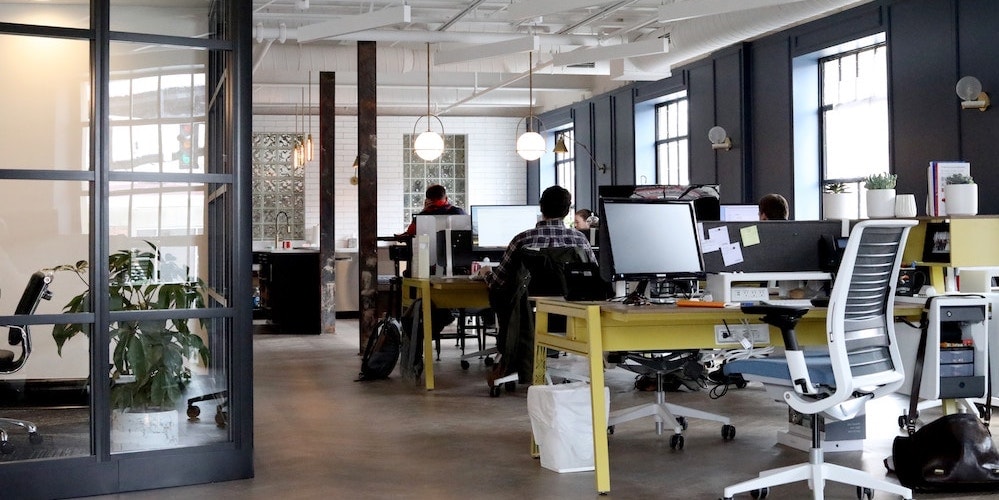
Just like in operations, manufacturing offices such as engineering, purchasing and others face flow challenges – including employees constantly making subjective decisions and judgment calls about which tasks are most important. With team members filtering priorities through their own, often unique, prioritization mechanism, it is nearly impossible to connect processes to create flow that moves information between people, departments, suppliers or customers at a predictable cadence so that the product is delivered on time.
The principles and guidelines of operational excellence, however, enable a company to design the way an office functions so information flows from activity to activity along fixed pathways at preset, predefined times. That way, everyone knows where to get their work from, when to expect it, and where and when they should send their finished work.
By designing the way information in an office should flow (“normal” flow), any flow condition outside of this design can be defined as abnormal flow. And that distinction is central to operational excellence since things will go wrong. It is how an office operates when things go awry that matters. Typically, when flow starts to become abnormal, management intervenes to help fix the problem or problems. If managers cannot resolve the issue quickly, they call a meeting – or multiple meetings. This process can take a lot of time and effort. Instead, when an office achieves operational excellence, the time that management spends overseeing the services the office provides can be greatly reduced. In fact, the need for management intervention will be almost eliminated. The office will run autonomously.
Eight Steps to Operational Excellence
Organizations can achieve operational excellence by following eight principles – in order:
- Design Lean value streams: The objective of this principle is to design on paper an end-to-end Lean value stream flow, starting from the time an order or request for service is received from the customer until it is delivered.
- Make Lean value streams flow: The next step is to take the design from paper to performance, beginning with formal education. After training, employees use standard Lean tools to achieve the designed future state.
- Make flow visual: To create operational excellence, flow must be made visual so that each employee can see how processes are connected to one another and to the customer. In operational excellence, there are two categories of visuals for flow: static and dynamic.
- Create standard work for normal flow: Once visual Lean flow allows employees to see how the flow should normally work, the next step is to apply standard work at, and between, the processes so that every employee will know what to do and when to do it.
- Make abnormal flow visual: In operational excellence, the intent is for all employees to be aware before abnormal flow happens so they know not only how to correct abnormal flow but can also prevent it from occurring in the future – without the intervention of management.
- Create standard work for abnormal flow: When flow breaks down, what is important is how an operation responds. The key is to establish standard work to get the flow back on track by having employees record the types of abnormal flow that have occurred and management’s responses to them. That way, people in the flow can take these actions automatically.
- Have employees in the flow improve the flow: Once a design has been implemented, the employees who work in the flow should use proven continuous improvement tools to support and improve the design of the flow to prevent abnormal flow from occurring.
- Perform offense activities: Operational excellence is about business growth. By designing self-healing, autonomous flow that employees can fix on their own, management can step away from running the operation and spend more time on growing it by performing offense activities.
Nine Guidelines for Office Flow
Within the first principle, which sets the stage for working through the others, there are nine guidelines to create flow in manufacturing offices that must be applied in the sequence listed. An organization applies each of the guidelines to a “process family,” or a service that goes through similar processing steps and has similar work content.
- Takt and takt capability: Takt time is the rate of customer demand. In the office, the unpredictability of both the volume and nature of requests can make it challenging to predict demand. In these cases, takt capability is used, which means setting a capability of what can be done (like how many quotes could be completed in a week) in terms of mix and volume.
- Continuous flow: In an office, continuous flow means completing one activity and moving the work on to the next process in the flow, without stoppage or interruption. Continuous flow eliminates the self-prioritization of work that commonly occurs in offices by establishing part-time processing cells that meet throughout the day or week at preset times.
- First in, first out (FIFO): FIFO is a form of flow that provides the physical pathway on which information moves for each service family between processes. FIFO preserves the sequence of work and eliminates the shuffling and reprioritizing to create predictability around when each job will be completed.
- Workflow cycles: Workflow cycles refer to the rate at which work moves or flows within or between different work areas or departments along a fixed pathway. They dictate the time by which work should be completed and help stabilize the flow of information in the office. When set up correctly, they yield a guaranteed turnaround time (GTT) for the flow, which eliminates chasing information, status meetings, and emails.
- Integration events: When information does not need to flow on a regular or consistent basis but rather only every quarter, for instance, an integration event is used to hand off a large amount of work from one area of the company to another area or to an outside service.
- Standard work: Standard work ensures that flow is repeatable and predictable, no matter who performs the work. At the activity level, it is created by identifying and setting the work content, tools, systems, forms and other information needed and the sequence required to complete the work. Flow-level standard work describes how each process connects to the next process, what path information will follow, when it should move along and so on.
- Single-point initialization: To eliminate reprioritization of work based on personal preferences or changing management priorities, an organization should try to set one point within the value stream at which work is introduced from outside the value stream by the customer, which is called single-point initialization.
- Pitch: Pitch is a tool that enables anyone to easily see if flow is operating normally and on time to customer demand without having to interrupt or ask questions. In order for everyone to see if pitch has been made or missed, it is important that it be visual.
- Changes in demand: When demand fluctuations exceed what the value stream can handle, the first step is to determine if they are due to a temporary fluctuation in demand or a true, permanent increase (or decrease). If it is a true change, then the operation needs to switch to another pre-established takt capability and operate according to standard work to handle the change. Then, when demand stabilizes, the office would switch back to takt capability one.
Autonomous Flow
Once a designed flow is implemented, along with visuals in place that tell employees if the flow is normal or abnormal, an organization needs to teach those who work in the flow how to recognize when abnormal conditions have occurred and to consult their standard work to correct them so the office can resume operating under normal conditions. The result is a self-healing value stream that flows work and information seamlessly and autonomously, eliminating the need for management intervention.
Manufacturing offices with self-healing value streams realize many benefits:
- A reduction in the number of meetings, including status updates or those to prioritize work
- The elimination of expedited requests
- A decrease in emails and phone calls to clarify work or chase information
- A reduction in interruptions
- The elimination of the need for management oversight
Another benefit: once management is removed from the day-to-day oversight of office processes, it can focus solely on business growth. That means it can meet with customers and potential customers, focus on voice of the customer and innovate new products and services with customers. In essence, management can take on a more strategic role to better position the company for the future.