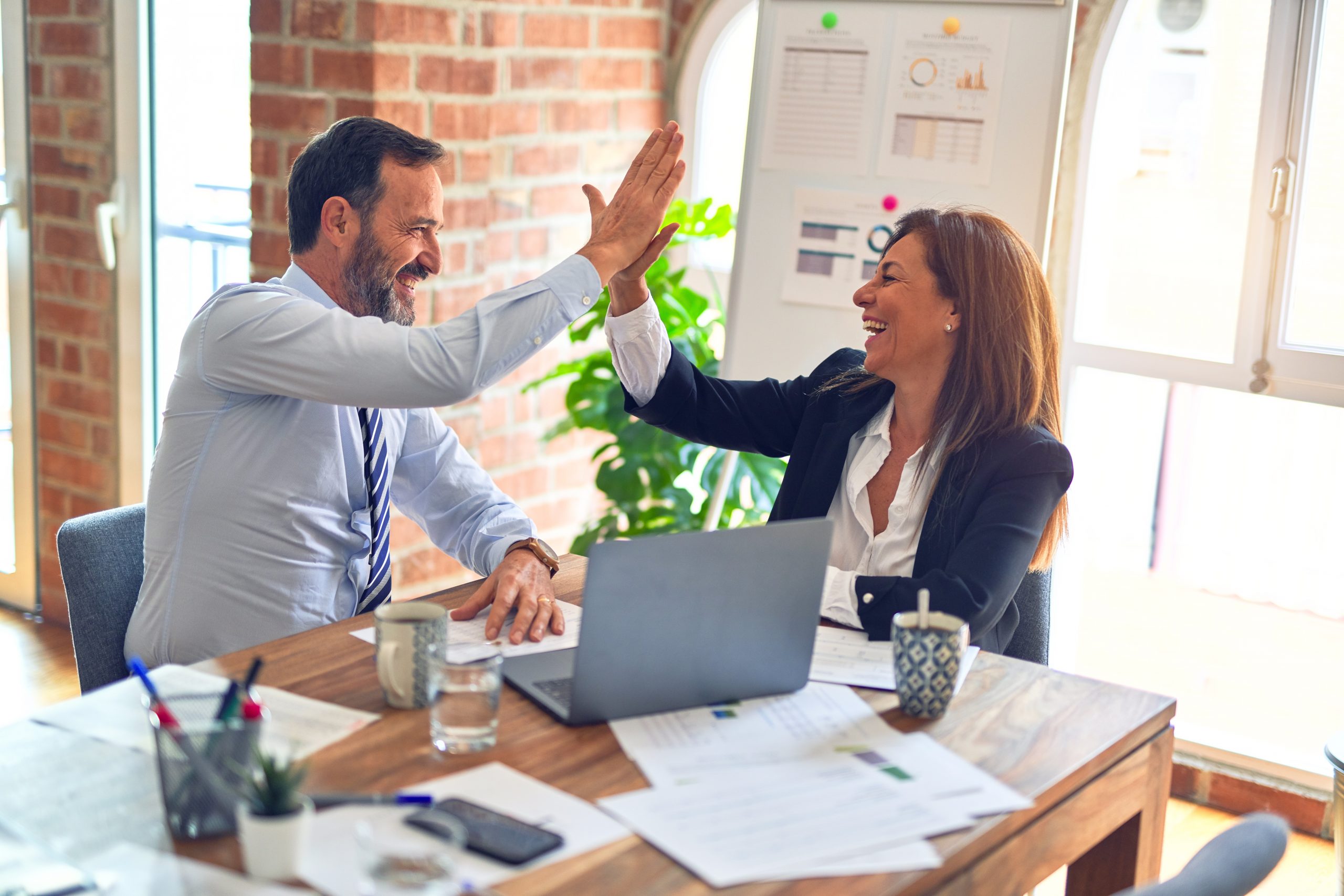
Lean Six Sigma projects are a learning journey and, unfortunately, despite practitioners’ best efforts, projects can become delayed on their way to completion. A number of reasons may contribute to project delays, such as the occasional unforeseen organizational crisis due to business, operational or personnel issues. The conventional management response to delays is to arrange for more detailed project reporting, followed by reviews looking at milestone achievements versus original targets. This strategy can result in a reprioritizing of resources, a reinforcement about the importance of the method, a reallocation of responsibilities or a reconsideration of whether Lean Six Sigma is a good fit for solving the problem at hand.
While these actions may address the symptoms of the problem, they do not always address the basic root causes of delays. In a busy, multi-site organization, the resolution of delays can take additional time (extending the project timeline), consume specialist resources and lead to frustration among the Lean Six Sigma teams. However, in the following case study, a project team discovered the benefits of putting aside time to work on this issue. By using a current reality tree, the team was able to analyze progress slowdowns and determine solutions for keeping projects on track.
Understanding Undesired Effects
To gain more information, the Lean Six Sigma team that investigated the causes of project delays started by looking at:
- Force-field diagrams supported by stakeholder analysis
- Lessons-learned evaluations from tollgate meetings relating to delays
- Balanced scorecards showing the improvement rate of the key performance indicators
- Creative brainstorming about delays, which were used to create a cause and effect diagram
This information provided some insight; however, in a dynamic organization, where actual processes are not always transparent, the real root causes and controlling factors were not evident. Matrix management structures, sub-contracting arrangements, differing personal work styles and geographical separation added even more layers of complexity. The consequences of these factors tended not to be visible because they were ingrained habits of individuals.
The team decided to use a current reality tree because they believed it would be a more objective and efficient method for drilling down to the root causes of delays. This is how the tool works:
- The team defines the project performance characteristic to be evaluated.
- Four to five people are selected as the core evaluation team. These people should be familiar with the tools and committed to the approach.
- To start construction of the current reality tree, each team member identifies five to seven consistent organizational or individual behaviors that negatively impact the project performance indictor selected in the first step. These negatives are called undesired effects (UDEs).
- The team constructs the current reality tree with these inputs using if/then logic (i.e., if this behavior occurs, then this effect results) to link the various UDEs.
- If a UDE contains more than one idea, or if additional UDEs are required to simplify the links between them, the team should refine the inputs.
- The team finalizes the relationships between the revised UDEs to finish the current reality tree.
The objective in creating the current reality tree was to identify the few root causes of delays that are under the organization’s control and to develop appropriate countermeasures. The team did not address other issues – such as changing customer requirements or insufficient resources – as they were considered boundary conditions.
Benefits of Current Reality Tree
Besides identifying root causes, the team experienced a number of other benefits from constructing the current reality tree:
- The team was able to improve dramatically the definition of each UDE. Originally, some UDEs needed to be rewritten because they contained multiple ideas or were not specific enough. The interaction between the various UDEs became easier to understand because of the visual representation. This enabled the team to organize their thoughts and thus improved their ability to communicate concerns to the broader organization.
- The relationship between various organizational factors (i.e., where they appeared in the tree and where they did not) helped improve the team’s ability to identify specific root causes.
- The presence and impact of negative reinforcement loops was an eye opener. The team realized that by simply removing these negative cycles, they could bring about dramatic improvement.
- Some effects that the team initially felt to be important did not pass the rigor of the if/then logic, clearing them to be addressed by other means.
At this stage, the current reality tree included about 70 UDEs. The UDEs could be categorized into five main groups:
- Real resource issues – Even with the high return on investment from Lean Six Sigma projects, individuals involved in projects sometimes became fully occupied by short-term firefighting. Irresistible short-term business needs were present that were not evident to the line manager.
- Mismatches between responsibility and authority – These issues were quite evident in parts of the organization. There was a recurring need to organize multiple escalation meetings in order to resolve issues.
- Lack of data – Data needed to support appropriate decision making was simply not available in a usable format. Practitioners made decisions based on the understanding of a few newsworthy events rather than rigorous, objective analysis of the full data set.
- Ineffective communication – The practical need to communicate effectively overwhelmed the project team’s ability to function. The effort needed to share data and progress in a timely manner within a large international organization, with matrix management across multiple time zones, was much higher than expected. The scope of the project needed to be reduced.
- Slacking off – Even though the organization had formally accepted Lean Six Sigma techniques, individuals tended to drop back to familiar, but admittedly less effective, ways of managing processes. For example: Parallel efforts were initiated based on premature conclusions, requests for data collection needed to be repeated, and the rigorous Improve and Control phases were skipped, resulting in premature reduction of project support.
The team presented the main conclusions from the current reality tree using a force-field diagram, which summarized the root causes. A sample of the current reality tree is shown below.

Maintaining MomentumÂ
The advantage of using this approach was that it offered a rigorous, objective method to understand the root causes of slow progress within Lean Six Sigma projects. After completion, the deployment team felt that the somewhat fuzzy topic had been transformed into operational tasks. They had defined achievable actions that were supported by rigorous, logical and transparent paths to the objective of reducing additional controversy.Â
The workload and commitment for this type of analysis should not be underestimated. Because it reflects the culture of the entire organization, the current reality tree will inevitably be complex and will require several days to construct. The tree diagram requires an owner who is dedicated to the task; beyond this person, the deployment team as a whole must be committed to the rigor of constructing the UDEs and their numerous interactions.
Maintaining the momentum of a Lean Six Sigma program is crucial in order to reduce the doubt, skepticism and cynicism that can creep in when the program appears stalled. The effort required for this use of a current reality tree is far less than typical alternatives, such as additional training, more use of consultants or personnel shuffling – none of which address the root causes. Also, this technique was preferable to a re-launch process, where the original deployment kickoff is repeated with additional emphasis; if issues were missed on the original launch, they also may have been missed in the re-launch. Even for healthy deployments, improving the speed of project execution brings more financial benefits and an improved bottom line.