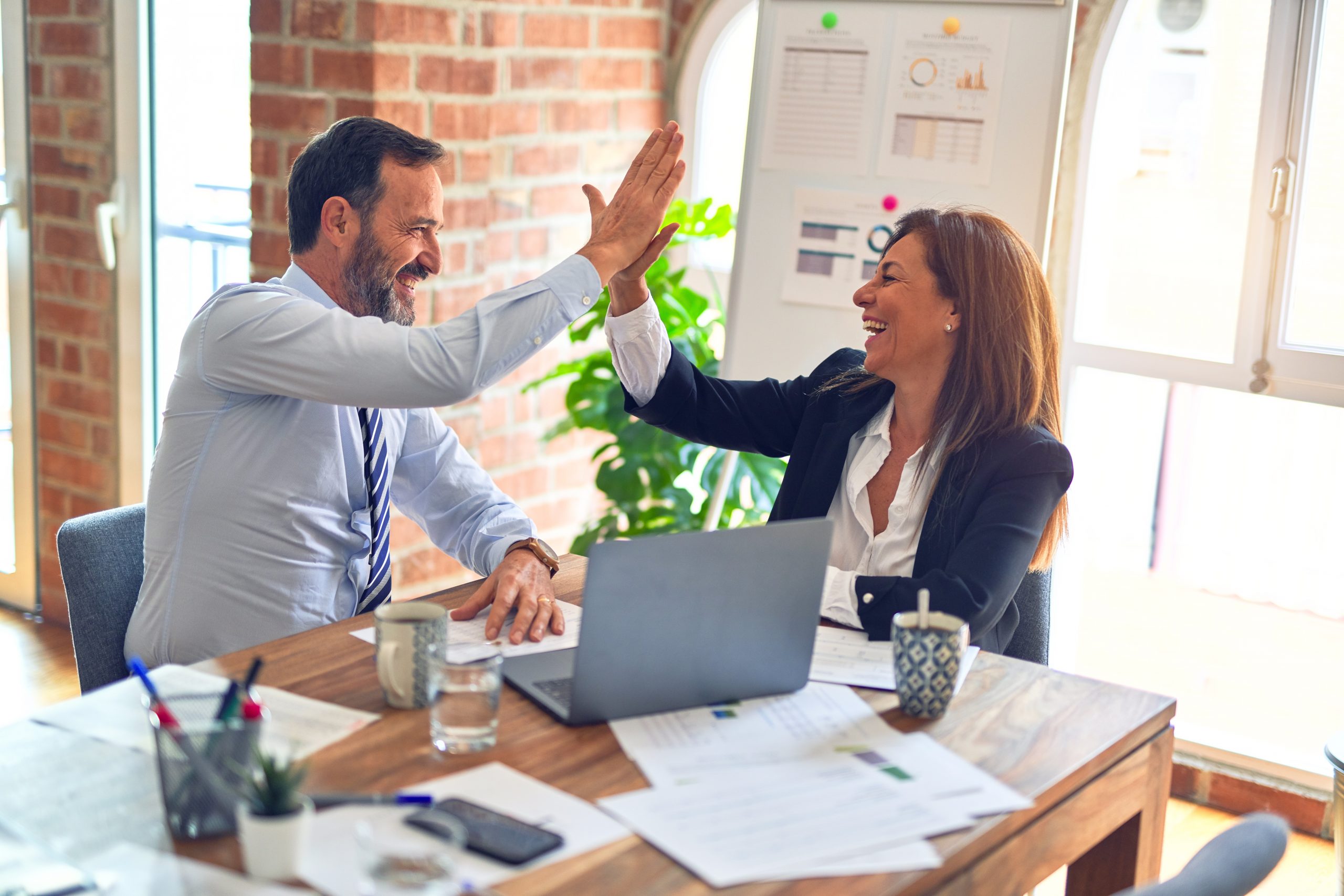
At a high level, there is usually agreement on the big issues in any healthcare organization. Through observation and feedback alone, key stakeholders may realize there are problems with excessive wait time in the emergency department, or that the first surgical case of the day rarely starts on time, or that it is taking too long to discharge a patient.
Consensus begins to break down, however, when the discussion turns to why these things are occurring. Everyone may have their own opinion on the subject. Instead of rounding up the usual suspects, resorting to finger-pointing or relying on intuition, improvement teams should trust a statistical method such as Six Sigma to identify and address the real source of the problem.
On the journey to performance excellence, many healthcare organizations have discovered the value of accurate measurement. Pursuing an evidence-based process, they have been able to uncover root causes and implement changes that stick. Once they had access to verifiable information and were able to measure what was really taking place, hospital process improvement teams have been able to either substantiate or disprove their initial assumptions.
Examples of the Value of Measurement
For instance, one hospital team working on a project to reduce errors in medication administration actually discovered a lower error rate than initial data collection had indicated. Using statistical analysis and digging a little deeper into the issue, they found the problem was really a lack of consistent documentation. It turned out that the involvement of multiple people in the process and the need for standard operating procedures were the real underlying factors. In other words, the team found that in this particular case, patients were usually receiving the right medicine at the right time, but the process was not always documented in the right way. Lack of proper documentation is a common problem and one that can present problems regarding compliance with regulatory requirements.
Another hospital had begun a Six Sigma project targeting the staff scheduling process in one of the nursing units. Prior to this effort, management had assumed it was not meeting budget targets for staffing due to the use of the Family Medical and Leave Act, sick leave and vacation leave; the result being additional overtime and usage of agency nurses. Here again, the statistical analysis was helpful in disproving such assumptions. Measuring the data and gathering voice of the customer (VOC) information through working sessions, the project team found that several factors were behind the staff scheduling challenges, including technical and compliance issues with the staffing matrix, along with resistance to rotation practices in and out of units. This knowledge allowed the team to develop and introduce viable solutions.
Right Path or a Dead-end Road?
Accurate measurement within a Six Sigma project can point out predictable peaks and valleys that may be managed with appropriate planning. It also can alert project teams to an unexpected increase in process variability that might require intervention. In some cases, the data will support an original hypothesis – but often the evidence will uncover sources of variation or poor process capability that would have gone unnoticed without the use of statistical tools.
Careful data collection and analysis helps to ensure the project team is focusing on the right things. One of the most common mistakes a team can make (especially when its members are somewhat new to the Six Sigma approach) is to invest significant time tracking data on the wrong trail. Team members may spend days and weeks manually collecting data, only to discover they are measuring something that is not germane to the outcome of the project.
This type of wild data chase can be frustrating, but it is best to quickly recognize and correct the situation. Gathering sufficient VOC early in the process and using tools such as the fishbone diagram can help to avoid the dead-end road scenario.
If measurements do reveal the team is on the wrong trail, the team leader will need to be flexible enough to reevaluate the project, and make sure they are using the most appropriate tools and information. Some project teams have found the need to take a temporary detour from the DMAIC structure to bring in Lean concepts, conduct Work-out sessions or identify another source of data.
Measurement System Analysis
There are a variety of questions that should be answered before a team moves ahead with a project. The first question is whether the issue is strategically aligned with business priorities. Secondly, is this truly something that requires the rigor of Six Sigma? Then:
- Does the team access to the right data?
- Will there be sufficient data points to measure defects and subsequent improvement?
- Are there multiple data sets that produce conflicting information?
- How will this be reconciled?
Measurement system analysis (MSA) uses tools such as Gage R&R to help the project team validate the data collection method it plans to use. Once this is verified and any conflicts have been resolved, the team can proceed with greater confidence in its approach and decision-making process. The MSA plan will include identifying data sources, the person(s) responsible for data collection and analysis, instruments or methods to be used, and reconciliation of any contradictory data sources.
Measuring to Stay on Track
Obviously, measurement does not take place only during the Measure phase of a project. Process mapping can help to measure steps, handoffs, travel time, wait time and so on. Measuring process capability before and after solutions have been implemented helps to quantify results.
Once a project has entered the Control phase, continuous monitoring and measurement will be the key to sustaining the gains. Did the adjustments work? Is there a significant difference between baseline performance and the new process capability? If the target was not reached, is there a need to recalibrate? Does the data point to other issues that need to be resolved using Six Sigma, Lean or Work-out tools? Continuously re-measuring after a project is considered complete ensures accountability and can help to further strengthen the business case for pursuing similar efforts across the organization. Many teams have found that while they were pleased with the initial progress they were able to achieve during the Improve and Control phases, the results may be even better when measured again several months later.
For example, one hospital completing a project targeting pressure ulcers reported a reduction of 50 percent at the close of the project. Within a year they were able to quantify further improvement with roughly a 75 percent reduction in pressure ulcers and an additional $1.2 million in annualized financial benefit to the organization.
It is possible to turn the most unyielding skeptic into a supporter by demonstrating that solutions have been guided by scientific methods and valid data. Six Sigma helps to drive change by taking common issues out of the fickle realm of opinion and placing them in a solid, fact-based framework.
In any improvement initiative, perception and reality may be miles apart. Ensuring accurate measurements at each milepost can help to shorten the distance and keep the project and results on the right track.