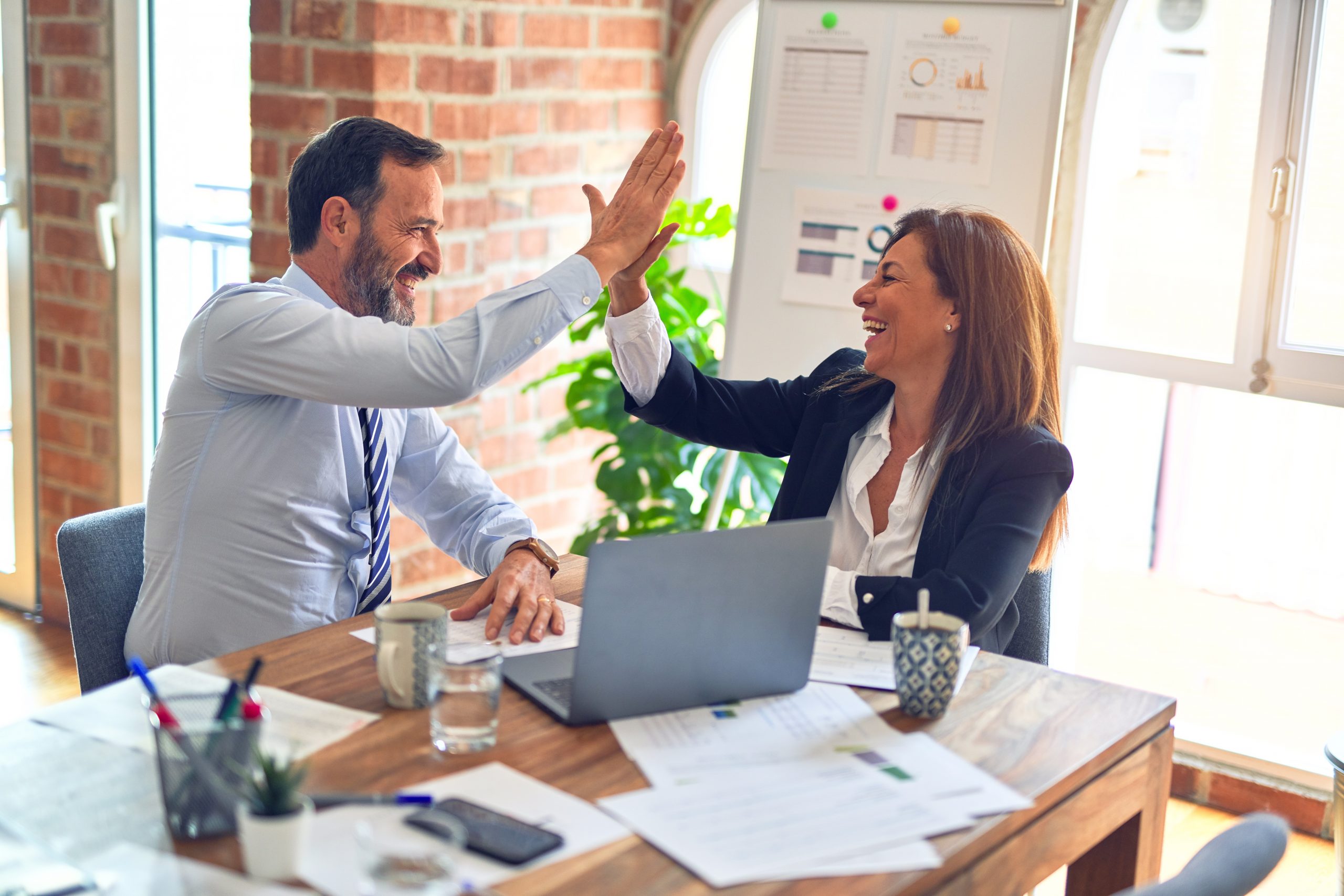
The future is knocking at the door of the U.S. banking industry. But how do banks get the future into their daily operations? More and more banks are using Design for Six Sigma (DFSS) to help them to take full advantage of such modern processes as electronic check presentment, thereby reducing expenses and increasing profits.
DFSS has particular application as the banking industry gets ready for the Check Clearing for the 21st Century Act (or what is called “Check 21”) to become effective on October 28. The act will allow the use of substitute representations of paper checks. According to the Federal Reserve Board, “Check 21 is designed to foster innovation in the payments system and to enhance its efficiency by reducing some of the legal impediments to check truncation.” The act paves the way for banks to implement interbank image exchange within their electronic check presentment (ECP) program. Combined with a reduction in costs for image software and hardware, this encourages both large and small banks to take full advantage of ECP.
Interbank Image Exchange a Big Cost-Saver
Current ECP processes simply transfer code data and payment information to the payee bank with the actual paper to follow the next day. However, most transit operations still rely on traditional paper processing incurring significant transportation costs.
ECP programs utilizing interbank image exchange promise to save banks billions of dollars on lower processing costs, decreased fraud losses, reduced portfolio of non-earning assets and increased revenues. For a bank processing one million checks per day, it is estimated they would exchange 127.5 million transit checks and save about $15.8 million per year (based on information from the September 1997 Image Archive Forum). But before any savings can be realized, banks must spend time and money on implementing flawless ECP programs. It is a complex undertaking to transform current item processing, returns processing, and research/adjustment processing into the future check information age.
The Design for Six Sigma methodology is powerful enough to handle the task. Six Sigma works because CEOs and management embrace and support it, employees who serve on the project team become committed through their involvement, and all outcomes are based on actual data. Design for Six Sigma is a complement to Six Sigma’s DMAIC (Define, Measure, Analyze, Improve and Control) methodology. The basic difference between the two methodologies is that DMAIC focuses on improving existing processes while DFSS focuses on developing new processes or completely overhauling existing processes. Those doing DFSS projects design a process to reach Six Sigma levels before it’s implemented, using the IDDOV (Identify, Define, Design, Optimize and Verify) steps.
Four Phases of Design for Six Sigma
Design for Six Sigma projects have four distinct phases and the many statistical tools available within them. The four phases build upon one another and always keep the mission of the project and voice of the customer at the forefront. The phases are:
Phase 1 – Identify opportunity
Define opportunity
Phase 2 – Develop concept
Phase 3 – Optimize design
Phase 4 – Verify design
Perhaps the most important – and often most risky – phase of a DFSS project is the first phase or the ID in IDDOV. The objective of Phase 1 is to provide clear direction for the efforts in Phases 2-4. Mistakes occurring in Phase 1 will obviously undermine what is done in later phases. It is important to budget enough time to produce the following:
1) Project charter
2) Business case
3) Project plan
4) Quality function deployment (QFD)
5) Critical to quality (CTQ) measures
The project charter, business plan and project plan all serve to guide the ECP project as it moves forward. The project charter includes the scope, which provides the boundaries of the work to be completed. One must make sure the scope is neither too broad nor too narrow. A broad scope can create an overburden and confuse project team members. For example, a scope of implementing an image archive and setting up image exchange is too large, and would likely fail. On the other hand, a scope too narrow may fail to allow the team members to feel as though they achieved anything. Management must determine the best way to split up the work into different projects (i.e., project scopes) in order to reach the organization’s overall objectives.
Utilizing the Voice of the Customer
The rest of the activities in Phase 1 become the guidelines to the end product. The power of DFSS is apparent here because the voice of the customer (both internal associates and external customers) is transformed into quantifiable requirements utilizing quality function deployment (QFD) and critical to quality (CTQ) measures.
In the second phase, develop concept, the objective is to identify how the requirements from Phase 1 will be met. The project team identifies alternative solutions through the use of creative methods such as brainstorming, assumption busting or TRIZ (Theory of Inventive Problem Solving). The team then begins to evaluate the alternatives using multi-voting, criteria-based matrix or Pugh concept selection techniques. Using these methods, the team determines which alternatives best meet the ECP project’s requirements. After the team identifies the best alternative solution, they identify potential problems using failure modes and effects analysis (FMEA).
Optimizing the Design Using Robust Design
By this point, the team is confident about the requirements and the chosen solution. Phase 3 of the project puts the pedal to the metal, and the project team works to optimize the design using robust design – a two-step process created by Dr. Genichi Taguchi. The steps are:
1) Minimize variability in the product or process (robust optimization).
2) Adjust the output to hit the target.
In a general sense, the ECP project team starts by identifying the ideal function of the solution. The ideal function of image exchange is the transformation of information from the transit checks deposited at a bank to an image cash letter and eventually to the transfer of funds from the payee bank. Robust design works to minimize the variability of the transformation process, thus minimizing problems that would create defects. This in turn enables the process to be at Six Sigma levels.
Final Steps Before the Cost Savings
In the last phase the project team verifies the design, builds a prototype, tests and fixes it using iterative cycles, and conducts capability studies to determine if the process meets all requirements outlined in Phase 1. Once the team is satisfied with the results, it implements a pilot production program and monitors it using process control charts and capability charts.
Total cost savings are realized when the pilot program is integrated into full production.