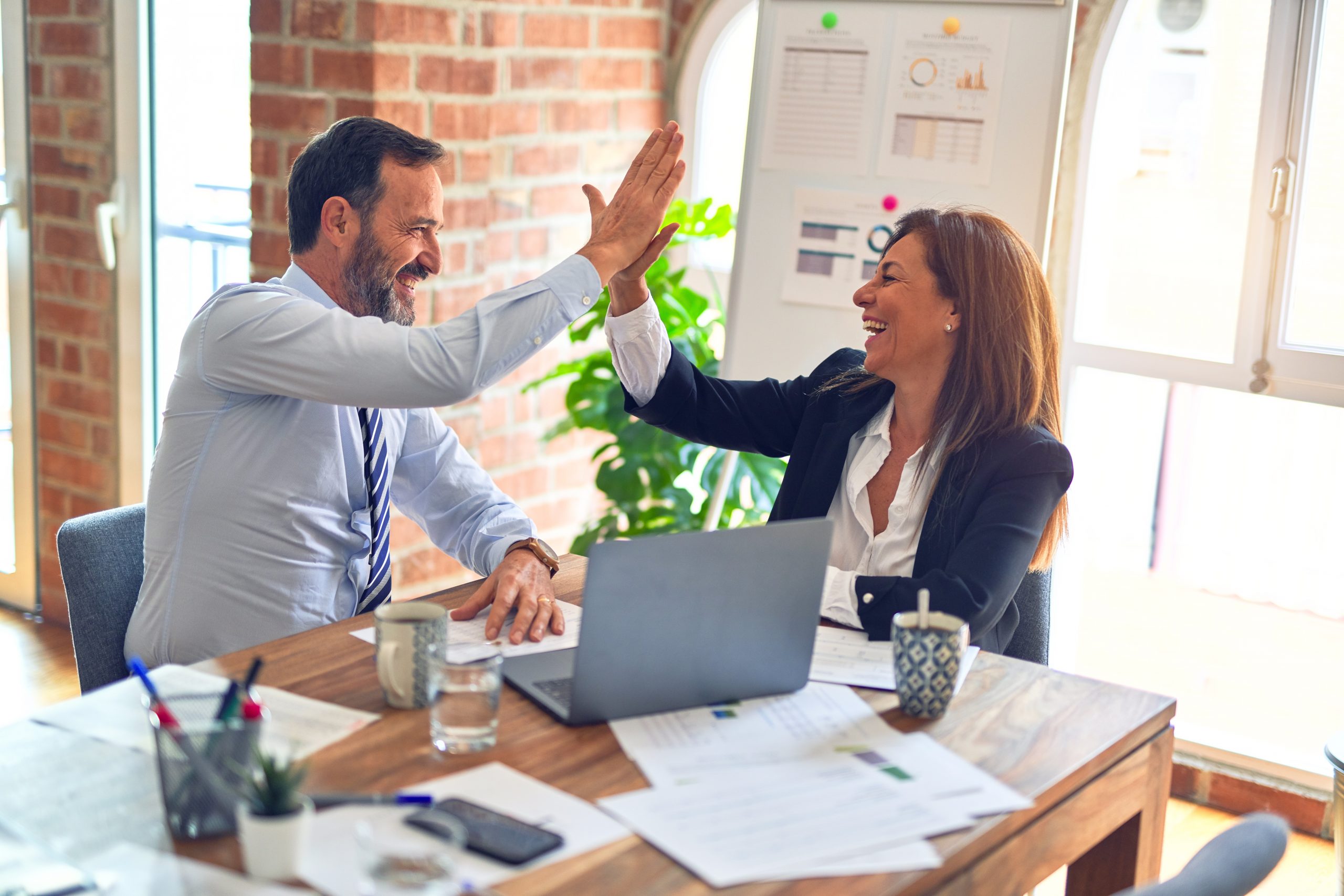
Six Sigma offers a variety of powerful tools that help organizations make data-driven decisions. Yet most people in an organization do not hold a degree in statistics and may feel that filling out endless data forms is pointless. When first starting a deployment, it is best to make things as easy and painless as possible for the non-Belt community. Once Six Sigma has gained momentum, Belts can enhance the statistical aspect and refine the methods they use.
Here are three examples for leaner tools that could be used to ease process owners and other non-Belts into the method during an initial deployment:
1. Failure Mode and Effects Analysis (FMEA)
If a Six Sigma team does everything manually in the standard FMEA template, it may need to fill in somewhere between 20 and 30 columns per row. To do that, team members may need to get thousands of data records from the process owner. And once the FMEA is complete, will the Champion even care if the risk priority number is 441 or 810?
When starting out, people may not even be capable of telling whether a defect occurs 7 percent or 70 percent of the time. But they do know what you need to be looking for – their most obvious pains. Most likely, the information Belts need from the process owner is this: What and where could something happen? Why would it happen? How bad is it? Who is going to do what about it, and is it effective?
That is a total of seven questions that almost everybody should be able to answer about their process. Asking these questions allows practitioners to get some data quickly, without misunderstanding or redundancy. As the initiative becomes more sophisticated, practitioners can work to refine the FMEA assessment process.
2. Analytic Hierarchy Process (AHP)
The AHP consists of simply going through a list of options and asking for each possible pair, Is (the first) more important than (the second) – and if so, by how much? But it can be tedious for larger amounts of options.
Time can be saved, however, by reviewing and optimizing the list beforehand, removing the unnecessary comparison questions. If the team already knows that gadget production is three times more important than widget production, why ask later if widget production is more important than gadget production? Taking that to the next level: If the team knows that gadget production is a factor three over widget production and that widgets are twice as important as trinkets – why waste stakeholder time by asking whether trinkets beat gadgets?
Optimizing AHP requires a bit of thought and definitely some information technology support. But for Belts doing the AHP on six factors, completing optimization first makes the difference between discussing 30 comparisons or nine. The AHP session may be condensed from two hours to 30 minutes, which key decision makers will appreciate.
3. Quality Function Deployment (QFD)
QFD is a support process for innovation and change, and also helps in assessing the status quo. It is nearly a science, and performs best in the hands of trained experts.
The information needed to first introduce QFD is not necessarily related to interactions, benchmarks and development status. What practitioners really need to know is: who is doing what, and why?
When practitioners know what requirements a process realizes, and what groups are engaged in the operation of the process, they have a solid basis for process improvement. They can still build intricate houses of quality later, when there is at least a formal requirement process.
Create Other Simplified Tools
The list does not stop here. With a small time investment studying a tool, chances are practitioners can find a simplified, leaner version that provides the information Belts really need from process owners in order to produce initial results.