.
Integrate Existing Initiatives into the Plan
Initiatives and projects already under way or planned for the foreseeable future need to be integrated into the overall plan to the extent that they impact the future state. However, one needs to be careful and review whether the deliverables for these initiatives are realistic.
For example, a company which was mapping its manufacturing process identified two projects that were expected to yield a substantial reduction in process time. However, when the team reviewed these projects it became obvious that the impact expectations were very unrealistic. When putting together an inventory of these current or planned projects or initiatives, the team should ask itself: Are the objectives for these projects clearly defined? Are these initiatives on track to deliver the expected results? What is the risk of these projects failing? Especially when it comes to technology projects, reviewing the track record of similar projects in the company can help to understand whether the team should count on successful completion or not.
Be Creative and Adapt the Approach to the Situation
Value stream mapping typically focuses on a product family. However, in many instances the concept of product family is limiting. In many process industries, the equipment is not dedicated to a certain product or family, and processing paths can vary from run to run. Similar issues arise in many service processes – for example, when customers can choose between various channels (Internet, phone, email, etc). Focusing narrowly on a product family does not really provide much insight into the improvement opportunities available. In such cases, the value stream perspective can be enhanced by combining the mapping with other tools such as bottleneck analysis.
Value stream mapping is a powerful tool that helps to identify the vital few Lean and Six Sigma projects that will yield the highest value to the process in question.